3D printing hamilton ontario
3D Printing Service Hamilton | Instant Quotes Online
Our 3D printing capabilities
We have over 90 3D printing shops in our network and are well known for manufacturing high-quality parts at competitive prices, from rapid prototyping with Fused Deposition Modeling (FDM) to functional end parts made with Selective Laser Sintering (SLS) or Multi Jet Fusion (MJF).
Gallery of 3D printed parts manufactured by Hubs
With over 65,000 customers from every industry, including aerospace, defense, robotics, medical, machinery, automotive and electronics, we have extensive experience meeting a diverse range of 3D printing requirements, from prototyping to production: Visual aids, concept models, injection-molding prototypes, form-fit & function prototypes, tooling and casting patterns, jigs, grips and fixtures, and durable end parts.
HP PA 12 - Dyed Black
Customer | True North Design |
Purpose | Structural and vacuum EOAT components |
Process | SLS / MJF |
Unit price | $69. |
Industry | Automotive |
Prototyping PLA
Customer | Allision Conner |
Purpose | End caps and cable strain relief for sheet metal enclosure |
Process | FDM |
Unit price | $7.92 / $4.72 / $2.80 |
Industry | Industrial Automation |
HP PA 12
Customer | US Hammer |
Description | A part for gasoline engine powered jackhammers |
Process | MJF |
Unit price | $22.18 |
Industry | Construction |
Markforged Onyx - Black
Customer | Autocom Manufacturing |
Purpose | A production part for 3D printed lathe gantry gripper fingers |
Process | FDM |
Unit price | $48.![]() |
Industry | Automotive |
PC Stratasys - white
Customer | Terumo medical corporation |
Purpose | Prototyping parts used for a disposable electrical device |
Process | FDM |
Unit price | $55.38 / $32.96 |
Industry | Medical |
Formlabs Clear Resin
Customer | Aversan Inc |
Purpose | A prototyping part of an injection molded component for an automated door mechanism |
Process | SLA |
Unit price | $29.83 |
Industry | Aerospace |
HP PA 12 - Dyed Black
Customer | True North Design |
Purpose | Structural and vacuum EOAT components |
Process | SLS / MJF |
Unit price | $69.![]() |
Industry | Automotive |
Prototyping PLA
Customer | Allision Conner |
Purpose | End caps and cable strain relief for sheet metal enclosure |
Process | FDM |
Unit price | $7.92 / $4.72 / $2.80 |
Industry | Industrial Automation |
HP PA 12
Customer | US Hammer |
Description | A part for gasoline engine powered jackhammers |
Process | MJF |
Unit price | $22.18 |
Industry | Construction |
Markforged Onyx - Black
Customer | Autocom Manufacturing |
Purpose | A production part for 3D printed lathe gantry gripper fingers |
Process | FDM |
Unit price | $48.![]() |
Industry | Automotive |
PC Stratasys - white
Customer | Terumo medical corporation |
Purpose | Prototyping parts used for a disposable electrical device |
Process | FDM |
Unit price | $55.38 / $32.96 |
Industry | Medical |
Formlabs Clear Resin
Customer | Aversan Inc |
Purpose | A prototyping part of an injection molded component for an automated door mechanism |
Process | SLA |
Unit price | $29.83 |
Industry | Aerospace |
HP PA 12 - Dyed Black
Customer | True North Design |
Purpose | Structural and vacuum EOAT components |
Process | SLS / MJF |
Unit price | $69.![]() |
Industry | Automotive |
Prototyping PLA
Customer | Allision Conner |
Purpose | End caps and cable strain relief for sheet metal enclosure |
Process | FDM |
Unit price | $7.92 / $4.72 / $2.80 |
Industry | Industrial Automation |
HP PA 12
Customer | US Hammer |
Description | A part for gasoline engine powered jackhammers |
Process | MJF |
Unit price | $22.18 |
Industry | Construction |
Markforged Onyx - Black
Customer | Autocom Manufacturing |
Purpose | A production part for 3D printed lathe gantry gripper fingers |
Process | FDM |
Unit price | $48.![]() |
Industry | Automotive |
PC Stratasys - white
Customer | Terumo medical corporation |
Purpose | Prototyping parts used for a disposable electrical device |
Process | FDM |
Unit price | $55.38 / $32.96 |
Industry | Medical |
Formlabs Clear Resin
Customer | Aversan Inc |
Purpose | A prototyping part of an injection molded component for an automated door mechanism |
Process | SLA |
Unit price | $29.83 |
Industry | Aerospace |
HP PA 12 - Dyed Black
Customer | True North Design |
Purpose | Structural and vacuum EOAT components |
Process | SLS / MJF |
Unit price | $69.![]() |
