3D printed underwater drone
CPSdrone – Making Underwater Drones
Start building now
Build your own
underwater drone
You can buy flying drones and build them for cheap. Let’s make the same for underwater!
Start building now
AS FEATURED ON:
What will you get?
CPS 5 Course is the world’s first DIY course on underwater drones.
Bill Of Materials
A complete list of every component needed for the underwater drone build, with online source links.
3D Models
STL files, GCODEs for Prusa 3D printers as well as CAD files for modeling programs.
Assembly Manual
Easy to follow instructions explaining how to build the CPS 5 underwater drone from scratch.
Video Lessons
Educational videos explaining the engineering behind all of our design decisions.
13 Chapters
Knowledge divided into 13 sections, each one covering the next part of the drone, with the final assembly at the end.
Our Support
We care about your progress in the course, that’s why we help you with your build either directly or in a discussion section located in every lesson.
Bill Of Materials
A complete list of every component needed for the underwater drone build, with online source links.
3D Models
STL files, GCODEs for Prusa 3D printers as well as CAD files for modeling programs.
Assembly Manual
Easy to follow instructions explaining how to build the CPS 5 underwater drone from scratch.
Video Lessons
Educational videos explaining the engineering behind all of our design decisions.
13 Chapters
Knowledge divided into 13 sections, each one covering the next part of the drone, with the final assembly at the end.
Our Support
We care about your progress in the course, that’s why we help you with your build either directly or in a discussion section located in every lesson.
Start building now
What will you build?
CPS 5 (Custom Printed Submarine) is a fully functional, 3D printed underwater drone. All of the components cost ~$700 (+VAT in EU).
85 meters Depth
We’ve tested CPS 5 up to simulated pressure of 85 meters underwater. It’s possible with our own watertight endcap design.
3D Printed
The majority of the drone is 3D printed – the entirety of the shell, propellers, mounts as well as water-proof endcaps.
Fast & Maneuverable
With top speed of 2m/s, CPS 5 is really maneuverable. It also has active self-leveling, which we test in the video below:
Live Video Feed
QGroundControl app which displays all of the data and the 1080p live video feed from the drone’s camera onboard.
Start building now
Ready to build a fully functional ROV?
Join today and get our entire 4 years (14 prototypes) of experience in just 1 extensive course.
Lifetime access
- Lifetime Unlimited Access!
- ALL 11 Chapters (73 lessons)
- Video lessons
- "How to do it differently" lessons
- Assembly manuals
- BOM (Bill Of Materials)
- 3D models
- Our great support
Price:
✅ 14-day money-back guarantee
Free Sample
- 1 Chapter
- BOM (Bill Of Materials)
- Explanation of the drone's structure
- Course essentials list
- Newsletter
Price:
No credit card required
Who are we?
Hello, my name is Filip Buława (left) and Peter’s name is Piotr Domanowski (right). We make underwater drones for 4 years already, since 2018.
We’ve started back in high-school in our home town in Poland. Back then it was just another cool 3D printing project for a competition.
Our first prototype, 2018
Our first school presentation about 3D printing
We’ve then decided to continue our project by making new prototypes for new competitions.
Our winning project for E(x)plory competition
Us just before winning a prize at REGENERON ISEF 2021
After over 2 years of us desperately trying to fund the project to make the drone actually usable, we’ve finally started making the online course.
We’ve moved to Gdańsk, where we have the Polish sea
Us at Maker Faire Prague in 2022
Our mission is to make building underwater drones as cool as the flying ones. You can help us by donating!
Facebook Youtube Instagram Envelope
Italy's WitLab Creates 3D Printed ArcheoRov, Ready for Underwater Archaeological Expeditions - 3DPrint.
