3D printed camera tripod
Tripod best 3D printer models・Cults
Telescoping Photography Reflector Tripod Adapter
Free
Amazon Basics Tripod Plate
Free
Mobile holder for Tripod
Free
Tripod MagSafe Mount
€2.77
Tripod MX 1000 Quick Release Plate
Free
Universal binoculars holder on tripod
Free
Telescopic Pvc Tripod For Studio Light
Free
Stove Temple Tripod 3D model
€4.99
Stove Temple Tripod 3D model
€4.99
GOPRO HANDLE
Free
3d printed cell phone holder || HIBRID DESIGN (UPDATE stl)
Free
Prusa MK3 Logitech C920S Web Cam Mount
Free
Beagle Camera Mount
Free
YATMo - Yet Another Tripod Mount
Free
Professional Camera Tripod
€5 -60% €2
Lighting tripod securing bracket gender
€0. 96
Raspberry Pi Zero 3D Printed IR Camera Case
€2.50
Tripod (Folding) Remix
Free
Tripod support
€1.25
Xiaomi Redmi 3 tripod adapter
Free
Raspberry Pi (model 3 A+) 3D Printed IR Camera Case
€3.50
1/4-20 Screw with knob
Free
Universal Phone holder tripod
€1
Xperia Z3 tripod mount
Free
Ikea Table Pi Cam Tripod Clamp
Free
Tarion TR-V1 base plate
Free
Smartphone tripod mount.
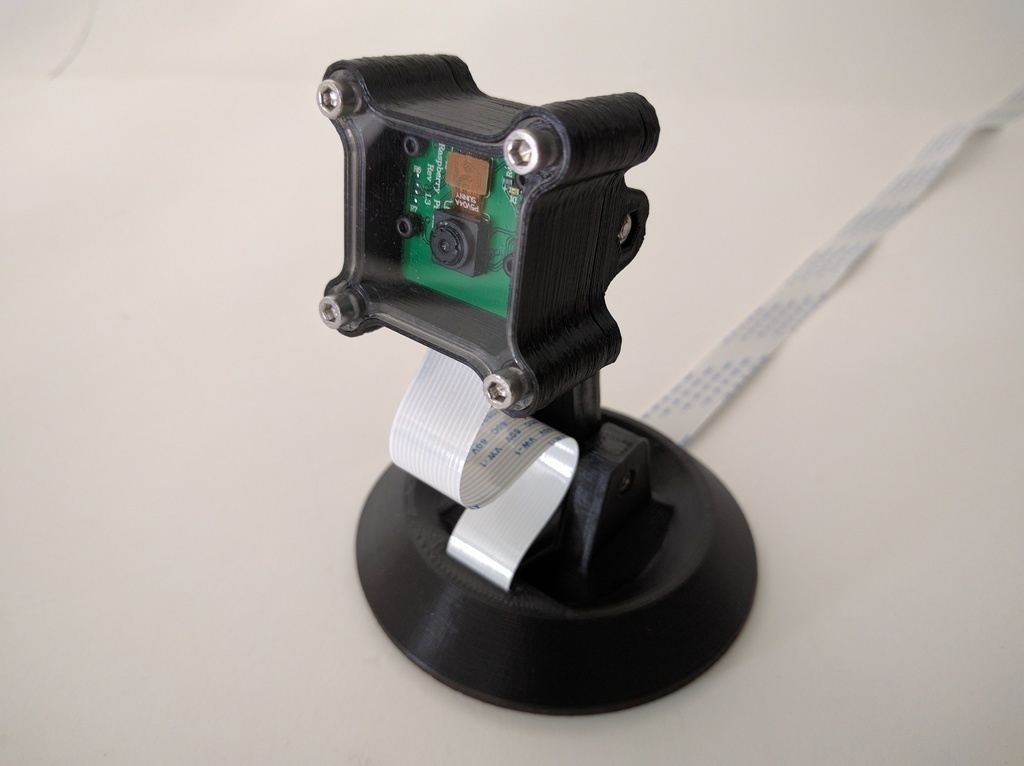
€3.89 -10% €3.50
Tripod
Free
Ball Stand with Plaque
Free
Part of Hama tripod
Free
VirtualBoy Tripod Bracket
Free
Kinect 360 Scanner Tripod
Free
tripod for mini typographic prism
Free
Mobile phone Cage
€10.90
MagSafe Mount
€2.25
M240D Pintle and Adapter for M2(M122) Tripod
€4. 16
bipod bottle mount
€12.50
Tripod to C-Stand Adapter
Free
Tripod
Free
Tripod pad - Hamma - Gamma Series
Free
Bottel Stand Ø 100mm
Free
Snowball Tripod Extension 50-200mm
€1.42
F-35 grabs cell phone
€0.50
Phone Holder for tripod
€0.50
Sony Camera Tripod
€4.95
GoPro Selfie handle
Free
Tripod chandelier
€2
Camera Tripod
€1. 04
How XSPECTER Combines SLA and SLS 3D Printed End Use Parts to Manufacture Its Outdoor Camera Tripod
With an innovative idea and lots of motivation, many entrepreneurs have already managed to fill gaps in the market. After he couldn't find anything similar available, Matthias Mähler had the idea to build the first prototype of a special camera tripod for night vision and handheld thermal imaging devices.
One of the main challenges was to implement a complex product design, which would have required an initial investment of more than €100,000 in tooling had he chosen injection molding. Without any prior knowledge of how the product would work on the market, this would have been very risky for a small startup. By using 3D printing in developing and later manufacturing the tripod, however, it was possible to avoid this substantial investment. Now, his company, XSPECTER, manufactures its first fully developed camera tripod T-Crow XRII in-house and is successfully selling it through an exclusive partner.
In an interview, Mähler told us how a finished product can be manufactured using a combination of different 3D printing technologies and why he chose this process.
