Cad files for 3d printing
3D Printer CAD Model Repositories – plugnplay3d
There are many 3D Printer CAD Model Repositories. The websites below are the ones we have used and recommend. Many have free downloadable CAD models and some are subscription services with low cost. A few are free CAD software companies with free models that have been designed with their software. We will add new websites as we find and use them.
Thingiverse (https://www.thingiverse.com/)Was created by the Makers of the MakerBot. Thingverse Is a universe of things. Download their files for free and build them with your lasercutter, 3D printer or CNC. This site is built with designers from all over the world. Thingiverse is one of the biggest and most popular free downloadable CAD file repositories in the universe.
Yeggi (https://www.yeggi.com/)Search engine for 3D printable models. The index contains 863,499 3D models. It is worldwide and many new models are added every day.
Hobbyists, kids, and backyard spaceship builders all agree that SketchUp Make is the easiest, most fun, entirely free 3D drawing tool in the world. We think you will too. SketchUp Make has many 3D models you can download all drawn on Sketchup free software.
Autodesk 123D (https://www.123dapp.com/)Autodesk123D has 10,000+ free 3D models for download or use free 3D modeling apps to create your own! Start with a 3D model, then customize it to your liking. Or, start from scratch with any of their amazing, free apps.
My Mini Factory (https://www.myminifactory.com/)A very large printable 3D model repository in which every 3D model has been certified printable and has been printed with good success.
3DShook (https://www.3dshook.com/)Choose from over 1,600 products and 6,000+ models to 3D print. These are tested, exclusive and designed by pros. 3DShook is perfect for 3D printing. Try this site for free.
A long-time repository with many interesting 3D models and projects.
YouMagine (https://www.youmagine.com/)The best open source print files and designs available for you to build upon or simply download and 3D print! Ultimaker’s companion 3D content repository, which contains many multi-part 3D printing projects.
CGTrader (https://www.cgtrader.com/)This is a 3D model marketplace for computer graphics and 3D printing, backed by a strong designer community. It contains digital material for 3D printing. With currently 260,000 3D models, this is a site that has many incredible pieces, but many are priced highly as a result.
GrabCAD (https://grabcad.com/)GrabCAD, Inc. is a Cambridge, Massachusetts-based startup that has created a free cloud-based collaboration solution that helps engineering teams manage, view and share CAD files
Cuboyo.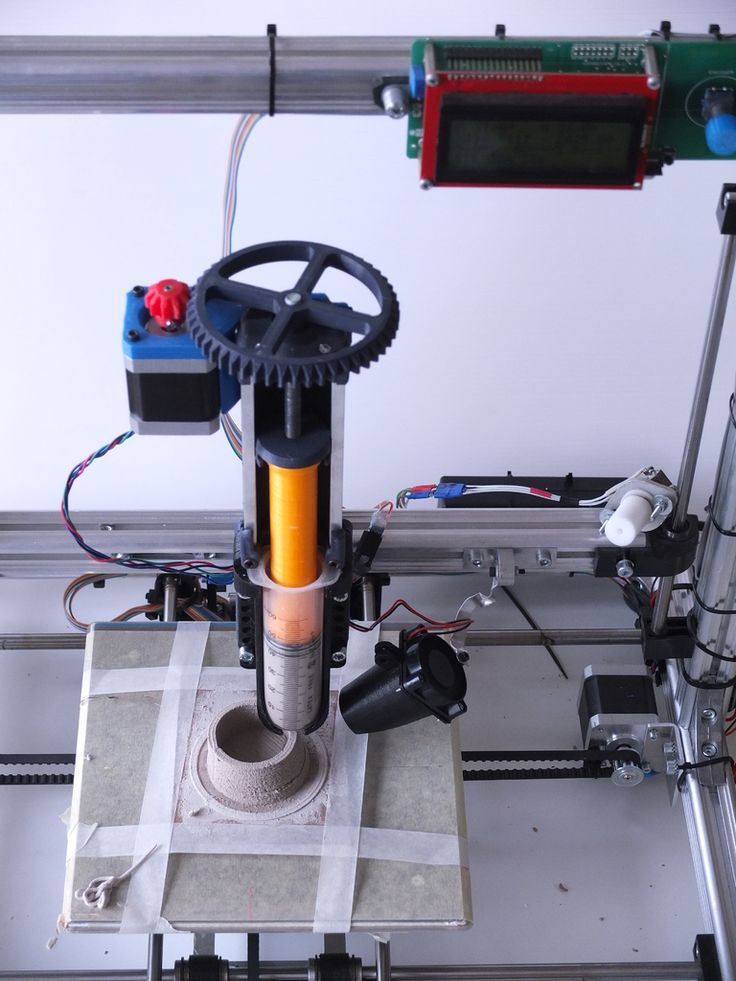
Three 3D Printing enthusiasts in Switzerland, with backgrounds in industrial engineering and software have launched Cuboyo. On Cuboyo you will find a whole array of 3D object files that you can print at your convenience anytime you want.
Pinshape (https://pinshape.com/)Pinshape is a thriving 3D printing community and marketplace full of quality 3D printable files. Sell and share your designs or download 3D files to print now!
3DAGOGO (https://3dagogo.com/)3DaGoGo offers a selection of awesome 3D designs that are verified to print in most consumer 3D printers. No more failed prints! A popular repository aligned with Astroprint containing many free and some low-priced 3D models.