Industry | Automotive |
Prototyping PLA
Customer | Allision Conner |
Purpose | End caps and cable strain relief for sheet metal enclosure |
Process | FDM |
Unit price | $7.92 / $4.72 / $2.80 |
Industry | Industrial Automation |
HP PA 12
Customer | US Hammer |
Description | A part for gasoline engine powered jackhammers |
Process | MJF |
Unit price | $22.18 |
Industry | Construction |
Markforged Onyx - Black
Customer | Autocom Manufacturing |
Purpose | A production part for 3D printed lathe gantry gripper fingers |
Process | FDM |
Unit price | $48.![]() |
Industry | Automotive |
PC Stratasys - white
Customer | Terumo medical corporation |
Purpose | Prototyping parts used for a disposable electrical device |
Process | FDM |
Unit price | $55.38 / $32.96 |
Industry | Medical |
Formlabs Clear Resin
Customer | Aversan Inc |
Purpose | A prototyping part of an injection molded component for an automated door mechanism |
Process | SLA |
Unit price | $29.83 |
Industry | Aerospace |
HP PA 12 - Dyed Black
Customer | True North Design |
Purpose | Structural and vacuum EOAT components |
Process | SLS / MJF |
Unit price | $69.![]() |
Industry | Automotive |
Prototyping PLA
Customer | Allision Conner |
Purpose | End caps and cable strain relief for sheet metal enclosure |
Process | FDM |
Unit price | $7.92 / $4.72 / $2.80 |
Industry | Industrial Automation |
HP PA 12
Customer | US Hammer |
Description | A part for gasoline engine powered jackhammers |
Process | MJF |
Unit price | $22.18 |
Industry | Construction |
Markforged Onyx - Black
Customer | Autocom Manufacturing |
Purpose | A production part for 3D printed lathe gantry gripper fingers |
Process | FDM |
Unit price | $48.![]() |
Industry | Automotive |
PC Stratasys - white
Customer | Terumo medical corporation |
Purpose | Prototyping parts used for a disposable electrical device |
Process | FDM |
Unit price | $55.38 / $32.96 |
Industry | Medical |
Formlabs Clear Resin
Customer | Aversan Inc |
Purpose | A prototyping part of an injection molded component for an automated door mechanism |
Process | SLA |
Unit price | $29.83 |
Industry | Aerospace |
HP PA 12 - Dyed Black
Customer | True North Design |
Purpose | Structural and vacuum EOAT components |
Process | SLS / MJF |
Unit price | $69.![]() |
Industry | Automotive |
Prototyping PLA
Customer | Allision Conner |
Purpose | End caps and cable strain relief for sheet metal enclosure |
Process | FDM |
Unit price | $7.92 / $4.72 / $2.80 |
Industry | Industrial Automation |
HP PA 12
Customer | US Hammer |
Description | A part for gasoline engine powered jackhammers |
Process | MJF |
Unit price | $22.18 |
Industry | Construction |
Markforged Onyx - Black
Customer | Autocom Manufacturing |
Purpose | A production part for 3D printed lathe gantry gripper fingers |
Process | FDM |
Unit price | $48.![]() |
Industry | Automotive |
PC Stratasys - white
Customer | Terumo medical corporation |
Purpose | Prototyping parts used for a disposable electrical device |
Process | FDM |
Unit price | $55.38 / $32.96 |
Industry | Medical |
Formlabs Clear Resin
Customer | Aversan Inc |
Purpose | A prototyping part of an injection molded component for an automated door mechanism |
Process | SLA |
Unit price | $29.83 |
Industry | Aerospace |
HP PA 12 - Dyed Black
Customer | True North Design |
Purpose | Structural and vacuum EOAT components |
Process | SLS / MJF |
Unit price | $69.![]() |
Industry | Automotive |
Prototyping PLA
Customer | Allision Conner |
Purpose | End caps and cable strain relief for sheet metal enclosure |
Process | FDM |
Unit price | $7.92 / $4.72 / $2.80 |
Industry | Industrial Automation |
HP PA 12
Customer | US Hammer |
Description | A part for gasoline engine powered jackhammers |
Process | MJF |
Unit price | $22.18 |
Industry | Construction |
Markforged Onyx - Black
Customer | Autocom Manufacturing |
Purpose | A production part for 3D printed lathe gantry gripper fingers |
Process | FDM |
Unit price | $48.![]() |
Industry | Automotive |
PC Stratasys - white
Customer | Terumo medical corporation |
Purpose | Prototyping parts used for a disposable electrical device |
Process | FDM |
Unit price | $55.38 / $32.96 |
Industry | Medical |
Formlabs Clear Resin
Customer | Aversan Inc |
Purpose | A prototyping part of an injection molded component for an automated door mechanism |
Process | SLA |
Unit price | $29.83 |
Industry | Aerospace |
HP PA 12 - Dyed Black
