3D printer tricks
Out of the Box 3D Printer Tips for Beginners
(Image credit: Shutterstock)You’ve unboxed your new 3D printer, put it together and installed any included software on your computer. Perhaps you’ve even printed a sample model from the manufacturer, just to make sure everything works.
However, even if you have one of the best 3D printers, you need more than optimism to make the most of it. Below, we’ve listed six tips for 3D printer fans who are just getting started with a new FDM printer.
1. Level your print bed.
(Image credit: Tom's Hardware)First, when we talk about “leveling the bed” understand that what we really mean is tramming the print surface. 3D printers have been tacked to the walls or flipped upside down and still work fine. Being level to a table has nothing to do with their ability to print.
When you level the bed on a 3D printer, you’re making sure that the nozzle is at the same height across the entire print surface. This allows the printer to lay down a perfect first layer and the foundation for a good print.
If your printer didn’t come with a probe to auto level the bed for you, have no fear. It’s really not that hard.
First, heat the nozzle and bed as if you’re setting up a print. Metal expands slightly when warm, so never calibrate a cold machine. Allow the printer to warm up for a few minutes.
Next, home your printer. This takes it to the 0,0,0 position.
Check your printer controls for something called Bed Leveling, Level Corners or Bed Tramming. This option will move the printer around the four corners of the bed while you adjust the springs underneath.
If you lack this option as well (basic Ender 3s don’t come with any leveling aids installed), it’s ok. Look for the “disable steppers” option, which turns off the stepper motors and allows you to push the print head by hand.
Slide the print head (or let the printer do it) to the first corner, centered more or less over the adjustment knob under the bed. Slip an ordinary piece of paper under the nozzle. Raise or lower the nozzle until it barely touches the paper.
Do this for all four corners and the center. Then do it again. Leveling the bed is indeed a balancing act and adjusting one corner can throw off the opposite corner.
2. Clean your print bed and make it sticky.
(Image credit: Shutterstock)Your print surface can be perfectly flat and level, but plastic won’t stick to it if it’s not clean. It’s a gross fact of life, but traces of skin oil from your hands can interfere with first layer adhesion. On top of that, a lot of PLA is made with gooey additives for extra shine and sparkle. These secret ingredients can leave a slick residue on your print bed.
91% isopropyl alcohol from the first aid aisle is the perfect cleaning agent. Wipe the print surface with alcohol and a paper towel after each print to keep it squeaky clean.
If you’re still having trouble getting that first layer to hold, it’s ok to use a little glue stick. Smear an even coating of washable glue stick – the purple kind is the best – on your warm print surface. The layer of glue gives it that extra bit of grab to hold down your prints.
3. Use rafts to increase your success rate.
(Image credit: Shutterstock)There are people who’d rather stick a fork in their eye than admit to using a raft. Rafts are exactly what they sound like – a chunky first layer that your model sits on. These adhesion helpers somehow defy uneven and dirty beds and practically guarantee a successful print.
You’ll find rafts under Build Plate Adhesion in Cura and under Support Material in PrusaSlicer. Other slicers have their raft options in other menus.
I still use a raft when printing tiny objects, like eyes or buttons for small models.
So why not use rafts all the time? The downside to rafts is they create a rough bottom on your print while wasting a bit of time and material. Believe me, they’re still worth it for new people just getting started.
4. Keep your nozzle clean and buy spares.
(Image credit: Tom's Hardware)Your new printer may have come with two nozzles, one installed on the hotend and a spare. Most FDM 3D printers rely on brass nozzles that wear out from use, especially if you're running filament with abrasive glitter or fibers.
If your printer uses them, the first thing you want to buy is more nozzles. For as little as 25 cents a piece, brass nozzles are the cheapest part of your printer. And the most critical.
Enclosed printers such as the Flashforge Adventurer 3 Lite and Voxel Aries use their own, proprietary hot ends that cost significantly more and presumably last a lot longer than the brass nozzles on popular, open-air printers such as the Creality Ender 3 Pro.
When the nozzle wears down, the opening becomes wider and throws off your carefully calculated print calibrations. Even worse, bits of grit and overcooked plastic can clog up the insides of your hotend.
You can spot a nozzle going bad when you have tiny gaps in the print or too much stringing. Run a 100mm of filament through your hotend – if it makes crazy curlicues instead of pouring straight down, your nozzle is dirty and you can replace it.
Keep the outside of your nozzle clean as well. Stray wisps of filament will collect on a hot nozzle and later drip on your print. Clean the outside of the nozzle while it’s hot by scraping it with a wooden craft stick or a brass brush.
5. Keep your filament fresh and tight.
(Image credit: Shutterstock)PLA is the most popular filament for 3D printing because it’s the easiest to work with and comes in a massive variety of colors. It does not readily absorb moisture, so you don’t need to worry about keeping it sealed in airtight containers.
That doesn’t mean you can throw it on the floor like your old collection of 90s CDs. The biggest problem for filament is dust and tangles. This is why proper spool handling is key to successful printing.
You can prevent dust and grit from clogging your printer by using a dusting sponge. Simply attach a small piece of sponge with a binder clip to the filament before it enters the extruder. Add a drop of olive oil to the sponge to lubricate the hotend and prevent stringing.
Want something more elegant? Print this universal filament filter from Creative Tools, the same people who made the 3D Benchy.
Tangles in your spool are even worse. If your spool develops a knot, the filament will stop feeding through the printer and cause a fail. Prevent tangles by never allowing the spool to uncoil. This means keeping one hand on the spooled filament at all times, and keeping it neatly wound by taping the filament in place.
I use masking tape since it’s easier to remove and doesn’t leave a sticky residue.
6. Find and download free files.
(Image credit: Tom's Hardware)The final piece to the 3D printing puzzle is finding the right models to print. Unless you’re an artist and know CAD, you need ready-made files. Lucky for you, there are literally millions of free files waiting for you to download.
