3D print long objects
How to 3D Print Models Larger than Your 3D Printer’s Build Volume
Don’t own a large format 3D printer yet? When determining what’s possible with a compact desktop 3D printer, think beyond the build volume. Just as assemblies such as your smartphone or even a road bridge consist of many individual building blocks, splitting a model into smaller parts that can be combined after printing is a great solution for 3D printing large objects that don’t fit on a build platform.
Splitting a part can also be the best way to get a high-quality result, even if the whole part could fit into a single build. This is the case when multiple or opposing surfaces need to be free of support marks, a design has complex overhangs, or a model contains cavities that would trap the liquid resin inside.
3D printing multiple pieces also opens up new opportunities, such as creating multi-material assemblies or combining rigid and flexible 3D printed parts to simulate overmolding.
When selecting a bonding method, your primary consideration should be the strength of the bonded joints, which is dependent on the ultimate use case of the parts:
-
Chemical fastening: Use a bonding agent for art, scale models, and complex shapes that are not meant for functional use and to sustain impact.
-
Mechanical fastening: Add screw thread or pockets to functional engineering parts that require a robust mechanical connection or if you need to repeatedly attach and detach components.
This guide will focus on creating large multi-piece stereolithography (SLA) 3D printed models using chemical fastening. Read on for a step-by-step walk through the process, from splitting your model to post-processing for a professional finish.
Formlabs’ Form 3L is the first affordable and easy-to-use large format 3D printer optimized for the reliable production of industrial-quality parts. The Form 3L SLA 3D printer offers a massive 30 cm x 33.5 cm x 20 cm build volume at an unprecedented value.
See the Form 3L
There are two methods we recommend for splitting models: Add features to your design that will allow the prints to align themselves, or simply split the parts with straight cuts, requiring you to align them during the fastening process.
Regardless of which method you choose, if you have a large number of parts it’s also a good idea to add a unique identifier (letters, numbers) to each part to help you solve the puzzle during assembly.
Use the CAD tool of your preference to split your 3D model and add basic aligners like slots, pins, grooves, recesses, and lips or more complex aligners like dovetails and cuts that follow existing creases in the model.
Adding aligners to a design can help when it comes to assembling parts.
In a perfect world these aligners make it simple to align and assemble your parts, but can lead to issues when they turn out even slightly different from your 3D models and don’t line up perfectly. Consequently, only use aligners if your printer can print dimensionally accurate parts that are unlikely to warp.
Splitting your 3D model along straight lines is less design-intensive than adding aligners. Straight cuts are also more forgiving when prints turn out slightly warped or have generally a higher degree of dimensional variation.
Adding identifiers to each part helps you solve the puzzle during assembly.
On the downside, straight cuts can be time intensive when it comes to assembly, as you have to manually align each part and make sure they remain in the correct position until the adhesive fully bonds them.
By default, the stereolithography (SLA) 3D printing process creates fully dense parts. Depending on your design, this might not be a requirement when 3D printing large objects. In such cases, 3D printing the outer shell or hollowing out your design are great ways to save a considerable amount of material and time. When printing hollow models with an SLA 3D printer, be sure to add venting holes to avoid creating pressure volumes with air and resin.
Sample part
See and feel Formlabs quality firsthand. We’ll ship a free sample part to your office.
Request a Free Sample Part
Hollowing out your model can save substantial time and material, as the printer will only need to print the outer shell.
Find out more on how to save material and time by hollowing out your 3D models.
We recommend three methods for bonding parts, depending on their size and ultimate use case:
Epoxy (5-30 minute) | Cyanoacrylate (CA, Super Glue) | Resin | |
---|---|---|---|
Area to bond | Large | Small/Medium | Small |
Paintable | Yes | Yes | Yes |
Impact strength | Medium | Low | Low |
For the largest parts and the strongest adhesion, use 5-30 minute epoxy. It has the longest work time, which helps when adjusting the position of larger 3D printed parts, but also leads to an overall slower assembly process. Most 5-minute epoxies won't change shape after about five minutes and reach approximately 75 percent cure strength in less than an hour.
For the largest parts and the strongest adhesion we recommend epoxy.
The next option is cyanoacrylate (CA, or Super Glue), which creates a quick, reasonably strong bond making ideal for small- and medium-sized parts. Clean the part thoroughly before applying it to the surface, as CA does not bond dirty surfaces well. CA has moderate impact strength, but is not recommended for high-impact applications.