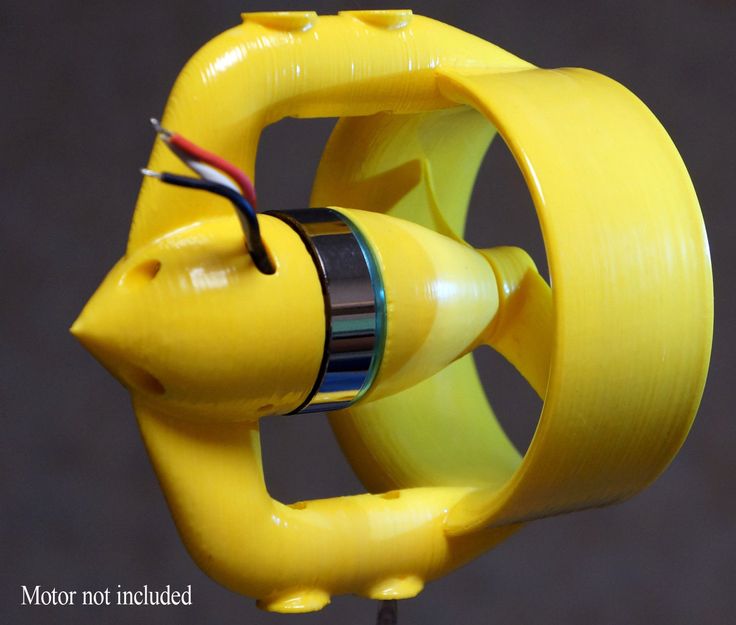
I really enjoy learning, and writing, about drones. There are a lot of applications for drone technology, ranging from the more mundane (but fun!) pizza delivery to cutting-edge drones being used as first responders in search and rescue operations. So, what’s even cooler than a drone flying through the air? Drones swimming through the water, of course!
We’ve seen drone technology and additive manufacturing used to help make the NEMO (Nautical Exploratory Modular Observer) and the Blue Robotics submarine drone with 3D printed thruster, and who could forget the CRACUNS submersible drone that can go straight from underwater to high in the air? Now, Italy-based WitLab has taken to the water as well – meet the 3D printed ArcheoRov.
ArcheoRov [Image: Maritime Journal]
The ArcheoRov is an underwater ROV (Remote Operated Vehicle). It doesn’t seem too intimidating at first – it’s less than 60cm long, and it’s not super speedy. But it can “swim” like a fish, instead of remaining stationary in one spot, and is 3D printed. WitLab’s Dr. Emanuele Rocco, one of the creators of ArcheoRov, explained that what’s really impressive about it is the acceleration of the design – from concept to delivery, the customized ArcheoRov only took ten weeks.
ArcheoRov was built in the Roverto WitLab, which is in the green Manufacturing Project incubator of Trentino Development. It was designed and built for Arc-Team, a company that provides multiple services in the cultural heritage field, including underwater archaeology, aerial shots by flying drones, archival research and historical studies, and archaeological excavations.
“The project was created to archaeological requirements. Six months ago l’Arc-Team Cles asked us a small submarine drone to explore the depths of the alpine lakes,” Andrea Saiani, the other ArcheoRov creator, explained to Wired Italy (translated). “It weighs 6 pounds, compared with 70-80 pounds of products already on the market, therefore, an archaeologist you can carry in a backpack.
It costs about 2,500 Euros, against an average of 25 thousand.”
Dr. Rocco explained that ArcheoRov is able to orient its body upwards or downwards, in order to get the best view possible from one of its two cameras, as it is able to “tip itself on end and sink or rise in seconds.” This characteristic makes the little underwater ROV perfect for sweeping visual surveys, necessary for archaeological expeditions. Its small size makes it suitable for the job Arc-Team needs it for: hard-to-reach stone age relics that are preserved deep in mountain lakes.
