3D printing for investment casting
Investment Casting with 3D Printing Technology
3D printing technologies and materials produce innovative casting patterns that provide consistency and quality in cast components – both in terms of prototyping and low volume production.
Application OverviewInvestment casting is a manufacturing process (also known as lost wax casting) where a master pattern (traditionally made of wax) is covered with a ceramic slurry. Preheated wax is then melted out of its ceramic shell before molten metal is poured into it. The process generally provides higher accuracy and surface finish compared to other casting processes and is often used in applications that carry low volume production and changing product designs. 3D printed molds offer greater complexity, substantial time and cost savings when creating wax patterns for prototyping and short production runs.
Benefits of Using 3D Printing Technology
for Investment Casting
Freedom of Design
3D printing allows you to create more complex designs than a traditional investment casting process
Cost-Effective
3D printing can be a more cost-effective option than traditional tooling
Time
With 3D printing, you can reduce your time to part versus waiting for tooling to be made
Application
Wax patterns used in traditional investment casting methods are produced using an injection molding process, with costs ranging from $5,000 – $25,000 and lead times estimating at around two months. A major hindrance for companies is that investment casting foundries are unable to produce prototype castings until the injection mold is completed. 3D printing with FDM technology provides an alternate method for producing investment casting patterns that are a lot more efficient and cost-effective.
3D printing with FDM technology provides an alternate method for producing investment casting patterns that are a lot more efficient and cost-effective. A foundry can produce a pattern that also services as a prototype for form and fit evaluation in a single day, providing a perfect match to the casting that would be produced if that exact pattern were to be used. An FDM part’s durability allows it to be put into an assembly for testing while preventing damage that often occurs in transportation and handling. Due to FDM being an additive process, patterns can be as complex or as simple as needed, without any impact on cost.
Process
The wax patterns used in Investment Casting are produced with an injection molding process. FDM patterns are direct replacements for traditional parts that are injection molded but does not melt like wax. It burns, leaving a small amount of ash in the shell cavity which is then later removed in a shell washing operation. To speed the burnout of the FDM pattern, venting is added to ceramic shells. To prevent defects, patterns need to be produced to close tolerances and with excellent surface finish. Using our expert finishing services, hand finishing is not required on FDM parts, making this method a reliable and strong route in the Investment Casting market.
Looking to use 3D printing for Investment Casting?
Speak with one of our advanced manufacturing experts on how you can implement 3D printing technology for your investment casting application.
ASK AN EXPERT
Related Resources
Recommended Products for Investment Casting with 3D Printing
3D Printing & Foundries | Investment Casting Patterns | Stratasys Direct
- March 13, 2018
Industry Highlight: 3D Printing and Foundries
Metal casting at foundries is one of many tried and true manufacturing processes that have been impacted by 3D printing.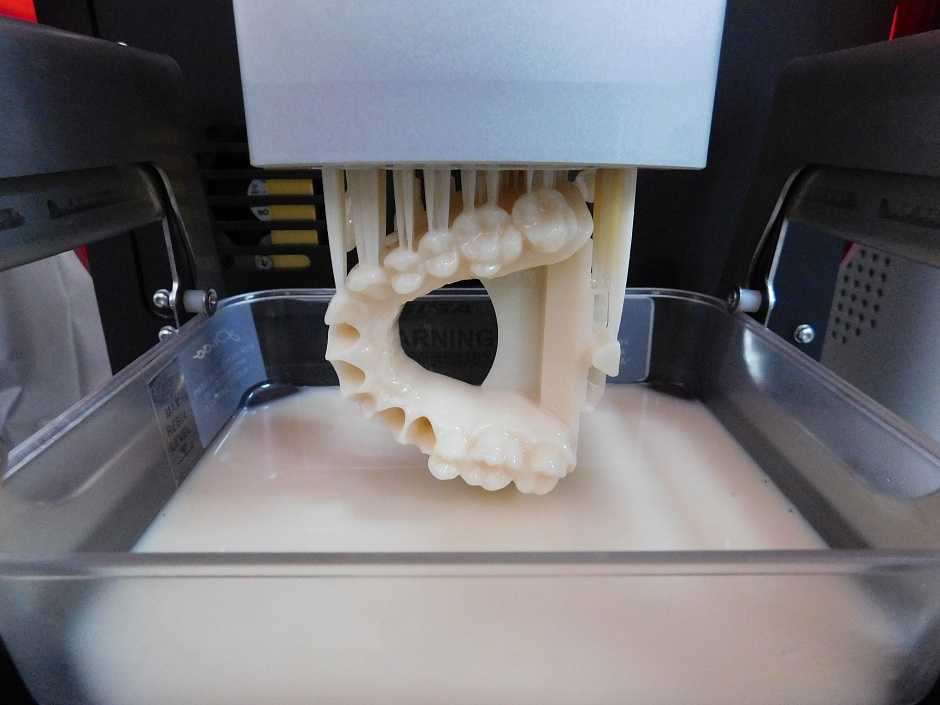
3D Printing Investment Casting Patterns
3D printing offers an effective tool-less solution for investment casting patterns with Stereolithography (SL). As an alternative to wax and wood, SL builds patterns with a UV laser that cures and solidifies thin layers of resin. Stratasys Direct builds SL investment casting patterns in a nearly hollow structure with a sparse internal lattice structure and thin walls. This proprietary build style translates to proportionately less ash and minimized thermal expansion forces during flash firing.
