3D printers making organs
3D-printed organs: The future of transplantation
CNN —
What if doctors could just print a kidney, using cells from the patient, instead of having to find a donor match and hope the patient’s body doesn’t reject the transplanted kidney?
The soonest that could happen is in a decade, thanks to 3D organ bioprinting, said Jennifer Lewis, a professor at Harvard University’s Wyss Institute for Biologically Inspired Engineering. Organ bioprinting is the use of 3D-printing technologies to assemble multiple cell types, growth factors and biomaterials in a layer-by-layer fashion to produce bioartificial organs that ideally imitate their natural counterparts, according to a 2019 study.
This type of regenerative medicine is in the development stage, and the driving force behind this innovation is “real human need,” Lewis said.
In the United States, there are 106,075 men, women and children on the national organ transplant waiting list as of June 10, according to the Health Resources & Services Administration. However, living donors provide only around 6,000 organs per year on average, and there are about 8,000 deceased donors annually who each provide 3.5 organs on average.
47-year-old Steve Verze is to become the first man in the world to be fitted with a 3D printed eye, according to Moorfields Eye Hospital. He tried the eye for size earlier this month, as photographed here.
British man given 3D printed eye in world first, hospital says
The cause of this discrepancy is “a combination of people who undergo catastrophic health events, but their organs aren’t high enough quality to donate, or they’re not on the organ donor list to begin with, and the fact that it’s actually very difficult to find a good match” so the patient’s body doesn’t reject the transplanted organ, Lewis said.
And even though living donors are an option, “to do surgery on someone who doesn’t need it” is a big risk, said Dr. Anthony Atala, director of the Wake Forest Institute for Regenerative Medicine. “So, living related donors are usually not the preferred way to go because then you’re taking an organ away from somebody else who may need it, especially now as we age longer.”
Atala and his colleagues were responsible for growing human bladders in a lab by hand in 2006, and implanting a complicated internal organ into people for the first time – saving the lives of three children in whom they implanted the bladders.
A bladder scaffold is seeded with cells at the Wake Forest Institute for Regenerative Medicine.
Courtesy Wake Forest Institute for Regenerative Medicine Every day, 17 people die waiting for an organ transplant, according to the Health Resources & Services Administration. And every nine minutes, another person is added to the waitlist, the agency says. More than 90% of the people on the transplant list in 2021 needed a kidney.
“About a million people worldwide are in need of a kidney. So they have end-stage renal failure, and they have to go on dialysis,” Lewis said. “Once you go on dialysis, you have essentially five years to live, and every year, your mortality rate increases by 15%. Dialysis is very hard on your body. So this is really motivating to take on this grand challenge of printing organs.”
“Anti-hypertensive pills are not scarce. Everybody who needs them can get them,” Martine Rothblatt, CEO and chairman of United Therapeutics, said at the Life Itself conference, a health and wellness event presented in partnership with CNN. United Therapeutics is one of the conference’s sponsors.
“There is no practical reason why anybody who needs a kidney – or a lung, a heart, a liver – should not be able to get one,” she added. “We’re using technology to solve this problem.”
To begin the process of bioprinting an organ, doctors typically start with a patient’s own cells. They take a small needle biopsy of an organ or do a minimally invasive surgical procedure that removes a small piece of tissue, “less than half the size of a postage stamp,” Atala said. “By taking this small piece of tissue, we are able to tease cells apart (and) we grow and expand the cells outside the body. ”
This growth happens inside a sterile incubator or bioreactor, a pressurized stainless steel vessel that helps the cells stay fed with nutrients – called “media” – the doctors feed them every 24 hours, since cells have their own metabolism, Lewis said. Each cell type has a different media, and the incubator or bioreactor acts as an oven-like device mimicking the internal temperature and oxygenation of the human body, Atala said.
