Wearable 3d prints
Wearable 3D printed fitness tracker never needs to be recharged
0Shares
Voting shortlists for the 2021 3D Printing Industry Awards are now open. Who do you think should receive top honors this year? Have your say now.
Researchers at the University of Arizona’s College of Engineering have used 3D printing to create a smart health monitoring device that’s able to operate continuously without ever having to be manually recharged.
Dubbed ‘bio-symbiotic’ by its creators, the tracker harvests electricity via a power casting unit, that wirelessly charges its integrated antenna. In turn, the device uses this power to capture the biosignals and energy generated by wearers as they work out, in a reciprocal process that allows it to function for unprecedented periods.
Using 3D printing, the team has also been able to customize their patch-like fitness monitor so that it stays attached to users during exercise, while its sensors monitor the wearers’ biosignals with such a high level of accuracy, that they can identify the deformation within each muscle and calculate an adopter’s workout intensity.
“There’s nothing like this out there,” said Philipp Gutruf, an author on the paper and Assistant Professor at the university. “We’ve introduced a completely new concept of tailoring a device directly to a person, and using wireless power casting to allow the device to operate 24/7, without ever needing to recharge.”
The engineers’ 3D printed device can be customized to monitor different muscles around the human body. Photo via the Science Advances journal.An ever-lasting fitness tracker?
Wearable electronics aren’t just useful workout tools for gym goers, but when worn constantly, they can gather sufficient data to identify early warning signs of deadly conditions such as cardiac arrhythmia. What’s more, AI advances are increasingly enabling vast quantities of this biodata to be processed at pace, allowing any potential trends and diagnoses to be found or made more quickly than ever before.
However, despite recent analytic progress, the Arizona team say that fitness hardware has found it difficult to keep up, and they accuse current devices of “lacking sensing functionality,” as well as failing to provide “uninterrupted data streams. ”
To get around these shortcomings, the researchers have developed a wearable that uses a wireless power transfer technique known as ‘far-field’ energy harnessing, to convert radio frequency (RF) signals into a source of power, in a way that enables it to capture data continuously with precision, that they say is “nearly imperceptible the wearer.”
The researchers’ ‘far-field’ sensor set up. Photo via the Science Advances journal.Designing a ‘bio-symbiotic device’
At the core of the team’s health tracker is an FDM 3D printed ‘mesh,’ which can be tailored to stick to and operate on different areas of a wearer’s body, without needing adhesives. To lend their device sensing functionality, the team has embedded it with tiny sensory electronics which rest upon flexible nodes, and are joined up via stretchable serpentine interconnects.
Theoretically, these operate by communicating with a power casting system via antenna, which fuels the device’s active-harvesting electronics, and fills the energy storage cells that activate its sensors. Any data collected during a workout can then be relayed to computers via the tracker’s integrated bluetooth low-energy (BLE) on-a-chip system, and analyzed for potential fitness-boosting trends.
Given that the device’s power casting system can be placed several meters away, it’s potentially ideal for home-use, something that can’t be said for many existing ‘far-field’ systems. What’s more, the team’s wearable can be personalized to collect data from specific limbs and joints such as the shoulder or bicep, enabling it to do so with a level of accuracy that’s well beyond most normal trackers.
“If you want to measure the way your bicep deforms during exercise, we can place a sensor in the devices that can accomplish that,” explains the paper’s lead author Tucker Stuart. “Because of the way we fabricate the device and attach it to the body, we’re able to use it to gather data a traditional, wrist-mounted wearable device wouldn’t be able to collect.”