The most popular file repositories are Thingiverse, Thangs and PrusaPrinters. All three of these websites allow you to download STL files for free.
- Thingiverse is the most widely-known file storage site and very popular, especially with students. Because of this, be wary of files without photos – they may have been uploaded by a 5th grader and never tested.
- Thangs is the newest file website and rapidly growing. Looking for a trendy print making the rounds on Tic Tok? It’s probably on Thangs.
- PrusaPrinters is the home of Prusa manufacturing, but they also sell filament and store free files that any brand of machine can use. They recently launched a reward program where you earn free filament by uploading files and submitting photos of your finished prints.
Denise Bertacchi is a Contributing Writer for Tom’s Hardware US, covering 3D printing.
Topics
3D Printing
30 Essential 3D Printing Tips for Beginners – Best Results – 3D Printerly
3D printing can be a difficult activity to get the hang of, especially if you are someone who isn’t used to these types of machines, so I decided to put some tips together to help users out.
There is a lot of information out there but I narrowed down some essential and useful tips that you can use to improve your 3D printing results and operation along the way.
We’ll go through tips for the best 3D print quality, tips for large prints, some basic troubleshooting/diagnostics help, tips for getting better at 3D printing, and some cool tips for 3D printing PLA. There are 30 tips in total, all spread out through these categories.
Stay tuned through this article to improve your 3D printing journey.
Tips to Make 3D Prints Better Quality
- Use Different Layer Heights
- Reduce the Print Speed
- Keep the Filament Dry
- Level Your Bed
- Calibrate Your Extruder Steps & XYZ Dimensions
- Calibrate Your Nozzle and Bed Temperature
- Be Wary of Your Filament’s Recommended Temperature Range
- Try a Different Bed Surface
- Post-Process Prints
1. Use Different Layer Heights
One of the first things you should look at learning about is layer heights in 3D printing. It’s essentially how tall each extruded layer of filament will be with your models, directly relating to the quality or resolution will be.
The standard layer height that you’ll see in most slicer software programs like Cura should be 0.2mm.
A lower layer height like 0.12mm will produce a higher quality model but will take longer to 3D print because it creates more layers to produce. A higher layer height like 0.28mm will produce a lower quality model but be quicker to 3D print.
0.2mm is usually a good balance between these values but if you want a model to have finer details and more pronounced features, you’ll want to use a lower layer height.
Another thing to note here is how the layer heights are in increments of 0.04mm, so rather than use a layer height of 0.1mm, we would either use 0.08mm or 0.12mm due to the mechanical function of a 3D printer.
These are referred to as “Magic Numbers” and are default in Cura, the most popular slicer.
You can learn more about that by checking out my article 3D Printer Magic Numbers: Getting the Best Quality Prints
The general rule with layer heights is to balance it out with the nozzle diameter between 25%-75%. The standard nozzle diameter is 0.4mm, so we can go anywhere between 0.1-0.3mm.
For more details on this, check out Best Way to Determine Nozzle Size & Material for 3D Printing.
Check out the video below for a nice visual about 3D printing at different layer heights.
2. Reduce the Print Speed
Print speed has an effect on the final quality of your parts, where printing with a slower speed can increase the quality, but at the cost of reducing the overall print time.
The increase in printing times usually isn’t too significant unless you really slow down the speed or have a pretty large model. For smaller models, you can decrease the print speed and not have much of an effect on printing times.
Another benefit here is that you can decrease some imperfections on your models depending on what issues you are having. Issues like ghosting or having blobs/zits on your model can be alleviated by reducing your print speed.
You do have to keep in mind though, sometimes having a slower print speed can negatively affect things like bridging and overhangs, since faster speeds means the extruded material has less time to droop down.
The default print speed in Cura is 50mm/s which works well in most cases, but you can try reducing it down for smaller models to get more detail and see the effects on the print quality.
I’d recommend printing multiple models at different print speeds so you can see the actual differences yourself.
I wrote an article about getting the Best Print Speed for 3D Printing, so check that out for more info.
Make sure you balance out your print speed with your printing temperature though because the slower the print speed, the more time the filament spends being heated up in the hotend. Simply lowering the printing temperature a few degrees should be fine.
3. Keep Your Filament Dry
I cannot stress how important it is to take care of your filament properly. Most 3D printer filaments are hygroscopic in nature, meaning that they readily take in moisture from the environment.
Some filaments are more hygroscopic while others are less. You should be keeping your filament dry to ensure that it performs optimally and doesn’t make your print’s surface texture look poor.
Check out the SUNLU Filament Dryer on Amazon to dry the moisture out of your filament. It provides a time setting up to 24 hours (default 6 hours) and a temperature range between 35-55°C.
Simply power the device, load your filament, set the temperature and time, then start drying the filament. You can even dry the filament while you are printing as it has a hole to put the filament through.
One of the best ways of doing this is to purchase a filament dryer which is a dedicated device engineered to store and keep 3D printer filament moisture-free. Here are the 4 Best Filament Dryers for 3D Printing that you can buy today.
There are different Ways to Dry Your Filament so check out the article to find out.
In the meantime, check out the following video for an in-depth explanation of why drying is necessary.
4. Level Your Bed
Leveling your 3D printer’s bed is fundamental for successful 3D prints. When your bed is uneven, it can lead to printing failures even near the end of a very long print (which has happened to me).
The reason leveling your bed is important is so the first layer can adhere to the build plate strongly and provide a solid foundation for the rest of the print.
There are two methods of leveling your print bed, either manually or automatically. A 3D printer like the Ender 3 V2 has manual leveling, while something like the Anycubic Vyper has automatic leveling.
Check out the video below for a guide on leveling your 3D printer.