“Then we mix it with this gel, which is like a glue,” Atala said. “Every organ in your body has the cells and the glue that holds it together. Basically, that’s also called ‘extracellular matrix. ’ ”
Richard Roth with Samira Jafari
Courtesy Samira JafariLiving organ donations save lives. This is how you become a donor
This glue is Atala’s nickname for bioink, a printable mixture of living cells, water-rich molecules called hydrogels, and the media and growth factors that help the cells continue to proliferate and differentiate, Lewis said. The hydrogels mimic the human body’s extracellular matrix, which contains substances including proteins, collagen and hyaluronic acid.
The non-cell sample portion of the glue can be made in a lab, and “is going to have the same properties of the tissue you’re trying to replace,” Atala said.
The biomaterials used typically have to be nontoxic, biodegradable and biocompatible to avoid a negative immune response, Lewis said. Collagen and gelatin are two of the most common biomaterials used for bioprinting tissues or organs.
From there, doctors load each bioink – depending on how many cell types they’re wanting to print – into a printing chamber, “using a printhead and nozzle to extrude an ink and build the material up layer by layer,” Lewis said. Creating tissue with personalized properties is enabled by printers being programmed with a patient’s imaging data from X-rays or scans, Atala said.
“With a color printer you have several different cartridges, and each cartridge is printing a different color, and you come up with your (final) color,” Atala added. Bioprinting is the same; you’re just using cells instead of traditional inks.
How long the printing process takes depends on several factors, including the organ or tissue being printed, the fineness of the resolution and the number of printheads needed, Lewis said. But it typically lasts a few to several hours. The time from the biopsy to the implantation is about four to six weeks, Atala said.
A 3D printer seeds different types of cells onto a kidney scaffold at the Wake Forest Institute for Regenerative Medicine.
The ultimate challenge is “getting the organs to actually function as they should,” so accomplishing that “is the holy grail,” Lewis said.
“Just like if you were to harvest an organ from a donor, you have to immediately get that organ into a bioreactor and start perfusing it or the cells die,” she added. To perfuse an organ is to supply it with fluid, usually blood or a blood substitute, by circulating it through blood vessels or other channels.
Depending on the organ’s complexity, there is sometimes a need to mature the tissue further in a bioreactor or further drive connections, Lewis said. “There’s just a number of plumbing issues and challenges that have to be done in order to make that printed organ actually function like a human organ would in vivo (meaning in the body). And honestly, this has not been fully solved yet.”
Once a bioprinted organ is implanted into a patient, it will naturally degrade over time – which is OK since that’s how it’s designed to work.
“You’re probably wondering, ‘Well, then what happens to the tissue? Will it fall apart?’ Actually, no,” Atala said. “These glues dissolve, and the cells sense that the bridge is giving way; they sense that they don’t have a firm footing anymore. So cells do what they do in your very own body, which is to create their own bridge and create their own glue.”
Atala and Lewis are conservative in their estimates about the number of years remaining before fully functioning bioprinted organs can be implanted into humans.
“The field’s moving fast, but I mean, I think we’re talking about a decade plus, even with all of the tremendous progress that’s been made,” Lewis said.
“I learned so many years ago never to predict because you’ll always be wrong,” Atala said. “There’s so many factors in terms of manufacturing and the (US Food and Drug Administration regulation). At the end of the day, our interest, of course, is to make sure the technologies are safe for the patient above all.”
Whenever bioprinting organs becomes an available option, affordability for patients and their caregivers shouldn’t be an issue.
They’ll be “accessible for sure,” Atala said. “The costs associated with organ failures are very high. Just to keep a patient on dialysis is over a quarter of a million dollars per year, just to keep one patient on dialysis. So, it’s a lot cheaper to create an organ that you can implant into the patient. ”
The average kidney transplant cost was $442,500 in 2020, according to research published by the American Society of Nephrology – while 3D printers retail for around a few thousand dollars to upward of $100,000, depending on their complexity. But even though low-cost printers are available, pricey parts of bioprinting can include maintaining cell banks for patients, culturing cells and safely handling biological materials, Lewis said.
Some of the major costs of current organ transplantation are “harvesting the organ from the donor, the transport costs and then, of course, the surgery that the recipient goes through, and then all the care and monitoring,” Lewis said. “Some of that cost would still be in play, even if it was bioprinted.”
