3D printer chamber
Open, and enclosed passive/active chamber 3D printers
All plastics, when extruded at high temperature, undergo a shrinkage during cooling which can be between 0.3 % and 4 %. This shrinkage can cause deformations, if the cooling is not smooth and homogeneous, giving rise to problems such as warping, delamination of layers or dimensional deformations of the part.
Material |
% of contraction during cooling |
---|---|
PLA |
0.3 - 0.5 |
PETG |
0.2 - 1.0 |
Nylon 12 |
0.7 - 2.0 |
Nylon 6-6 |
0. |
ABS |
0.7 - 1.6 |
ASA |
0.4 - 0.7 |
PP |
1.0 - 3.0 |
HIPS |
0.2 - 0.8 |
PC/ABS |
0.5 - 0.7 |
Fibre-reinforced nylon |
0.5 - 1.0 |
PEEK |
1.2 - 1.5 |
Fibre-reinforced PEEK |
0.5 - 0.8 |
PVDF |
2.0 - 4.0 |
Table 1.
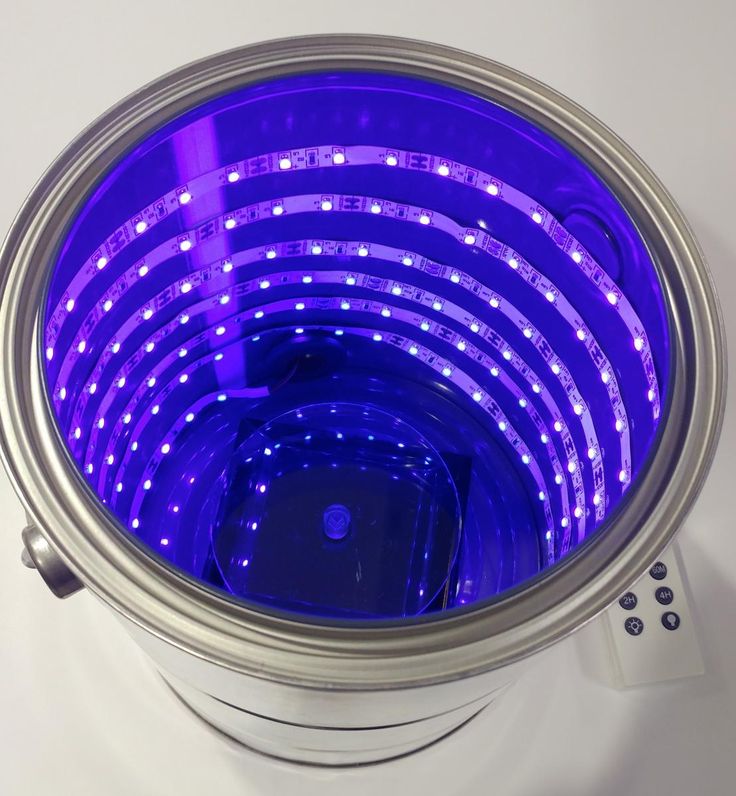
To avoid this problem, the temperature around the part should ideally be slightly lower than the material's glass transition temperature (Tg) throughout the printing process, and should be slowly reduced to room temperature after printing.
Material |
Tg (ºC) |
Printing temperature (ºC) |
---|---|---|
PLA |
40 - 60 |
190 - 215 |
PETG |
75 - 85 |
220 - 260 |
Nylon 12 |
55 - 65 |
260 - 290 |
Nylon 6-6 |
75 - 85 |
255 - 280 |
ABS |
90 -100 |
220 - 240 |
ASA |
90 - 100 |
240 - 260 |
HIPS |
80 - 90 |
210 - 240 |
PC/ABS |
100 - 150 |
270 - 285 |
PEEK |
140 -160 |
380 - 400 |
PEI |
190 - 210 |
350 - 400 |
Table 2: Tg and printing temperature of various filaments.

Those materials that suffer low shrinkage rates (less than 0.5%) do not require heating the part environment, as the shrinkage effects are practically negligible, so they can be printed perfectly well on open 3D printers, even large parts. These materials are mainly PLA and most PETg filaments (but not other copolyesters such as PET or CPE), as well as their derivatives.
It is possible to print materials with higher shrinkage percentages on open printers, however this possibility is limited to small parts, so with this type of materials it is advisable to use closed printers or printers with an active heated chamber.