The Arizona team’s FDM 3D printing process in-action.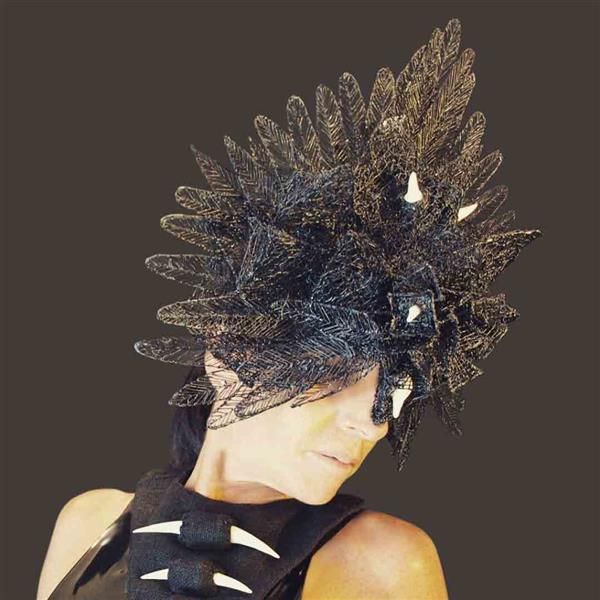
Fitness tracking in-action
To put their bio-symbiotic design into practise, the researchers initially 3D printed a test model from a Ninjatek elastomer, before slotting its electronics into place by hand. Using an Xbox Kinect camera, the team found that they were able to scale their prototype to fit snugly onto a test subject’s muscles, through creating an athlete-specific 3D model, and dividing it up into ‘physiological landmarks.’
For testing purposes, the engineers chose to base their device on the upper arm and lower leg areas of their model, before attaching it to the relevant volunteer, who subjected it to running, jumping and rowing, as well as push-up experiments.
During these tests, the Arizona team say their device demonstrated a “stable biointerface” while yielding “high-fidelity data streams,” and by deploying multiple units at the same time, they were able to monitor various areas simultaneously, including aspects such as temperature changes and muscle deformation, in a way that outstrips the performance of “current gold-standard devices. ”
Overall, although their device was only tested for 48 hours at a time, the engineers believe that this was sufficient to demonstrate the viability of their approach. In future, by incorporating microfluidic designs into their tracker, the engineers say that it could have significant clinical applications, as a means of monitoring patients’ vitals for longer, and providing doctors with enhanced diagnostic data.
A graph depicting some of the results provided by the team’s athletic testing program. Images via the Science Advances journal.FDM printing’s sensing suitability
Thanks to the ever-growing accessibility and flexibility of FDM 3D printing, the technology has become a widely-adopted means of creating low-cost experimental sensors. Much like the Arizona team’s device, researchers at Jeonbuk National University have also 3D printed piezoelectric sensors that don’t require external power to function, and are powered by human movement.
A team at Sungkyunkwan University, meanwhile, have 3D printed wearable biosensors of their own, which are specifically designed to address personalized monitoring applications. Composed of a flexible silicone elastomer and sugar-based scaffold, the researchers’ devices can be utilized as diagnostic tools, for capturing users’ changing body strain signals.
Elsewhere, scientists at the National and Kapodistrian University of Athens, have developed an ‘e-ring’ glucose-monitoring system, capable of tracking diabetics’ blood sugar levels. Built using a conventional Flashforge Creator Pro 3D printer and conductive filament, the device could serve as a less-invasive self-testing alternative to normal glucometers.
The researchers’ findings are detailed in their paper titled “Biosymbiotic, personalized, and digitally manufactured wireless devices for indefinite collection of high-fidelity biosignals.”
The research was co-authored by Tucker Stuart, Kevin Albert Kasper, Ifechukwude Christian Iwerunmor, Dylan Thomas McGuire, Roberto Peralta, Jessica Hanna, Megan Johnson, Max Farley, Thomas Lamantia, Paul Udorvich and Philipp Gutruf.
To stay up to date with the latest 3D printing news, don’t forget to subscribe to the 3D Printing Industry newsletter or follow us on Twitter or liking our page on Facebook.
For a deeper dive into additive manufacturing, you can now subscribe to our Youtube channel, featuring discussion, debriefs, and shots of 3D printing in-action.
Are you looking for a job in the additive manufacturing industry? Visit 3D Printing Jobs for a selection of roles in the industry.
Featured image shows the engineers’ 3D printed sensing device attached to a bicep. Photo via the Science Advances journal.
Tags Jeonbuk National University National and Kapodistrian University of Athens ninjatek Philipp Gutruf Sungkyunkwan University Tucker Stuart University of Arizona xbox
Paul Hanaphy
Paul is a history and journalism graduate with a passion for finding the latest scoop in technology news.