You can learn How to Level Your 3D Printer Bed to start creating high-quality parts right away.
5. Calibrate Your Extruder Steps & XYZ Dimensions
Calibrating your 3D printer is important for getting the best quality 3D prints, especially the extruder.
Calibrating your extruder (e-steps) basically means that you are ensuring that when you tell your 3D printer to extrude 100mm of filament, it actually extrudes 100mm rather than 90mm, 110mm or worse.
It’s quite noticeable when your extruder isn’t properly calibrated compared to when it is extruding the perfect amount.
Similarly, we can calibrate the X, Y & Z axes so that your printing dimensional accuracy is optimal.
Check out the video below on how to calibrate your e-steps.
In the video, he shows you how to change these values in a software program, but you should be able to change it within your actual 3D printer by going to “Control” or “Settings” > “Movement” or something similar, and looking for the steps per mm values.
Some older 3D printers may have an outdated firmware that doesn’t allow you to do this, which is when you’d use a software program to do it.
You can download the XYZ Calibration Cube on Thingiverse. Once you print the model, you want to measure the cube with a pair of digital calipers and try to get a value of 20mm for each measurement.
If your measurements are above or below 20mm, this is where you would increase or decrease the steps value for X, Y or Z depending on which one you are measuring.
I put together a complete guide called How to Calibrate Your 3D Printer. Be sure to give it a read for detailed information.
6. Calibrate Your Nozzle and Bed Temperature
Getting the right temperatures in 3D printing is important for getting the best quality and success rate. When your printing temperature isn’t optimal, you might get print imperfections like layer separation or bad surface quality.
The best way to calibrate your nozzle or printing temperature is to print something called a temperature tower, a 3D model that creates a tower with a series of blocks where the temperature changes as it prints the tower.
Check out the video below to see how to create a temperature tower directly in Cura without needing to download a separate STL file.
7. Be Wary of Your Filament’s Recommended Temperature Range
Each 3D printer filament comes with a manufacturer-recommended temperature range in which the filament performs the best. Make sure that you print the material within the provided range for the best results.
You can look for this parameter on the filament’s spool or the box that it came in. Alternatively, this information is written on the product page of the website you order it from.
For instance, Hatchbox PLA on Amazon has a recommended nozzle temperature of 180°C-210°C in which it works optimally. So with the temperature tower, you would input a starting value of 210°C, then put it in increments down to where the top would reach 180°C.
8. Try a Different Bed Surface
There are many different types of bed surfaces that can be used on a 3D printer. Some of the most popular ones include Glass, PEI, BuildTak, and Creality.
For instance, the PEI build surface boasts the benefit of easy print removal and doesn’t necessitate the use of bed adhesives like glue. You can modify your 3D printer with a PEI print bed to make printing a lot easier.
Similar to PEI, other bed surfaces have their own pros and cons that may or may not suit your preferences.
I’d highly recommend going for the HICTOP Flexible Steel Platform with PEI Surface from Amazon. It has a magnetic bottom sheet with adhesive that you can easily stick to your aluminum bed and attach the top platform afterwards.
I’m currently using one and the best part about it is how my 3D models have great adhesion throughout, then after the bed cools down, the model actually detaches itself from the bed.
I wrote an article about the Best 3D Printer Build Surface, so feel free to check that out.
Do watch the following video for more useful information on the subject.
9. Post-Process Prints for Better Quality
After your model comes off the build plate, we can further process the model to make it look better, otherwise called post-processing.
The usual post-processing we might do is to remove the supports and to clean up any basic imperfections like stringing and any blobs/zits on the model.
We can take this a step further by sanding the 3D print to remove the visible layer lines. The usual process is to start with a low grit sandpaper like 60-200 grit to remove more material from the model and create a smoother surface.
After that, you can move to higher grits of sandpaper like 300-2,000 to really smooth and polish the outside of the model. Some people go even higher in sandpaper grit to get a shiny polished look.
Once you’ve sanded the model to your ideal level, you can start to prime the model using a can of primer spray lightly around model, maybe doing 2 coats.
Priming allows paint to adhere to the model easier, so now you can apply a nice spray paint of your chosen color for the model, either using a can of spray paint or an airbrush.
Check out my article on How to Prime & Paint 3D Prints, focused on miniatures, but still useful for normal 3D prints.
I also wrote an article about Best Airbrush & Paint for 3D Prints & Miniatures if you’re interested in that.
You can also skip the spraying and use a fine paintbrush to get those finer details in your models. It does take some practice to learn how to sand, prime and paint models to a good standard, but it’s a great thing to learn.
The video below is a great visual on how to post-process your 3D prints to a really high standard.
Tips for Large 3D Prints
- Consider Using a Larger Nozzle
- Split the Model Into Part(s)
- Use PLA Filament
- Use an Enclosure to Protect the Environment
10. Consider Using a Larger Nozzle
When 3D printing larger models, using a 0.4mm nozzle can take a very long time to complete a model. If you double the nozzle diameter to 0.8mm and double the layer height to 0.4mm, you would essentially half the number of layers being printed which would significantly reduce printing times.
The difference in quality would be noticeable, but if you are printing a large model where details aren’t important, this would make the most sense.
I’d recommend getting something like the SIQUK 22 Piece 3D Printer Nozzle Set from Amazon, including 1mm, 0.8mm, 0.6mm, 0.5mm, 0.4mm, 0.3mm & 0.2mm nozzles. It also comes with a storage case to keep them together and secure.
For objects like vase, you can easily take your printing time from 3-4 hours down to 1-2 hours by using a larger nozzle diameter, as shown in the video below.
11. Split the Model Into Part(s)
One of the best tips for large 3D prints is splitting your model into two different parts, or more if required.
Not only does it make large 3D prints possible to be printed if they are larger than the build volume, but also retains their overall quality. There are multiple software that you can use for cutting your model into different parts.