Customer | True North Design |
Purpose | Structural and vacuum EOAT components |
Process | SLS / MJF |
Unit price | $69.![]() |
Industry | Automotive |
Prototyping PLA
Customer | Allision Conner |
Purpose | End caps and cable strain relief for sheet metal enclosure |
Process | FDM |
Unit price | $7.92 / $4.72 / $2.80 |
Industry | Industrial Automation |
HP PA 12
Customer | US Hammer |
Description | A part for gasoline engine powered jackhammers |
Process | MJF |
Unit price | $22.18 |
Industry | Construction |
Markforged Onyx - Black
Customer | Autocom Manufacturing |
Purpose | A production part for 3D printed lathe gantry gripper fingers |
Process | FDM |
Unit price | $48.![]() |
Industry | Automotive |
PC Stratasys - white
Customer | Terumo medical corporation |
Purpose | Prototyping parts used for a disposable electrical device |
Process | FDM |
Unit price | $55.38 / $32.96 |
Industry | Medical |
Formlabs Clear Resin
Customer | Aversan Inc |
Purpose | A prototyping part of an injection molded component for an automated door mechanism |
Process | SLA |
Unit price | $29.83 |
Industry | Aerospace |
HP PA 12 - Dyed Black
Customer | True North Design |
Purpose | Structural and vacuum EOAT components |
Process | SLS / MJF |
Unit price | $69.![]() |
Industry | Automotive |
Prototyping PLA
Customer | Allision Conner |
Purpose | End caps and cable strain relief for sheet metal enclosure |
Process | FDM |
Unit price | $7.92 / $4.72 / $2.80 |
Industry | Industrial Automation |
HP PA 12
Customer | US Hammer |
Description | A part for gasoline engine powered jackhammers |
Process | MJF |
Unit price | $22.18 |
Industry | Construction |
Markforged Onyx - Black
Customer | Autocom Manufacturing |
Purpose | A production part for 3D printed lathe gantry gripper fingers |
Process | FDM |
Unit price | $48.![]() |
Industry | Automotive |
PC Stratasys - white
Customer | Terumo medical corporation |
Purpose | Prototyping parts used for a disposable electrical device |
Process | FDM |
Unit price | $55.38 / $32.96 |
Industry | Medical |
Formlabs Clear Resin
Customer | Aversan Inc |
Purpose | A prototyping part of an injection molded component for an automated door mechanism |
Process | SLA |
Unit price | $29.83 |
Industry | Aerospace |
HP PA 12 - Dyed Black
Customer | True North Design |
Purpose | Structural and vacuum EOAT components |
Process | SLS / MJF |
Unit price | $69.![]() |
Industry | Automotive |
Prototyping PLA
Customer | Allision Conner |
Purpose | End caps and cable strain relief for sheet metal enclosure |
Process | FDM |
Unit price | $7.92 / $4.72 / $2.80 |
Industry | Industrial Automation |
HP PA 12
Customer | US Hammer |
Description | A part for gasoline engine powered jackhammers |
Process | MJF |
Unit price | $22.18 |
Industry | Construction |
Markforged Onyx - Black
Customer | Autocom Manufacturing |
Purpose | A production part for 3D printed lathe gantry gripper fingers |
Process | FDM |
Unit price | $48.![]() |
Industry | Automotive |
PC Stratasys - white
Customer | Terumo medical corporation |
Purpose | Prototyping parts used for a disposable electrical device |
Process | FDM |
Unit price | $55.38 / $32.96 |
Industry | Medical |
Formlabs Clear Resin
Customer | Aversan Inc |
Purpose | A prototyping part of an injection molded component for an automated door mechanism |
Process | SLA |
Unit price | $29.83 |
Industry | Aerospace |
Instant, online 3D printing quotes
-
Upload a CAD to start (STEP, STP, IGES, IGS, SLDPRT, 3DM, SAT, STL, OBJ or X_T)
-
Price updates in real-time as you change materials, lead time, etc.
.
-
No hidden costs. Our instant quotes are not just indications, but the actual price, and include shipping and customs up front.
Learn about how our quoting algorithm works
Our ordering process
Receive instant quote
Upload your CAD to our online quoting platform
Confirm specs
Configure your part specifications and select a lead time that suits your schedule
Production
We select the best manufacturer for your order, and production begins immediately
Quality control
We take full responsibility for making sure your parts are manufactured according to our standards
Delivery
Our 3D printing service has been rated 4.9/5
Over 259 customers are satisfied with our 3D printing service.
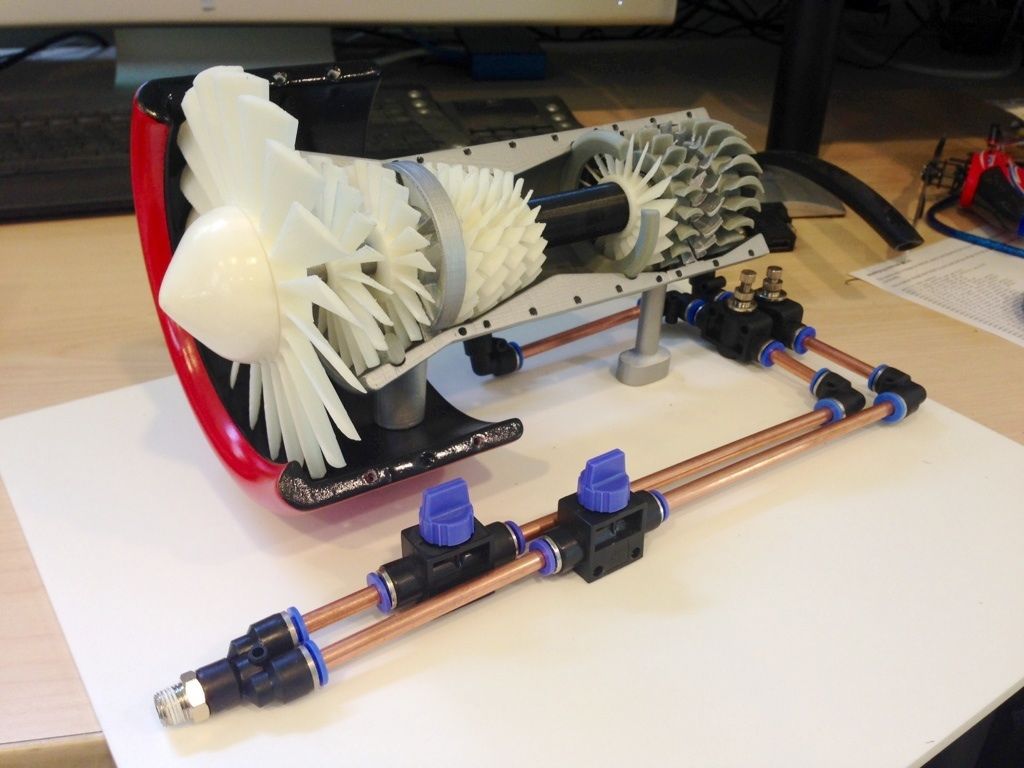
“Perfect Prints, Fast Delivery, Competitive Pricing”
“Gr8 hub. Super fast service. Prints are awesome. Loved my first experience.”