Webinar
Watch this webinar to learn how to achieve custom manufacturing and low volume production of end-use parts quickly and cost-effectively with 3D printing.
Watch the Webinar Now
Night vision and handheld thermal imaging devices are standard equipment for hunters, boaters, and in the security industry. The problem: the devices do not work through glass and windowpanes. When driving a car at night, this means that drivers have to hold the device out of the open window by hand or get out of the vehicle again and again.
Recreational hunter and entrepreneur Matthias Mähler set about looking for a suitable solution to mount his devices on the outside of his vehicle.
After realizing that there was no suitable mount or tripod on the market, he took matters into his own hands. He began with the prototype construction of a stabilizing and controllable tripod for night vision and thermal-imaging devices, which can be mounted on the roof or windowpane of a car using suction or magnetic feet.
The T-Crow XRII with different cameras on the car window (left) and on the car roof (right).
With integrated 360° rotation and an additional tilt range of 55°, the T-Crow tripod from XSPECTER enables you to comfortably track animals and obstacles from inside the vehicle.
The thermal image on a tablet screen inside the car.
“3D printing was integrated into my production line because I used these technologies to produce the prototypes. It worked so well that we ended up designing the entire product using various 3D printing technologies, and we are still producing it with 3D printing today,” says Mähler.
First, Mähler iterated several prototypes of the tripod in partnership with 3D printing service providers on FDM printers. Once the rough product design was in place, he contacted Formlabs partner AMPro 3D for advice on which 3D printing technologies and materials would be suitable for the first series production.
“We adapted the whole thing to the SLS process, because the high details and the lack of support structures naturally give you many more options in SLS printing. We went almost seamlessly from the prototype to series production.”
Matthias Mähler
A ready-to-ship T-Crow tripod with the housing produced in Nylon 12 Powder.
He chose the Formlabs SLS 3D printer Fuse 1 as well as the large-format SLA 3D printer Form 3L to initiate the mass production of T-Crows through 3D printed end-use parts.
"I believe that the Formlabs 3D printers really are the best printers currently available on the market in terms of value for money"
Matthias Mähler
White Paper
In this white paper, we evaluate the value proposition of bringing SLS 3D printers in-house, in comparison with outsourcing SLS parts from a service bureau.