Some of the best ones include Fusion 360, Blender, Meshmixer, and even Cura. All of the methods are discussed in-depth in my How to Split & Cut STL Models For 3D Printing, so do check that out for a detailed tutorial.
A useful tip here is to cut the model where it’s less noticeable, so you can glue the parts together later and so there aren’t large seams or gaps in the connected model.
The following video by MatterHackers goes over cutting your models.
12. Use PLA Filament
PLA is the most popular 3D printer filament that boasts a variety of desirable features. It’s often compared to ABS in terms of its quality, but the former is simply undefeated when it comes to being user-friendly.
The experts recommend using PLA for printing large prints. Doing so can give you the best chances of success as PLA is less prone to cracking when a print enlarges, unlike ABS.
A very popular and great brand of PLA filament to go with would be HATCHBOX PLA Filament from Amazon.
Other options of filament that people use are:
- ABS
- PETG
- Nylon
- TPU
PLA is definitely the easiest out of all these materials due to the lower temperature resistance and the lesser chances of warping or curling away from the build plate.
13. Use an Enclosure to Protect the Environment
I’d highly recommend bringing in an enclosure for your 3D printer when creating larger parts. It’s not entirely necessary but it can definitely save some potential print failures due to changing temperature conditions or drafts.
When you get temperature changes or drafts on larger models, you are more likely to experience warping of the material since there is a large footprint on the build plate. The smaller the object you print, the less print failures you can expect, so we want to minimize that.
You can use something like the Creality Fireproof & Dustproof Enclosure from Amazon. Many users who were experiencing print failures, especially with ABS found that they had much more success printing with an enclosure.
One user who has the Creality CR-10 V3 said it was printing several large parts at once and he had pieces near the edge that would warp, wasting time and filament due to needing to print it again.
A friend recommended the enclosure above and it helped largely with warping, going from every other print having warping to none at all. It works well because it keeps the temperature more stable and prevent drafts from affecting the print.
Simply opening a door and cool air waving in could affect large prints easily.
You can also use an enclosure to protect the environment from hazardous fumes that are emitted from filaments like ABS and Nylon, then vent them out with a hose and fan.
Tips on Diagnosing & Troubleshooting 3D Printing Issues
- Ghosting
- Z-Wobble
- Warping
- Layer Shifting
- Clogged Nozzle
14. Ghosting
Ghosting or ringing is when the features of your model reappear on the surface of your print in an undesirable way and make the print look defective. It is mostly caused by high retraction and jerk settings that cause the printer to vibrate during printing.
One of the first things that you can do to fix ghosting is to check if any printer parts are loose, such as the hot end, bolts, and belts. Make sure your 3D printer is on a stable surface because if the surface is wobbly, the print quality can be affected.
Another working solution is to place vibration dampeners (Thingiverse) on the feet of the 3D printer to prevent it from vibrating.
You can also reduce your print speed, which is also a great tip to get high-quality prints.
If you want to know more, check out my guide on How To Solve Ghosting in 3D Printing for an in-depth analysis.
The video below is really helpful in showing you what ghosting looks like and how to reduce it.
15. Z-Banding/Wobble
Z-Banding, Z-Wobble or Ribbing is one common 3D printing issue that cause your model to look poor in quality. It can often make the part have visible imperfections that shouldn’t be there.
You can diagnose Z-Banding in your 3D printed model by looking at its layers and observing if they align with the layers above or below it. It’s easy to spot if the layers do not match with each other.
This usually results when the print head is wobbling slightly, meaning that it is not quite fixed in position. You can confirm the diagnosis by holding the 3D printer frame in one hand and shaking the print head a little with the other, being careful not to do it while the nozzle is hot.
If you see that the print head is shaking, you are probably experiencing Z-Banding. This will likely cause your prints to come out with misaligned layers and wobbling.
To fix the issue, you want to stabilize the movements of your print head and print bed so there isn’t a lot of looseness in your 3D printer mechanics.
The following video can walk you through the process fixing wobble of your print head and the print bed. A cool tip is, where you have two eccentric nuts, mark one edge of each nut so they are parallel.
Check out my article on How to Fix Z Banding/Ribbing in 3D Printing – 5 Easy Solutions to Try if you still have issues with Z-Banding.
16. Warping
Warping is another common 3D printing issue that causes the layers of your model to turn inwards from the corner, ruining the dimensional accuracy of the part. Many beginners experience it at the start of their 3D printing journey and fail to print high-quality models.
This issue is caused mainly due to rapid cooling and abrupt temperature changes. Another reason is the lack of proper adhesion to the build platform.
The ideal fixes to solve your warping issues is to:
- Use an enclosure to reduce rapid changes in temperature
- Increase or lower your heated bed temperature
- Use adhesives so the model sticks to the build plate
- Ensure cooling is turned off for the first few layers
- Print in a room with a warmer ambient temperature
- Make sure your build plate is properly leveled
- Clean your build surface
- Reduce drafts from windows, doors, and air conditioners
- Use a Brim or Raft
Whatever the cause, the first thing that you should do if you haven’t already is get an enclosure for your 3D printer.
This will help provide an ambient temperature for your prints, especially if you’re printing with ABS which requires a heated build plate.
However, if it’s not possible to get an enclosure at the present, you can increase your bed temperature to see if it fixes warping. If the temperature is already too high, try lowering it and check if that helps.
Another way to prevent warping is to use build plate adhesives. Anything from regular glue sticks to specialized 3D printer bed adhesive will work here.
- If you only want to settle for high-quality adhesives, take a look at the Best 3D Printer Bed Adhesives guide.
For more information on fixing warping, check out 9 Ways How to Fix 3D Prints Warping/Curling.