“Great print quality, great doing business again!”
“Great service, friendly guy. Very responsive. ”
“Fantastic quality, fast printing and shipping! Thanks! ”
“Perfect! Everything was fantastic, well-communicated and the parts turned out absolutely perfectly. I'm very impressed, many thanks :)”
“Quick service and fast shipping, thank you so much!”
“very accomodating, high quality parts, fast turnaround. Pleasant experience ! Thank you. ”
“The printed part is working well in its intended application. Service provided was excellent in all aspects.”
“Great service, got me the parts quickly and done well. Communicated if there was any problems with the part and made sure I was delivered a good product. ”
“My order was ready the next day and the service was great. I will use them again for sure. Picked up my order and saw their machine's, really high end equipment and very friendly staff.”
“Excellent service and quality. Will order again.”
“Good experience, highly recommended and will use again.”
“Parts were made quickly and at a fair price”
“Very helpful. Very knowledgeable. Great experience. The did what I was looking for perfectly. Thank you. ”
“A++ as usual. Amazing, quick and thoughtful. ”
“Rob was instrumental in getting my print turned around in short order. I couldn't be more pleased with the whole experience!”
“Excellent service! Second time using them and not disappointed!”
“Very satisfied, with the communication, the recommendations, the product and turnaround time. The thing is jokes, and we've already got the other offices wanting to know how/where we got it. ”
“Remarkable quality
Very Precise Printer
I have a good amount of experience with 3D printers and this is the best home manufacturing i have come across.
Two thumbs up!”
“Fantastic service, superb print, and unexpectedly speedy turn-around!!”
“Prints were completed very quickly. Responsive and helpful when I had questions. Great service!”
“Great communication and speed of service. ”
“Everything works well, thanks for the backup. Will print again with you guys in the future.”
“Very helpful at every step. Fast printing and delivery. Prints turned out wonderfully. ”
Show more reviews
Show less reviews
Teams build better parts
Create your Hubs team and start collaborating
Read more
The Hubs Standard - consistent quality, every time
Hubs takes the stress out of manufacturing by guaranteeing the quality and consistency of every part. Each order is dimensionally and visually inspected to make sure it meets the Hubs Standard.
3D printing materials
We can generate instant 3D printing quotes for 25+ plastics. For metal 3D-printed parts, you can request a quote from our parent company, Protolabs.
Available materials
SLS
PA 12 Glass filled PA 12
Desktop FDM
Prototyping PETG Prototyping ASA Prototyping TPU Prototyping ABS Prototyping PLA
Desktop SLA
Formlabs Standard Resin Formlabs Clear Resin Formlabs Tough Resin 2000 Formlabs Rigid Resin 4000 Formlabs Grey Pro Resin Formlabs Flexible Resin 80A Formlabs High Temp Resin Formlabs Durable Resin
MJF
HP PA 12 Glass filled HP PA 12
Industrial FDM
Markforged Onyx ABSplus Stratasys ULTEM 9085 Stratasys Stratasys ASA ABS M30 Stratasys ULTEM 1010 Stratasys
Industrial SLA
Accura 25 (PP-like) Accura ClearVue Accura Xtreme White 200 (ABS-like)
3D printing locations near Hamilton
Hamilton Coquitlam Oakville
Kitchener Mississauga Brampton
Erie, PA Toronto Markham
Buffalo, NY
The 3D Printing Handbook
No one understands 3D printing like us - our founders literally wrote the book. Click here to download the sample chapters.
Buy the book from Amazon
FAQ's
How much does your 3D printing service cost?
The cost of your 3D printed parts depends on factors such as part volume, part complexity, choice of material, which 3D printing technology is used, and if any post processing is required. For more details on these cost factors, see our article on the cost of 3d printing. To check the cost of your 3D printed part, simply upload a CAD (.STL) file and select your material and 3D printing technology to receive a quote within seconds.
How do you guarantee the quality of my prints?
Your parts are made by experienced 3D printing shops within our network. All facilities are regularly audited to ensure they consistently meet the Hubs quality standard. We include a standardized inspection report with every order and offer a First Article Inspection service on orders of 100+ units.
