3D print iem shell
▷ iem shell 3d models 【 STLFinder 】
14mm planar iem shell (not tested)
thingiverse
14mm planar iem shell (not tested)
Universal IEM Shell (Ear Phone Shell)
thingiverse
This is an Universal IEM shells I have created using my ear impression. it went through several edition. hope you folks like it. ...I have not tested printing it, will be printing it soon.
Universal IEM Shell (don't use)
thingiverse
DON'T DOWNLOAD, I'M WORKING ON A NEW DESIGN Here's my attempt at a universal IEM shell after trying to use OnShape. I was among a group of people who couldn't find a universal shell model in order to make their IEMs, so I decided to make my own. I...
IEM shells (two sizes)
thingiverse
Two different universal IEM shells modeled after my ear impressions. These are meant for 0.78mm 2-pin connectors, SLA printing is recommended. ...Just mirror the model to get the left side, you can add bores to the nozzle as needed in meshmixer.
HeadFi Free In Ear Monitor (IEM) Shell
thingiverse
This is a free for all shell design I made for a fellow maker in the Head-Fi Forums. ... It is a universal In Ear Monitor Shell taken inspiration with VE EVE in-ears.
IEM In Ear Monitor Earphone Balanced Armature Mold/Shell
thingiverse
Print this w/ DLP/SLA printer... Probably fits a 2-4 speaker configuration with 2-3 id2mm od 2.5mm tubes. ie. ...22955+29689/33aj007+29689/33aj007+30783, etc.
3d Printable IEM (Test run)
thingiverse
A proper, 3d printable IEM shell with 3 parts! The nozzle, chamber and faceplate. Use 10mm drivers, and short MMCX connectors for the chamber (Feel free to edit the model to your desired connector and shell shape type). However, it is highly...
UIEM Shell (Untested, 2 versions)
thingiverse
This is my latest attempt at a universal IEM shell. I printed the first version and it was entirely too big. ...The second version should hopefully be much better.
IEM storage box
thingiverse
Storage box for in-ear monitors. ... I also printed some padding in TPU to avoid scratching my IEMs but just some fabric will do.
Custom IEM Right Side
thingiverse
IEM Right is the original scan from 123d catch. ...Right Final with cuts is after modifying it to provide a good seal and room for the driver.
Custom IEM Earbuds
thingiverse
Download williamyeny's general iem template here: https://www. thingiverse.com/thing:1418780 2. Take a picture of your ear and head to Smoothie 3D : https://www.smoothie-3d.com
3. Create a shape for your IEM 4. Extract the model and edit it in any...
Microphone and IEM holder.
thingiverse
Designed this to hold a microphone, IEM, spare batteries and a card to signify the singer. I've included the Fusion 360 files so you can modify it to your needs. ...
IEM Desk Stand
thingiverse
Simple display stand for displaying IEMS on a desk. ...Headphones can orient multiple ways on the stand, it has space for the coiled cable and a 1/4" adapter
IEM Cable clip
thingiverse
If you're like me and like to use your IEMs with the cable tucked inside your shirt, you'll know how annoying it is when you get a bit sweaty and suddenly the cable starts tugging. This clip solves that issue while also alleviating the cable noise...
Simple Threaded IEM Container
prusaprinters
I felt the container that came with my IEMs was too small and cramped, so I made a larger container. This model also makes a great earplug case when scaled down in size.</p><p>I've printed several of these in eSun ePA and various brands...
Sennheiser ew g4 IEM - CASE
thingiverse
Sennheiser ew g4 IEM - CASE
Shuoer S12 IEM tuning "plug"
thingiverse
A simple plug and play tuning addon for LETSHUOER S12 planar IEM. ...
Printed with no supports, 0.12mm high quality PLA.
