3D printed space marine shoulder pads
Free STL file Space Marine Shoulder Pads・3D print design to download・Cults
Imperial Fists Space Marine Icon Moulded 'Hard Transfer' (Updated)
€1.11
Black Templars Unit Icons Moulded Hard Transfers & Shoulder Pads
€2.86
Space Wolves Great Companies Icons Hard Transfers
€3.43
First Founding Space Marine Chapter Icons Moulded 'Hard Transfers'
€5.67
Salamanders Space Marine Icon Moulded 'Hard Transfer'
€1.09
Dark Angels, Ravenwing and Deathwing Space Marine Icon Moulded 'Hard Transfer' Pack
€2.86
Flesh Tearers Space Marine Icon Moulded 'Hard Transfer'
€2.23
Raven Guard Space Marine Icon Moulded 'Hard Transfer'
€1. 09
Best 3D printer files of the Game category
Toy Tugboat
Free
Cromulon's Head
€4.43
Marble Run Compatible Wide Format 8 Marble Finish
Free
Beholder - 28mm D&D miniature
Free
Tiny Tie - Eachine E011 based
Free
Nano Drone Wrist Mount (CX-10D)
Free
are you my boss ?
Free
Shape Shaker_Caterpillar
€3
Best sellers of the category Game
CRAMER Truggy RC 4x4 Full 3D Printed
€7.50
Octopus 2.
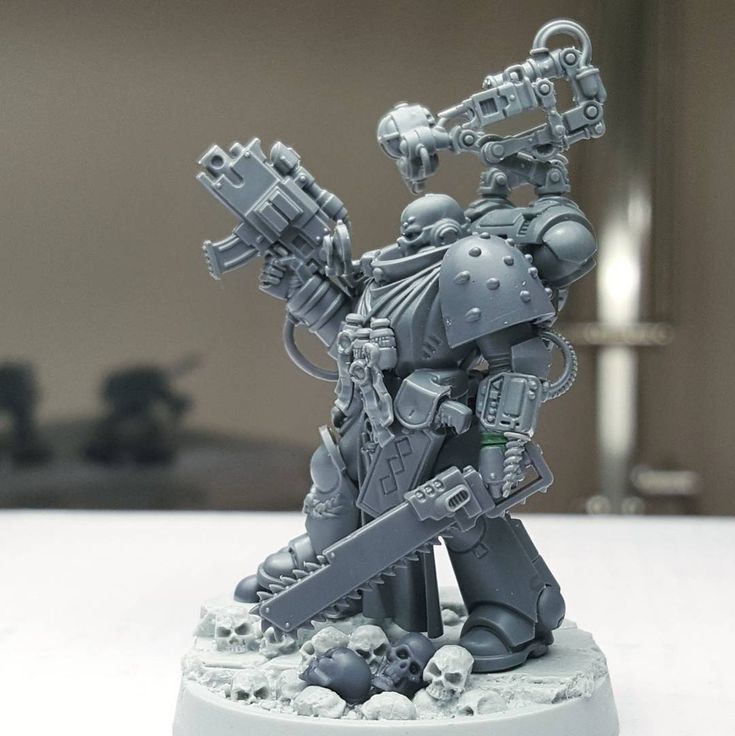
€4.09
SM Healer Conversion Kit
€6
Voidwalker Exosuits Truescale
€14.82
Lion Foo
€5.50
Nice Flexi Hedgehog
€1.05
SPACE DWARF SQUAD
€6.15
Emberfolk Fighters
€10.25
Space Dwarf All - terrain vehicle
€16.41
Snake and Rattlesnake
€4.09
Lazy Cat
€4.09
Articulated Tarantula
€4.09
Combat Director
€1.54
Wodfolk Explorer
€10. 25
Fotiann Wildmen
€10.25
Heavy Imperial Fire Support Weapons [Presupported]
€5
Would you like to support Cults?
You like Cults and you want to help us continue the adventure independently? Please note that we are a small team of 3 people, therefore it is very simple to support us to maintain the activity and create future developments. Here are 4 solutions accessible to all:
ADVERTISING: Disable your AdBlock banner blocker and click on our banner ads.
AFFILIATION: Make your purchases online by clicking on our affiliate links here Amazon.
DONATE: If you want, you can make a donation via PayPal.