We have partners in our network with the following certifications, available on request: ISO9001, ISO13485 and AS9100.
Follow this link to read more about our quality assurance measures.
How do I select the right 3D printing process for my prints?
You can select the right 3D printing process by examining which materials suit your need and what your use case is.
By material: if you already know which material you would like to use, selecting a 3D printing process is relatively easy, as many materials are technology specific.
By use case: once you know whether you need a functional or visual part, choosing a process is easy.
For more help, read our guide to selecting the right 3D printing process. Find out more about Fused Deposition Modeling (FDM), Selective Laser Sintering (SLS), Multi Jet Fusion (MJF) and Stereolithography (SLA).
How can I reduce the cost of my 3D prints?
In order to reduce the cost of your 3D prints you need to understand the impact certain factors have on cost. The main cost influencing factors are the material type, individual part volume, printing technology and post-processing requirements.
Once these have been decided, an easy way to further cut costs is to reduce the amount of material used. This can be done by decreasing the size of your model, hollowing it out, and eliminating the need for support structures.
To learn more, read our full guide on how to reduce the cost of 3D printing.
Where can I learn more about 3D printing?
Our knowledge base is full of in-depth design guidelines, explanations on process and surface finishes, and information on how to create and use CAD files. Our 3D printing content has been written by an expert team of engineers and technicians over the years.
See our complete engineering guide to 3D printing for a full breakdown of the different 3D printing technologies and materials. If you want even more 3D printing, then check out our acclaimed 3D printing handbook here.
We have an extensive range of online resources developed to help engineers improve their capabilities.
Introductory guides
Design guides
Material guides
Applications
CAD & file preparation
Post processing & finishing
Our other manufacturing capabilities
CNC machining
CNC machining
Milling (3-, 4- & full 5-axis), turning and post-processing
-
50+ metals and plastics & 10 surface finishes
-
Tolerances down to ±.0008” (0.020 mm)
-
Lead times from 5 business days
See our CNC machining services
Put your 3D printed parts into production today
Get an instant 3D printing quote
3D Printing Hamilton - Get A Quote
Are you looking for 3D printing services in Hamilton or the Greater Toronto and Hamilton Area? (including Mississauga, Brampton, Oakville, and Burlington)
Agile Manufacturing is a trusted 3D printing partner for many businesses in the GTHA for prototyping, design, and production.
When it comes to 3D printing, it’s important to have a responsive and reliable manufacturing service for your growing business.
Agile Manufacturing fits the bill and is your one stop shop for all things 3DP!
Get a Custom Quote Now
What is 3D Printing?
3D Printing, also known as additive manufacturing (AM), is the process of building parts or objects layer-by-layer using a three-dimension technology from a digital CAD file. Each layer can be seen as a thinly sliced cross-section of the object.
AM is the opposite of subtractive manufacturing (CNC) which is cutting out a piece of metal or plastic. Additive technologies enables you to produce complex shapes that are otherwise unable to be built using other manufacturing methods.
Manufacturing has greatly improved over the years and has become increasingly ‘digital’ due to 3D printing technology. This technology has already changed how companies design and produce manufactured goods.
Many industries (aerospace, automotive, manufacturing) have already made the switch to 3DP for faster and more reliable prototypes and production parts.
At Agile Manufacturing, we provide the highest quality 3DP and AM services to cater to your needs.
Why Choose Additive Manufacturing?
In short, AM is fast and relatively low cost.
From design to manufacturing, a prototype can be delivered in a matter of days. Where this technology excels is in rapid prototyping and low volume production.
Businesses can take advantage of AM technology for short to medium runs and bridge production. 3DP greatly reduces the time to get the first version of a product and makes it possible to print complex geometries and interlocking parts that require no assembly.
Stereolithography (SLA) is a AM process where UV light and photopolymer resin are used to make printable parts. The resin is cured by the laser which hardens the plastic. These layers are made at high speed, making SLA a great option for rapid prototyping.
Benefits of 3D Printing in Hamilton
Cost EffectivenessTraditional prototyping and production methods such as CNC machining and injection molding requires expensive machinery and tools which carries higher labor and material costs.
On the other hand, AM is a one-step process, avoiding the expensive upfront costs of tooling. In addition, 3D printers use only the material that is needed to print the parts and requires little supervision, which lowers labor costs.
Reduces Waste3DP utilizes only the specific material that is needed to complete the job. As it is an AM method, material is layered onto itself as needed, whereas traditional subtractive manufacturing methods require larger upfront material costs and contributes to more waste due to leftover material.
The streamlined processes of 3D printing help speed up production schedules which reduces material and energy consumption long term. As material science evolves AM is expanding the number of sustainable and biodegradable materials available, further offsetting the environmental impact.
Consistent Customization of PartsWhen going through many different iterations of a design, 3DP does not require the creation of a new tool, mold, die or jig like other manufacturing processes. Different designs can simply be reprinted without high upfront costs.
AM simply requires a slicer software that can interpret the part into slices to send data to the printer. The designer can re-design their part in CAD and send it back to the operator for printing.
Production of complex geometries is made possible using additive technologies that are not possible in traditional manufacturing (injection molding, cast urethane, etc.). Consolidation can also easily be accomplished with 3DP which can reduce the number of parts needed for a design, thus reducing assembly and design costs.