For smaller prints you can also simply use the liquid resin from your SLA 3D printer. Pour a small amount of resin into a tray from the bottle or cartridge, use a dropper or syringe to pick it up, and place it onto the surface to bond. Join the parts and wipe off any excess resin that might spill out around the edges. To solidify the resin and bond the parts, use a 5mw UV laser light pen (405nm wavelength) and direct it to the bonding area around the parts.
This method will create a chemical bond, just as if the part was printed on your SLA 3D printer, but is only applicable to small bonding surfaces as the low power light pen cannot penetrate the model deep enough to create a strong bond.
Note: When dealing with resins, make sure to wear protective equipment including appropriate eye protection and gloves.
Webinar
Formlabs 3D Model Manager Evan Fisher walks the viewers through CAD and PreForm tips for larger parts and introduces Form Wash L and Form Cure L for post-processing.
Watch the Webinar Now
Now that you’re finished assembling your model, the final step is post-processing. This step consists of geometric correction of the part to ensure it has an even surface true to your original 3D model and aesthetic finish to get a consistent painted surface.
Depending on the accuracy of your printer and the size of the printed parts, it’s almost inevitable to have slight voids or incorrections where the parts meet. Automotive putty (such as Bondo 907) sticks to the resin well and should be applied to the surface in thin layers to patch these inaccuracies. Alternatively, use resin to fill the seams and cure it using a UV pen. Sand lightly after each layer dries to help bring the part towards its final form.
Patching parts with automotive putty (red area on the image) will help you mend slight voids or incorrections in between parts.
Sanding will help you remove support marks and any remaining inaccuracies from your model. Start with carefully dry sanding the surface using ~150 grit sandpaper to remove large support marks and level the edges where parts meet. Once the part’s surface is even, wet sand it with ~320 grit sandpaper to remove all remaining layer lines. Move the sandpaper in a random motion to avoid creating a grain. In most cases these two steps will create a smooth enough finish, but you might continue increasing the sandpaper grit count by a factor of ~2 and wet sand the entire part until the surface reaches the desired smoothness.
Power sanding works best on large flat surfaces, but can easily destroy small features. For smaller parts we recommend manual sanding, for larger ones a combination of manual and power sanding.
For larger parts, a combination of power and manual sanding can save you considerable time. Power sanding works best on large flat surfaces, but can easily destroy small features, sharp corners, and the subtle contours characteristic of SLA printing. Power sanding also creates a lot of dust, so make sure to prepare the surrounding area.
Note: Power tools require your full attention and wearing protective equipment. It is very easy to leave the sander stationary and quickly wear down that area without realizing it.
Once you’re finished sanding your model, rinse it in soapy water to remove any dust or debris and dry it thoroughly before moving onto the last step.
Priming ensures paint adhesion to the surface and can alert you to where you may need to sand more or trim support marks you may have missed. Generic plastic primer in matte grey shows details exceptionally well—apply it to the surface in several thin coats for the best results. Continue sanding on critical areas, apply a light coat of primer again, and repeat this process until the full part has an even surface.
Note: When priming and painting, wear protective equipment including a respirator designed for paint fumes.
Generic grey primer shows details exceptionally well and will help you uncover spots where additional sanding is required.
Find out more about sanding and priming from our extended guide.
For a finish with multiple colors, you’ll need to mask your model. First, plan the order in which you will paint your model depending on the color, opacity, and size of the area that will have the specific color. Start with the smaller parts so you’ll need to cover less when painting the bulk of the area with the main color. Use painter’s tape for covering the edges and corners, and sheets of paper to cover larger sections faster. Tape guides (lasercut) can also be helpful to create clean lines, circles, and complex shapes.
When it comes to masking, figuring out the correct order is your first priority. In our case, the parts were first painted silver and the sections that would remain silver on the final part were then covered with painter’s tape to hide them from the next l
Just as with priming, apply several thin coats rather than one heavy coat for the best results. Most spray paints work best in warm, slightly humid, and not windy conditions, but always check the specific paint can or technical documentation for the manufacturer’s recommendations.
Consider the time the paint takes to dry: Let layers sit before applying the same color and allow the paint to dry fully before applying a new color.
The area we covered with painter’s tape remained the original silver color after its removal.
Learn the ins and out of painting 3D printed parts in our extensive guide
Wondering how it looks when all these pieces come together?
“Excuse me sir, but that R2-D2 is in prime condition, a real bargain.”