Currently I use 2mm thick sony IEM tuning foams for dampening, great, but not perfect. ...Feel free to improve it.
iem 4
thingiverse
e
shell
thingiverse
shell
shell
grabcad
shell
shell
thingiverse
shell
SHELL
grabcad
SHELL
shell
grabcad
shell
Shell
grabcad
Shell
shell
grabcad
shell
shell
grabcad
shell
Shell!!!
grabcad
shell
Shell
cults3d
shell
shell
grabcad
shell
shell
grabcad
shell
ED/4 Parts Ver.
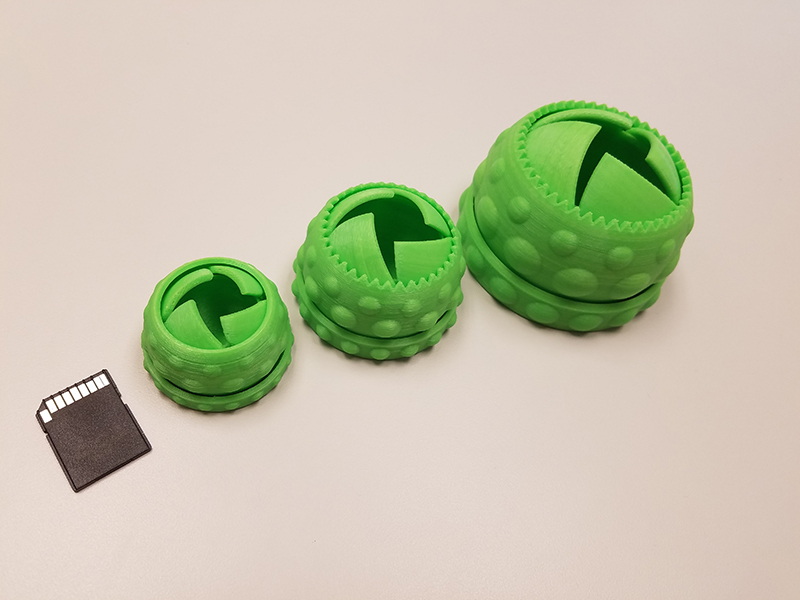
Click and drag to rotate
DIGITAL PREVIEW
Not a Photo
DIGITAL PREVIEW
Not a Photo
DIGITAL PREVIEW
Not a Photo
DIGITAL PREVIEW
Not a Photo
DIGITAL PREVIEW
Not a Photo
DIGITAL PREVIEW
Not a Photo
DIGITAL PREVIEW
Not a Photo
Product Description
This is a pair of universal in-ear monitor shell(left & right) for KnowlesED/TWFK/DTEC/GQ series BA drivers without engraving on the back covers and this model contains seperated 4 parts from the get-go.(You don't need to seperate each part after receciving, but it's a little bit more expensive than one part models for Black Hi-Def Acrylate. )
* Only for shells, other items(BA driver, connector , circuit, wire. etc.) are not included.
These shells are the result of a year-long effort.
These are designed specifically(different internal structure form the RAB BA driver version shells) for Knowles ED/TWFK/DTEC/GQ series BA balanced armature drivers(speakers), normal 2pin iem connentor(Plastic one's connector) and Knowles acoustic dampers(filters, 2.08⌀ BF series).
it's recommended for someone who has basic Knowledge about custom IEM DIY.
These shells have designed with 3D scanning of 95% pecentile standard ear mold and engineered to have ergonomic low profile shape for easy & comfortable fitting, which means the shape of the shells are easy to handle with two fingers.
And these shells doesn't require felxible tubes to connect to BA drivers. It's a direct connection between the shell and a BA driver by epoxy adhesive on top of thin bouble sided tape.
You need to polish the surfaces and drill the nozzles with 2. 1⌀ drill bit after receiving them(look at the explanatory image). Also you need to sand the edge of the back covers(plates) in order to fit in the shells.
The nozzles are fitted to comply 200 ear tips or Sony XBA series ear tips.
Because these shells have been originally desigened and tested for Black Hi-Def Acrylate , I highly recomend you to choose Black Hi-Def Acrylate for printing material.