WORD OF MOUTH: Invite your friends to come, discover the platform and the magnificent 3D files shared by the community!
Free STL file Space Marine Shoulder Pads
Blank (Chaos) Space Marine Shoulder Pad Collection
Free
(Chaos) Space Marine Shoulder Pads - World Eaters
Free
Space Marine Shoulder Pads - Black Templars
Free
(Chaos) Space Marine Shoulder Pads - Iron Warriors
Free
(Chaos) Space Marine Shoulder Pads - Thousand Sons
Free
(Chaos) Space Marine Shoulder Pad - Night Lords
Free
Space Marine Shoulder Pads - Iron Hands v1
Free
Space Marine Shoulder Pads - Iron Hands v2
Free
Best 3D printer files of the Game category
ZeroBot Pro - Raspberry FPV Robot
Free
Armour - Gambeson
Free
Holiday Special! THE GRINCH!
Free
Christmas 2021 - KRUMPUS
Free
Palm Tree
Free
AMONG US (DEVIL)
€1. 03
Maker Faire Robot
Free
Best sellers of the category Game
SM Healer Conversion Kit
€6
Space Dwarf All - terrain vehicle
€16.41
Wodfolk Explorer
€10.25
Dirt Bike
€1.40
Lazy Cat
€4.09
Nice Flexi Hedgehog
€1.05
Nice Flexi Dragon
€1.77
Exolothreftes Truescale
€5
Articulated Dragon
€4.09
RC 1/10 Dodge Challenger
€7.50
Voidwalker Exosuits Truescale
€14. 82
Emberfolk Fighters
€10.25
Dancing skeleton
€3.59
Off-Road Car
€2
Enourmous Imperial Heavy Tank
€10
Alteyr Champion
€5.13
Would you like to support Cults?
You like Cults and you want to help us continue the adventure independently? Please note that we are a small team of 3 people, therefore it is very simple to support us to maintain the activity and create future developments. Here are 4 solutions accessible to all:
ADVERTISING: Disable your AdBlock banner blocker and click on our banner ads.
AFFILIATION: Make your purchases online by clicking on our affiliate links here Amazon.
DONATE: If you want, you can make a donation via PayPal.
WORD OF MOUTH: Invite your friends to come, discover the platform and the magnificent 3D files shared by the community!
How Relativity Space prints rockets on a 3D printer
Relativity Space co-founder, CEO Tim Ellis / Relativity Space / AFP
Relativity Space is printing a metal space rocket on a 3D printer that it invented specifically for this purpose. Almost all: 95% is printed, and the remaining 5% falls on electronics, seals and some other elements. 3D printing has many advantages. She's cheaper. She's faster. It is made on the spot, no need to wait until the parts are brought from another factory. It is stronger: fewer places for fastening parts. “The Shuttle had 2.5 million parts,” says Relativity Space co-founder Tim Ellis. “According to our estimates, SpaceX and Blue Origin have reduced this number to 100,000 per rocket. We have a thousand - less than in your car.
Many space companies use 3D printing, but only for individual components. Skeptics insist that no one knows how the printed rocket will behave during takeoff and in space. So far, the startup's first rocket, Terran 1, has successfully passed all ground tests. The first copy for a real flight is collected slowly and carefully checked. Now it is ready for 85%. A test flight is scheduled for the end of this year. But investors believe in the idea. Last November, Relativity Space completed a series funding round and raised $500 million. After that, according to research company Pitchbook, with a business valuation of $2.3 billion, Relativity Space became the second most valuable venture capital-funded space company in the world. In 1st place, of course, SpaceX (however, Pitchbook does not include Blue Origin in the rating, which is fully funded by Jeff Bezos).
Relativity Space has since raised another round, raising $650 million, based on a company-wide valuation of $4.2 billion. reusable. After all, competitors do not sleep. Relativity Space is just one of more than a dozen rocket companies created in the last 10 years.
Launch from Mojave
Ellis was born in 1990 in Texas. He is the eldest of three children of an architect father and a dentist mother. As a child, Ellis was fond of Lego and persuaded his parents to buy about 200 sets. He immediately threw away the instructions from them and collected the spaceships he invented himself. Until now, the thumb of his right hand, when at rest, arched back more than his left - Ellis assured the Los Angeles Times that this was the result of long hours when he assembled and disassembled the parts of the designer.
