3D printer national geographic
What, Exactly, Is a 3-D Printer?
This week a 25-year-old law student at the University of Texas named Cody Wilson made international headlines when he used a 3-D printer to "print out" a functional .38 caliber pistol.
He then put design software online so that—in theory, at least—anyone in the world who downloaded the software and had access to a commercial 3-D printer and $60 worth of plastic could make their own handgun.
It was a demonstration that not only sparked a lively debate on gun control in the U.S. and abroad, but also threw a spotlight on a vibrant, fast-developing manufacturing technology that could change the shape of the future.
So what is a 3-D printer?
Invented in the mid-1980s, it is a printer that uses plastic, wax, resin, paper, gold, titanium—a whole host of materials—instead of ink to create a solid, three-dimensional object. In much the same way that your desktop printer is directed to print the words in a document, the 3-D printer's jets, guided by computer-assisted design (CAD) software, create an object by spraying or squeezing one thin layer of material at a time onto the platform, then melding them into place with a precisely directed laser. As these microscopically thin layers build up, the desired three-dimensional object slowly takes shape.
While 3-D printing is not a fast manufacturing process, it can be highly efficient because there is virtually no wastage. Unlike traditional manufacturing, where material is cut away by machinery or a lathe to create an object, the "additive" process of 3-D printing uses only what is necessary to make the object. This precision results in a finished product that is both more finely made and up to 60 percent lighter in weight—something of particular interest to the aviation industry.
What can you make with one?
In theory, just about anything. "It doesn't have to be a Saturday Night Special," says Jonathan Rowley, design director at Digits2Widgets, a London-based firm that specializes in 3-D printing. "This technology has plenty of wonderful applications. It can be used for everything from dental work to architectural models, jewelry, precision engine parts, spoilers [the wings for Formula One cars], dolls [with custom faces], sunglasses . .. The list is endless."
On a much larger scale Boeing and Airbus are already making numerous small parts using 3-D printing technology, and some have visions of aircraft-hangar-size printers creating huge sections of wing and fuselage. By 2050 entire planes may be made from 3-D "printed" parts.
For the most part, at least at present, 3-D printing is used to make prototypes, to do custom work, or for limited production runs. A major advantage is that the manufacturer doesn't need to spend a lot of money retooling machinery every time the product or specifications change—only the software needs to be modified.
What kinds of materials can the printers use?
Again, just about anything. In Australia researchers are using 3-D printer technology and living cell tissue to try to "print" nerve endings, muscle cells, and cartilage with the hope that someday they can be fused onto human limbs.
Can I do this at home?
Yes and no. The technology has been around for nearly 30 years, and in that time the cost of 3-D printers has dropped dramatically to the point where consumer models are available for as little as $1,200. These home printers, though, are typically used for making knick-knacks and ornaments—stuff that looks, well, rather homemade. Nothing too fancy.
If you are planning to manufacture high-quality goods, like jewelry, you will need to spend considerably more money for a commercial-grade printer. How much? The sky's the limit, depending on what you want to make and the sorts of materials you plan to use. Then of course there is the matter of developing the design and coding the software. And you still need to know a great deal about the physical properties and appropriateness of the materials you are planning to work with.
"It will be a while, I think, before we see a cottage industry flourishing with people making high-quality boutique goods," says Rowley. "But I can imagine such a thing in the future."
As for the white plastic, single-shot .38 that grabbed the headlines this week, that was turned out on a commercial printer that originally cost $30,000 but was bought secondhand on eBay for $5,000. A technological tour de force, perhaps, but there are cheaper and quicker ways to obtain a pistol.
Read This Next
15 iconic images from the National Geographic archive
- Photography
15 iconic images from the National Geographic archive
Over 115 years ago, National Geographic published its first picture essay and never looked back. These recent images are pulled from the National Geographic archive and celebrate the power of photography today.
Black Canada lynx seen for the first time ever
- Animals
Black Canada lynx seen for the first time ever
The dark-furred cat has a genetic condition called melanism that has been observed in about a third of cats, but not previously in this species.