*** Update: since Black Hi-Def Acrylate, possible printing materials are limited to Smooth Fine Detail Palstic and Smoothes Fine Detail Palstic.
Things you may need except the shells
- ED/TWFK/DTEC/GQ series BA drivers X2
- 2-pin female iem connector X2
- Knowles Acoustic damper X2
- 2.1⌀ drill bit X1
- Interdental toothbrush X1
- Pile & Polshing tools
- J-B weld epoxy adhesive
- Thin double sided tape (for temporay adhesion between shells and BA driver before filling the shells with epoxy)
- Thin litz wires
- Circuit & electic parts(capacitors or resistors , to tune the iems electrically)
Tags
earphones IEM In-ear monitor Inear headphonesDetails
FUD
By Crazy_Jo
View Shop
Send Message
Follow
More From This Shop
First non-commercial review and examples of 3D printing on PICASO Designer XL
Hello everyone! In touch Artyom Rodin aka Articoon.
Today we will be reviewing the Designer XL 3D printer from a well-known manufacturer - PICASO 3D.
Article written for #competitionCreality #competitionKreality
- Introduction
makes many people smile..."
However, I decided that this post will be useful for those who are thinking about purchasing a professional 3D printer with a large build area for their production/studio. The second motivation for writing this article was that although printers sell like hot cakes and you can only buy PICASO XL by standing in line, there are no reviews for this printer other than commercial ones!
So, it became necessary to restore the balance of power and write your own review.
2. Why him? A bit of background...
If anyone doesn't know me, I'm Artyom, I have my own 3D printing studio rodinlabs.ru and I've been printing a lot on a farm of 3D printers since 2015. No, I really type a lot! https://www.instagram. com/3dprinting_msk/
That's it, there will be no more ads, I promise. It just needed to get you up to speed.
The point is that for 6 years of communication with various 3D printers - from Wanhao i3 to Stratasys Fortus 450mc, many attempts were made to find FDM printers of similar quality and lower cost. I got my hands on: PICASO 3D, 3dq Prism Pro and Mini, Vortex, Wanhao, Anycubic, UnicBot, Ultimaker, MakerBot, Tevo, Flying Bear, Creality, ZAV, Hercules, Artillery, 3d systems Cube, CubeX Trio, various self-assembly- self-sticks and, finally, in 2020 I met and continue to work with Stratasys Fortus 450mc. nine0003
In addition to the latter, the longest-lived were:
- Anycubic Chiron - https://aliexpress.ru/item/32896071619.html - lived on average up to 6 months
- Artillery X1 - https://aliexpress.ru/item/ 32887558875.html - started to crumble earlier, after 3-4 months
- Self-assembled printer from "Foxprinters" with an area of 1000x500x1000 mm - https://foxprinters.
ru/3d-printer-bigfarm-1000 - done, prints, but requires constant attention .
But only PICASO printers impressed me with their eternity and reliability. One of my first printers - PICASO Designer is still working 24/7 since 2015. nine0043 An attempt to change the power for Chinese printers failed. The choice remained in favor of PICASO. And the other day I bought another printer - Designer XL.
Yes, printers have their own "logic". Yes, they are wayward and sometimes "enrage" their foil heaters. Yes, some functions work through one place and this also infuriates. Despite some shortcomings, there are still more positives - this is the print quality and the confidence that you can leave the printer for a week of printing and occasionally go up to it and change the plastic. nine0003
After 5 years, I can say with complete confidence:
90% of the quality of 3D prints depends on the hands of the operator and careful maintenance of the printer!
That is, you will be absolutely right that you can print on your IGIP or Pryusha like on Picasso. Ok, no problem :)
3. PICASO Designer XL
Printer Feature Overview A short list of features is as follows:
However, I wanted to focus on three interesting points in more detail:
1) The platform on 32 bit processor makes a very fast response to the control commands from the joystick-twist.
Picture from another printer - PICASO X PRO, the company's flagship. If I'm not mistaken, then the XL has the same board of its own design, maybe with a few changes. I didn't find any information about this anywhere.)