Initial calibration tests of ArcheoRov’s underwater camera [Image: WitLab]
ArcheoRov’s two batteries are sealed inside pressure-resistant units. The maneuverability comes from its three 130W T100 electric thrusters: one downward facing thruster at the rear, and two facing forward at the front. Each thruster packs 2.36 kg of push, which is enough to pull along the attached WiFi-enabled buoy that provides researchers at the surface a data link to the ArcheoRov. Dr. Rocco said once, when he got tired, the ArcheoRov was even able to tow him along. Eventually, the researchers would like to be able to get rid of the wire-guided buoy and “mount a GPS system to draw an area to be scanned automatically by flaps of the robot, which then reports the data of his observations to the researcher.”
The research team had a lot of ideas at the beginning, and used one of WitLab’s rapid prototyping machines to print up three possible candidates. Once they constructed the plastic outline for what would become the ArcheoRov, they just needed to attach the motors, which were powered from a source outside the tank, and see what type of configuration gave them the response they were looking for. Finally, ArcheoRov had its first successful underwater outing in Madrone Alpine Lake, in Trentino, Italy, at 2,400m altitude.
One of the most pertinent features of the ArcheoRov is that the design is open source, so anyone with a 3D printer and a love for things under the sea is able to access it and build their own ArcheoRov. It uses the Robot Operating System (ROS), which is a set of open source software tools and libraries. Dr. Rocco believes that we are entering a new phase of professional experimentation, where researchers can work on assembling their own ROV or drone for the exact purpose they need, whether it’s pollution monitoring, marine biology, exploring reefs and shipwrecks, and archaeologists who research the seabed.
Dr. Rocco said, “This is important because by doing so we are enabling the developer community to easily add their custom software extensions or even make ArcheoROV semiautonomous…Now it’s quick and cheap, people can design their own ROV.”
The ArcheoRov hardware was designed using SOLIDWORKS, and software written using Python. The first model, with a camera for navigation and one for 3D shooting, is already available, but WitLab is already back to the drawing board, developing a sonar-equipped version with a thermometer and a mechanical arm. A Kickstarter campaign is in the works for next year.
Check out this video to see the ArcheoRov swimming in action:
Discuss in the ArcheoRov forum at 3DPB.com.
[Sources/Images: WitLab / Maritime Journal / Wired]
Stay up-to-date on all the latest news from the 3D printing industry and receive information and offers from third party vendors.
Tagged with: 3d printed drone • 3d printed submarine drone • 3d rapid prototyping • Arc-Team • archaeology • ArcheoRov • cad • cameras • italy • open source • open source designs • Remote Operated Vehicle • Robot Operating System • ROS • ROV • solidworks • underwater • underwater drone • underwater ROV • WitLab
Please enable JavaScript to view the comments powered by Disqus.
3D Printed Extreme Drone
Phillip Keane of Nanyang Technological University has 3D printed a fixed body quadcopter that can withstand extreme environments. This was reported in a press release from the university.
Modern multicopters are manufactured according to the same principle as other electronic devices - the case consists of several parts on which various internal components are mounted, after which the case is assembled with screws into a single structure and, if necessary, sealed. Compared to a traditional collapsible body, a solid surface allows you to initially make a more durable device, while the drone will not be afraid of dust and water, and using various specialized materials, you can achieve more interesting design features, such as resistance to high temperatures.
The author of the project used a Stratasys Fortus 450mc printer, on which the entire quadcopter body was made from ULTEM 9085 thermoplastic. During printing, the printer stopped three times to allow other components to be installed: motors, an electronic board, wires, and a separately printed plate that covers the cavity intended for the battery.
The body and electronics of the resulting quadcopter can withstand an ambient temperature of 150 degrees Celsius. Despite the fact that the presented drone has a weak point - the battery cannot withstand heating above one hundred degrees - it is still much higher than the capabilities of conventional serial drones, the popular DJI Phantom quadrocopter, for example, officially withstands temperatures up to +40 degrees Celsius. The developers note that they did not set themselves the goal of making a drone that is resistant to high temperatures - they were more interested in a drone with a durable non-separable case, in which the electronics are installed at the printing stage.