Stratasys Direct utilizes two Stereolithography materials for investment casting patterns. SC 1000P is a custom photopolymer formulation developed for low cost investment casting patterns. SC 1000P has low water absorption, and patterns built with this material are less prone to dimensional distortion. SOMOS® Element is a newer antimony-free formulation for investment casting patterns. This material is specifically used when a project calls for casting with reactive metal alloys where antimony may contaminate the cast metallurgical properties.
Stereolithography offers a new design freedom, unbound to tooling. Designs can be easily altered and gating systems can be proven out prior to tooling. SL delivers excellent pattern accuracy and repeatability, at less expense than conventional methods. These benefits translate to higher yields in the casting process and makes the piece easier to ship and more durable in-transit than a wax pattern.
Expertise in Action
Each foundry is unique, which is why we tailor the process and product for each customer’s distinctive operations. We work to fit into each customer’s unique operations by utilizing a successful process. We start by associating each project with lot sizes, materials, as-cast shrink compensation, surface roughness and dimensional requirements to ensure on-time delivery of quality patterns.
Then, printing parameters are customized to each pattern’s geometry and cast metal alloy. The patterns are optimized with low CTE, print time and material usage. Stratasys Direct has significant experience seamlessly bonding and assembling large SL patterns. Projects more than seven feet in diameter have been assembled with custom assembly fixtures and expertly delivered in large part packaging. We apply specific surface finishes to parts in order to work with foundry-specific face coats. Our sophisticated leak testing device checks each pattern for a perfect seal, and we offer vacuum ports and testing equipment for quality control at the foundry.
Custom Tools for Foundry Functions
Stratasys Direct offers a host of advanced manufacturing solutions for developing manufacturing tools and aids for foundry customers including hybrid wax setters, wax pattern assembly jigs, straightening fixtures, pattern and core inspection gauges, sand casting patterns, match-plates and core-boxes.
Our engineers are experts in examining a customer’s unique operations and identifying areas that custom jigs, fixtures and other manufacturing aids could transform your production floor.
Even with a centuries old manufacturing process, 3D printing can widen foundries customer base by offering a compatible processes and custom tools.
3D printers in the production of investment casting process
Basics of 3D
Casting
Author: Aleksey Chekhovich
Author: Aleksey Chekhovich
Basic steps of investment casting | The main advantages of 3D printing in comparison with traditional technologies | Examples of 3D printing in manufacturing
As already mentioned in the introductory article of our “casting” cycle, shell casting uses one-time models and molds. Today we will look at how additive technologies increase the efficiency of the investment casting process. This is one of the most accurate casting methods in the modern industry, allowing you to obtain products with tolerances of 100-200 microns.
Investment casting basic steps
- A sample model is being created.
- The specimen is attached to the sprue.
- The sample and sprue are lowered several times into the refractory material, creating a shape around the sample.
- The sample is removed from the refractory mold. The mold is ready for pouring metal.
- Metal is poured into a mould.
- After cooling, the mold material is removed by mechanical processing, chemical cleaning or dissolution in water.
- Parts are cut off from the sprue and lightly sanded.
The creation of new products, and especially casting parts, is the most time-consuming and expensive part of the technological process. In standard production, a new iteration of a product often requires new casting tooling as it is either too costly or impossible to upgrade an existing one.
It is not for nothing that additive technologies are called revolutionary: they have reduced the time for manufacturing products for pilot production by several times and even dozens of times. For example, a prototype car engine block can be 3D printed in just two weeks, while it takes six months to produce it using traditional methods. 3D printing not only saves time, but also allows you to grow models and shapes of any complexity. In casting, in this sense, the possibilities are limited.
When it comes to part precision, the application of 3D printing is also unmatched. This technology is most widely used in jewelry, dentistry, instrument making - in those industries where small dimensions and complex geometry of the product are a priority. In the manufacture of objects such as small machine parts, jewelry, dental prostheses or implants, particularly high precision and quality castings are required.
Photo 1. Models created on a 3D wax printer
Key advantages of 3D printing over traditional technologies
- High performance;
- increased accuracy;
- high quality;
- the possibility of round-the-clock operation;
- application of 3D printing materials with qualities optimized for specific applications.
Photo 2. Wax models printed on a FlashForge WaxJet 400 3D printer and finished jewelry
The construction of models in a 3D printer is carried out using MJP (MultiJet Printing) technology, based on multi-jet modeling using wax or photopolymer. This makes it possible to obtain models with high detail and excellent surface quality.