2) The long-awaited function of connecting printers to a single network has also appeared. That allows you to create a real farm from 3D printers and manage it remotely. For large studios and productions - an indispensable function. However, a network connection will also be useful for those who have at least one X-series printer at their disposal.
3) High performance extruder (up to 100 cm3/h) with heating temperature up to 410*C. Table - up to 150*C. Thanks to this, you can safely print materials such as Ultran 630 (aka Nylon 6 CF), PC, PEKK / PEEK (very rare, but it happens). Other materials of the type ABS CF / GF (charcoal / glass filled) - chews like seeds. True, it is worth mentioning here that a steel nozzle is purchased separately for filled materials.
4) BONUS - print area 360x360x610 mm. We recently compared similar printers and came to the conclusion that Designer XL is the leader in terms of construction among competitors (proofs in the comments). nine0003
4. What is outside and inside? Design and packaging of the printer PICASO Designer XL
In this section, we will look at the printer from the outside and take a little look inside.
The design of the printer is, firstly, concise, and secondly, very well thought out. The printer will ideally fit into any interior and production:
Complete set:
The printer comes with everything you need:
Plastic spool - typically 2. 5 kg ForMAX
Original tool kit:
Nozzle - 1 pc.
Nozzle replacement wrench - 1 pc.
USB stick - 1 pc.
Warranty card
Power cable - 1 pc.
USB cable for network connection
Adhesive for adhesion - 1 pc.
Plastic feed tube - 1 pc.
The body is made of dibond, reinforced with a steel frame and stiffeners. Door fixings, covers and inserts - printed from Formax (ABS CF). There is nothing to complain about here, the assembly is of high quality, all the doors and covers fit snugly, the magnets fall into the grooves. Moving on:
Backlight
The backlight on the printer is a special treat for 3D printing aesthetes. It makes great photos for a portfolio of works ;-)
I know you already want to take a look at the hardware and the quality of the printed products. But let's take a look at the details of the case a little more:
Plastic dump container before printing:
A magnet is hidden on the inside that fixes the container tightly:
Door mount and plastic spool printed in "draft" mode:
Spool mount allows you to put both wide kilogram spools and large 2. 5 kg spools:
5. Print head and table on PICASO Designer XL
The PICASO Designer XL printhead is reinforced with a frame, moving along XY - rails (used to be BOSCH, now not visible), bearings - Japan. Plastic feed system - Direct with all-metal thermal barrier. A Flow Control system is installed in the head to control the presence and supply of plastic. If the plastic is clogged or runs out, the head goes to the side and gives a color indication to the operator.
There is no trace left of the printed parts. All functional units are securely fastened with milled parts. The printed parts remain only in the head itself: the plastic feed unit and some spacers are made of Ultran 630 to withstand the high temperatures during printing. nine0003
The XL has a thicker Teflon tube than the X or X PRO. This is most likely due to the fact that it has greater rigidity and does not interfere with printing. In general, the head even has a special mount for brittle plastics (CERAMO, Formax, Carbex, Titan GF, etc. ). Checked - works.
Nozzle blowing from both sides:
All to the table!
The table is made on a frame of profiles and the design looks like this:
Pay attention to this stray:
The working surface is glass with magnets, which is attached with two latches at the back:
and three magnets at the front:
and two magnets at the front:
The hook mentioned above allows you to lift the glass, which makes it easier to install and replace the glass.
By the way, about the glass itself. It has a thickness of as much as 8 mm:
What? And where are the screws for calibrating the level of the table?
The fact is that on XL and XL PRO table calibration is fully automatic. The printhead measures 5 positions and beyond, the difference in height is compensated by each of the four steppers located at the corners (of which there are also 4 :) ):
By the way, you can run print jobs both from a flash drive and over the network, as I mentioned above in paragraph 3.
The table calibration function can be enabled before each print. And then, when you start any task, the table will calibrate and only then start printing. This "procedure" takes up to 5 minutes. If you are in a hurry, calibrate the table once and print...