Formlabs Optical Systems Engineer Adrian Tanner 3D printed this R2-D2 replica consisting of 105 3D printed pieces on a Formlabs SLA printer. It even has working electronics inside, borrowed from the Form 2 — the galvo drivers to make the sounds, the cartridge dispenser for lights, and the Z axis driver for the dome motor.
White Paper
In this free report, we look at how in-house large-format 3D printing with the Form 3L stacks up against other methods of production, chiefly outsourcing and using FDM printers. We also compare costs between methods, and review when it would be best to bring the Form 3L in-house.
Download Now
The Form 3L large format 3D printer offers a 30 cm x 33.5 cm x 20 cm build volume for 3D printing massive industrial-quality parts.
Eliminate the turnaround time of outsourcing or the manual work of assembly for large scale 3D prints. Now you can 3D print large objects in one piece with the Form 3L, the first affordable large format 3D printer using SLA technology.
Curious to see how SLA parts perform? Explore our materials to learn more about SLA resins, and request a free sample part to experience SLA quality firsthand.
Request a Free Sample Part
How to 3D print large objects
BlogDecember 16, 2020 (Last updated)
3 min read
3D printing is something of the latest craze. No longer exclusively the domain of corporations, home printing machines are becoming increasingly more affordable and accessible. There are whole networks of people who share files and offer their services at a scale that is continually increasing.
1. Use a 3D Modelling Software
Courtesy: Luban3D
When it comes to 3D modeling software, we recommend Luban 3D. It is a generative design software created by a small expert team to facilitate small-scale home printers with large-scale printing ideas. There are many options available when it comes to breaking down a large project into something more manageable: printing off separate layers to stack as you go, printing off smaller chunks to assemble, printing off interlocking layers, radial layers and even interlocking panels that resemble a jigsaw puzzle. Luban3D will work with you to find the solution to your large-scale project that meets your needs and the specifications of your machine.
2. Buy a large a 3D printer like the Creality CR-10S Pro
Courtesy: Creality
Here we are looking at a large-scale printer available on the market for home buyers. The Creality CR-10S Pro comes from a line of reliable machines. It is available for just under $600 which, for a large-scale printer, isn’t bad. It is easy to assemble and the navigation touchscreen is intuitive, although changing the language may be necessary during the initial set-up. The calibration is not quick but it leaves a nice finish. The downside is that there is a build-up of filament dust due to how it is arranged, so regular checks to clean it and ventilation are recommended. Another problem encountered was overheating causing the fan to sag – smaller tests when using a new material are recommended to determine if this is going to be an issue. Here is where you can find the CREALITY CR-10S PRO on Amazon.
3. Hire a 3D printing service that offers large scale 3d printing
Outsourcing large-scale 3D printing is a way of benefiting from the expertise available in the industry while avoiding the high investment cost of buying your own 3D printer. We provide large-scale printing for a range of individuals whether they are looking for prototypes, final products, both or everything in between. Our printers have a build volume of 23.6” x 23.6” x 19.7”. We’ve worked on products including architectural models, art sculptures and event fabrication. This isn’t the limit of what we can work on however – bring us a file and we’ll see what we can do! When it comes to recommending services, we suggest going to Printaworld for all of your large-scale 3D printing needs. That’s us! We can complete your project within 1 -2 weeks or 1 – 2 months depending on what you want and how large the objects you are wanting printed. Let us know if there is a deadline! Here at Printaworld, we can save you time, money and energy.
When it comes to 3D printing large-scale, there are a variety of options available to suit every budget, space and need. If you have a smaller-scale machine but still want to make something larger at home, software that disassembles your project into smaller, more manageable pieces is the way to go. If you have the budget at your disposal, purchasing a large-scale machine is efficient and effective. If you want to save money, you can always outsource and hire a 3D printing service. Whatever the route you want to go, we can offer and suggest a solution.
Visit Our Social Media Pages
About the author
Editorial Team
10 rules for preparing a model for 3D printing / Habr
Download the model, print it, use it - what could be easier!? But, if we talk about FDM 3D printers, then not every model can be printed, and almost every model (not prepared for 3D printing) has to be prepared, and for this it is necessary to imagine how this 3D printing goes.
First, a couple of definitions:
Slicer is a program for converting a 3D model into a control code for a 3D printer. (There are plenty to choose from: Kisslacer, Slic3r, Skineforge, etc.). It is necessary, because the printer will not be able to immediately eat the 3D model (at least not the printer in question). nine0003 Slicing (slicing) is the process of translating a 3D model into a control code.