Image 1: An open 3D printer. Source: Prusa3D
Open printers are mainly recommended for printing PLA, PETg and flexible filaments.
Closed printers or printers with a passive heated chamber
Closed printers are those whose printing area is completely enclosed. Some manufacturers use the term passive heated chamber, as they tend to accumulate the heat generated by the printing platform.
The internal temperature that these printers can reach varies greatly from one printer to another depending on the material they are made of, their volume, the temperature of the printing platform, the quality of the insulation and the temperature of the room where they are located. In general, the best quality printers are capable of providing temperatures between 45°C and 65°C at best.
Although these temperatures are not very high, they are close to the Tg of materials such as Nylon, ABS or ASA, making them easier to print and allowing the production of larger parts. Although these types of printers substantially improve the printing of these types of materials, they can fail with large volume parts. These printers are recommended for printing small to medium sized parts in PETg, ABS, ASA, Nylon or HIPS.
Image 2: A 3D printer with a passive heated chamber. Source: Raise3D
In general, it is not advisable to use PLA in this type of printers when they are completely closed, as the heat generated can exceed the Tg of the filament, causing it to soften inside the hotend and cause a jam.
Closed printers with an active heated chamber
These are 3D printers capable of controlling the temperature inside the chamber. They are usually more complex and cost more than the previous ones. They also incorporate high temperature hotends (400 ºC - 500 ºC) and liquid cooling systems.
There are two types: high temperature and low temperature.
Low-temperature heated chamber
Low-temperature active heated chamber printers typically allow controlled maximum temperatures of between 80 ºC and 120 ºC. These printers are designed for the production of high quality, large ASA, ABS, Nylon or PC parts.
Image 3: A 3D printer with a low-temperature heated chamber. Source: 3ntr
Although these types of 3D printers are sometimes advertised as compatible with PEEK, they are not usually compatible with all types of PEEK, only with some low-temperature PEKK, and always limited to small parts.
These types of 3D printers are ideal for producing ABS, ASA, Nylon and PC parts that require good dimensional stability and low deformations, making them the best option when producing technical parts or functional components with these materials.
High temperature heated chamber
In general, they allow temperatures in the range of 160 ºC - 180 ºC to be controlled. These printers are specifically designed for the production of parts in PEEK, PEKK and PEI, so it is not common to use other types of materials. This equipment is expensive and requires specialized and trained personnel for its use.
Image 4: A 3D printer with a high temperature heated chamber.
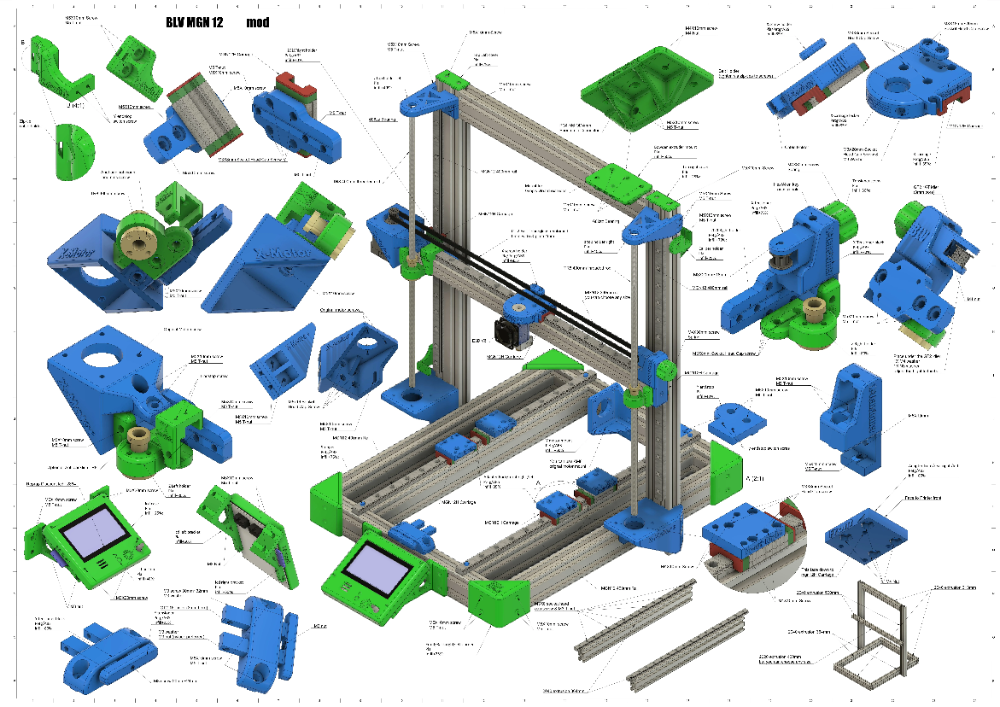
When selecting a type of printer, it is very important to determine beforehand what type of parts and materials will be used.