6. PICASO Designer XL
printer menu 3DTool wrote very well about the printer menu, in this paragraph I am quoting the text from the review in full. nine0003
Let's dwell on the available menus in more detail.
Picaso Designer XL has the ability to connect to a common pool of printers via a local network, the USB slot on the front panel allows you to use classic USB flash cards, instead of more expensive and less convenient SD cards. and in general, has not changed compared to previous models of the line. Only a few new features have been added, such as automatic table calibration with the output of the sensor measurement results on the screen. nine0189
The first thing we see when turning on Designer XL is the company's welcome logo, which is familiar to us. Next, there is a general menu with large icons, let's look at each of them in more detail.
1) Print . This menu, as you might guess, will allow you to run a job from a memory card, as well as manage the process during printing. Pause and stop. It is noteworthy that the new firmware version allows you to select the diameter of the currently installed nozzle. nine0189
2) Plastic. The menu has not changed much. Allows you to perform service functions such as loading and unloading plastic, a combination of these functions in one run, cleaning the print head and working with plastic profiles. For example, changing them or importing/exporting them.
3) Service. The service menu contains the main service functions. Nozzle replacement, table calibration, manual pressure adjustment, cleaning system calibration and other service functions. Such as software update and error list. New algorithms for drying plastic and manual control of the table, as well as diagnostics, are also located here. nine0189
4) Settings. Contains information about the printer - the number of hours worked and printed plastic, serial number and version of the firmware and BIOS of the device. Next are the main settings for turning on / off sensors and control systems, setting up and calibrating encoders and network parameters when connected via ethernet.
Allows you to turn on/off the preheat function before printing.6) Sleep mode. Turns off the machine's light without turning off printing. Useful for saving energy and printing in offices where bright backlighting interferes with work. nine0189
And a hidden Debug menu that provides access to the displayed sensor readings and current error codes.
7. Slicer PICASO Polygon X
A lot of information has also been written about the slicer, but its latest version has greatly improved usability (from English usability - “convenience and ease of use, degree of usability”).
For example, I will briefly insert here a video that speaks about the generation of supports for itself:
This video demonstrates how easy it is to remove supports on ABS plastic using standard Polygon X settings.
That is, PICASO 3D took care of the users and made the process of removing supports as simple as possible, through multiple tests and selection of extrusion widths on all elements (perimeters, shell, supports) relative to nozzle diameters. Respect!
( Yes, there are some small mistakes in printing, but the case is for post-processing, so it's nonsense ).
8. Overview of printed products on the 3D printer PICASO Designer XL. The final. 01
Cons:
- service
- Availability - all printers are sold out a month in advance.
To buy - pay and wait a month or two :)
- Price - obviously not for home use.
The PICASO 3D Designer XL 3D printer is perfect for large-scale printing with any available materials. Thanks to the friendly interface and software, working with the POLYGON X printer and slicer is simple and intuitive. If you plan to print constantly - take two at once, one will be for safety net. nine0003
If you liked the article, like it and write something in the comments :-)
P.S. All questions about the printer or the purchase or operation of XL can be asked personally, in any way convenient for you, or in the comments to this post.
***
...and follow me on social networks. I will be glad to any communication!
Sincerely, Artyom Rodin, RODINLABS Prototyping Lab.
More interesting projects - Instagram
Add to VK - VK
***
Complete guide to 3D printing [part 2]
3D printing is used in a variety of industries, both for rapid prototyping and short-term production.
A key application of 3D printing in various industries is the rapid prototyping of new parts during R&D. No other technology has the capability to instantly produce plastic or metal parts - even in non-factory conditions. nine0335
3D printers can be used in-house by companies, while some businesses prefer to order 3D printed prototypes through service bureaus.
Medical
3D printing can be used to make medical components such as titanium implants and surgical guides (SLM), 3D printed prostheses (SLS, FDM) and even 3D bioprinted human tissues. Components for medical equipment and technology - X-ray machines, MRI, etc. - can also be made by 3D printing. nine0003
SLA and SLS technologies are also widely used in the dental industry for model making, prostheses and restorations.