Download the White Paper
For the manufacturing of the T-Crows, XSPECTER relies on a combination of SLA and SLS 3D printing to produce almost all of the components for the 3D printed camera tripod, except for the electronics.
The case is made on the Fuse 1. Thanks to the Formlabs material Nylon 12 Powder, the case remains light and is resistant to environmental impacts. It is also very well-suited for subsequently melting in threaded bushings during assembly.
For axles and gears, XSPECTER uses their Form 3L and Durable Resin. The flexible, yet impact-resistant and low-friction properties of the material make it possible to install interference fits, which are required for the two-axis control system.
Gears for the T-Crow made of Durable Resin on the Form 3L.
After the individual parts have all been printed and post-processed in-house, they are assembled using the threaded inserts and are completely ready for dispatch within three days.
All 3D printed components of the T-Crow before assembly.
'With the printers we currently have, we could produce 1,500 complete T-Crows ready for dispatch in one year," says Mähler.
See the Form 3LLearn More About the Fuse 1
Compact Steadicam/Tripod
Hi all! In this post I will tell you about my product. This steadicam, perhaps, is not quite an ordinary design. It is impossible to call it some outstanding invention, all this has already been invented before me. But some of its functions, namely a quick conversion into a small tripod and a few interesting "goodies" that I have not yet seen from anyone, are still present.
This fixture looks like this:
These photos clearly show its use as a tripod. nine0003
And this is what the steadicam looks like when folded:
The counterweights of this steadicam are located on its two front legs, they are ordinary M14 washers (standard size and enlarged (body)) which are selected depending on the required weight. The washers are fixed on the leg with an M14 nut, which is also a counterweight.
The next photo shows the hinge on which all this "dangles":
The design resembles a ball joint. The ball itself was bought at an auto parts store, it seems it is intended for attaching the gas stop of the trunk lid from some domestic car. The recess for the ball is simply printed in the handle, and from the usual ABS, which does not prevent this hinge from spinning very easily and isolating the camera from an ever-trembling hand. nine0003
Another feature of this steadicam:
There is a "trigger" in the handle, which is a brake. When you press it, the ball inside the ball joint is clamped, which helps to turn the camera more quickly, dampen its vibrations, and even tilt the camera up or down. In this case, the camera does not begin to shake along with the hand.
The balancing mechanism looks like this (bottom view):
Turning the plastic printed screw (by the handle at the bottom of the photo) you can move the platform where the camera is mounted along the longitudinal axis. If you loosen the screw located in the center of the photo, you can move the platform in the transverse axis, sliding it along the shaft. nine0003
To the right of the handle is an eccentric clamp, by loosening which you can turn the shaft along which the head moves in the transverse axis, which makes it possible to tilt the camera, for example, when using the device as a tripod. Or wiring overlooking the ceiling or the ground.
The legs are telescopic and fixed with eccentrics like on a real tripod
To unfold the product, to use it as a steadicam, just extend the front legs with weights by opening the eccentric clamps, spread them apart, fix them with nuts and turn the head to the desired position. nine0003
To convert it into a tripod, just slide the third leg out of the handle.
It can be seen that when designing, I used SolidWorks. And while I was creating models for this little thing, I discovered a way to model with surfaces. It is always very interesting to learn something new about the ways of designing in CAD, and expand your abilities in this area. In general, the ability to create your own 3D models is important not only for a person who has a 3D printer. And how some people who have a 3D printer, but do not know how to create 3D models, have not yet got bored with this machine, I can’t imagine. After all, the ability in 3D graphics, and the presence of a printer at hand, gives great opportunities in creativity. Urgently learn 3D modeling if you don't already know how! I don't think this is bad advice. I myself have known him since school, then it was 3Ds max. A little later, when I was living with one aircraft modeling, I began to master Solidworks. A "stereo builder" appeared at me recently. nine0003
Okay, I got carried away with tediousness. I'll tell you how all this was printed and collected.