On the Road to 3-D Printed Organs
For years, scientists have predicted that 3-D printing—which has been used it to make toys, homes, scientific tools and even a plastic bunny that contained a DNA code for its own replication—could one day be harnessed to print live, human body parts to mitigate a shortage of donor organs. So far, researchers also used 3-D printing in medicine and dentistry to create dental implants, prosthetics, and models for surgeons to practice on before they make cuts on a patient. But many researchers have moved beyond printing with plastics and metals—printing with cells that then form living human tissues.
No one has printed fully functional, transplantable human organs just yet, but scientists are getting closer, making pieces of tissue that can be used to test drugs and designing methods to overcome the challenges of recreating the body’s complex biology.
First steps
A confocal microscopy image showing 3-D–printed stem cells differentiating into bone cells
LEWIS LAB, WYSS INSTITUTE AT HARVARD UNIVERSITY
The first 3-D printer was developed in the late 1980s. It could print small objects designed using computer-aided design (CAD) software. A design would be virtually sliced into layers only three-thousandths of a millimeter thick. Then, the printer would piece that design into the complete product.
There were two main strategies a printer might use to lay down the pattern: it could extrude a paste through a very fine tip, printing the design starting with the bottom layer and working upward with each layer being supported by the previous layers. Alternatively, it could start with a container filled with resin and use a pointed laser to solidify portions of that resin to create a solid object from the top down, which would be lifted and removed from the surrounding resin.
When it comes to printing cells and biomaterials to make replicas of body parts and organs, these same two strategies apply, but the ability to work with biological materials in this way has required input from cell biologists, engineers, developmental biologists, materials scientists, and others.
So far, scientists have printed mini organoids and microfluidics models of tissues, also known as organs on chips. Both have yielded practical and theoretical insights into the function of the human body. Some of these models are used by pharmaceutical companies to test drugs before moving on to animal studies and eventually clinical trials. One group, for example, printed cardiac cells on a chip and connected it to a bioreactor before using it to test the cardiac toxicity of a well-known cancer drug, doxorubicin. The team showed that the cells beating rate decreased dramatically after exposure to the drug.
However, scientists have yet to construct organs that truly replicate the myriad structural characteristics and functions of human tissues. “There are a number of companies who are attempting to do things like 3-D print ears,” and researchers have already reported transplanting 3-D printed ears onto children who had birth defects that left their ears underdeveloped, notes Robby Bowles, a bioengineer at the University of Utah. The ear transplants are, he says, “kind of the first proof of concept of 3-D printing for medicine.”
Researchers have been using 3D-printing techniques in hopes of developing tissues that can be transplanted into humans. Some printed tissues, such as skin and bone, are already being tested in humans, while many others are early in development.
See full caption
THE SCIENTIST STAFF
Bowles adds that researchers are still “a ways away” from printing more-complex tissues and organs that can be transplanted into living organisms. But, for many scientists, that’s precisely the goal. As of February 2020, more than 112,000 people in the US are waiting for an organ transplant, according to the United Network for Organ Sharing. About 20 of them die each day.
For many years, biological engineers have tried to build 3-D scaffolds that they could seed with stem cells that would eventually differentiate and grow into the shapes of organs, but “to a large extent those techniques don’t allow you to introduce kind of the organization of gradients and the patterning that is in the tissue,” says Bowles. “There is no control over where the cells go in that tissue.” By contrast, 3-D printing enables researchers with to very precisely direct the placement of cells—a feat that could lead to better control over organ development.
Differentiation
Ideally, 3-D printed organs would be built from cells that a patient’s immune system could recognize as its own, to avoid immune rejection and the need for patients to take immunosuppressive drugs. Such organs could potentially be built from patient-specific induced pluripotent stem cells, but one challenge is getting the cells to differentiate into the subtype of mature cell that’s needed to build a particular organ. “The difficulty is kind of coming together and producing complex patternings of cells and biomaterials together to produce different functions of the different tissues and organs,” says Bowles.