Aerospace
The aerospace industry has become a major consumer of 3D printing technology because it can produce very light parts with an excellent strength-to-weight ratio. Examples include things as simple as cab bulkheads (SLS) and down to revolutionary engine components (SLM) such as the 3D printed fuel injector tip designed and manufactured by GE. nine0003
Cars
Automotive companies regularly use 3D printers to make one-off parts and repairs, as well as rapid prototypes. Common 3D printed automotive parts include brackets, dashboard components, and antennas (FDM).
More extreme examples include vehicles with large 3D printed metal structural components, such as early models from automotive startup Divergent.
Jewelry and art
3D printing technologies such as SLA are widely used (as an indirect fabrication process) in the production and repair of jewelry, while almost all types of 3D printers can be used to create works of art and sculptures.
Engineering
Advances in additive manufacturing with high quality workmanship have expanded the scope of applications in construction and architecture. Concrete 3D printing, which is a bit like FDM but with very wide nozzle extruders, plays an important role in this industry, but more common 3D printing technologies such as SLM can be used for products such as bridge structures. nine0003
3D printing file formats:
3D printing parts can be designed with standard CAD software, but 3D printers can only read certain file formats. There are four main file formats for 3D printing.
STL: The most common file format for 3D printers, STL contains part geometry information in the form of tessellated triangles. It does not contain information such as color, material, or texture. The file size is proportional to the detail, which can be a problem. nine0003
OBJ: Less common than STL, the OBJ file format encodes the geometry of a 3D model and can include curves and free-form surfaces in addition to tessellation. It can also contain color, material, and texture information, making it useful for full color processes.
3MF: Invented by Microsoft, 3MF is an XML-based format with small file sizes and a good level of error prevention. It has not yet been widely adopted, but is supported by companies such as Stratasys, 3D Systems, Siemens, HP, and GE. nine0003
AMF: The successor to the STL format, AMF is much more compact and allows you to tessellate both curved and flat triangles, making it much easier to encode parts of various shapes. Since its inception, the format has been slowly adopted.
3D printing settings and specifications:
3D printing uses specific terminology that may not be clear to beginners. These terms refer to printer settings and/or specifications that can affect how 3D printed parts turn out. nine0003
Infill
When making 3D printed parts, it may be necessary to specify an infill percentage, which refers to the internal density of the part. A low infill percentage will result in a mostly hollow part with minimal material holding the mold together; a high infill percentage will result in a stronger, denser, and heavier part.
Layer Height
Layer height, sometimes referred to as z-resolution, is the distance between one 2D part layer and the next. A smaller layer height means finer resolution (and higher possible level of detail) along the z-axis, i.e. top down. A low layer height is an indication of a high quality printer, but users can set a higher layer height for faster, more economical printing. nine0003
Print speed
The printer's print speed, measured in millimeters per second, indicates the speed at which the machine can process the source material. Like the layer height, this value can either be a measure of the printer's maximum speed or be user-defined: slower print speeds usually result in more accurate prints.
Print temperature
When applied to processes such as FDM, print temperature usually refers to the temperature of the hot end, the part of the print head that heats the thermoplastic filament. Some FDM printers are also equipped with a heated print bed, the temperature of which is specified by the manufacturer. In both cases, the temperature is usually controlled by the user. nine0003
Resolution
In 3D printing, resolution almost always refers to the smallest possible movement along the X and Y axes (width and depth) of either the laser beam (SLA, SLM, etc.) or the printhead (FDM). This value is more difficult to measure than the height of the layer, and it is not always proportional to it.
Shells
Like wall thickness in injection molding, shell (or shell thickness) refers to the outer wall thickness of the 3D printed part. When 3D printing, users usually have to choose the number of shells: one shell = outer walls as thick as a 3D printer nozzle; 2 shells = twice the thickness, etc. nine0003
Color 3D printing:
Since 3D printing is primarily used as a prototyping tool, single color prints are sufficient for most applications. However, there are several options for color 3D printing, including high-end material inkjet printers, multi-extruder FDM printers, and post-processing options.