Agile Manufacturing Inc. runs the most up to date AM technologies ensuring the best quality and turnaround on the market today.
We also provide 3d printing services in the following areas: Toronto, Kitchener, Calgary, Ottawa, Montreal, Vancouver
3D printing. What are we breathing?
Hello dear. In this article, I will try to tell you about what and in what quantities can be released from plastics during the FDM 3D printing process. The issue will be considered not from the side of global environmental pollution, but from the side of possible pollution of the room or workshop in which the FDM 3D printer directly operates.
I recommend that you read at least the fourth and fifth sections. Link to the video version of the article at the end. Here is the content of the article:
1 What and how much is released from plastics?
2 At what point in time is the emission of suspended particles maximum?
3 Effect of print settings
4 Particulate matter and VOC control methods
5 Pins
I must say right away that all the data is again for foreign plastics. In the comments, you write to me that it would be interesting to read about our materials, and not about foreign ones. Yes, I agree, perhaps the conclusions drawn from my work may not be applicable to "our" plastics. But in defense, I note that, firstly: the conditional foreign ABS should not radically differ from “our” ABS. Secondly, our major producers say that they buy raw materials from European firms. In this regard, I believe that the voiced data should be relevant for domestic filaments.
1 What and how much is released from plastics?
Two types of air pollutants are emitted from any plastic during operation of a 3D printer. Firstly, these are ultra- and finely dispersed (or suspended) particles, the size of which ranges from several nanometers to several micrometers. The second is volatile organic compounds.
In fact, the first group is micro dust, consisting of fragments of plastic, as well as fragments of fillers. In [1], an analysis was made of the release of suspended particles from various plastics during printing of a cylindrical sample with a duration of 60 minutes. Plastics PLA, PVA, ABS, PC, ASA, nylon were analyzed. An analysis of the results showed an interesting regularity in the intensity of the release of suspended particles during the operation of a 3D printer. Look at this graph:
Zero is the start of printing. It is clearly seen that it is at the very beginning of printing that there is a sharp increase in the concentration of suspended particles, then the concentration gradually decreases. The researchers attribute the initial peak to the nozzle's heating period to operating temperature. At this point, the plastic, which is motionless inside the nozzle, is subjected to prolonged heating and, consequently, thermal degradation. It can be seen from the graphs that such a picture is typical for absolutely all plastics. In support of this, the researchers from [2] come to similar conclusions.
Now let's look at each plastic separately. I think it will be most interesting for you to find out which plastics are leaders in terms of the number of emitted particles. ASA took first place, followed by nylon, PC and ABS, respectively. PLA and PVA turned out to be the most environmentally friendly.
This is how the size distribution of emitted particles looks like when printing a sample for pollution leaders:
And this is how the graphs for PLA of various companies and PVA look like:
The difference in the graphs is obvious. Please note that PLA and PVA emit particles at the very beginning of printing, and then, after a while, the release of particles almost stops.
Here are the results of measurements made by the authors of another study [3]:
On this graph, manufacturers and the type of plastic are labeled at the bottom, and the intensity of the release of suspended particles is measured along the vertical axis. Again, ABS and PC are among the leaders in terms of pollution. Additionally, HIPS and nylon joined them in this study. The most environmentally friendly again turned out to be PLA.
As far as carbon or fiberglass reinforced plastics are concerned, they are practically unexplored. In one of the works [4], along with other plastics, I was able to find this:
Underlined in red is PETG with 8-12% fiberglass. As you can see, such plastic is the leader in the selection of large particles. Once again I will say that this is the only result that I could find, so I can’t draw serious conclusions here, but anyway I decided to add it to the publication.
Now let's move on to the isolation of volatile organic compounds. In short, when printing with almost any filament, dozens of different compounds are released. Here, for example, is a table from [4]:
Plastics are signed in the table above. The first column lists the names of the chemical compounds. If there is no number for some connection, it means that it was not fixed by the device during printing with a specific plastic. Analyzing the table, we see that ASA and ABS plastics again become leaders in the anti-rating (ULTRAT is ABS with the addition of 3% polycarbonate). PETG becomes the most environmentally friendly (GLASS Transparent is also PETG, but with the addition of fiberglass).
Now let's turn to the results of research from another work [3], which examines a slightly different set of plastics:
This figure shows two histograms. The left histogram shows plastics with a maximum release of volatile organic compounds up to 40 micrograms per minute, and on the right - with an intensity of more than 40 micrograms per minute. The name of each column indicates the printer on which the material was printed.
Polycarbonate and TGlase (PETT plastic) are the most environmentally friendly. PLA looks a little worse. And nylon turned out to be the worst in terms of the number of emissions. It is interesting to note that for ABS plastics, the amount of emissions is highly dependent on the 3D printer on which they are printed, and can differ by as much as five times.
Pay attention to polycarbonate. If it is one of the most polluting in terms of the release of suspended particles, then it is the most environmentally friendly in terms of the release of volatile organic compounds.