To imitate the patterns seen in vivo, scientists print cells into hydrogels or other environments with molecular signals and gradients designed to coax the cells into organizing themselves into lifelike organs. Scientists can use 3-D printing to build these hydrogels as well. With other techniques, “the patterns achieved have typically been two-dimensional,” Eben Alsberg, a bioengineer at the University of Illinois, tells The Scientist in an email. “Three-dimensional bioprinting permits much more control over signal presentation in 3D.”
So far, researchers have created patches of tissue that mimic portions of certain organs but haven’t managed to replicate the complexity or cell density of a full organ. But it’s possible that in some patients, even a patch would be an effective treatment. At the end of 2016, a company called Organovo announced the start of a program to develop 3-D printed liver tissue for human transplants after a study showed that transplanted patches of 3-D printed liver cells successfully engrafted in a mouse model of a genetic liver disease and boosted several biomarkers that suggested an improvement in liver function.
Vasculature
Only in the past few years have researchers started to make headway with one of the biggest challenges in printing 3-D organs: creating vasculature. After the patches were engrafted into the mouse’s liver in the Organovo study, blood was delivered to it by the surrounding liver tissue, but an entire organ would need to come prepared for blood flow.
“For any cells to stay alive, [the organ] needs that blood supply, so it can’t just be this huge chunk of tissue,” says Courtney Gegg, a senior director of tissue engineering at Prellis Biologics, which makes and sells scaffolds to support 3-D printed tissue. “That’s been recognized as one of the key issues.”
Mark Skylar-Scott, a bioengineer at the Wyss Institute, says that the problem has “held back tissue engineering for decades.” But in 2018, Sébastian Uzel, Skylar-Scott, and a team at the Wyss Institute managed to 3-D print a tiny, beating heart ventricle complete with blood vessels. A few days after printing the tissue, Uzel says he came into the lab to find a piece of twitching tissue, which was both “very terrifying and exciting.”
For any cells to stay alive, [the organ] needs that blood supply, so it can’t just be this huge chunk of tissue.
![]()
—Courtney Gegg, Prellis Biologics
Instead of printing the veins in layers, the team used embedded printing—a technique in which, instead of building from the bottom of a slide upwards, material is extruded directly into a bath, or matrix. This strategy, which allows the researchers to print “free form in 3-D,” says Skylar-Scott, rather having to print each layer one on top of the other to support the structure, is a more efficient way to print a vascular tree. The matrix in this case was the cellular material that made up the heart ventricle. A gelatin-like ink pushed these cells gently out of the way to create a network of channels. Once printing was finished, the combination was warmed up. This heat caused the cellular matrix to solidify, but the gelatin to liquify so it could then be rinsed out, leaving space for blood to flow through.
But that doesn’t mean the problem is completely solved. The Wyss Institute team’s ventricle had blood vessels, but not nearly as many as a full-sized heart. Gegg points out that to truly imitate human biology, “an individual cell will have to be within 200 microns of your nearest blood supply. . . . Everything has to be very, very close.” That’s far more intricate than what researchers have printed so far.
Due to hurdles with adding vasculature and many other challenges that still face 3-D–printed tissues, laboratory-built organs won’t be available for transplant anytime soon. In the meantime, 3-D printing portions of tissue is helping accelerate both basic and clinical research about the human body.
Emma Yasinski is a Florida-based freelance reporter. Follow her on Twitter @EmmaYas24.
When will we be able to print new organs on a 3D printer? In China alone, there are 1.5 million people on the waiting list, in the United States - 113 thousand, of which, on average, 20 people die a day without waiting for a donor. A new kidney - the most demanded organ - has to wait from three to five years. This problem can be solved by printing the necessary organs on special 3D printers.