17. Layer Shifting
Layer Shifting is when layers of your 3D print start moving unintentionally in another direction. Imagine a square with its top half not aligning perfectly with its bottom half. That would be layer shifting in the worst-case scenario.
One of the most major causes of Layer Shifting is a loose belt that moves the print head carriage in the X and Y direction.
You can simply tighten the belt as shown in the video at the end of this section to resolve Layer Shifting. Another thing that you can do is 3D print an adjustable belt tensioner (Thingiverse) and place it on your belt, so it makes the tightening process much easier.
As for the tightness, it’s advised not to overdo it. Just make sure that your belts do not droop and are fairly firm in position. That should do the trick.
Other fixes for layer shifting are:
- Check the pulleys connected to the belts – resistance should be low with movement
- Ensure your belts aren’t worn out
- Check your X/Y axis motors are working properly
- Reduce your printing speed
Check out my article 5 Ways How to Fix Layer Shifting Mid Print in Your 3D Prints.
The video below should help out with layer shifting issues also.
18. Clogged Nozzle
A clogged nozzle is when there’s some sort of blockage inside the hot end nozzle that’s causing no filament to be extruded on the build plate. You try printing, but nothing happens; that’s when you know your nozzle is clogged.
- That said, your firmware can also cause your 3D printer not to start or print. Check out 10 Ways How to Fix Ender 3/Pro/V2 Not Printing or Starting for a detailed guide.
You’ve probably got a piece of filament stuck inside the nozzle that’s preventing any more filament from thrusting out. As you use your 3D printer, such pieces can accumulate over time, so make sure you maintain the machine.
Unclogging a nozzle is pretty easy for the most part. You first have to increase the nozzle’s temperature to somewhere around 200°C-220°C using your 3D printer’s LCD menu so the blockage inside can melt.
Once done, take a pin that’s smaller than your nozzle diameter, which is 0.4mm in most cases, and get to clearing out the hole. The area will be very hot at that time, so make sure your movement is careful.
The process can definitely get a bit involved, so it’s worth checking out How to Clean Your Nozzle and Hotend Properly for step-by-step instructions.
The video below by Thomas Sanladerer is helpful for cleaning out a clogged nozzle.
Tips for Getting Better at 3D Printing
- Research & Learn 3D Printing
- Make a Habit of Consistent Maintenance
- Safety First
- Start With PLA
19.
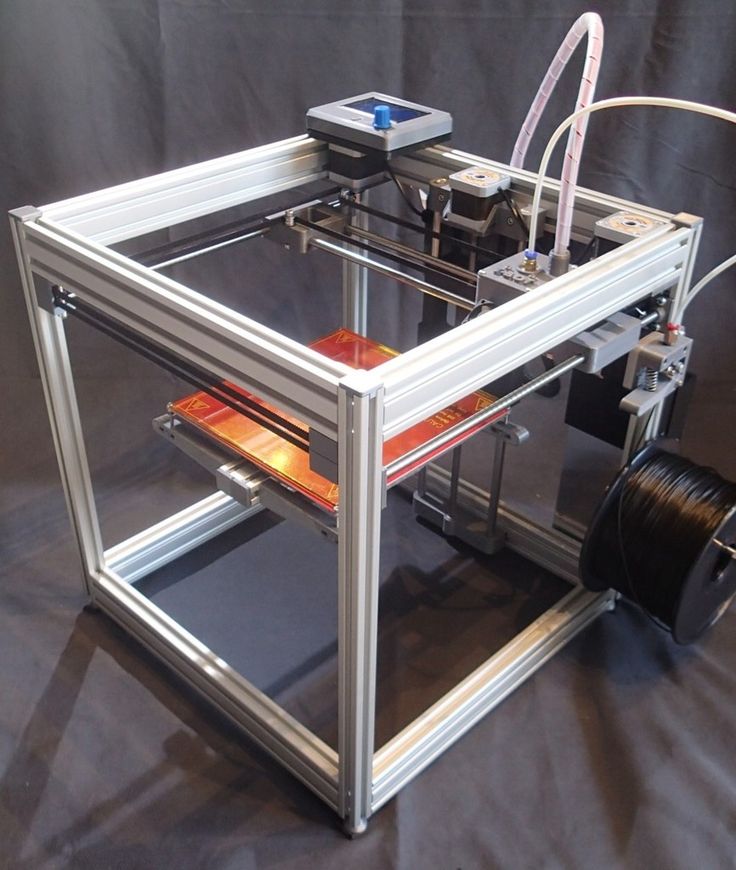
One of the best tips for getting better at 3D printing is to research online. You can also check out YouTube videos of popular 3D printing channels like Thomas Sanladerer, CNC Kitchen, and MatterHackers for good sources of relevant information.
Thomas Sanladerer did a whole series about learning the basics of 3D printing in easily digestible videos, so definitely check that out.
It’ll probably be a while until you learn the ins and outs of 3D printing, but starting small and staying consistent can both prove to be highly successful for you. Even after years of 3D printing, I’m still learning things and there are always developments and updates along the way.
I wrote an article called How Exactly Does 3D Printing Work to clearly understand the whole concept of this phenomenon.
20. Make a Habit of Consistent Maintenance
A 3D printer is just like any other machine, such as a car or a bike that requires consistent maintenance from a user’s end. If you don’t develop a habit of taking care of your printer, you’re prone to run into a number of problems.
Maintenance of a 3D printer can be carried out by checking for , damaged parts, loose screws, loose belts, intertwined cables, and dust accumulation on the print bed.
In addition, the extruder nozzle should be cleaned if you change filaments from low temperature filament like PLA to high temperature filament like ABS. A clogged nozzle can lead to issues like under-extrusion or oozing.
3D printers have consumables that you’ll want to replace every so often. Check out the video below for some great advice on maintaining your 3D printer.
21.
