Duke 3d printing lab
Bluesmith Printing Service | 3D Printing
Bluesmith Printing Service
OIT offers the Bluesmith 3D printing service that allows you to submit an .STL file and have the model of your choice fabricated and finished by one of the knowledgeable staff members at the Innovation Co-Lab Studio on West Campus. We offer both Fused Deposition Modeling (FDM) and Stereolithography (SL) for this service. For a small fee, you have the option of a basic service that does not include support structure removal and finishing or you can choose the premium service that includes top priority in the queue over all non-premium orders and also includes support structure removal and finishing. You can submit your .STL file and request an estimate HERE.
Pricing & Types of Service
The cost of 3D printing varies widely based on the technology used and amount of material depending on the size and design of each model.
Technologies & Equipment
We offer six types of 3D printing technology: Fused Filament Fabrication (FFF), Stereolithography (SLA), Multijet (MJP), Continuous Filament, Polyjet and Laminate (LOM). Most printing technologies generally require an overnight run time of the printer.
- FFF Printing
- Equipment – We use several FFF tools but primarily rely on Ultimaker 2+ and 2+ Extended 3D Printers
- Material choices – Nearly infinite. The CoLab supports PLA and PETG but over 1,000 other filament materials exist.
- Strengths – This printing type allows the greatest variety of material types (nearly infinite options exist), is typically the fastest 3D printing technology, has the largest build volume and is by far the cheapest printing method.
- Weaknesses – This is the lowest resolution 3D printing technology. The support material is difficult to remove and leaves scars on the print. The likelihood of failure increase exponentially with the size of the job.
- SLA Printing
- Equipment – Formlabs Form 2
- Material Choices – Acrylic-like materials in
- Strengths – A relatively high-resolution 3D print that balances cost for performance
- Weaknesses – More expensive than FFF, limited selection of materials.
The support material is difficult to remove and leaves scars on the print.
- When to use this technology – Use when you need a higher resolution print than FFF can provide but don’t want the expense of MJP or Polyjet.
- Continuous Fiber
- Equipment – Markforged 2
- Material Choices – Carbon fiber or fiberglass embedded nylon
- Strengths – Extremely strong. Very similar to FFF but winds carbon fiber or fiberglass string into the print job creating a part that’s several hundred times more resilient than regular FFF prints.
- Weakness – Limited material choices. More expensive than FFF. The support material is difficult to remove and leaves scars on the print.
- When to use this technology – Use in circumstances where you need to make extremely strong, useable parts
- LOM – Coming Soon!
- Equipment – MCor ARKe
- Material Choices – Colored paper
- Strengths – Multicolor printing
- Weaknesses – Specialty printer
- When to use this technology – This tech is a specialist in color printing.
This tool will allow you to build photo realistic models and apply colored surface textures
- MJP
- Equipment – 3DSystems MJP3600
- Material Choices – White ABS. Navy, white-opaque and black polycarbonate. Cast-able wax.
- Strengths – Similar to SLA but much higher resolution. No surface scars when removing support material. The support material is easily removed. 14-micron layer resolution.
- Weakness – Expensive and limited material selection
- When to use this technology – Use this when you need the highest resolution 3D print possible or prints without surface scars from support material
- Polyjet
- Equipment – Stratasys J750
- Material Choices – Nearly infinite.
- Strengths – Highest quality visualization 3D printing available. Full-color 3D printing. Easily removable support material with no surface scars on the part. 17-micron layer resolution.
- Weakness – Expensive…very expensive.
- When to use this technology – When you need full color, high resolution, scar free parts that can be made from a mix of solid and or flexible materials.
Pricing Structure
- FFF
- $10 base charge (100 grams included)
- $5 for each additional block of 100 grams
- Material Choices – Battleship Grey PLA or Blue PETG
- Model must be less than 223 x 223 x 305 mm
- For FFF printing users are welcome self-support and print for free in the CoLab
- SLA
- $30 base charge (100ml included)
- $10 charge for premium materials (flexible or tough resins)
- $10 charge for each additional 50ml
- Continuous Fiber
- $10 base charge
- $5 per 50 cubic centimeters of plastic
- $3 per cubic centimeter of carbon fiber
- $1 per cubic centimeter of fiber glass
- LOM
- Coming soon!