This guide discusses the concepts in a general way and does not focus on a specific make or model, although they may be mentioned at some point. There may be important differences in calibration or adjustment procedures between different makes and models, so it is recommended that the manufacturer's manual be consulted before reading this guide.
Subscribe to our monthly newsletter and you will receive every month in your email the latest news and tips on 3D printing.
* By registering you accept our privacy policy.
Bringing High Temperature 3D Printing To The Masses
Despite the impressive variety of thermoplastics that can be printed on consumer-level desktop 3D printers, the most commonly used filament is polylactic acid (PLA). That’s because it’s not only the cheapest material available, but also the easiest to work with. PLA can be extruded at temperatures as low as 180 °C, and it’s possible to get good results even without a heated bed. The downside is that objects printed in PLA tend to be somewhat brittle and have a low heat tolerance. It’s a fine plastic for prototyping and light duty projects, but it won’t take long for many users to outgrow its capabilities.
The next step up is usually polyethylene terephthalate glycol (PETG). This material isn’t much more difficult to work with than PLA, but is more durable, can handle higher temperatures, and in general is better suited for mechanical parts. If you need greater durability or higher heat tolerance than PETG offers, you could move on to something like acrylonitrile butadiene styrene (ABS), polycarbonate (PC), or nylon. But this is where things start to get tricky. Not only are the extrusion temperatures of these materials greater than 250 °C, but an enclosed print chamber is generally recommended for best results. That puts them on the upper end of what the hobbyist community is generally capable of working with.
But high-end industrial 3D printers can use even stronger plastics such as polyetherimide (PEI) or members of the polyaryletherketone family (PAEK, PEEK, PEKK). Parts made from these materials are especially desirable for aerospace applications, as they can replace metal components while being substantially lighter.
These plastics must be extruded at temperatures approaching 400 °C, and a sealed build chamber kept at >100 °C for the duration of the print is an absolute necessity. The purchase price for a commercial printer with these capabilities is in the tens of thousands even on the low end, with some models priced well into the six figure range.
Of course there was a time, not quite so long ago, where the same could have been said of 3D printers in general. Machines that were once the sole domain of exceptionally well funded R&D labs now sit on the workbenches of hackers and makers all over the world. While it’s hard to say if we’ll see the same race to the bottom for high temperature 3D printers, the first steps towards democratizing the technology are already being made.
Engineering Challenges
Put simply, a machine that supports these so-called engineering plastics needs to be an amalgamation of a traditional 3D printer and an oven. But of course, therein lies the problem. The printer itself, especially of the type and quality that we’ve become accustomed to at the desktop level, wouldn’t survive in such an environment. For a consumer 3D printer to successfully produce parts in PEI and PEEK, it would need to be extensively modified; which is exactly what NASA did with a LulzBot TAZ 4 back in 2016.
LulzBot TAZ 4 modified for high temperature printing.The first step was building an insulated enclosure that could fit around the TAZ 4, and installing an array of 35 watt infrared heating lamps inside of it. Naturally the machine’s exposed electronics would overheat in such an environment, so they had to be relocated to the outside of the box.
The stepper motors would overheat as well, but rather than trying to move them, the team at Langley Research Center opted to design cooling jackets to fit over each motor through which pressurized air could be circulated.
Like other desktop 3D printers, the TAZ 4 also utilized a number of printed parts in its construction. Printed in ABS , these parts would have quickly failed inside the heated chamber meant to support PEEK. The parts were reprinted in PC, but even this material wasn’t resilient enough for permanent use. So in classic RepRap tradition, the team printed the third and final set of parts on the modified printer itself in a form of PEI known commercially as Ultem.
Somewhat surprisingly, the team had little trouble upgrading the TAZ 4 with a hotend and nozzle that could extrude plastics at up to 400 °C. The popular E3D-v6 hotend costs less than $100 USD and was found to be capable of reaching these temperatures, though the team did need to replace its thermistor with a higher-rated model and make some adjustments to the printer’s Marlin firmware to allow it to reach temperatures that under normal circumstances would trigger a thermal shutdown.