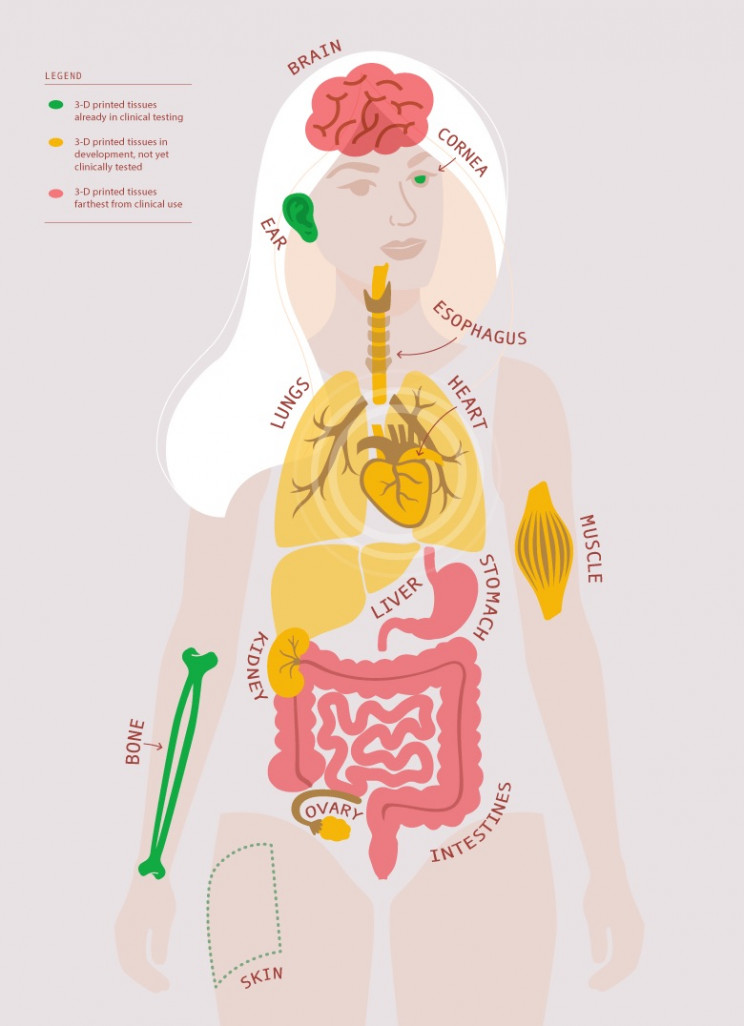
True, not earlier than the next ten years.
Bioprinting technology: how and why are organs printed today?
(Video: RBC)
The principle is about the same as in conventional 3D printing: we get a three-dimensional object on a special printer.
The first stage is preprinting : first, a digital model of the future organ or tissue is created. For this, images obtained on MRI or CT are used.
Then they print, layer by layer - this technology is called additive. Only instead of a conventional 3D printer, there is a special bioprinter, and instead of ink, there are biomaterials. These can be human stem cells, which in the body perform the role of any cells; porcine collagen protein or seaweed-based cell material.
If the cells are alive, they are biopsied and prepared in a bioreactor until they multiply by division to the desired number. During printing, the bioprinter polymerizes the cellular structure - that is, binds it with the help of ultraviolet light, heating or cooling. Cell layers are connected using a hydrogel - organic or artificial.
The resulting structure is then placed in a biological environment where it "ripens" before transplanting. This is the longest stage: it can last several weeks. During this time, the structure stabilizes, and the cells are ready to perform their functions.
Then the organ is transplanted and they monitor how it takes root.
Bioprinting: how living organs are printed on a 3D printer
(Video: RBC)
In addition to conventional additive bioprinters, there are other bioprinters. Some of them print collagen directly on an open wound: this way you can quickly build up new skin even in the field. In this case, the ripening (post-printing) step is skipped.
There are also printers that print in outer space, in zero gravity. In the future, they can be used on the ISS:
There are more than 100 companies in the world that produce 3D bioprinters. 39% of them are in the USA, 35% are in Europe (of which more than half are in France and Germany), 17% are in Asia, 5% are in Latin America.