Custom 3D-printed wearables never need to recharge
Researchers have developed a type of wearable device they call a “biosymbiotic device,” which has several unprecedented benefits.
Wearable sensors to monitor everything from step count to heart rate are nearly ubiquitous. But for scenarios such as measuring the onset of frailty in older adults, promptly diagnosing deadly diseases, testing the efficacy of new drugs, or tracking the performance of professional athletes, medical-grade devices are needed.
Not only are the new devices custom 3D-printed and based on body scans of wearers, but they can operate continuously using a combination of wireless power transfer and compact energy storage.
“It’s as simple as putting the device on. Then you forget about it, and it does its job.”
“There’s nothing like this out there,” says Philipp Gutruf, assistant professor of biomedical engineering, faculty fellow in the College of Engineering, and a member of the BIO5 Institute at the University of Arizona. “We introduce a completely new concept of tailoring a device directly to a person and using wireless power casting to allow the device to operate 24/7 without ever needing to recharge. ”
Current wearable sensors face various limitations. Smartwatches, for example, need to be charged, and they can only gather limited amounts of data due to their placement on the wrist. By using 3D scans of a wearer’s body, which can be gathered via methods including MRIs, CT scans, and even carefully combined smartphone images, Gutruf and his team can 3D-print custom-fitted devices that wrap around various body parts.
Imagine a virtually unnoticeable, lightweight, breathable, mesh cuff designed specifically for your bicep, calf, or torso. The ability to specialize sensor placement allows researchers to measure physiological parameters they otherwise couldn’t.
“If you want something close to core body temperature continuously, for example, you’d want to place the sensor in the armpit. Or, if you want to measure the way your bicep deforms during exercise, we can place a sensor in the devices that can accomplish that,” says Tucker Stuart, a doctoral student in biomedical engineering and first author on the paper. “Because of the way we fabricate the device and attach it to the body, we’re able to use it to gather data a traditional, wrist-mounted wearable device wouldn’t be able to collect.”
Because these biosymbiotic devices are custom fitted to the wearer, they’re also highly sensitive. Gutruf’s team tested the device’s ability to monitor parameters including temperature and strain while a person jumped, walked on a treadmill, and used a rowing machine. In the rowing machine test, subjects wore multiple devices, tracking exercise intensity and the way muscles deformed with fine detail. The devices were accurate enough to detect body temperature changes induced by walking up a single flight of stairs.
Gutruf and his team aren’t the first to adapt wearables to track health and body function. However, current wearable devices do not have the ability to track metrics continuously, or with enough precision to make medically meaningful conclusions.
Some wearables used by researchers are patches that stick to the skin, but they come off when skin goes through its normal shedding process, or sometimes when a subject sweats. Even highly sophisticated wearable devices used in clinical settings, such as ECG monitors, face these issues. Also, they aren’t wireless, which severely limits mobility. Patients can’t go about their normal daily routines if they’re tethered to bulky external devices.
The biosymbiotic device that Gutruf’s team has introduced uses no adhesive, and it receives its power from a wireless system with a range of several meters. The device also includes a small energy storage unit, so that it will function even if the wearer goes out of the system’s range, including out of the house.
“These devices are designed to require no interaction with the wearer,” Gutruf says. “It’s as simple as putting the device on. Then you forget about it, and it does its job.”
The research appears in the journal Science Advances.
Funding for the research came from the Flinn Foundation Translational Bioscience Seed Grants Pilot Program. The team has also been working with Tech Launch Arizona, the commercialization arm of the university, to protect the intellectual property and launch a startup to bring the technology to market.
Source: University of Arizona
Socks-DIY, from design to molding
ski
Loading
07/13/2019
5074
Personal diaries
Reprap
X190714: Das Ordnung to the 3D thermal insulation solution for the hot end, needs an obvious rethink.
Greetings!
Grain of Truth in Socks - yes,and almost every Step
Stefan rolled out a technique for molding socks for custom hit blocks from heat-resistant silicone. I liked this design technique for its 'matryoshka' approach
(the 15-minute video shows and tells the order of design too).
For you and me, the theme is 'accordion', one might say - annual, but for small-scale production under the order of Colleagues on the site - that's it.
The fact is that most domestic manufacturers do not complete budget models of 3D printers with such rubber bands. With the Chinese, I will not write here, guess for yourself.