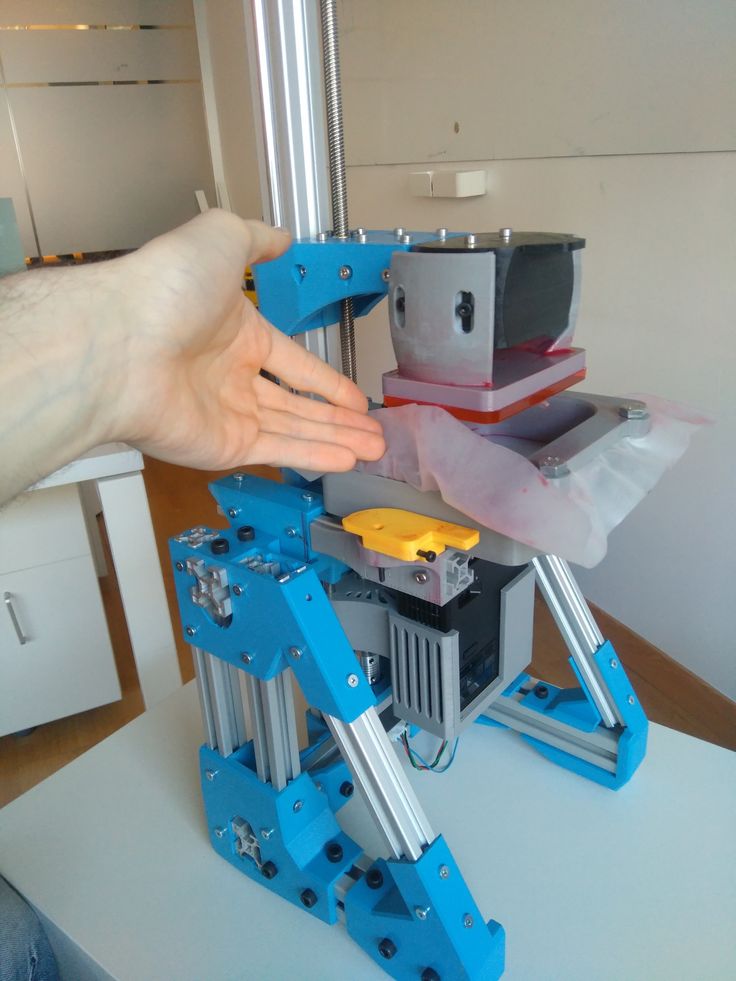
3D printing can often get dangerous, so make sure you put safety first to become more like the professionals of this business.
First off, the extruder nozzle is typically heated to high temperatures when it’s printing and you have to be careful not to touch it when it does.
In addition, filaments like ABS, Nylon, and Polycarbonate aren’t user-friendly and need to be printed with an enclosed print chamber in a well-ventilated area to protect yourself from fumes.
The case is even sensitive over at the department of SLA 3D printing. Uncured resin can cause skin infections when touched without gloves and respiratory issues when breathed in.
This is why I put together the 7 3D Printer Safety Rules You Should Be Following Now for printing like an expert.
22. Start With PLA
PLA isn’t the most popular 3D printer filament for no good reason. It’s considered the perfect material for beginners due to its ease of use, biodegradable nature, and decent surface quality.
Therefore, starting your 3D printing journey with PLA is a good way to get better at 3D printing. There’s nothing better than mastering the basics first and moving onto harder levels.
Let’s get into some useful tips for 3D printing PLA to get you started in the right direction.
Tips for 3D Printing PLA
- Try Using Different Types of PLA
- Print a Temperature Tower
- Increase Wall Thickness to Improve Strength
- Try a Bigger Nozzle for Prints
- Calibrate Retraction Settings
- Experiment with Different Settings
- Learn CAD and Create Basic, Useful Objects
- Bed Leveling is Very Important
23. Try Using Different Types of PLA
Many people don’t know that there are actually several types of PLA that you can make use of. I’d recommend starting out with regular PLA without any extra characteristics so you can learn about 3D printing, but once you’ve learned the basics, you can try using different types.
Here are some of the different types of PLA:
- PLA Plus
- Silk PLA
- Flexible PLA
- Glow in the Dark PLA
- Wood PLA
- Metallic PLA
- Carbon Fiber PLA
- Temperature Color Changing PLA
- Multi-Color PLA
This really cool video below goes through almost every filament out there on Amazon, and you’ll see plenty different types of PLA for yourself.
24. Print a Temperature Tower
3D printing PLA at the right temperatures gets you much closer to printing it successfully. The best way to achieve the perfect nozzle and bed temperature is by printing a temperature tower, as shown in the video below.
Basically, it will print a tower with several blocks with different temperature settings and actually automatically change the temperature as it’s printing. You can then view the tower and see which temperatures give you the best quality, layer adhesion, and less stringing.
I wrote a pretty useful article called PLA 3D Printing Speed & Temperature – Which Is Best, so feel free to check that out.
25. Increase Wall Thickness to Improve Strength
Increasing your wall or shell thickness is one of the best ways of making strong 3D prints. If you’re after a functional part but don’t want to use a complicated filament like Nylon or Polycarbonate, this is the way to go.
The default wall thickness value in Cura is 0. 8mm, but you can bump that up to 1.2-1.6mm for improved strength in your PLA parts. For more information, check out How to Get the Perfect Wall/Shell Thickness Setting.
26. Try a Bigger Nozzle for Prints
3D printing PLA with a large nozzle allows you to print at an increased layer height and make stronger parts among other benefits. You can also increase the print times significantly with a bigger nozzle.
The default nozzle diameter of most FDM 3D printers is 0.4mm, but bigger sizes are also available, including 0.6mm, 0.8mm, and 1.0mm.
The bigger the nozzle you use, the faster your print speed will get in addition to being able to print bigger parts. The following video discusses the benefits of 3D printing with a large nozzle.