As Ellis got older, he began making amateur films with his friends, mostly action movies, where the characters were often confronted by zombies. He entered the University of Southern California to become a screenwriter. But already in his first year, he became interested in the profession of an aerospace engineer and joined the Rocket Propulsion Lab at the university, which was engaged in the development of rockets.
The University of Southern California is known for its space program. Its alumni include Apollo 11 commander Neil Armstrong, astronaut and former head of NASA Charles Bolden, and Dana Rohrabaker, chairman of the House Space and Aeronautics Subcommittee. There are several laboratories where students create real rockets and satellites. “I was amazed,” Ellis recalled in an interview with the university website about the first time he went to test the rocket engine he designed and built with his comrades in the Mojave Desert. – I always advise students: take part in practical classes. So you will understand why you need to study this or that differential equation, scheme or line of code.
They wanted to be the first student group to launch a rocket into space. But, having carried out dozens of successful launches, they did not even achieve a suborbital flight - this was done by their successors in 2019, having developed more powerful engines.
Why leave Bezos and Musk
At Rocket Propulsion Lab, Ellis met and became friends with classmate Jordan Noone. Then their paths diverged for a while. Noon went to SpaceX, where he worked, among other things, on the Dragon 2 spacecraft. His emergency rescue system uses a 3D printed SuperDraco engine.
Ellis interned for three summers at Bezos' Blue Origin, and after graduation he was accepted full-time. He convinced Bezos to create a metal 3D printing division (by then many competitors, including Boeing, were doing it). He also created it from scratch. The traditional way of producing parts is turning on a lathe, stamping or casting with a mold. In 3D printing, robotic arms deposit layer upon layer of molten metal. A printed rocket has fewer parts, and therefore, places to connect them using welding, rivets, etc., and therefore fewer vulnerabilities. Skeptics object that if defects are found, the entire part has to be discarded and its manufacture must be started anew. But Ellis says that Relativity Space has developed a way to restart the printing process from the right place. “3D printed rockets are the future of rocketry and space exploration,” he told Inc. magazine.
Ellis and Noon often called each other and talked about rockets, although they worked for different space companies. They put together a rough cost structure to understand why rockets are so expensive. “80 to 90% goes to wages,” Noon told Bloomberg. 3D printing can dramatically reduce these costs.
Ellis once mentioned that he was going to start a startup to 3D print entire rockets. He later admitted to Inc. that he tried to get Bezos to print more parts for the rocket, but his suggestions were never fully implemented. Then he decided to take up rocket science himself. Noon liked the idea. Both left in December 2015 to create startup Relativity Space.
“I never saw him give up, give up, or fail to solve a problem, even a really difficult one,” Ellis told the Los Angeles Times of Noon. “I knew our startup was going to have a lot of problems, and he was the right person to make it all work.” And Noon noted: “I am strong in technical and practical aspects, and Ellis is strong in creative thinking and non-standard solutions. ”
For 1 kg of satellite
Relativity Space received its first money from venture investor Mark Cuban. Ellis and Noon made about 20 attempts to guess Cuban's email address, as Cuban preferred texting to other forms of communication. Some of the letters were returned with a note that such an address does not exist, some got to other people. But one of the addresses turned out to be correct, and Cuban read the letter with the headline "Space Is Sexy: 3D Printing of an Entire Rocket." Ellis and Noon asked for $100,000. Cuban, after five minutes of texting them, agreed to invest $500,000 (although they had to wait two months to check if they were fraudsters). “They are smart, resourceful, driven and always learning,” Cuban wrote in an email to The Times. “These are exactly the traits I look for in innovators.”
First, the startup needed to create a huge 3D printer - there were no models on the market suitable for their purposes. A lot of effort was put into this. But now the latest generation printer is able to print a part up to 32 feet (almost 10 m) high, while the height of the Terran 1 rocket is 115 feet (35 m). Ellis and Noon say that even if the rocket venture fails, they can always cash in on the sale of industrial 3D printers.