My translation was described as:
I love E3Ds silicone socks, but even they have managed to ruin some of my prints.
In today's video, I'll improve on an existing and common 'sock' design, create a 3D printed five-piece silicone mold in Autodesk Fusion 360, and then mold brand new 'socks' using high temperature 2-component silicone.
Google translation - caption-translatable, checked tolerably.
Enjoy watching!
Regards,
Ski.
P.S.
Design & Cast your own Hotend Silicone Socks!
CNC Kitchen ; Published: 13 Jul. 2019
https://youtu.be/O5UiXky85hA
[]
Article comments
More interesting articles
dallas9
Loading
05. 10.2022
945
6
Subscribe to the author
Subscribe
Don't want
About printing composites on the example of the article https://3dtoday.ru/we-print/usilennyi-komplekt-napecatannyx-...
Read more
one
Follow author
Follow
Don't want to
Bought in CSN Flexpla. Test prints were for CNC machines 16k20f3. The first pancake is lumpy as usual...
Read more
DrProg
Loading
03/24/2019
15602
79
Subscribe to the author
Subscribe
Don't want
- How so, sick? After all, I clearly advised you not to visit such establishments at least a couple . ..
Read more
Rules for 3D modeling for 3D printing
It is known that a prerequisite for 3D printing is the presence of a 3D model, according to which the printer will grow a three-dimensional object. But, even after simulating an object, you should not assume with absolute certainty that the job is done, and soon the printer will give you the finished product. The fact is that not all models are suitable for 3D printing. There are certain requirements for the dimensions, thicknesses and design of models - and these requirements vary depending on the material used and the printer. In addition to these individual characteristics, there are general requirements that distinguish print models from other 3D models. And now we will talk in more detail about how to prepare a model for 3D printing.
First of all, you need to remember that STL files (for one-color models) and WRL (for color plaster 3D printing) are suitable for 3D printing. Almost all 3D modeling programs allow you to export models to STL, so this should not be a problem. You should also take into account that for online download on our website, files no larger than 50 MB each are accepted, as well as an extended list of formats that are automatically exported to STL: STP, STEP, OFF, OBJ, PLY and directly STL. If the file size is more than 50 MB, then you need to send the model to our email address: [email protected]. By the way, one of the easiest ways to reduce the volume of the model and the file size is to create hollow 3D models, we already wrote about how this works in our blog.
Before you start creating a model for 3D printing, it is important to understand what material you want to print the product from. Each material has its own individual characteristics for 3D modeling - maximum and minimum model dimensions, wall thicknesses, distance between moving parts, etc. You can learn more about the requirements for a particular material in the appropriate section on our website.
If you use the online model upload on our website, it will automatically check for standard 3D modeling errors. Models are checked instantly, and if errors that prevent 3D printing were not found, then immediately after uploading the model will appear in your personal account in the "My Models" section. If the model did not pass the test, then you will see a notification that the file cannot be loaded, then you will need to check and refine the model again.
What are the most common errors encountered when modeling for 3D printing?
- Inverted normals - incorrectly oriented normals. Normals should always point outward, they define the boundaries of the object and allow the 3D printer software to understand which is the inside and which is the outside of the model. If at least one of the normals is directed in the opposite direction and contradicts the other normal, then this causes a failure in 3D printing, since the printer cannot distinguish between the front and back sides of the object.
- Non-manifold geometry - Non-manifold 3D model is a prerequisite for 3D printing.
The essence of this concept is that each edge of a 3D model must have exactly two faces.
The following errors are usually included in this concept:
o Mesh with holes - "unclosed" mesh problem. Remember the basic rule of 3D modeling: your model must be "watertight" or "airtight". If a hole is formed, it means that some edge is missing one face, therefore the model is not manifold, and therefore not suitable for 3D printing.
o Presence of internal polygons. There must be no faces inside the model, for example inside walls.
o Common fins. An error occurs when more than two polygons are attached to the same edge. Each edge in your 3D model should connect only two adjacent faces.
o Matching edges. Occurs when two separate edges are created at the same location and are not connected, such edges must be merged into one common edge.
o Polygon overlap.
Learn more