In addition to calibrating your 3D printer for the right nozzle and bed temperature, it’s worth checking out the recommended temperature range for your specific PLA filament and staying within the provided figures for the best results.
As previously mentioned, you can go with the SIQUK 22 Piece 3D Printer Nozzle Set from Amazon which includes nozzle diameters of 1mm, 0.8mm, 0.6mm, 0.5mm, 0.4mm, 0.3mm & 0.2mm. It also comes with a storage case to keep them together and secure.
27. Calibrate Retraction Settings
Calibrating your retraction length and speed settings can help you avoid a ton of problems when printing with PLA, such as oozing and stringing.
These are basically the length and speed at which the filament retracts within the extruder. The best way to calibrate your retraction settings is to print a retraction tower that is made up of many blocks.
Each block will be printed at a different retraction speed and length, allowing you to easily pick the best result and get the optimal settings from it.
You can also print a small object with different retraction settings manually multiple times and evaluate which settings have produced the best results.
Check out How to Get the Best Retraction Speed and Length Settings for more information. You can also check out the following video for a nicely detailed guide.
28. Experiment with Different Settings
Practice makes perfect. Those are the words to live by in the world of 3D printing. The art of this craft is harnessed only when you keep at it relentlessly and let your experience guide you towards printing better.
Therefore, keep experimenting with different slicer settings, keep printing with PLA, and don’t forget to enjoy the process. You’ll eventually get there with time, given that you stay motivated to learn 3D printing.
Check out my article Best Cura Slicer Settings for Your 3D Printer – Ender 3 & More.
29. Learn CAD and Create Basic, Useful Objects
Learning Computer-Aided Design or CAD is an amazing way of honing your design skills and making basic objects to 3D print. Making STL files for 3D printing has its own class that’s levels above casual users.
That way, you will be able to better understand how models are designed and what it takes to create a successful print. The best part is that getting started with CAD isn’t very difficult.
Luckily, there are a good deal of great software that can help you begin your designing journey very easily. Don’t forget to use PLA as the 3D printer filament with your models to gradually get better at the craft.
Check out the video below for an illustration on how to create your own 3D printed objects on TinkerCAD, an online design software.
30. Bed Leveling is Very Important
One of the most important things with 3D printing is making sure your bed is leveled correctly since this sets the foundation for the rest of the print. You can still successfully create 3D models without a leveled bed, but they are more likely to fail and not look as great.
I’d highly recommend making sure your bed is flat and leveled consistently to improve your 3D printing experiences. If you want the best quality models as well, make sure to do this.
Check out the video below on a great method for leveling your 3D printer bed.
Composite printer: breakthrough 3D printing technology created in Russia | Articles
Russian developers have proposed a unique 3D printing technology that allows you to create composite parts of any shape. During their production, the strength losses characteristic of traditional manufacturing methods will be minimized. Until the end of 2018, prototypes of new devices will begin to be used by companies such as BMW and Airbus, and their introduction into mass production is expected in a couple of years.
Despite the outstanding characteristics of composite materials, many industrial companies are in no hurry to implement them. Modern carbon plastics may lose some of their properties in the process of creating final products from them. This is due to one of the main features of composites, which is that they are able to resist loads in only one direction - along the laying of carbon fibers (they have anisotropy), which forces manufacturers to put up with the loss of strength of final products for the sake of universality of their mechanical characteristics. However, Russian developers figured out how to turn the inconvenient feature of the material to good use.
The new Russian 3D printer , created by the developers of the Anisoprint company, is able to control the trajectory of carbon fiber laying at each point of the product. Thanks to this, specialists are able to add strength where it is critical.
In addition, the new equipment should save manufacturers of composites from having to drill holes in them for subsequent mounting of parts. It also significantly reduces strength and can lead to significant complications (in particular, the appearance of such a problem with the fuselage parts of the Boeing 787 Dreamliner slowed its time to market by several years).
- Instead of laying layers of fibers in different directions and then drilling a hole in this array that will destroy its structure, with our printer we can run reinforcing threads around the hole, similar to how wood fibers go around a knot, Fedor Antonov, CEO of Anisoprint, said. “Therefore, our materials are somewhat reminiscent of natural objects created from synthetic components.
Ultimately, this structural optimization results in products that are twice as strong and half as light as aluminium, at a comparable size. This opens up huge opportunities for the use of composite 3D printing in aviation and other areas that require the maximum reduction in weight of parts while maintaining their rigidity .
According to Alexander Gromov, Professor of the Department of Nonferrous Metals and Gold, NUST MISIS, high strength and low weight are really very important for materials. However, to fully compare the new composites with metals, many tests will still be required, which should show their properties such as resistance to abrasion, fatigue loads and chemicals .
- At the same time, today we can say that Russian specialists have solved the main problem - they have selected the formulation of the starting materials necessary to place carbon fiber in plastic in the 3D printing process. This is a significant result, since with the help of additive technologies it is possible to create parts of such a shape that cannot be achieved by casting,” Alexander Gromov added.
At the same time, according to other experts, the 3D printing method proposed by Anisoprint also has its drawbacks.
- In the new printer, carbon fiber is fused into plastic inside each layer of the part, which increases their internal resistance to mechanical stress. However, these layers are laid parallel to each other and are held together only by a binder polymer, the strength of which is limited,” explained Artem Avdeev, director of the innovative company StereoTek. — Mechanical resistance can be improved by intertwining composite layers inside the parts, making the structure of the material voluminous — this will make it possible to advance even further in the process of improving the mechanical characteristics of products and expand their applicability.
Currently, prototypes of the new printers have entered the market. In particular, the first samples of technology are working at the research center of the BMW automobile company, the Technical University of Munich and the Central Research Institute for Special Machine Building (specializes in the creation of rocket technology). In addition, by the end of 2018, the Russian composite printer will be operated by Airbus .