Printing and assembly
Everything was printed from cheap black ABS with 100% infill, some parts were printed from new PETG for myself (also cheap), namely the tips of the legs. The legs themselves are made up of aluminum shafts, from laser printer cartridges. These shafts are fairly light and strong aluminum tubes with diameters of 14, 12, 10 mm (it seems the most common sizes in A4 printers). nine0003
Tube diameter 10 mm Fits easily and with little play inside the tube diameter 12 mm to make the legs telescopic.
These tubes are called magnetic shafts, usually there is a long magnet inside, which can also be used, for example, to make a magnetic holder for small metal tools. There is also a photodrum - the same strong thin-walled tube, but with a diameter of about 24 mm. There are many applications for these tubes, and in every workshop for repairing and refilling cartridges there is a whole box of them, which in most cases is simply taken out to the trash. nine0003
By the way, before I cut all these tubes to the size I needed, I had to use them as drills.
Using a needle file, I drew teeth on one end of the tube, as on a core drill. The other end, where there is a narrow insert protruding from the tube, was clamped into a drill.
And with this “collective farm” drill, I went through all the holes where a shaft of a similar diameter is placed. By the way, this method can be used for deep drilling of soft materials such as foam. For example, laying cable channels in the wings of an aircraft model. nine0003
Yes, I know, it was possible to print the parts so as not to bore the holes, but at that time my printer printed quite terribly, and all because of homemade nylon bearings and oil-soaked PLA bearings. Therefore, the desire to pick up the gaps, something was not at all. Anyway, I was going to do post-processing and it seemed to me the best solution was to file everything to the right size. Now, of course, I won't do that. The printer has been completely redone, ordinary, but slightly modified bearings have been installed, all backlashes have been removed. And the axles move easily and, most importantly, quieter than with nylon, a paradox! nine0003
The screw that moves the head forward/backward was printed from two halves, which were then glued together.
Naturally, he did not enter his carving later. After a little thought, I found a solution how to grind one to the other. My cheap Chinese drill came with some strange abrasive blocks.
I still don't know why they are needed, can someone tell me? But I found my use for them, crumbling a little abrasive from them, using a bar with sandpaper, right into the thread, which needed to be “lapped”
Creepy photo. Not only is a terrible “collective farm” going on, but also a lot of dirt gets into the frame. I wanted to do this thing as quickly as possible in order to move on to other projects, which are in bulk in my head, so in the process of work there was no time to take care of the beauty of the photos.
"Nut" was also printed from two halves and this facilitated the lapping process. The screw, as it became clear, was clamped into a drill. (what would I do without it?) The halves of the nut were simply clamped with one left hand on the screw, and the screw was turned several times along the thread in both directions. The sand rubbed from these miracle bars quickly made the details compatible. nine0003
The screw that goes into the camera has been pulled out of a small pocket-size camera stand.
The large wheel that protrudes from the sides of the head to allow the screw to be driven in was printed and simply glued to the wheel of the tripod screw using an adhesive made from acetone and abs.
The most difficult thing for me was to figure out how to make leg restraints so that when unfolding they do not fall out on the floor. What I came up with, I myself do not really like and seems too complicated, but another has not yet come to mind. nine0003
This is what these restraints look like - wire hooks that hang inside the legs. The plastic sleeve is glued into the lower leg extender:
And the hook clings to the rod inserted into the plastic hinge that secures the upper leg to the steadicam body.
Or as in the case of the 3rd leg: a rod inserted into the handle.
These rods, like the axles of the eccentric clamps, are made from old bicycle spokes
There are recesses for the eccentric in the upper parts of the legs:
The whole clamp consists of 3 parts: body, eccentric and shaft.
Cam body is simply glued to the leg with epoxy, like all other places where metal and plastic are fixed.
The hinge on which this whole structure wobbles, as I said, was purchased from an auto parts store.
The surface finish of the ball itself was appalling. As if it was sharpened by hand, on a loose lathe. Unfortunately I didn't take a "before" photo. But bringing the ball to an almost mirror state did not take much time. nine0003
A drill, sandpaper (grain size 120, 400, 800, 2000), a drill with a felt nozzle, and GOI paste came to the rescue again.