- MJP
- $20 base charge
- $.
50 per gram of material
- $.25 per gram of support
- Polyjet
- $30 base charge
- $1 per gram of material
- $.50 per gram of support
Failure Policy
3D printing is an experimental technology that often fails. Equipment failures are not unusual. CoLab Staff will make every attempt to print your object successfully. If equipment breaks or the print failed without cause we will attempt to print it again. The likelihood of failure increases significantly with more difficult-to-print models. If the failure is a result of simply submitting too difficult of a model, customers will still be charged an attempt fee of half the price of the initial quote. Users can accept the failed job or we can make a second attempt at the print; in this scenario, we will make additional attempts at 50% of the original estimate.
Duke University's 3D Printing Innovation Lab Allows Surgeons to Create Accurate 3D Printed Medical Training Models - 3DPrint.

3D printers in Duke University’s Innovation Co-Lab [Image: Innovation Co-Lab Studio]
3D printing is becoming increasingly more accessible and affordable in many industries, including the medical field. We often see the technology used for the purposes of creating accurate training models and simulators, so that medical professionals can practice surgeries and procedures ahead of time – this not only saves on costs, but can also allow surgeons to offer a better level of care.
Tawfig Khoury, MD, an otolaryngology (ear and throat) resident at Duke University, is focused on the latter, and uses 3D printing to improve patient care. He makes 3D printed medical models of the ear’s delicate temporal bones, which are later used for the purposes of medical training.
“One focus of my research has been taking CT scans of temporal bones, and printing an exact, patient-specific replica. Our residents can then practice drilling and performing other tests without having to work on an actual patient,” Dr.
Khoury explained.
Tawfiq Khoury, MD, Otolaryngology
Resident
Dr. Khoury works on his 3D printed models at the university’s Innovation Co-Lab Studio, which contains a network of over 80 3D printers, ranging from MakerBot and Markforged to Ultimaker and Formlabs, that have been used for various projects since the facility began to really grow last year and explore new uses for 3D printing at the university.
“With recent renovations, we now have a state-of-the-art facility, with high-end equipment across an entire floor dedicated to the lab,” Dr. Khoury said.
“The Innovation Lab is a great example of how different departments across the hospital, as well as other healthcare groups, residents, and students, can work together to create something of value for the community.”
The lab, previously described as a “creativity incubator,” also includes 3D scanning equipment, CNC machines and laser cutters, digital modeling workstations, and a multitude of electronics.
Physicians from several of the university’s medical specialties, including cardiology, neurosurgery, and neurology, use the patient record system Epic to access an ordering system in order to have medical models 3D printed in the studio from ultrasounds and CT and MRI scans. Occasionally, the Innovation Co-Lab Studio can provide its 3D printing services at no cost if the 3D printed replica models are created specifically for patient care.
One of the 80 3D printers in Duke University’s Innovation Co-Lab Studio [Image: Cara O’Malley]
In order to receive and handle requests for 3D prints from around the world, the studio uses 3DPrinterOS, the popular online cloud management system, as a service to the university’s community. 3DPrinterOS users have access to an online, live-streaming video of the project while it’s being 3D printed.
Since the facility’s expansion, a wider community of users have been taking advantage of its services. The expansion also gives Dr. Khoury the opportunity to, according to a post by Scott Behm with Duke’s Department of Surgery, “set his sights on some short- and long-term goals.”
Dr. Khoury feels that 3D printing, even though it can already create accurate models for the purposes of medical training, can go even further at the university. Before his residency at Duke is complete, he hopes to set up an efficient system in order to assist patients with facial trauma who must have maxillofacial reconstruction surgery. His main goal in this is to enable the routine creation of 3D printed models for eventual use in implants for this type of procedure.