The model is cut (sliced) in layers. Each layer consists of a perimeter and/or fill. The model may have a different percentage of filling with a fill, and there may not be a fill (hollow model).
On each layer, movements occur along the XY axes with the application of a plastic melt. After printing one layer, it moves along the Z axis to the layer above, the next layer is printed, and so on. nine0009
1. Mesh
Intersecting faces and edges can lead to funny slicing artifacts. Therefore, if the model consists of several objects, then they must be reduced to one.
But it must be said that not all slicers are sensitive to the grid (for example, Slic3er).
And even if the grid is crooked, and it’s too lazy to fix it manually, then there is an excellent free cloud service cloud.nettfab.com that will help in most cases.
2. Flat base
Desirable, but not mandatory. A flat base will help the model stay on the printer table better. If the model peels off (this process is called delamination), then the geometry of the base of the model will be broken, and this can lead to a shift in the XY coordinates, which is even worse.
If the model does not have a flat base or the base area is small, then it is printed on a raft - a printed substrate. The raft damages the surface of the model it comes into contact with. Therefore, if possible, it is better to do without it. nine0009
3. Wall thickness
The walls must be equal to or thicker than the nozzle diameter. Otherwise, the printer simply will not be able to print them. The wall thickness depends on how many perimeters will be printed. So with 3 perimeters and a nozzle of 0.5mm, the wall thickness should be from 0.5, 1, 1.5, 2, 2.5, 3mm, and above it can be any. That is, the wall thickness should be a multiple of the nozzle diameter if it is less than N * d, where N is the number of perimeters, d is the nozzle diameter.
4. Minimum overhangs
Each overhanging element requires a supporting structure - support. The fewer overhanging elements, the less supports you need, the less material and printing time you need to spend on them, and the cheaper the print will be.
In addition, the support spoils the surface in contact with it.
It is allowed to print without wall supports, which have an inclination angle of not more than 70 degrees.
5. Precision
Accuracy along the XY axes depends on backlash, structural rigidity, belts, in general, on the mechanics of the printer. And it is about 0.3 mm for hobby printers. nine0003 The Z-axis accuracy is determined by the layer height ( 0.1-0.4 mm). Hence, the height of the model will be a multiple of the height of the layer.
It should also be taken into account that after cooling, the material shrinks, and at the same time the geometry of the object changes.
There is also a software side of the problem - not every slicer correctly processes internal dimensions, so it is better to increase the diameter of the holes by 0.1-0.2 mm.
6. Small parts
Small details are quite difficult to reproduce on an FDM printer. They cannot be reproduced at all if they are smaller than the nozzle diameter. In addition, when processing the surface, small details will become less noticeable or disappear altogether. nine0009
7. Bottlenecks
Bottlenecks are very difficult to handle. If possible, it is necessary to avoid such places that require processing, which cannot be approached with a sandpaper or a microdrill. Of course, you can treat the surface in a solvent bath, but then small elements will melt.
8.
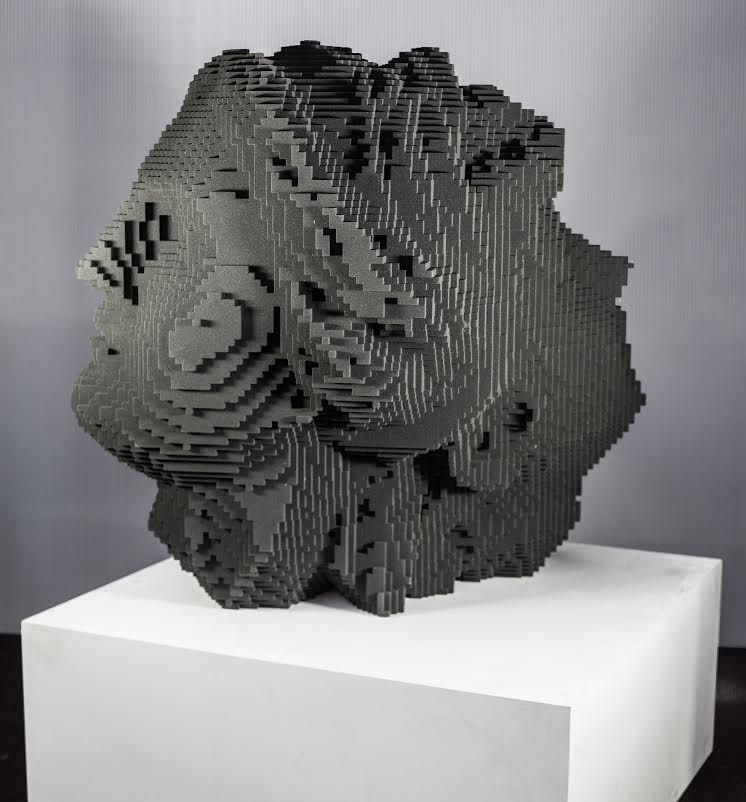
When modeling, it is necessary to take into account the maximum possible dimensions of the print. If the model is larger than these dimensions, then it must be cut in order to print in parts. And since these parts will stick together, it would be nice to immediately provide connections, for example, a dovetail. nine0009
9. Desktop location
How to place the model on the desktop depends on its strength.