Ah drill! What a useful invention. This is a lathe, and drilling, and grinding, and lapping machine in one case.
The final polishing of the surface was carried out simultaneously with a drill and a drill with a felt nozzle lubricated with GOI paste.
I think the design of the hinge will be clear from this render.
The trigger simply presses on the ball and locks it in its seat. nine0003
A few words about fasteners.
Most fasteners are bolts and nuts inserted into printed slots. But there are also a handful of small screws, most of which are in the head
Post-processing.
There is nothing supernatural in post-processing. First, sandpaper 80, then 120, then 400 and finally 800. After that, the surface was pre-smoothed with a soft watercolor brush dipped in acetone. And the final touch is processing in an acetone bath without heating, but with a fan inside, for 15 minutes, which removes the white coating from the plastic remaining after brushing, and gives the final gloss. On solid fillings, after all manipulations with solvents, a pattern of this very filling appears. Therefore, it would be better to use the method proposed by MexaLbl4 in this article. I myself tried this method after making the steadicam, successfully replacing the aluminum powder with easily accessible baby powder, and was very pleased with the result. Thanks to MexaLbl4 for the idea. nine0003
Conclusion
On this I think it's time to finish the story and start summing up. In principle, the product turned out to be working, so far I managed to try it only with a mobile phone as a camera. Stabilization is the video turns out to be smooth, but sways a little, until I realized this problem is from incorrect settings or from an unsuccessful design. An attempt to put on a weighty "reflex camera" revealed another drawback. The lateral balance adjustment clamp rotates under the weight of the camera, if you pull it up and down, no matter how you tighten it. nine0003
It would be nice to have one solid key on this shaft to keep the clamp from turning, but I haven't figured out how to do it reliably and easily yet.
There are no complaints about the tripod, it stands stably even on slippery surfaces.
And finally, a video of the product in operation.
Best Tripod・Cults 3D printer models
Telescopic reflector for photography Tripod adapter
Free
Amazon Basics Tripod Plate
Free
Mobile tripod holder
Free
MagSafe Mount
2. 77 €
Tripod MX 1000 quick release plate
Free
nine0128 Universal binocular holder on tripodFree
Telescopic pvc studio light stand
Free
Oven temple tripod 3D model
4.99 €
Oven temple tripod 3D model
4.99 €
GOPRO HANDLE
Free
3d printed mobile phone holder || HIBRID DESIGN (UPDATE stl)
Free
Webcam Mount Prusa MK3 Logitech C920S
Free
Beagle Camera Mount
Free
YATMo - Yet Another Tripod Mount
Free
Professional camera tripod
5 € -60% 2 €
Floor bracket for light stand
0,96 €
3D printed case for Raspberry Pi Zero IR camera
2,50 €
nine0128 Tripod (Folding) RemixFree
Tripod support
1. 25 €
Xiaomi Redmi 3 tripod adapter
Free
Raspberry Pi (model 3 A+) 3D printed IR camera case
3,50 €
1/4-20 Handle screw
Free
nine0128 Universal tripod with phone holder1 €
Xperia Z3 tripod mount
Free
Ikea Table Pi Cam Tripod Clamp
Free
Tarion TR-V1 base plate
Free
Tripod mount for smartphone. Smartphone tripod adapter. Cell phone holder adapter. Adaptador de telefono móvil para el tripode. nine0129
€3.89 -10% 3. 50 €
Tripod
Free
Ball stand with label
Free
Part of Hama tripod
Free
VirtualBoy Tripod Bracket
Free
Kinect 360 Scanner Tripod
Free
tripod for mini printing prism
Free
Mobile phone cage
€10.90
MagSafe Mount
2.25 €
M240D Pole and tripod adapter M2(M122)
€4.16
bipod bottle holder
12.50 €
Tripod to C-Stand Adapter
Free
Tripod
Free
Tripod platform - Hamma - Gamma series
Free
nine0128 Bottle holder Ø 100 mmFree
Snowball tripod extension 50-200 mm
1.