Someday in the future, Dr. Khoury believes that we will be able to rely on 3D printers as a way to create organic replacement organs or body parts out of bioink or hydrogel, such as an eardrum, which can then be infused with live cells and implanted in a patient’s body.
Discuss this story and other 3D printing topics at 3DPrintBoard.com or share your thoughts in the Facebook comments below.
Stay up-to-date on all the latest news from the 3D printing industry and receive information and offers from third party vendors.
Tagged with: 3d printed medical models • 3D printed training models • 3D printing cloud platform • 3D printing studio • 3dprinteros • bones • ct scan • Duke Innovation Co-Lab • Duke University • ears • Medical Training • otolaryngology • patient care • patient-specific printing • Surgical Training
Please enable JavaScript to view the comments powered by Disqus.
3D printing laboratory - All about plastics - education, technology, perspectives
Prototyping and modeling using 3D printers has recently become more and more widespread. This is due not only to the development and cheapening of equipment for creating three-dimensional models, the emergence of new polymeric materials for three-dimensional printing, but also the emergence of the need for such modeling for medical products, aircraft parts, instrumentation, automotive and aircraft manufacturing, as well as souvenirs. and other areas. The use of polymeric materials for structural purposes for prototyping made it possible to produce not only models, but also small batches of technical products.
According to the recent study “3D Printing Market (2013-2020)” published by Markets and Markets (“M&M”), between 2013 and 2020, the annual growth of the 3D printing market will be 23%, resulting in will grow to 8.4 billion US dollars by 2020 (http://www.orgprint.com/wiki/3d-pechat/obzor-tehnologij-3D-pechati).
3D printing is a technology for creating three-dimensional objects from a digital sample (CAD) by layer-by-layer application of additive materials. 3D printing methods include stereolithography (SLA), powder laser sintering (SLS), electron beam melting (EBM), layer-by-layer printing with molten polymer thread (FDM), formation of three-dimensional models from layer-by-layer sheet material (LOM) and others.
Initially, 3D printing was used exclusively for prototyping objects, but recently a radical step has been taken towards production. Automotive, aerospace, medical, and consumer products are among the industries that are actively embracing 3D printing. According to M&M, 3D printing in medicine and aerospace will grow exponentially in the near future. 3D printing has significant growth potential, it is indispensable where piece production of personalized products is needed.
This article touches upon some aspects of 3D printing, which is carried out by layer-by-layer printing with a melted polymer thread (rod).
Layer-by-layer printing with a molten polymer thread , also known as Fused Deposition Modeling or simply FDM, is used to obtain single products that are close in their functional characteristics to serial products, as well as for the manufacture of investment molds for casting metals.
The main polymer materials used in FDM technology in Russia are ABS plastic, PLA (polylactide), to a lesser extent polyamide (PA-12 or PA-11), TPU, PET-G and a number of other polymers. Almost all polymeric materials are imported.
High impact polystyrene (HIPS) is used as support polymers. This material is used for printing ABS plastic, PMMA, PET-G. Polyvinyl alcohol PVA (PVOH, PVA or PVAL) is also used as a support polymer, however, due to the water solubility of this polymer, it is more difficult to obtain a thread from it, modification of the standard technology is required.
At the Interplastica-2018 exhibition, work was announced on the synthesis of special grades of structural polymer materials for 3D printers at the Kabardino-Balkarian State University (PSU, PFS, etc.). In the report of KNRTU (Kazan), the topic of using PP filament for 3D printing was mentioned, which is not surprising, since in the Republic of Tatarstan a wide range of PP grades is produced by Nizhnekamskneftekhim PJSC. The problem with polyolefins in printing is associated with poor adhesion to the 3D printer substrate and high shrinkage when cooled.
FDM printing technology is as follows: a polymer thread is fed into a heated head with a controlled temperature, in the head it is heated to a melt state and the resulting thermoplastic modeling material is fed with high precision in thin layers onto the working surface of a 3D printer. The layers are applied on top of each other, joined together and cooled, gradually forming the finished product.