Subscriber Exclusive Content
Why are people so dang obsessed with Mars?
How viruses shape our world
The era of greyhound racing in the U.

See how people have imagined life on Mars through history
See how NASA’s new Mars rover will explore the red planet
Why are people so dang obsessed with Mars?
How viruses shape our world
The era of greyhound racing in the U.S. is coming to an end
See how people have imagined life on Mars through history
See how NASA’s new Mars rover will explore the red planet
Why are people so dang obsessed with Mars?
How viruses shape our world
The era of greyhound racing in the U.S. is coming to an end
See how people have imagined life on Mars through history
See how NASA’s new Mars rover will explore the red planet
See More
Just Press Print
Please be respectful of copyright. Unauthorized use is prohibited.
Please be respectful of copyright. Unauthorized use is prohibited.
Please be respectful of copyright. Unauthorized use is prohibited.
Please be respectful of copyright. Unauthorized use is prohibited.
Please be respectful of copyright. Unauthorized use is prohibited.
Please be respectful of copyright. Unauthorized use is prohibited.
Please be respectful of copyright. Unauthorized use is prohibited.
Please be respectful of copyright. Unauthorized use is prohibited.
Please be respectful of copyright. Unauthorized use is prohibited.
Please be respectful of copyright. Unauthorized use is prohibited.
Please be respectful of copyright. Unauthorized use is prohibited.
Please be respectful of copyright. Unauthorized use is prohibited.
Please be respectful of copyright. Unauthorized use is prohibited.
Please be respectful of copyright. Unauthorized use is prohibited.
Please be respectful of copyright. Unauthorized use is prohibited.
1 / 15
1 / 15
<p>A bionic ear printed by researchers at Princeton University uses “inks” made of silicone and chondrocytes, cells that produce cartilage. The metal coil receives and transmits electrical impulses, which could stimulate the auditory nerve, as a cochlear implant does.</p>
A bionic ear printed by researchers at Princeton University uses “inks” made of silicone and chondrocytes, cells that produce cartilage. The metal coil receives and transmits electrical impulses, which could stimulate the auditory nerve, as a cochlear implant does.
Photograph by Frank Wojciechowski. Source: Michael McAlpine, Princeton University
This story appears in the December 2014 issue of National Geographic magazine.
Rocket engine parts, chocolate figurines, functional replica pistols, a Dutch canal house, designer sunglasses, a zippy two-seater car, a rowboat, a prototype bionic ear, pizzas—hardly a week goes by without a startling tour de force in the rapidly evolving technology of three-dimensional printing.
What sounds like something out of Star Trek—the starship’s replicator could synthesize anything—is increasingly becoming a reality. Indeed, NASA is testing a 3-D printer on the International Space Station to see if it might provide a way to fabricate meals, tools, and replacement parts on long missions.
Back on Earth, long-term business plans are being reimagined. Airbus envisions that by 2050 entire planes could be built of 3-D printed parts. GE is already using printers to make fuel-nozzle tips for jet engines. And interest isn’t limited just to corporate giants.
“We all know that 3-D printing is going to play a big role in the future,” says Hedwig Heinsman, one of the partners in the Dutch architectural firm DUS, which is printing a house on the banks of Amsterdam’s Buiksloter Canal.
Over three years a 20-foot-tall printer, the KamerMaker (Room Maker) will create walls, cornices, and rooms, trying out materials, designs, and concepts. “I can see a time coming where you will be able to choose and download house plans like you were buying something on iTunes, customize them with a few clicks on the keyboard to get just exactly what you want, then have a printer brought onto your site and fabricate the house,” adds Heinsman.
Additive manufacturing—as 3-D printing is also called—has been around for about 30 years. It’s the quick pace of advances that has created the recent buzz and inspired some grandiose predictions. But there is a huge and possibly unbridgeable gap between what can be made on highly sophisticated commercial 3-D printers and what you can make on a home printer. A 3-D printer works in much the same way as a desktop printer does. Instead of using ink, though, it “prints” in plastic, wax, resin, wood, concrete, gold, titanium, carbon fiber, chocolate—and even living tissue. The jets of a 3-D printer deposit materials layer by layer, as liquids, pastes, or powder. Some simply harden, while others are fused using heat or light.