Terran 1 /Relativity Space
Created with Cuban's money, the first printer could print parts half the size of the last generation. But the working rocket engine printed on it made an impression on investors. First, they invested almost $10 million in the startup, then another $35 million, and in October 2019d. - another $ 140 million. Ellis and Noon planned to stop there. They did not want to dilute their share, and the funds raised should have been enough for the time before the first commercial launch, if they worked without haste. But in November 2020, another $500 million round of funding was raised. As Ellis explained to CNBC, “the development and scaling of the project needs to be accelerated. ” That summer, the startup moved to a new 11,000-square-meter headquarters in Long Beach, California. m, where there will be a site for the production of rockets (the most important thing is that their new printer climbed there in height). Over the past year and a half, the company has more than doubled the number of employees. She now has 400+ people and plans to hire 200 more this year.
Ellis told Inc. that they already have $1 billion in launch contracts from government and commercial entities. Terran 1 can carry up to 1250 kg of payload. This is smaller than SpaceX's Falcon 9, but larger than Rocket Lab's Electron. Relativity Space is targeting a mid-sized satellite niche, much like a car, Ellis said. Its competitors are the Russian Soyuz-2-1V and the European Vega. Or the same Electron, if Terran 1 displays several small satellites at once.
The launch cost of Terran 1 is $12 million, i.e. slightly less than $10,000 per 1 kg. Last year, Roscosmos CEO Dmitry Rogozin announced a more than 30% reduction in the price of launch services for a number of satellites to the level of SpaceX: to $15,000–17,000 per 1 kg instead of $20,000–30,000.
Target Mars
The competitive advantage of Relativity Space is not only in cost, but also in the fact that it can print a rocket to customer requirements, changing both the diameter of the rocket and the shape of the fairing for the satellite - of course, within the limits allowed by aerodynamics, Forbes explained. And she can do it quickly. Once the technology has been proven in practice, Relativity Space is going to print the rocket in 30 days and take another 30 days for pre-launch tests, Ellis told Scientific American. According to him, even SpaceX takes 12 to 18 months to build a conventional rocket. But Musk claims that his reusable rocket is ready for a new flight 51 days after the previous launch.
So in June, Relativity Space raised another $650 million from investors to accelerate the development of its own reusable Terran R rocket (of course, also almost completely printed on a printer). Its first launch is scheduled for 2024. It will be larger than the first one - 216 feet (66 m) high and designed for 20 tons of payload.
For Ellis and Noon, the main thing is that this project is another step towards interplanetary flights. Musk is looking for a way to get colonists to Mars, and Ellis and Noon are hoping to help them settle on the Red Planet. "If you believe - and I believe - that Elon [Musk] and NASA will send people to Mars, then <...> they will need a whole bunch of things," Ellis told CNBC. “Our printers are reducing the amount of infrastructure that would need to be transported from Earth to Mars in order to establish a colony there,” explained Noon Inc. – Traditionally, you need to send tons of equipment for a factory that will be able to produce factories that, in turn, will produce cars, houses, warehouses ... In our vision of the future, you simply send a 3D printer to Mars that prints everything using Martian raw materials this is". In a speech to the students of his alma mater, Ellis added: “We are going to 3D print the first rocket made in Mars <...> I don’t see a future in 50 years in which rockets will not be 3D printed. It just doesn't make sense otherwise, because printing is much easier and cheaper."
3D printing in astronautics - Zelenyikot
Now 3D printing has lost its aura of novelty and innovation, having become one of the technological operations of modern industry. Astronautics is a rather conservative industry, but there is also a search for the use of 3D printers. Plastic printing has already gone into space as an experiment, and metal powder sintering is used in rocket science.
At large enterprises in the space industry, 3D plastic printing has found application in prototyping and mold making. Selective laser sintering of metal powder has not yet earned the trust of rocket scientists, and still does not compete with casting, stamping and milling. Metal 3D printing technology is still perceived as an experiment, often carried out at public expense. For example, in 2015, a combustion chamber for a rocket engine was printed with copper using NASA funds.
Further experiments were carried out with different alloys and manufacturing techniques. One of the engines with a 3D printed combustion chamber was tested at the stand, but the engines for rockets produced under a government contract were left unchanged.
Private space companies are more open to innovation and bolder in introducing advanced technologies into mass production. RocketLab, a New Zealand company, has mastered 3D printing technology in the manufacture of elements of the Rutherford rocket engine. One of the key elements of a rocket engine is printed - a combustion chamber and a nozzle with a cooling jacket, where rocket fuel must circulate during engine operation. Rutherford was tested first on the bench, then during the space launch. The first rocket launch failed due to a failure in the communications system, and the second, in January 2018, was successful.