Inkjet Printing Technologies
Major 3D printing companies such as Stratasys, 3D Systems and Mimaki have developed 3D inkjet printers for printing materials and binders that can print 3D models in full color as well as 2D inkjet printers. However, these machines are expensive and the parts do not always have excellent mechanical properties. nine0003
Multiextrusion
Several FDM 3D printers are equipped with two (or more) printheads, allowing you to simultaneously print on two spools of filament - different colors or even different materials - within the same print job. It's simple and affordable, but usually limited to two colors.
Filament replacement
Single extruder FDM 3D printer can produce multi-color prints. To do this, you need to pause printing at certain points and replace the spool of thread with a thread of a different color. This is a very slow method of applying color and does not allow precise control over where each color goes. nine0003
Adding color after printing
Many 3D printed parts can be dyed, tinted or painted after printing. While this adds another step to the process, it often strikes the best balance between quality and economy.
Post-Processing 3D Printed Parts:
Many 3D printed parts require at least some level of post-processing after leaving the print bed. This may include important processes such as the removal of supports, or additional cosmetic processes such as painting. Some processes apply to all or most 3D printing technologies, and some are specific to a particular technology. nine0003
Removing the support
3D printing technologies such as FDM and SLA require the installation of support structures (vertical posts between the printed layer and the part itself) so that the printed object does not collapse during the manufacturing process.
These supports must be removed when the part is finished. Some printers, such as dual-extrusion FDM machines, can print dissolvable support structures, allowing the support structures to be easily detached from the part using liquid chemicals. Insoluble supports must be manually cut from the part, leaving a mark that may need to be sanded down. nine0003
Wash and remove powder
Some 3D printing technologies (such as SLA) leave sticky marks on parts, while others (SLM, SLS) may leave powder marks. In these cases, the parts must be washed - manually or with a special machine - or the powder removed with compressed air.
Heat treatment
Many key 3D printing technologies print parts from materials that are not yet in their final chemical state after leaving the printing mold. Such details are sometimes called "green". nine0003
Many 3D printed metal parts require heat treatment after printing to increase layer fusing and remove contaminants. And bonded inkjet 3D printers, for example, produce parts that need to be stripped and sintered after printing to remove resin bond layers from inside metal parts.
Some 3D printed resin parts require post-curing after printing to increase their hardness and make them usable. nine0003
Surface Treatment
3D printed parts can be subjected to a wide variety of surface treatments, from textural treatments such as sanding and smoothing, to visual treatments such as painting and toning. Some technologies, such as FDM, can create a rather rough surface that requires sanding, while others, such as SLA, produce a much smoother surface.
Combination of 3D printing with other technologies:
3D printing does not have to be used as a separate process. Rather than being seen as a competitor to CNC machining and injection molding, it can actually complement these and other manufacturing processes.
Combination examples include:
- 3D print the main body of the part and then CNC mill the thin parts to tighter tolerances;
- 3D printed master pattern for investment casting or vacuum casting; nine0011
- 3D print the part and then injection mold using injection molding.
There are hybrid manufacturing systems that combine 3D printing with other technologies. For example, Mazak's INTEGREX i-400 AM and DMG MORI's Lasertec DED can perform both 3D printing and CNC milling.
Will 3D printing replace other manufacturing processes?
Analysts have long speculated about whether 3D printing could replace other manufacturing processes, including:
- Processing;
- Moulding;
- Casting.
However, despite the desire of AM equipment manufacturers to position 3D printing as an end-to-end manufacturing technology, in practice, 3D printing is still limited to some specific manufacturing operations, especially low-volume production of specific materials.