In Russia, bioprinters are produced by 3D Bioprinting Solutions, which is also engaged in research in the field of bioprinting.
The cheapest and most compact bioprinter - Tissue Scribe by American 3D Cultures, costs from $1.5 thousand
In second place - Australian Rastrum from Inventia for $5,000.
Aether bioprinter from the USA can be bought from $9,000. biosystems.
3D Bioplotters from the German EnvisionTEC cost from $100,000, and the Russian FABION (3D Bioprinting Solutions) is even more expensive.
Finally, the most expensive bioprinters — more than $200,000 — are NovoGen MMX from Organovo (USA) and NGB-R from Poietis (France).
In addition to the cost of the printer, the printing process itself is an additional 15-20% of the cost of the entire project. It will cost even more to obtain the necessary cell material.
So far, the most successful experience has been the transplantation of cartilage - the very ears of Chinese children.
Small artificial cell bones are printed on a printer and then coated with a layer. They are planned to be transplanted instead of a broken or damaged area, after which they completely regenerate in three months. In the future, they want to use the technology for spinal injuries.
The most promising direction is 3D printing of leather. Already in five years they promise that this can be done directly on a person, over or instead of the damaged area. Skin and other tissues are being printed from cells from cancer patients to test various therapies.
More complex organs, such as kidneys or hearts, have so far only been printed as prototypes or transplanted into mice, not humans.
In order for the organs to take root and function well in the human body, they take the patient's cells, and then they divide until they are enough for printing. There are entire institutes that create cell lines for bioprinting. But the problem is that cells have a division limit, after which they are no longer usable. Therefore, it is possible to print a model of the heart, but not life-size - that is, it is not suitable for transplantation into a person.
The second problem is that the printed organ must function in conjunction with the rest of the body : digest food, secrete hormones, deliver blood and oxygen. A complex system of cells, tissues, nerves and blood vessels is responsible for all this. So far, it has not been possible to reproduce it exactly.
Finally, bioprinting technologies are not yet regulated in any way. All research must go through all stages of testing, including on humans, and then obtaining patents.
So far, experts predict the introduction of technology not earlier than in 10-15 years. By then, bioprinters and cellular materials will be widely available, and even the most remote regions will be able to use bioprinting.
More to read:
- History and technology of bioprinting (ENG)
- Overview of the current state of bioprinting and major challenges
- How bioprinting will change our lives (ENG)
- Video: what the bioprinting process looks like (ENG)
- Video: Graphic explaining the printing process from living cells (ENG)
- Video: Ear 3D printing (ENG)
Subscribe and follow us on Yandex.Zen — technology, innovation, economics, education and sharing in one channel.
Printing organs: how ears, skin and noses are made with a 3D printer
- Natalka Pisnya
- BBC Russian Service, USA
Subscribe to our “Context” newsletter: it will help you understand the events.
Image copyright, Masela family archive
Photo caption, Luc Masela with his parents one month after the artificial bladder transplant. year 2001.
Luc Masela, now 27, is an athlete with a degree in economics, works for a large exhibition company, travels a lot and recently met, in his words, "the most beautiful girl in the world." Both she and most of his current friends were extremely surprised when they learned that 17 years ago he survived a dozen and a half operations.
Luke was born with spina bifida - and although he was able to walk, his bladder was severely damaged. By the age of 10, he almost did not leave hospitals: due to improper functioning of the bladder, fluid began to return to the boy's kidneys, doctors diagnosed an irreversible pathology of the organ.
You need JavaScript enabled or a different browser to view this content
Video caption,"3D printed" organs are here
Doctors offered the family two solutions: lifelong dialysis or the creation of a new bladder from a segment of the intestine. This would guarantee Luke several years of medically supervised life and a high risk of developing cancer.
The urologist who was taking care of the boy invited the Masela family to take part in an experimental program: to grow a new bladder from his own cells. Then, in 2001, it sounded like science fiction: only nine people took part in the program before Luke. Despite this, his family agreed.