In addition to heat resistance, the body of the drone is also very durable. Tests on the simulator showed that one arm of the quadcopter can withstand a load of up to 20 kilograms, which, according to the developers, taking into account various amendments, corresponds to 17 kilograms in the real world. Thus, the body of a small quadrocopter can withstand a load weighing more than 60 kilograms. Although the installed motors and propellers do not allow for such a payload, such a body still has an advantage in strength compared to other multicopters of comparable size.
There are other drone designs for extreme environments. For example, the University of Melbourne printed a titanium frame for a fire multicopter, and the Korea Institute of Advanced Technology built a full-fledged FAROS fire drone - the drone can switch to vertical movement mode on the fly, clinging to walls and resting against them with small wheels, and also withstands direct exposure to flames temperatures up to a thousand degrees Celsius.
Nikolai Vorontsov
Found a typo? Select the fragment and press Ctrl+Enter.
3D Printer Drone and Quadcopter Models
This article is an introduction to 3D Printing your own quadcopter drone. You will get acquainted with some basic principles of drone building, and we will describe some points step by step. The task will be relatively simple, since the description will be detailed.
What we need to get started
In addition to the 3D printer, we will need some non-printable parts such as a motor, batteries or accumulators, some electronics, sensors, a remote control and a knack to put it all together.
Why print a drone?
As a matter of fact, we will print the frame and body structure. Sometimes propellers can be printed. Why is it important? Because drones fall and break. Especially if you are a beginner pilot. This picture shows everything clearly:
If we 3D print parts, we will have an almost infinite supply of spare parts, which will make it easier to survive pilot training and regular plane crashes. Apart from the fact that the quadcopter will be easier to repair, a homemade drone will allow you to get a better feel for its inner workings and mechanics.
And one more important point: 3D printing allows you to quickly develop parts according to your own design. Let's say you have purchased a new camera and want to install it on your quadcopter. Then you just open up your favorite 3D modeling program and end up printing out the part and testing it. Make changes, print again, etc.
What is a quadcopter drone?
A quadcopter is a multi-rotor helicopter that rises and moves with four main rotors and does not have a tail rotor. This is the most common type of amateur radio-controlled drones.
Small in size and highly maneuverable, these quadcopter drones can fly both indoors and outdoors. In addition, at this size, quadcopter drones are cheaper than conventional helicopters and more reliable due to their simple design.
Here is a detailed overview of the details of a commercially available high-end quadcopter drone used for aerial photography.
Almost all parts that are not motor or electronics can be 3D printed. The printed version of the drone looks a little different.
3D printed Crossfire quadcopter. Link to project: http://www.thingiverse.com/thing:32281
In addition to visual and aesthetic differences, the printed version has the advantage of being easy to update and is also modular. In the next video, Dennis Baldwin talks in detail about his quadcopter.
How to Print a Quadcopter Drone
If you want to build your own drone, we offer several entry points to the project. Here is a detailed guide to 3D printed quadcopter:
http://www.instructables.com/id/3D-Printed-Quadcopter-with-Arduino/?ALLSTEPS
Titch Micro Drone
https://www.myminifactory.com/object/ 38967
Brushed Y6 Micro Quad
https://www.myminifactory.com/object/brushed-y6-micro-quad-31348
Millennium Falcon Drone Shell
https://www. myminifactory.com/object/millennium-falcon-drone-shell-10144
Micro 105 FPV Quadcopter
https://www.myminifactory.com/object/micro-105-fpv-quadcopter-21362
Micro 105 FPV Quadcopter
https ://www.myminifactory.com/object/3drobotics-iris-19615
Hexacopter drone
https://www.myminifactory.com/object/hexacopter-drone-19600
And this is the instruction for building an H-shaped drone:
http://www.instructables.com/id/Make-an-H-Quadcopter-with-3D-printing/?ALLSTEPS
Printed remote control
If you want to 3D print
insectoid ornithopter on a 3D printer
Detailed Guide to the Insectoid Ornithopter:
http://www.