True Rutherford from RocketLab is quite light, has a thrust of about 2. 5 tons and a weight of about 25 kg. Nine of these engines are required in the first stage of the Electron rocket to launch a payload of just 200 kg into low Earth orbit.
Several 3D printed metal elements are used in the much more powerful Merlin engines on SpaceX's heavy Falcon 9 rocket. However, the key elements of this engine are made using other technologies; milling, injection molding, hot forming, etc.
American startup Relativity Space has gone the farthest. Its founders propose to produce a fully 3D printed rocket. Although we are talking about the mass use of parts created using selective laser sintering technology using a specially designed 3D printer based on Kuka robots.
According to the authors of the project, they managed to reduce the total number of rocket parts from 100,000 to 1,000. A small parabolic antenna, a solar array deployment mechanism, elements of an imaging system, a small CubeSat satellite body. Three-dimensional printing reduces the mass of elements, reduces the total number of parts, opens up new possibilities in the design of parts based on topological optimization, allows you to replace wire loops with conductive threads stretched directly through the walls of the structure.
Although the products were never launched into space, relying on previously mastered technologies. Although, it is possible that the results obtained will find application in future satellite platforms.
With regard to 3D printing, the conservatism of space technology manufacturers affects, because it is not enough to develop a new structural element, it is necessary to conduct its multiple tests on Earth, then launch it into space and see there the direct benefits that the novelty will provide compared to analogues of previous years. Therefore, it is easier for private beginners to use new technologies, because their development and so require a full test.
A separate area of 3D printing that has not yet got out of the experimental stage is printing in space. This direction is considered as a promising opportunity to realize the dreams of the theoreticians of astronautics of the last century, and start production in space. At first, such production could cover the needs in space, and then on Earth, opening up the possibility of moving into space the most environmentally hazardous industries. However, 3D printers are still far from solving global problems.
An experiment on 3D printing with ABS plastic in microgravity was carried out onboard the ISS. The astronauts were able to successfully print a ratchet key from a file transmitted from Earth, confirming the fundamental possibility of creating new products in orbit.
The company that equipped the ISS with a 3D printer - Made In Space - hopes to develop technology and create printers capable of creating structural elements of spacecraft and orbital stations directly in a vacuum.
In 2013, Deep Space Industries, a private company, set out to develop a 3D printer that could print metal in zero gravity. The company aims to extract minerals from asteroids, so it is planned to use the main material of metal asteroids, iron-nickel alloy, as a raw material. However, today all references to this development have been removed from the DSI website.
Another company that has set its sights on asteroids, Planetary Resources, also sees a future in using space resources in orbital manufacturing. As an experiment, the company printed a small design in an earth laboratory using a powdered metal meteorite as a material. (Header photo).
The Russian company Anisoprint is developing a technology for 3D printing from composites and is considering printing composite elements of spacecraft in orbit as a possible application.
Another Russian startup 3D Bioprinting Solutions plans to conduct an experiment on the Russian segment of the ISS, with the biofabrication of body tissues. It is assumed that microgravity conditions will allow the formation of stable three-dimensional structures and full-fledged tissues and even organs, the creation of which on Earth is prevented by gravity. The equipment for the experiment has already been sent to the ISS.
On Earth, 3D printers can already handle not only small items, but entire houses. Similar experience is proposed to be applied in the creation of extraterrestrial settlements or scientific bases. In the USA, Russia and other countries, developments and experiments are being carried out in this direction.
The European firm Foster and Partners, commissioned by ESA, carried out design work on the design of a lunar base printed from regolith. As a confirmation of the proposed technology, the company ordered the printing of one block of volcanic basalt using a D-Shape construction printer.
Samara State Technological University is developing a lunar lander that could sinter building blocks from regolith. It is supposed to use sunlight as a source of energy, which is concentrated by deployed reflectors.
Unfortunately, most 3D printing projects in space remain on Earth for the time being. This is partly due to the imperfection of the technology, partly to the insignificant benefits that the new technology promises. Much depends on economies of scale here: while the entire industry is based on the use of earlier technologies, therefore, the novelty turns out to be more expensive and riskier than repeating the past. Although 3D printers are able to give a certain benefit, we should expect an increase in their popularity in the space industry.