The diameter of the nozzle through which a thread with a diameter of 3 or more often 1.75 mm is fed is 0.3-0.4 mm in the first case, and 0.1-0.3 mm in the second case. Therefore, the requirements for a polymer thread should be quite stringent in terms of sizing (thickness variation), stability of rheological properties (melt flow), melt purity (presence of impurities or contaminants).
1 shows the scheme of printing polymer thread FDM
1. Flow chart of 3D printing by FDM polymer filament printing.
The production of thread (rod) for FDM technology is carried out on extrusion plants for extruding rod, including a dryer, an extruder, usually a single-strand extrusion head, a calibrator (if necessary), a cooling bath, a gauge for the thickness (diameter) of the thread, 2 (rarely 4 -x positional) bar winder on the coil. There is a lot of information on the Internet about homemade filament extruders, as a rule, of low productivity and low quality filament. However, the production of thread must be carried out on specialized extrusion lines.
A diagram of such a line is shown in fig. 2.
Fig. 2. Extrusion plant for the production of polymer thread
I would like to note that for the wide development of FDM technology in our country, it is necessary to clearly define the characteristics of polymer materials that determine the possibility of their use in 3D printing technology with a polymer thread, as well as to synthesize or modify industrial polymers in order to obtaining material with the required characteristics. In particular, both thermophysical properties (for example, the thermal diffusivity coefficient, which determines the cooling rate of the material), and rheological properties (fluidity at different temperatures), as well as temperature parameters of the weldability of layers depending on the properties of the feedstock, etc., should be taken into account.
3D printing in chemistry - Ananikov Laboratory AnanikovLab.
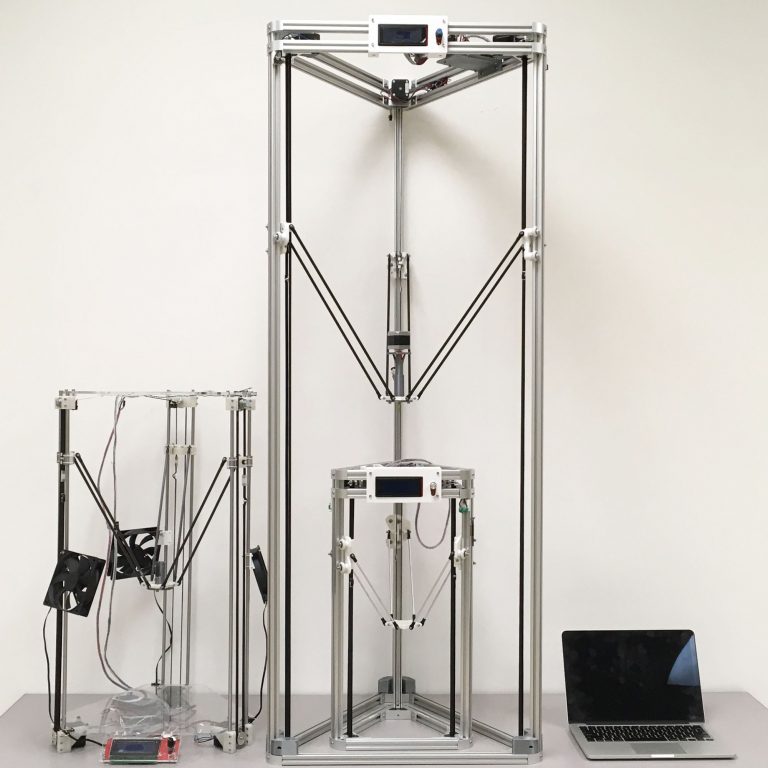
The cheapest, simplest, and most common 3D printing method is Fused Deposition Modeling (FDM). In the vast majority of cases, this method uses the direction of the polymer: the polymer in the form of a thread with a diameter of about 2 mm, wound on a spool, is fed into a small extruder, where it melts and is extruded (pressed) through the nozzle already in the form of a thin thread, from which the layers of the future part are formed. . The nozzle opening diameter and layer thickness together determine the resolution of an FDM printer. The design of such a 3D printer is relatively simple, so these devices are produced by many companies and their cost is low compared to 3D printers designed for printing by other additive methods. A significant advantage of FDM technology is the low cost of consumables, which are various polymers: acrylonitrile butadiene styrene (ABS), biodegradable polylactide (PLA), polyethylene terephthalate (PET), polypropylene (PP), nylon, polycarbonate, etc.