Ultimately, the NASA report concluded that the modifications to the LulzBot TAZ 4 were a complete success. They noted that attempting to print PEI with the IR heating lamps off lead to serious print issues such as warping and delamination, though this was to be expected. No final dollar figure is given for the cost of the modifications, but considering the base price of a TAZ 4 was approximately $2,200 USD at the time, the entire project was likely 1/10th the cost of comparable commercial offerings.
Starting from Scratch
NASA’s experiment showed that it was possible to modify an existing open source desktop 3D printer to print high temperature engineering plastics, and they even showed it could be done relatively economically. But nobody would say that bootstrapping this way was an ideal solution. There was too much duplicated effort involved in the conversion, as the engineers had to specifically undo design choices originally made by LulzBot. Even so, the experiment did create a valuable baseline for other projects that want to start from scratch.
Just last month, a team from the Michigan Technological University unveiled Cerberus, an open source high temperature 3D printer capable of producing parts in PEI and PEKK that can be built for just $1,000 USD. Rather than attempting to adapt an existing design, the team started from the ground up with high temperature printing in mind. All of the sensitive electronic components are mounted well away from the sealed build chamber, which uses a mains-powered 1 kW space heater core to rapidly bring it up to operating temperature.
Crucially, all of the stepper motors have also been moved outside of the build chamber. While this does make the kinematics somewhat more complex than what you’d see in a traditional desktop 3D printer, it means the Cerberus doesn’t need a dedicated motor cooling system like NASA’s modified TAZ did.
A simplified design combined with the use of off-the-shelf control electronics including the Arduino Mega 2560 and RAMPS 1. 4 board, and the same E3D-v6 hotend used on the modified TAZ 4, puts the Cerberus well within the means of the motivated hobbyist. Especially since the team has provided clear and detailed assembly instructions for their printer, something notably missing from NASA’s report.
Expanding Possibilities
Between NASA’s TAZ 4 retrofit and all-new designs such as the Cerberus, it’s clear that the technical capability to print PEI and PEEK objects in the home workshop is there for anyone who wants it badly enough. It’s not quite as easy as buying a $200 3D printer on Amazon yet, but if the demand is there, more low-cost machines based on these core principles will certainly start hitting the market. It’s really not much different than the current wave of affordable laser cutters that have been taking over makerspaces these last few years.
Makers all over the globe have been printing PPESo, is there a demand for them? This time last year, the answer might have been different. But with the world still combating the COVID-19 pandemic, there’s a new demand for rapidly produced personal protective equipment (PPE) that nobody could have anticipated.
As explained in the documentation for Cerberus, the team at Michigan Technological University was inspired to look into developing an affordable high temperature 3D printer specifically because it could be used to create PPE that would survive heat sterilization. Rather than being disposable, the team believes items such as face masks printed in PEKK could be used over the long term.
Printed parts that can be repeatedly sterilized would obviously have other potential medical applications. A portable low-cost machine that can produce these components could potentially save lives in remote areas of the world were rapid access to traditional supplies and equipment may be unavailable.
Critics of 3D printing have often said that the core failing of the machines is that the parts they print are rarely robust enough to be used as anything more than a rough prototype. But when a $1,000 printer can produce parts in aerospace-grade materials, it seems like we’re closer to a manufacturing revolution than ever before.
📷 Best Camera 3D Print Files・Cults
📷 Best Camera 3D Print Files
Free Download Camera Accessories 3D Files
printer accessories for your camera. You can find handles, cases, protective cases, straps, tripods for your Canon, Nikon, Leica, Sony, Panasonic cameras, etc. 3D printing will help you get the most out of your camera.
nine0008 Lens Cap HolderFree
Lens Hood
Free
Camera Gimbal
Free
Made with Love Bokeh Kit
Free
LiftPod - Multipurpose Foldable Stand
Free
nine0008 Bokeh KitFree
SD Card Holder
Free
Professional DSLR slider V4.