In some areas, 3D printing has certainly overtaken other processes. For example, rapid prototyping with inexpensive plastics like ABS now dominates 3D printing, as ABS is cheaper to print than machined. 3D printing also seems to have established itself as the ideal tool for making objects such as patient-specific titanium medical implants: the speed and geometric flexibility of 3D printing is hard to beat in these specific situations. nine0003
In addition, 3D printing is an ideal tool for making objects such as patient-specific titanium medical implants.
Despite this, processes such as CNC machining currently remain the best for producing high quality parts and prototypes from engineering materials such as POM, PEI, PPS and PEEK, with surface finishes far superior to 3D printing. . In addition, processes such as injection molding are still infinitely faster for mass production of simple plastic parts. nine0003
In addition, although additive manufacturing is one of the most significant technological advances in manufacturing, which allows it to take a stronger position in manufacturing in general, more established processes such as CNC and injection molding are also being improved to produce higher quality parts. .
3D printing will continue to take an increasing share of manufacturing jobs, but it will not completely replace other technologies.
What did 3D printing look like 10 years ago? nine0013
A decade ago, the nascent 3D printing industry was gearing up for what it believed was going to be a 3D printing revolution: a 3D printer in every home, allowing families to print new items they might need, such as a spare part for a refrigerator, a new toy for kids, or even components to build a second 3D printer.
In 2012-2014, FDM 3D printer manufacturers such as MakerBot actively promoted their 3D printers in the consumer market, trying to convince ordinary people that a 3D printer can improve their home life and work. However, it was clear that these companies were trying to exploit the novelty factor of 3D printing and that their products had no practical application; a 2012 MakerBot press release seems to prove it: Make an entire chess set at the touch of a button. Friends, classmates, colleagues and family members will see what you are doing and say "Wow!". nine0003
Just a few years later, this so-called 3D printing revolution clearly failed, and many 3D printer manufacturers began to rethink their goals, moving from consumer to professional and industrial markets, where there were more concrete (and profitable) applications of additive technology.
In addition, those who were already working in the professional and industrial fields - companies such as 3D Systems and Stratasys - began to try to destroy the idea of 3D printing as a prototyping technology, positioning it as a viable mass production tool (which, obviously, , could be more profitable for the 3D printing industry, as manufacturers would have to fill entire factories with 3D printers, buy 3D printer management software, and hire 3D printing consultants). nine0003
What will 3D printing look like in 10 years?
3D printing companies have abandoned the prospect of putting a 3D printer in every home. However, in 10 years, they can expect some form of additive manufacturing to appear in more factories.
Although there is less talk about 3D printing today than in 2012, the technology continues to gain momentum in the professional and industrial world.
According to a recent report, market research firm 3DPBM Research expects the value of additive metal manufacturing to rise from $1.6 billion in 2020 to $30 billion by 2030, and this is largely due to the repositioning of AM as a manufacturing tool and the development of more high-performance engineering materials. (That said, 3D printing will remain a valuable prototyping tool in many industries, and prototyping applications will benefit just as much from technological advances.) nine0003
However, not only metal AM is being developed. Technologies such as HP's Multi Jet Fusion have opened up new possibilities for plastic printing, and innovators such as Carbon have developed new high-speed processes in the photopolymerization category. Niche areas such as 3D bioprinting and micro 3D printing are also regularly opening up new opportunities, and composite 3D printing (such as continuous carbon fiber 3D printing) is also on the rise: IDTechEX predicts that by 2030, the market size of composite 3D printing will be $1.7 billion
In short, 3D printing will gradually become a serious competitor to other manufacturing processes in many disciplines.
How to outsource 3D printing services?
Investments in 3D printing hardware and software are not suitable for all businesses, so many successful companies outsource their 3D printing needs to third parties, such as online 3D printing service bureaus (for one-time projects) or prototyping partners and production, such as 3ERP (for one-time projects or repeat orders). nine0003
When outsourcing 3D printing services, it is important to consider whether your business needs design and manufacturing services or just manufacturing services. (Keep in mind that a poorly executed 3D model may fail for 3D printing).