2 At what point in time is the emission of suspended particles maximum?
Let's look at two graphs from [5]:
The left graph shows the particulate concentration inside the MakerBot 3D Printer, while the right graph shows the particulate concentration in the room where the 3D printer is located. Two peaks on the graphs mean two consecutively printed parts. Again, we see that a sharp increase in the number of suspended particles occurs at the very beginning of the printing of the part.
And here is another graph from another work [2]:
Shown here are three graphs showing the change in the concentration of suspended solids when printed with ABS plastic. According to the legend, the graphs differ in nozzle temperature. As in the previous work, it can also be seen here that after heating, at the moment of printing, an increase in the concentration of suspended particles occurs. From these graphs, another interesting point is visible.
3 Effect of print settings
These three graphs show that as the temperature of the nozzle increases, the concentration of suspended particles increases. However, the difference between the charts is significant. Other scientific works [4] confirm this:
This graph shows particulate matter concentration versus ABS nozzle temperature. It can be seen that at a nozzle temperature above 250 degrees there is a sharp increase in the number of ejected particles.
It is interesting to note the effect of printing speed on the concentration of suspended particles. Here is a graph from [2]:
These graphs show the dependence of the concentration of suspended particles when printing with ABS plastic at different print speeds. We compared printing at speeds of 30 mm/s (FR30 in the graph), 60 mm/s (FR60) and 90 mm/s (FR90). It is interesting to note that the maximum concentrations are observed at an average printing speed. In this case, the minimum concentration is observed for a speed of 90 mm/s.
4 Particulate matter and VOC control techniques
4.1 Studies have shown that reducing nozzle temperature reduces the amount of suspended particles released. Therefore, do not raise the nozzle temperature unnecessarily.
4.2 Increasing the print speed reduces the concentration of suspended particles. Another positive effect of increasing the printing speed is to reduce the printing time, which leads to a decrease in the time during which suspended particles are released.
4.3 Filtration. HEPA filters are effective for almost all sizes of particulate matter, but to be useful, you need a 3D printer with a closed chamber. In addition, HEPA filters do not capture volatile organic compounds at all, which, as it turns out, are emitted in abundance from some plastics. They need charcoal filters.
4.4 Ventilation or ventilation. I think this is the most efficient way for most conventional FDM 3D printers used at home and in workshops. Here are pictures from [5] showing the distribution of the concentration of suspended particles in a room with a 3D printer:
In a well-ventilated room, the concentration of particles is an order of magnitude lower and at a distance of more than a meter from the printer, only slightly higher than the background level.
4.5 Optimize printer performance. In paragraphs 4.1 and 4.2, I have already touched on the printing modes, but the authors of the scientific work [2] went further and proposed an interesting way to reduce the amount of suspended particles released. Its essence lies in the fact that we first heat up the empty nozzle to operating temperature, then load the filament and immediately start printing. After printing is completed, remove the filament. Here are graphs from [2] showing the result of such manipulations:
Both graphs show the emission of suspended particles when printing ABS with a nozzle temperature of 240°C and a speed of 60 mm/s. The top graph is printing without loading/unloading the filament.
5 Conclusions
As a conclusion, firstly, I would like to note that such plastics as ASA, ABS and nylon are leaders in terms of the amount of emitted particles and volatile organic compounds. The average highlights are polycarbonate and HIPS. The most environmentally friendly and in terms of suspended particles and volatile organic compounds are PLA and PETG.
Second, print in well-ventilated rooms or ventilate the room when printing. Try not to increase the temperature of the nozzle unnecessarily.
You may have noticed that I didn't say a word about how harmful it all is. The fact is that the assessment of the harmfulness of all this required quite a lot of time. I haven't been able to get definitive answers yet. Now I’ll just say that it’s rather harmful, especially with regular contact. Therefore, in this article, I deliberately did not touch on the topic of harmfulness. I hope that I will be able to deal with this issue to the end and then I will publish all the results.
Video version of the article:
That's all for now.
Sources:
1. Chýlek, R., Kudela, L., Pospíšil, J. , Šnajdárek, L. (2019). Fine particle emission during fused deposition modeling and thermogravimetric analysis for various filaments. Journal of Cleaner Production, 117790. doi:10.1016/j.jclepro.2019.117790
2. Deng, Y., Cao, S.-J., Chen, A., Guo, Y. (2016). The impact of manufacturing parameters on submicron particle emissions from a desktop 3D printer in the perspective of emission reduction. Building and Environment, 104, 311–319. doi:10.1016/j.buildenv.2016.05.02
3. Azimi, P., Zhao, D., Pouzet, C., Crain, N. E., Stephens, B. (2016). Emissions of Ultrafine Particles and Volatile Organic Compounds from Commercially Available Desktop Three-Dimensional Printers with Multiple Filaments. Environmental Science & Technology, 50(3), 1260–1268. doi:10.1021/acs.est.5b04983
4. Gu, J., Wensing, M., Uhde, E., Salthammer, T. (2019). Characterization of particulate and gaseous pollutants emitted during operation of a desktop 3D printer. Environment International, 123, 476–485. doi:10.1016/j.envint.2018.12.014
5. Zontek, T. L., Ogle, B. R., Jankovic, J. T., Hollenbeck, S. M. (2017). An exposure assessment of desktop 3D printing. Journal of Chemical Health and Safety, 24(2), 15–25. doi:10.1016/j.jchas.2016.05.008
Possibilities of 3D printing: art, fashion, medicine
Sculpture by Monika Gorchikova (Czech Republic)
Expressive sculptures by contemporary artists, dresses for fashion shows, architectural models and parts of the human body - a short guide on how to use 3D printing was compiled by Artyom Dezhurko .