"The essence of the operation was reduced to two stages: first, a piece of bladder tissue was taken from me, and over the next two months, cells were grown in the laboratory in order to grow a new healthy bladder from them," says Luke.
Photo copyright, Masela family archive
Photo caption,Luc Masela, 17 years after his artificial bladder transplant
Next came the transplant, which he said took 16 hours. “I opened my eyes and saw a cut through my entire stomach, tubes of all possible sizes were sticking out of me, except for them - four IVs and a bottle-feeding machine,” he recalls. “I stayed in the hospital for another month, I was prescribed bed rest, after that I stayed at home for another month.
The operation was performed by Dr. Anthony Atala, Pediatric Regenerative Surgeon. In two months, out of a hundred patient cells, scientists created one and a half billion. Further, an engineering structure was created on a collagen frame: the bladder was “sculpted” like a two-layer pie, the core of which dissolved over time, and it started working like a normal organ, taking root thanks to Luke’s own cells.
- An animal capable of regrowing its head
- The birth of a chimera: why do scientists need a human-animal hybrid?
- Swedish company 3D prints body parts
Luke and Dr. Atala haven't seen each other for 10 years after being discharged from the hospital. Once a dying child became the champion of the school wrestling team and went to college.
The professor took charge of the Wake Forest Institute of Regenerative Medicine in North Carolina in those 10 years, but he never forgot about Luke: his bladder was one of the most challenging and most successful projects in his early practice.
By 2018, Atala won the Christopher Columbus Prize for "work on a discovery that will have a significant impact on society"; The Times and Scientific American magazines at various times named him "Physician of the Year", he was also recognized as "one of the 50 scientists on the planet who in the next 10 years will change the way we live and work."
How to print a new face
Skip the Podcast and continue reading.
Podcast
What was that?
We quickly, simply and clearly explain what happened, why it's important and what's next.
episodes
The End of the Story Podcast
In the mid-2000s, Atala's team turned their attention to an ordinary household 3D printer and wrote special software for it, later specialized machines were created for the laboratory. Now the laboratory "grows" up to 30 different types of cells and organs, as well as cartilage and bones.
One of the team's latest achievements is ears and noses grown outside the human body.
The main customer and sponsor of Atala's developments is the US Department of Defense, and many of the patients are military victims of military operations.
It works like this: first, a CT scan of the ear or nose is done. One of Atala's assistants, Joshua Corpus, jokes that at this stage, people often ask to "improve" the shape of the nose if they thought theirs was too wide or hooked, and the ears if they were too wide.
After that, a special computer code is written, and the printing of the basis of the organs begins.
For this, a bioresorbable polymer, polycaprolactam, is used. At the same time flexible and durable, in the human body it disintegrates within four years.
After printing, the layers of polycaprolactam resemble lace; after transplantation, after a few years, their place will be taken by the person's own cartilage tissues.
Polycaprolactam is then saturated with a gel created from the patient's cells, cooled to -18 degrees Celsius - so the cells, according to scientists, are not damaged, they are "alive and happy."
Image caption,Printing a test kidney sample on a bioprinter
In order for the polymer and gel structure to take shape and become something more durable, ultraviolet light is used in the laboratory - it does not damage cells.
The future implant is printed for 4-5 hours, then it is finally formed and inserted under the epidermis.
Skin can also be grown: children affected by fires were the first to take part in the early trials of Atala - after the "printing" of the skin, scientists observed the patients for several more years. The new skin did not crack, did not burst, and grew with the children.
The most difficult job, according to the scientist, is facial wounds: it's not enough just to stretch the skin, you need to accurately calculate the geometry, align swelling, bone structure, and understand how a person will look after that.
In addition to the skin and ears, Atala can "print" the bones of the jaws, grow blood vessels and cells of some organs - the liver, kidneys, lungs.
This technology is especially appreciated by oncologists: on the basis of patient cells, it is possible to recreate the body's response to various types of chemotherapy and observe the reaction to a particular type of treatment in the laboratory, and not on a living person.