The high cost of tooling up a factory has long been a barrier to developing niche products. But now anyone with an idea and money could go into small-scale manufacturing, using computer-aided design software to create a three-dimensional drawing of an object and letting a commercial 3-D printing firm do the rest.
Since a product’s specifications can be “retooled” at a keyboard, the technology is perfect for limited production runs, prototypes, or one-time creations—like the one-third-scale model of a 1964 Aston Martin DB5 that producers of the James Bond filmSkyfall had printed, then blew up in a climactic scene.
And because a 3-D printer builds an object a bit at a time, placing material only where it needs to be, it can make geometrically complex objects that can’t be made by injecting material into molds—often at a considerable savings in weight with no loss in strength. It can also produce intricately shaped objects in a single piece, such as GE’s titanium fuel-nozzle tips, which otherwise would be made of at least 20 pieces.
This same precision is making it possible to fabricate things never before made. A team of Harvard University researchers has printed living tissue interlaced with blood vessels—a crucial step toward one day transplanting human organs printed from a patient’s own cells. “That’s the ultimate goal of 3-D bio-printing,” says Jennifer Lewis, who led the research. “We are many years away from achieving this goal.”
Additive manufacturing is much slower than traditional manufacturing, but that could change, says Hod Lipson, a professor at Cornell University long involved with 3-D printing.
“Printer speed, resolution, and the range of materials that can be printed are all being developed right now, along with printers that are capable of printing with multiple materials and creating objects with working parts and active circuitry,” Lipson says.
He and his team printed a replica of Samuel Morse’s telegraph. With a nod to history, they tested it by tapping out the message an awed Morse sent in 1844: “What hath God wrought?”
God may have wrought the principles, but people are pressing the buttons. In May 2013 a political activist named Cody Wilson grabbed headlines when he announced the test-firing of the world’s first 3-D printed handgun, the Liberator, a single-shot . 38-caliber pistol made with $60 worth of plastic.
The news initially unnerved law-enforcement officials, who foresaw disposable, untraceable guns printed like term papers. But making a reliable gun is not simple—or cheap. When a California firm, Solid Concepts, printed a limited edition of a hundred Browning Model 1911 .45-caliber pistols, it did so with a printer and facilities that cost the better part of a million dollars.
“It’s simply a lot easier for crooks to get hold of a gun the old-fashioned way—buying them or stealing them—than to fuss over a 3-D printer for a couple of days, only to end up with a warped plastic blob or, even worse, something that blows up in their hands,” says Jonathan Rowley, design director of Digits2Widgets, a London 3-D printing firm that made the parts of a nonworking version of Wilson’s gun for the Victoria and Albert Museum.
Few people will be crushed by not being able to print a Saturday night special, but many may be disappointed with the misshapen trinkets that are the typical fare. “People read about the fabulous things that are being made with 3-D printing technology, and they are led to believe that they will be able to make these things themselves at home and that what they turn out will be of a really high standard of workmanship,” Rowley says. “It won’t be.”
While consumer printers may one day allow us to make whatever we like, Rowley envisions a different grassroots revolution, one where people can test ideas that once would never have made it off the back of an envelope.
Read This Next
15 iconic images from the National Geographic archive
- Photography
15 iconic images from the National Geographic archive
Over 115 years ago, National Geographic published its first picture essay and never looked back. These recent images are pulled from the National Geographic archive and celebrate the power of photography today.
Black Canada lynx seen for the first time ever
- Animals
Black Canada lynx seen for the first time ever
The dark-furred cat has a genetic condition called melanism that has been observed in about a third of cats, but not previously in this species.
Subscriber Exclusive Content
Why are people so dang obsessed with Mars?
How viruses shape our world
The era of greyhound racing in the U.S. is coming to an end
See how people have imagined life on Mars through history
See how NASA’s new Mars rover will explore the red planet
Why are people so dang obsessed with Mars?