Russian developers are going to make the first version of the printer for full-fledged serial production in two years.
SEE ALSO
Stamped into space: Russian 3D printer will be tested for the first time on the ISS | Articles
The research program on the Russian Segment of the ISS includes tests of a 3D printer designed to operate in microgravity conditions. It will go into orbit in June this year. The main objective of the experiment is to learn how to print products with predictable characteristics, Roscosmos told Izvestia. Experts believe that at the current stage of technology development, such a device will help in the repair of household items and appliances on the ISS, but the polymer will not withstand the conditions of open space. In the future, the use of 3D printing can significantly accelerate the exploration of extraterrestrial space, simplify the organization of expeditions to the Moon and Mars, and even their colonization.
High art
The program of scientific and applied research and experiments on the Russian segment of the ISS included the development of additive manufacturing technologies for products in space. Simply put, this is printing from polymer materials using a 3D printer in zero gravity. The experiment will show how close we are to solving the problem of the operational supply of orbital stations and bases with spare parts, Roscosmos told Izvestia.
Now all the equipment used in space is delivered from Earth. This imposes serious restrictions on the weight and dimensions of the cargo, and besides, you have to take into account the delivery time - some flights have to wait weeks or even months. Therefore, one of the most important tasks arising in space exploration is the optimization of cargo traffic.
The ability to quickly, on the spot, produce the necessary tools, parts would be extremely useful when working on the Earth's orbit, and even more so during expeditions to the Moon and Mars.
But before you send a 3D printer on expeditions to distant planets, you need to learn how to print products with predictable characteristics in zero gravity. After the experiment, the samples made on board the ISS will be compared with similar samples created on Earth. So the researchers will find out the influence of microgravity on the 3D printing process and the characteristics of the created objects.
“In microgravity, the substance used for 3D printing begins to behave completely differently than on Earth,” Alexander Bloshenko, executive director of Roscosmos for advanced programs and science, explained to Izvestia. - In particular, a powder that could be melted and baked in a certain way cannot be used. Therefore, the task of the experiment is to work out the conditions in which you will have to work, and "adapt" to weightlessness in the conditions of the ISS.
Space cabinet
Printer developed at the National Research Tomsk Polytechnic University (TPU). It is similar in size to a bedside table. Weight - no more than 30 kg. The principle of its operation is the same as that of devices for terrestrial conditions - the technology of layer-by-layer imposition of a molten polymer thread is used. But the need to adapt it to work in zero gravity has made adjustments to the design and a number of printer elements, TPU noted.
- The entire design of the 3D printer is block-modular, all its components are located in a single housing. This is important for safety reasons and operating conditions of the station,” said Vasily Fedorov, head of the research and production laboratory “Modern production technologies” of TPU.
There are other features. Hot air on Earth is lighter than cold air, it goes up, and cold air comes in its place. But in zero gravity there are other convection conditions. Therefore, heat transfer in the printer will work in a completely different way. The influence of radiation is also taken into account.
- We are creating a printer so that it can work in the conditions of the ISS, that is, with continuous exposure to flows of heavy charged particles, - said Vasily Fedorov. — Doing so may cause the printer's electronic components to malfunction. Therefore, its design includes microcircuits that are resistant to radiation, and algorithms are used to correct errors in actuators.
The set of scientific equipment includes the 3D printer itself, a hermetically sealed complex with a system for filtering gases generated during the printing process, an embedded computer to control the process, and consumables.
TPU has already made a working layout and prototype equipment. He successfully passed all tests. Now in the stage of adjustment are flight samples of scientific equipment, which will go into space.
Good luck or bad luck?
Roskosmos believes that in the future 3D printing technology in zero gravity will simplify the implementation of long-distance and long-term expeditions. Apparatus and the necessary parts can be made right in space, without worrying about where to get them and how to repair broken ones. The results of the experiment on the ISS are planned to be used to develop technical requirements for the equipment of advanced industrial complexes, both orbital and planet-based.
Izvestia asked the experts to assess the potential of the experiment and the 3D printing technology itself in space.
- Classical additive technologies (layer-by-layer building up and synthesis of objects. - Izvestia) are good on Earth. Each layer of material shrinks slightly following it with the help of gravity. In zero gravity conditions, there is no such help, so the requirements for materials and printer operation parameters change. For example, the material must solidify rather quickly so as not to rise and scatter in the apparatus. The print speed should be much faster. Therefore, colleagues have to overcome certain difficulties,” explained Yousef Khesuani, co-founder and managing partner of 3D Bioprinting Solutions.
The expert also noted the need for post-processing of samples. Otherwise, tiny particles of material that need to be disposed of for safety reasons will simply scatter around the station.
— The very idea of the experiment is very interesting, and it will be useful to conduct it, — says Nikolai Kozlov, Professor of the Department of Technology of Composite Materials, Structures and Microsystems at MAI. “In my opinion, with the help of such a printer it will be convenient to create a variety of components and parts from polymers that can fail on board the station during operation or will be required during a long flight. This is convenient because the printer is easy to set up to create an object of any shape.
As for the materials used overboard, the current polymer materials widely used for 3D printing do not have sufficient resistance to space factors for this, experts say.
To assess the prospects for using 3D printers in space, we need to understand where we can get consumables. The economic feasibility of using the technology directly depends on this.
- The polymers themselves, which can be used as a material for a 3D printer, we are unlikely to find on other planets, - said Nikolai Kozlov. - These are synthetic materials, so you will have to carry all of them with you.
Theoretically, when creating planetary bases, the use of local resources, for the Moon - regolith, can reduce the cost of printing, Nikolai Kozlov noted.
- There are ideas about using solar energy to melt regolith - lunar soil, but such technologies are highly energy intensive and require large investments.