But the liver, kidneys, lungs and heart are still being tested. Atala says he raised them in miniature, but creating organs from various tissues to real size requires a lot of additional research.
But, according to him, cells were grown in the laboratory and a vagina was created for a girl who was born several years ago with a congenital deformity of the genital organs - several years have passed since the transplant.
Image caption,Bioprinted polycaprolactam ear implant base
Atala smiles and adds that his team is also working on a working penis. This research has been going on for several years, and the most troublesome for scientists is the complex structure of tissues and the specific sensitivity of the organ itself.
Among others, Igor Vasyutin, a Russian post-graduate student of the First Moscow State Medical University (MSMU) named after Sechenov, is working on this under laboratory conditions. He is a cell biologist, Atala's right hand.
Vasyutin has been in the USA for about a year - he came on an exchange. He is ready to talk about the behavior of stem cells for hours, but becomes less verbose when it comes to Russian science.
Vasyutin's alma mater has not reached mass regeneration of human organs and is still training on animals: local scientists "printed" a mouse thyroid gland on a 3D printer.
They are also involved in the study of human organs. According to the head of the Institute of Regenerative Medicine at MSMU Denis Butnar, several years ago the Institute recreated a special engineering design of the buccal mucosa. She functioned perfectly for the first six months, but subsequently had to undergo a second operation.
Image caption,Test specimen of an ear implant exposed to ultraviolet light
In Russia, however, over the past few years, the Italian surgeon-transplantologist Paolo Macchiarini has been practicing, the man who was the first in history to perform a synthetic organ transplant operation - a plastic tube that replaced the patient trachea.
- Paolo Macchiarini: the rise and fall of the famous surgeon
However, seven of his nine patients died, and the breathing tubes implanted in the remaining two subsequently had to be replaced with donor ones.
Several criminal cases were brought against him, including on charges of pressure on patients and fraud, and the world's leading doctors called Macchiarini's operations "ethical Chernobyl."
Will printed organs replace donors?
At the zenith of his career, Macchiarini argued that a new perspective is opening up for humanity: you can "print" any human organ on a printer, create an engineering structure from it, enriched with the patient's stem cells, and get the perfect prosthesis.
Be that as it may, complex human organs - the liver, kidneys, heart, lungs - have not yet been able to grow any regenerative surgeon.
Bioprinting of the so-called simple organs, however, is already available in the US, Sweden, Spain and Israel - at the level of clinical trials and special programs.
The US government is actively investing in such programs - in addition to Wake Forest, cooperating with the Pentagon, the Massachusetts Institute of Technology also receives significant amounts to recreate the work of the liver, heart and lungs.
Skin application test on a burnt wound
According to Professor Jorge Raquela, a gastroenterologist at the Mayo Clinic Research Center, "Bioprinting is one of the most exciting branches of modern medicine, it has huge potential, and the turning point of the most important discoveries is already close."
Meanwhile, Pete Basillier, head of R&D at analytics firm Gartner, insists technology is advancing much faster than understanding the implications of 3D printing.
Such developments, according to Basilière, even if created with the best of intentions, give rise to a set of questions: what will happen when "improved" organs are created, the basis of which will not only be human cells - will they have "superpowers"? Will a regulatory body be created to monitor their production? Who will check the quality of these organs?
More than 150,000 Americans are on the waiting list for organ transplants every year, according to a report from the US National Library of Medicine. Donor organs will receive only 18% of them; every day in the United States, without waiting for a transplant, 25 people die. Organ transplants and subsequent rehabilitation cost insurance companies and patients $300 billion in 2012 alone.
- A 3D printer helped a cyclist who lost his jaw
- Genetically modified pigs - human organ donors?
- The world's first child with both hands transplanted plays baseball
Most Americans are potential donors: upon obtaining a driver's license, they voluntarily answer the question of whether they agree to donate their organs in the event of a car accident or other dangerous incident . In case of consent, a small "heart" and the word "donor" appear in the corner of the document.
Professor Atala's driver's license is like that - despite all his achievements and faith in the "publishing organs", he is ready to share his with those around him.