How viruses shape our world
The era of greyhound racing in the U.S. is coming to an end
See how people have imagined life on Mars through history
See how NASA’s new Mars rover will explore the red planet
Why are people so dang obsessed with Mars?
How viruses shape our world
The era of greyhound racing in the U.
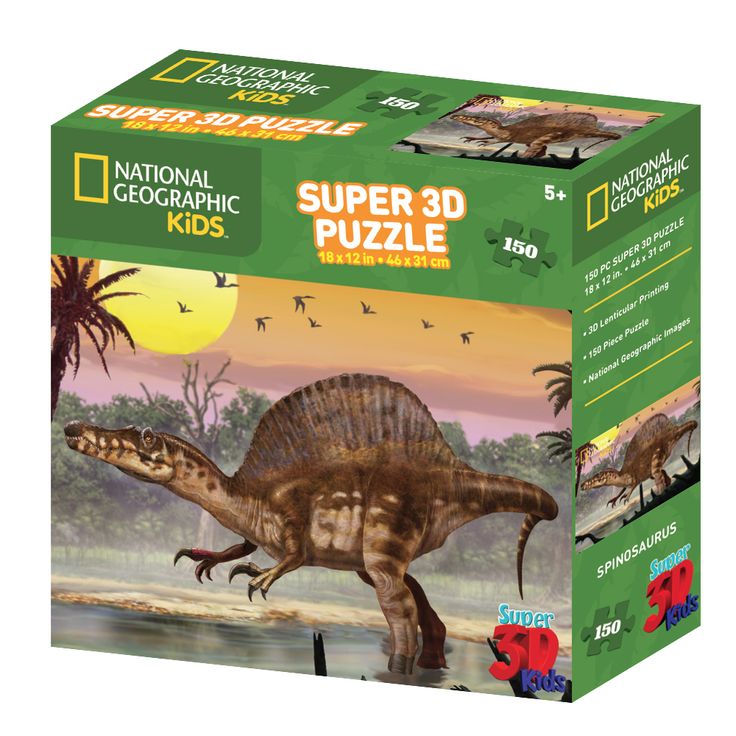
See how people have imagined life on Mars through history
See how NASA’s new Mars rover will explore the red planet
See More
3D printing in medicine: from discoveries to practice
3D printing technology appeared thanks to the discovery of the American inventor Charles Hull in 1983 and gradually spread to all areas of production.
The use of technology in global healthcare began in the 2000s. Since then, the use of 3D printing for medical purposes has evolved significantly. What has happened in these 30 years in the industry, what changes have made scientists believe in resolving the most complex issues of medicine?
The first 3D printers.
Shortly after the 3D printing device was patented, Hull 3D Systems launched the first 3D printer (1988). Due to high equipment costs, large industrial corporations first registered the right to use the technology, but the investment quickly paid off, and 3D printing began to be used in architecture, education, cartography and retail.
Opening History 3D print
During the manufacture of small plastic parts for the future prototype instead of fixing with ultraviolet radiation of individual thin layers of photosensitive polymers, Ch. Hull put on each other thousands thin layers of plastic and on each such layer I applied the epoxy resin that I had previously used to make coatings, and fixed the already obtained shape with ultraviolet light. As a result of the experiment, it became clear that the principle of layer-by-layer imposition and gluing of plastic will allow creating three-dimensional objects of any shape.
The technology was first applied in medicine
In 1999, a group of scientists and physicians from the Wake Forest Institute of Cell Regenerative Medicine (USA) implanted an organ grown on the basis of the patient himself, in the laboratory of the patient, in the USA. The operation set a precedent for creating an exact copy of the patient's organ, the bladder, using computed tomography and a 3D printer.
A functioning liver has been created.
Wake Forest Institute scientists have created a functioning liver based on bio-ink. This time they didn't just print a base for overlaying living tissue, but accurately reproduced liver tissue. Although the organ could not be transplanted, the experiment was an impressive confirmation of the concept of printing organs and tissues.