Examples of 3D printing in manufacturing
Photo 3. Model and casting of a component of gas turbine engines
American company Turbine Technologies, Ltd. developed a modification of internal combustion engines, on which high-pressure turbines are installed. The company purchased a 3D printer for printing wax models and receives a finished casting within 3-4 days. Wax models are now made directly from 3D CAD models, and Turbine Technologies' foundry produces gas turbine engine prototype components with greater accuracy and lower costs.
Photo 4. Goodwill Zvelitini's gold coin
And here is a unique example: for the 40th anniversary of the king of the South African Zulus tribe, Goodwill Zwelitini, a coin was cast from 18-carat gold. Its diameter is 100 mm, its thickness is 7 mm, and its weight is just under 0.5 kg. The manufacturer was challenged to print the coin in the shortest possible time, and thanks to the outstanding 3D printing capabilities, it was produced in just a week.
Photo 5. 3D-printed master model to obtain a silicone mold
Printing wax has its drawbacks. All costs for growing a wax model are borne by the final product, since the model is disposable and cannot be reused. iQB Technologies specialists decided to slightly modify the process, which allowed to reduce production costs. A model of a metal souvenir product was created at one of the Russian enterprises (see photo 5). In order not to pay for all the wax that is spent on each product, the model was 3D printed not from wax, but from plastic (photopolymer resin). Further creation of master models was carried out by melting wax and investment casting.
Let us dwell on this example in order to consider the entire technological process step by step.
After the plastic models are 3D printed, they are mounted on a slab.
Mounts are installed.
Forms are filled with silicone.
The silicone mass, as a rule, is highly susceptible to gassing, therefore, to remove air bubbles, the molds are placed in an impromptu degassing chamber.
When the polymerization of the silicone is completed, the flasks are removed. A plastic model is "walled up" inside the silicone.
This is followed by the most difficult stage - the separation of the silicone mold into pieces and the extraction of the master model.
The silicone mold is reassembled and casting wax is poured into it.
The mold is taken apart and wax master models are obtained, which are attached to the sprue riser (the so-called herringbone model assembly).
The Christmas tree is dipped in a special solution and sprinkled with ceramic sand - thereby creating a refractory shell around the model. Then the herringbone is heated, and all the wax flows out, leaving a cavity that exactly repeats the shape of the model. Metal is poured into it. The mold is destroyed, the finished castings are cut off from the sprue riser and cleaned.
The process is over - we have received the finished product.
And how are additive technologies used in the process of casting on burnt models? Read on our blog!
Article published on 02. 08.2017 , updated on 12.12.2022
An error occurred
Please try again later!
Investment casting material overview
To call this post a full-fledged review is probably not entirely correct, but nevertheless,
, at the very least, 2 castings from PLA, 2 castings from PMMA, one
casting from ABS and one from an unknown material took part in the experiment.
This story began with an Internet acquaintance with Evgeny Polyutsky
(http://3dtoday.ru/blogs/049f55549b/), who asked about the possibility of casting
a small gear for a R/C machine made of bronze. The story about the gear and its happy ending
can be read in Evgeny's group: (https://vk.com/3d_pechatnik)
The local 3D printing center printed 4 copies of the required PLA gear for me.
The result is visible in the photo, the print quality, it seemed to me, is not very good, but the part
is small, and I was more interested in what would come of it.
Well, what they printed, they cast: D
Then this story was continued by a certain Moscow 3D printing center, with a proposal
to cast their printout from PMMA (if anyone is interested, they can google what kind of material
is and what it is used for ).
Christmas Tree:
Molded:
This product is not very functional, but it perfectly demonstrates the possibilities
technology: it is almost impossible to remove the mold and get a copy, but it's easy to print and
to cast!
This figure was received in exchange for the previous casting, also made of PMMA:
Cast (about 980 grams, bronze): casting system.
Next in line is unknown material that came to me through two hands, from some
an office supposedly engaged in the development of a burnable photopolymer, and
needed a check according to the standard annealing and pouring modes. I must say right away that it didn’t work :)
Cast together on the same Christmas tree with our serial products, everything is in order with ours
- trouble with printouts: holes, artifacts, clumsy surface.
I suspect that this material requires special firing conditions that we were not told about
.
Next came our good friend, whom I promised to help with a diploma, the topic
of which was precisely 3D printing with subsequent casting, the advantages and
strengths of this technology. In general, demonstration materials were needed:
printouts from PLA and their copies already in bronze. As usual, they made it to the last, threw
a cry in the ads here on the portal .... So I met Ilya
(http://3dtoday.ru/blogs/eta4ever/), Ilya promptly printed two Aztecs and two turbines,
for which many thanks to him!
The diploma was passed in triumph, there was essentially no protection: D
And the ABS review concludes, the quality of the casting is worse than that of PLA, but has the right to life.