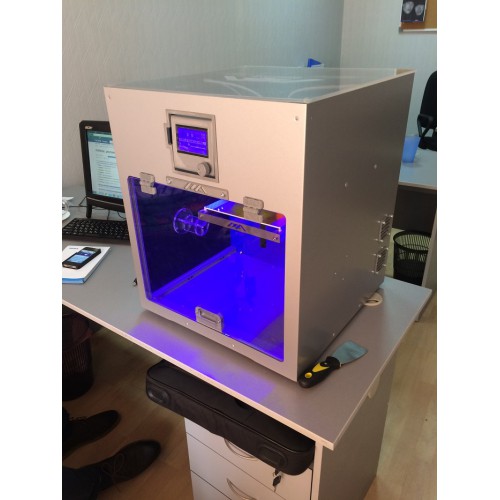
Free
Flip Lens Cap
Free
LiftPod - Easy Lock Edition
Free
Electric_Driver_Upgrade_For_Slider_V4.0
Free
Adapter thread M42 to Sony E (NEX)
Free
Shoulder rig
Free
Smartphone teleprompter - tripod adapter
Free
Foldable Mini Tripod
Free
nine0008 3D printed pinhole cameraFree
SD and micro SD holder 1-10 elements
Free
60 NeoPixel Ring Camera Mount
Free
DSLR Camera FollowSlider V2.

Free
Camera hot shoe - Universal phone holder
Free
3D Printed Pinhole 35 mm
Free
Canon EF Eyecup
Free
Canon lens hood
Free
Camera Lens Cap Holder - 62mm
Free
Sony A6000/A7 Hot Shoe Cover
Free
Tripod Ball Head
Free
Simple Camera Slider
Free
Sony E-mount Rear Lens Cap
Free
Proteus LED Light Panel - DIY and Expandable
Free
Cage modular DSLR
Free
Rollei QAL-40 Camera Mounting Plate (C4i, C5i, C40i, C50i, Compact Traveler No 1, Compact Traveler No 10, CT-4A, CT-5A, CT-5C, M5 Mini, PGA-584, PGA-484, TT-1, T2S)
Free
Tripod Leveler
Free
Smooth Q Gimbal - Camera Attachment (Sony RX100 & Others)
Free
Shoulder rig for DSLR (NOT just for Canon 5D)
Free
Hand held Camera Rig
Free
Mini Tripods
Free
Adapter m43 (m4/3) to canon FD lens
1,50 €
Camera speedlight umbrella flash holder
Free
Lens cap 55mm SONY camera
Free
1-Wege-Stativneiger, 1 Way Tilt Head
Free
Sony A-Mount Overhead Lens Mount
Free
Sony E-Mount body to Nikon F-Mount Lens adapter
Free
Motorized Camera Slider MK3
Free
Protective cage for cage modular DSLR
Free
Digital Camera Pinhole Adapter
Free
Handle for Cage modular DSLR
Free
Lens cap
Free
Hot Shoe - Camera Sight
Free
Here is our selection of best STL files for camera , all these accessories are taken from Cults STL file library and available for 3D printing .
This collection includes free 3D files of camera accessories. Many 3D models of were created by members of our 9 community0202 3D designers as well as photographers. Therefore, they are fully aware of the operating limitations of each camera. They have designed a very wide range of 3D printed camera accessories for cameras for owners of Canon, Nikon, Leica, Sony or Panasonic cameras. All brands of cameras are represented here.
Many camera parts are made of plastic, as are accessories such as tripods, sun visors or shutters. In this context, it is quite logical to think about 3D printing. Therefore 3D designers compete in ingenuity, creating truly ingenious models, such as gambling or time-lapse automatic accessories.
How to choose a 3D printer, or why you need a heating table and a closed chamber In this article I will talk about the different categories of printers for this very important parameter.

Printers without underbed heating
They are able to print only one type of plastic - PLA. This material is suitable for prototypes, souvenirs, and when heated to 60 ° C, it becomes soft and the product loses its shape. With great effort on such printers, you can try to print with other materials, but the result will not please you. Usually these are Prusa-type printers with a movable table, but there are also "cubes".
Problems occur due to shrinkage (reduction in size) of the plastic product after cooling. If the plastic shrinks (and this is almost all plastics, except for PLA), then the edges of the product begin to tear off the table on which the print is being made, the geometry of the product is irreparably damaged or it completely peels off from the table, risking damage to the print head, which continues to move. nine0007
The plus (or minus?) of such printers is that manufacturers save not only on the table heater, but on everything else. Therefore, these are cheap printers.
At the same time, in the description of such printers, the absence of table heating may not be indicated in any way (be careful!), but sometimes the possibility of printing with other plastics, except for PLA, is indicated, which misleads the buyer. And you will encounter printing problems after purchasing such a printer.