3D printed surgical instruments invented
Photo source: NCBI
Facial reconstruction surgery.
In 2014, Swansea surgeons reconstructed the face of a motorcyclist who was badly injured in a road accident. Steven Power became the first patient in the world with a craniofacial injury for which doctors used 3D printing at every stage.
Since then, we have regularly received news of successful 3D-printed implants or transplantation of bones and joints. Messages about the joint success of scientists, doctors and engineers come from China, the USA, and European countries.
How are technologies developing in Russia?
-
- Nizhny Novgorod doctors of the Volga Federal Medical Research Center (FSBI "PFMIC" of the Ministry of Health of Russia) in 2016 performed two successful operations to implant 3D-printed hip joint prostheses.
- Specialists from the laboratory of Tomsk State University have invented a variant of bone tissue based on phosphorus and calcium. Scientists have suggested that tissue created from animal bones, and therefore biocompatible with the human body, can eventually replace titanium implants.
- The clinic at the St. Petersburg State Pediatric Medical University successfully performs operations using simulated organs to prepare for intervention for heart defects. Now, to save the child, instead of several complex operations, one will be needed - a long, but less risky one.
We think over the right access, how to choose the tactics necessary for this operation, choose the type of operation. Because with complex congenital heart defects with difficult hemodynamics, the details are of tremendous importance. And the correct approach to the operation will have either a positive or a negative result.
Evgeny Kulemin, cardiac surgeon
What is 3D printing?
Three-dimensional printing, or additive technologies, is a production method in which solid three-dimensional objects are created by sequential layering of materials. Plastic, metal, ceramics, powder, liquids and even living cells are used.
Additive manufacturing is the opposite of subtractive manufacturing and traditional methods, milling and cutting, where the appearance of the product is formed by removing excess, rather than layering materials.
Steps for creating a 3D object:
- Modeling an object in a computer program
- Seal
- Post-processing
3 Advantages of the technology:
Press speed, high accuracy and building an object in the desired geometric form. The creation of complex and anatomically accurate medical structures and the embodiment of three -dimensional tangible objects became possible thanks to translation due 2D radiographic data such as X-rays, MRI (Magnetic Resonance Imaging) or CT (Computed Tomography) images into digital files and further converting the virtual model into a solid 3D product.
How is 3D printing useful for medicine?
Epis, grown on the basis of the patient's cells, in the Laboratory of the Wake Forest Institute.
Photo source: National Geographic
In the 16 years of 3D printing in medicine, doctors around the world have performed hundreds of successful operations, and scientists continue to explore the possibilities of technology. Western researchers called 2016 a turning point for additive manufacturing in medicine.
How to keep a child busy? 3D print Einstein's favorite toy!
News
Subscribe to the author
Subscribe
Don't want
27
Children must play. They should, because games contribute to development - physical and mental. But in our time, kids spend more and more time watching cartoons and computer games, which makes development rather one-sided. The Real Play Coalition, formed by the Lego Foundation, National Geographic magazine, LEGO and Unilever, offers to pump the space between the ears of future scientists, engineers and architects the way Albert Einstein did - with the help of Anker-Steinbaukasten!
Anker-Steinbaukasten is a play set made of stone building blocks.
The blocks of the original kits, produced in various versions to this day, consist of a mixture of quartz sand, chalk and linseed oil pressed into molds. But why not take the combination of business and pleasure to a new level and print the constructor on a 3D printer, preferably with the participation of the child himself?
For this purpose, the coalition contacted the American collector Seth Keller, who bought Einstein's favorite toy at an auction for $160,000. 3D printing of a replica will cost much less, and you won’t have to model anything, because Seth kindly agreed to the offer to scan a valuable find. The constructor consists of 160 blocks, originally made in three shades - "brick" red, yellowish-brown limestone and "slate" blue. The 3D-scanned models are edited and ready for printing, and the archive can be downloaded completely free of charge from the Open Einstein website.
Do you have interesting news? Share your developments with us, and we will tell the whole world about them! We are waiting for your ideas at news@3Dtoday.
Learn more