3D printing was invented by American Chuck Hull in 1984. Modern 3D printers are capable of printing large objects, up to a car body; and use different printing techniques (stereolithography invented by Chuck Hull is just one of them). However, whatever the technique may be, the essence is the same: the printer creates an object by building up the material in layers. Thus, you can create an arbitrarily complex shape. 3D printers print from different materials: plastic, cellulose, ceramics, metals, sugar.
This material is an illustrated overview of how 3D printing is currently used in various fields: art, architecture, technology, fashion, medicine.
Richard DuPont, USA
Nick Erwink, USA
"Princess", Eric van Straten, Netherlands
A modern 3D printer prints layers so thin that they can no longer be seen with the naked eye. Therefore, sculptors love it: 3D printing is the same casting, but technologically simplified and allowing endless replication of the object. Sculptures with her help are very different: from photographically accurate images of famous football players to the vicious postmodern statuettes of Eric van Straten.
Michael Hansmeyer and Benjamin Dillenburger. Digital Grotesque, 2015
Study paper by Andy Zheng and Christina Eromenok at RPI School of Architecture
PTW Architects. Model of the Beijing National Water Sports Center, 2007
Most often, 3D printing is used for rapid prototyping - creating models of mechanisms and, especially often, architectural models. In addition, now 3D printers have begun to be used to produce large parts from which prefabricated houses are created. The Chinese company Winsun is experimenting with this technology.
In the automotive industry, 3D printing scale model production is widespread and seems to have completely supplanted the old plasticine sculpting technique. A model of James Bond's car from the movie "Skyfall" was printed on a 3D printer. And in 2010, a prototype of the Urbee car was created, the entire body of which was printed on a 3D printer.
ideas2cycles, Finland, The Fixer, 2012
Several bicycle frames have been created using a 3D printer (and even an entire Airbike bike - developed by EADS), but in their case there is no talk of mass production yet. More promising is the printing of couplings made of durable plastic, with the help of which in small "garage" bicycle workshops it is possible to assemble frames from factory metal tubes.
Chair Gaudi (Bram Genin)
A mold is printed on a 3D printer, which is then used to cast the supporting structure of the chair.
Hot Pop Factory
Sculpture of Charles and Ray Eames DSW chairs scanned and 3D printed.
LINK system
Christian Sjöström, Sweden, 2015.
Prototype Node
Modeling in Grasshopper. Charles Freed, UK, 2015.
3D printed as whole furniture (e.g. Gaudi chairs, designed by Bram Genen, 2009) and piece by piece (designed by Benjamin Vermeulen), as well as connections with which prefabricated furniture can be assembled without using bolts and nuts. Such joints have been made before, but 3D printing has greatly simplified their production.
Noah Raviv. Hard copy collection. 2014
Noah Raviv. Hard copy collection. 2014
Chromat. Formula 15 collection. Spring-summer 2015
Michael Schmidt, Francis Bitonti. Dita Von Teese dress. Laser printing (SLS). 2013
Iris van Herpen, Julia Koerner, Voltage Show. Print materialize. 2013
Iris van Herpen. Crystallization Collection. Summer 2010
Iris van Herpen. Autumn-Winter 2013-14
3D printers can print elements from which plastic fabric is then woven. Either from this fabric, or directly from plastic, dresses, bathing suits, shoes are created. Iris van Herpen has released several collections of 3D printed dresses and shoes. United Nude prints shoes designed by famous designers and architects: Zaha Hadid, Rem Koolhaas, Ross Lovegrove. But the most famous piece of clothing created using this technology is Dita Von Teese's mesh nylon dress.
#Cast is a custom tire consisting of the letters that the patient most often typed on Twitter. Manufacturer FATHOM, designer Eva DeCapri (USA). 2014
Prosthesis on the model of the patient's skull. Photo from Walter Reed Hospital in Washington
Arm splint. The developers are UCLA School of Architecture and Urban Planning students Nicholas Solakian, Peter Nguyen and Derek Buell. 2013
Medicine is the most promising application for 3D printing. By scanning the surface of the body, it is possible to create fixation bandages that exactly match the anatomy of a particular patient, “custom” prostheses and implants that reproduce lost parts of the skeleton. One unfortunate man who lost half of his face had the missing half printed on a 3D printer. There is no photo of this person here, but you can easily find it if you wish.
Printer self-reproduction
There are printers that can print parts of themselves. Undoubtedly, in the coming years they will learn to breed.
Growing donor organs
3D printing technologies for living tissues and organs are being developed. Living cells are used as the material, with which the printer "seeds" the matrix.
The text was first published in the online magazine of the Rizoma Design School, edited by Tatyana Bakina.
Artem Dezhurko
Art and design historian, exhibition consultant and curator, architectural journalist.
More
Fashion Architecture
Field of study
Fashion field at the HSE School of Design
HSE School of Design is a meeting place for the most talented students in Moscow and Russia who see their career in the fashion industry.