The best known non-heated printer is the Makerbot Replicator 2
From Chinese models - TEVO Michelangelo
Next, the story will be about more interesting printers with a heated table from 100 ° C to 170 ° C, which are designed for printing with plastics with shrinkage - from classic ABS to Polycarbonate. The higher the maximum temperature of the table, the more plastics you can print, because. heating of the table prevents damage to the part due to shrinkage during printing. At the same time, the higher the melting temperature of the plastic, the stronger the table should be heated. nine0007
Printers with heated table up to 100°C
Suitable for printing with many plastics, except for technical ones. At the same time, printing large products with popular ABS plastic at such a low temperature will be problematic. In reality, ABS requires from 110°C to 130°C on the table, especially for cheap brands with high shrinkage, which are very widely represented on the market. Printing with more interesting technical plastics - nylon, polypropylene, polycarbonate, on such printers will not work at all. nine0007
Chinese printers include Anycubic, various Flashforge models.
Printers with heated table up to 120°C
Perfect for ABS printing. But, if you need to print large ABS products, then such a printer also needs a closed print chamber. It is needed to maintain a high air temperature around the printed product, which reduces shrinkage during printing along the entire height of the product. The higher the chamber temperature is kept, the better for printing! nine0007
And this is where things get interesting. Those manufacturers who have conventional models with an "open chamber" cover them with a plastic transparent "aquarium" on top, and sellers offer them under the guise of printers with a closed chamber! Of course, such a solution is cheap, but the larger the volume of the chamber, the more difficult it is to maintain a high temperature in it, and in this case the volume increases significantly. This means that in such printers, the temperature in the chamber will be lower than necessary for high-quality printing.
Even more interesting is the situation when the printer is closed on the sides, but completely open on top and does not have any cover at all. At the same time, sellers pass them off as printers with a closed camera (be careful!).
The question is, why not close any printer from above completely, without increasing the volume with an "aquarium"? Yes, because all simple models are designed so that a bundle of wires rises vertically from the extruder (print head), as well as a tube through which a thread with plastic is fed (look carefully at the photos of the printer from all sides when choosing). All this sticks out from the top of the printer and does not allow it to close normally. This is especially true for printers with remote Bowden plastic feed, where the motor pushing the plastic thread is placed on the printer body. nine0007
It would seem, so what? Well, turn the wires to the side of the extruder so that they do not stick up and do not interfere ... However, for this you need to apply design solutions with a horizontal arrangement of wires and tubes suitable for the extruder, and design the printer initially taking into account the closed chamber.
Interestingly, even some expensive closed imported printers have a large height and an increased clearance inside the chamber between the extruder and the top cover, because. in them, the designers could not (did not want to) turn the plastic supply tube horizontally. So, in them the volume of the chamber is larger than necessary. nine0007
Most of both imported and domestic printers fall into this category.
Printers with heated table from 130°C to 150°C
These printers are already quite well developed by designers. Most of these printers do have a well-heated closed chamber with side wires and extruder tubes. They can print both large products made of ABS plastic, and small products made of technical plastics - nylon, polypropylene, polycarbonate. nine0007
Of the domestic printers in this category, we note Picaso3D and PrintBox3D.
Printers with heated table up to 170°C
Here we come to closed printers with a very high table temperature. These printers have been engineered to take into account the trend in 3D printing to increase operating temperatures, which means the ability to print with increasingly durable, heat-resistant plastics. There are few such printers, they are expensive, with rare exceptions.
Why heat the table so much? The fact is that the higher the melting temperature of the plastic, the more the table and the surrounding air in the chamber must be heated, otherwise the product will peel off the table during printing and printing will be interrupted. So, for polycarbonate, the extruder print temperature can reach 310 ° C. If small details can be printed at a table temperature of 130°C, then medium ones are already from 150°C, and large ones can be kept on the table only at 170°C.
In addition, these printers have the potential to print other refractory plastics. For example, at an extruder temperature of 400°C, PEEK (polyether ether ketone) can be printed. This refractory and durable plastic is used in aviation and space technology. nine0007
In this high-temperature category, we note the Chinese Intamsys FUNMAT HT printer with an extruder temperature of up to 450°C, a bed temperature of up to 160°C.
Of the domestic ones, we cannot fail to mention the Faberant Cube
3D printer with extruder temperature up to 340°C, bed temperature up to 170°C.
Terminals
If you want to print with different plastics, and not just one PLA, then the 3D printer must have a heated bed.