The load should be distributed across the print layers, not lengthwise. Otherwise, the layers may disperse, because. adhesion between layers is not 100%.
To make it clear, let's look at two L-shaped models. The lines show the print layers.
The strength of the printed part depends on how the force is applied relative to the layers. In this case, a small force will be enough for the right "G" to break it. nine0009
10. File format
Slicers work with the STL file format. Therefore, you need to save the model for printing in this format. Almost any 3D editor can export to this format on its own or using plugins.
PS:
Now you know the intricacies of modeling for FDM 3D printing and, I hope, they will be useful to you. Happy 3D modeling!
Infill for 3D printing. What are and how to choose the right
6262 views Posted on: 13.12.2015
Author: 3D4U.COM.UA
By now you should have printed a lot of objects, because the best way to master something is to gain experience and do a lot of activities in the chosen area.
I'm sure you've seen several infill options in your 3D printing software, and you may have wondered how each infill will affect the final result of your product. There are a huge number of different filling options, but in this article we will focus on the 4 most common types. These are rectangular, triangular, wavy and hexagonal (honeycomb). nine0009
Rectangular
Rectangular infill is the most common type of infill, although it doesn't really provide any real benefit. In most slicer programs, it is set as the default value, due to which it has become the most popular. Many beginners use it because they have not yet explored all the possibilities of 3D printing and software.
Wavy
Wavy filling is practically useless. Its only use is to reduce the rigidity of a part and give it more flexibility. nine0009
Triangular
Triangular filling increases the strength of the outer walls and withstands high side loads. It is rational to use it for 3D printing of long thin structures or for strengthening walls. Examples are bridges or support beams for ceilings or roofs.
Hexagonal
Hexagonal infill is the best option for increasing the strength of the model, in addition, it significantly speeds up the 3D printing process due to the efficiency of its shape. nine0111 Hexagonal infill will save you energy, time, material and money, and will ensure high strength and rigidity of the final product. That is why bees form their combs in the form of hexagons. Nature uses this variant everywhere because it is efficient, mathematically perfect and elegant. Upon closer examination, it can be seen that this unique natural phenomenon is a combination of spheres to form a mosaic. Doubt? Take a straw and soapy water and create some bubbles. Obviously the soap bubble is spherical, but try to surround it on all sides with six small identical bubbles and see what happens when you do that. nine0009
In summary, what conclusion can we draw from the above? No matter how experienced or creative your designers or engineers are, nature will always take its toll, and we must pay attention to its lessons. Hexagonal infill will suit almost any of your creations, ensure the strength of your object, save material, as well as your time and money. In our opinion, hexagonal infill should be the new default in slicer software.
If you have not purchased a 3D printer yet or you do not want to understand the intricacies of 3D printing, you can order the production of parts on a 3D printer from 3D4U. We will select for you the appropriate filling option, its density, as well as the material and accuracy of 3D printing
Related articles
- Top 20 interesting toys for children on a 3D printer.
Category: 3D printing
02/15/2022
12655 views
What kind of toys can be created on a 3d printer? What are the advantages of 3d printing toys at home? In this article you will find...
Read more - 12 common 3D printing mistakes to avoid.
5406 views
As an industry, 3D printing is evolving every day, so it's important to know all aspects of this technology today. In this...
Read more - What can be printed on a 3D printer?
Category: 3D printing
03.02.2022
2755 views
When hearing about a 3D printer for the first time, most people are interested in the question of what can be printed on a 3D printer.
Learn more