The process of 3D printing of chemical equipment elements from chemically resistant plastic using an FDM 3D printer.
The polymer filament deposition method has an average spatial resolution (usually 0.1 - 0.2 mm) and makes it possible to manufacture parts of various shapes and levels of complexity (Fig. 1). The enormous possibilities of 3D printing make it a very promising technology in education and science. Piece-by-piece production of unique laboratory equipment, visual aids (Fig. 2), mock-ups, models (including working mechanisms with moving parts) - all this is feasible even with the widely available FDM printing method.
Fig. 1. Attached spiral channel made from two different resins in a single 3D print run with two extruders running in sync. Finished products and a 3D model are shown.
Fig. 2. Ball-and-stick model of a molecule made by FDM printing from PLA plastic. To obtain a higher quality, the model was made in parts with subsequent assembly.
The high chemical resistance of some polymers (such as polypropylene, nylon, polyethylene terephthalate) in combination with the FDM printing method is well suited for the manufacture of small chemical laboratory equipment and chemical-technological laboratory installations. However, the real potential of 3D printing is not realized in the manufacture of standard laboratory equipment that can be bought, but in the creation of special products, such as chemical reactors, mixers and other elements of chemical installations, developed in-house for unique experiments.
The layering technology is mature enough to reproduce even the fine details of small chemical equipment. For example, Figure 3 shows a photograph of a mixer with three inlets and one outlet. The diameter of the internal channels of this mixer is only 2 mm. The conical notches on the inlet pipes are clearly visible, and the height of these notches is 0.5 mm. To increase the mixing efficiency, a miniature helical fin is made inside the central outlet channel. Of course, this is not yet the same thing as shoeing a flea, but everything is moving towards this. The manufacturing time of the mixer was 30 minutes. Try to make such a micro-mixer in half an hour using conventional methods!
Fig. 3. Mixer-tee in the working chamber of a 3D printer, made of polyethylene terephthalate using the FDM method.
Fig. 4. Chemical microreactor with a complex labyrinth channel inside, made of PET by FDM printing. The individual parts of the reactor and the assembly are shown.
The ability to manufacture products with a complex internal structure, as already noted, is one of the main advantages of 3D printing. This possibility is well illustrated in Figure 4, which shows a complete chemical reactor the size of a matchbox. Like the "adult" chemical reactor, this "baby" has a shell, a lid connected by bolts to the shell, and a gasket to seal the working space. It is enough to look under the lid to see the complexity of the inner world of this worker of science: a labyrinth channel is organized inside the reactor, forcing the reaction mixture entering the shell through the side pipe to move along a complex trajectory, so that the reaction time is optimal to obtain the desired products. There are small baffles at the bottom of the labyrinth channel to keep the finely dispersed catalyst from being washed out quickly. The reaction products leave the reactor through the lower branch pipe.
Microreactors can consist of any number of elements, each of which is individually manufactured using 3D printing (Fig. 5). Individual elements (Fig. 6) are eventually combined into workable chemical plants (Fig. 7).
Fig. 5. Microreactor, consisting of a shell, a lid, a catalytic cartridge and a replaceable nozzle. The individual parts of the reactor, the reactor assembly and a three-dimensional model of the assembly are shown.
Fig. 6. Mixer and zigzag microreactor made of PET.
Fig. 7. Laboratory chemical plant assembled from a microreactor and mixer, created by FDM printing methods.
3D printing can significantly speed up experimental chemical research, because it makes it possible to manufacture even complex multi-component chemical equipment right in the laboratory without significant material costs.