3DShare (https://3dshare.com/)3DShare is the new marketplace for 3D printable files. Think of it as the appstore for 3D files. A busy 3D marketplace for designers and buyers, but with very low pricing and many free 3D models.
Printables.com (https://www.printables.com/)
Printables Your go-to site for high-quality 3D-printable models, no matter what machine you have. Download pre-sliced print files for your 3D printer and start printing immediately. Free and easy to use. Unique reward system. More than 120.000 models. Just download and print. Formerly PrusaPrinter.org
Cults・Download free 3D printer models・STL, OBJ, 3MF, CAD
Top design
By Holoprops
Do you want a fantastic way to customize your Switch Dock? Here's the Nintendo Switch Crystal Dock Decor! Super easy to print in any color to go along with your TV setup, it's print-in-place with no support. The model was carefully designed not to obstruct the AirFlow of the Switch or the cables at the back.
Download STL Files
01
STAR WARS ADVENT CALENDAR 2022 DAY #14 VINTAGE CHRISTMAS TR-33 DROID FIGURE, ORNAMENT.
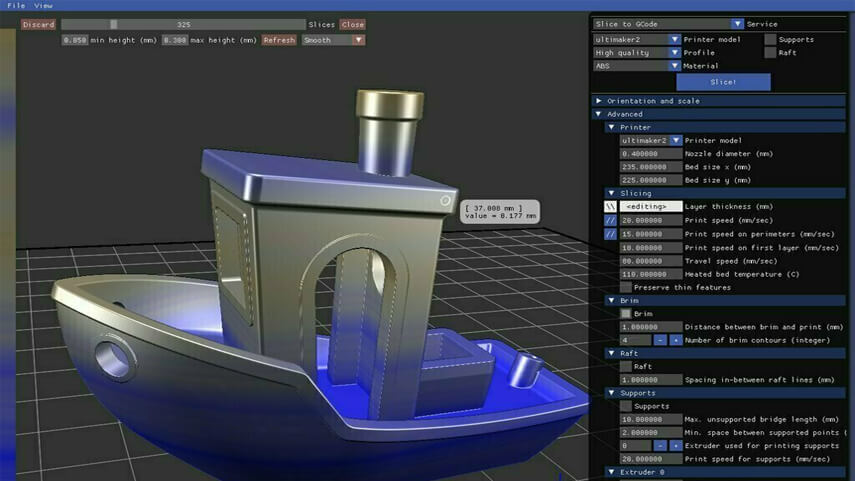
Free
02Rabbit 2023
Free
03PRINT-IN-PLACE MAGIC HAT KEYCHAIN
€2.99 -50% €1.49
Legs for Fruit
Free
05Santa Stocking Surprise by Play Conveyor
€3.07
06Bird nestingbox
€1.75
07Krampus
€2.90
08Maze Cube - Rookie
Free
09KUPPA, THE HAIRY FLEXI GNOME TO PRINT IN PLACE WITH HANDS UP
€2. 37
No-Face Mask | Spirited Away | Cosplay
€1.89
11BARAKA
€18.17
12Christmas vase tree
Free
13The Starry Night - Vincent van Gogh
Free
14The Thing from Wednesday - Flexi Print in Place
€4.53
15Table Lamp IN3
€3.08
16PRINT-IN-PLACE BUNNY KEYCHAIN
€2.99 -50% €1.49
Paper Pot Maker Dual - Gardening Tool
€1. 19
Mini Chevrolet Camaro
€1.88
19Skeleton Pirate - Flexible - Easy to Print - NO Supports
€2.50 -30% €1.75
Birdhouse
€0.99
01
Imperial Heavy Weapons & Regimental Flags [PRESUPPORTED]
€3
02Spartan Pen Holder
€1.80
03ItsLitho "Drop" personalized lithophane Christmas ball
€1.90
04FLEXI PRINT-IN-PLACE STANDING YETI
€2. 80
Foot FLSUN V400
€3
06App to create keychains
€3.50
07wall key holder (dragon ball)
€1.25
08FLORK WORLD CUP ARGENTINA KEY RINGS
€2.18
01
Pumpkin Mimic Monster
€1.93
02Phone Tablet Holder Stand
€3.48
03Flexy Baby Frilled Lizard Print In Place No Supports
€2.65 -50% €1. 32
Bones Tower / No Supports
€2.84
05Winner of the Ginmasio Crossfit contest | Kettlebell Medals
Free
06Ski + snowboard for Lego character
€0.50
07Toiletpaper holder
Free
08Revolving xmas tree
Free
09Flexi-friend Figure
€0.94
10Flexy Skeleton Toy.
€2.63
11GDIWol
€8
12Steve Irwin's Worst Nightmares
Free
13Nestable Christmas Tree
€1. 90
Snowflurtle: Winter Snowflake Turtle Cinderwing3D Mash-up, Flexi Articulating
€3.32
15christmas object santaclaus socks mug penholder
€0.73
16STAR WARS ADVENT CALENDAR 2022 DAY #12, VINTAGE STORMTROOPER NUTCRACKER (WORKING) FIGURE, ORNAMENT. 3.75", 1/18 KENNER, HASBRO
€2.84
17Gandalf pipe \ vape
€1.57
18Rugby Kicking Tee
€1
19Little BOO is ready for Christmas
€2.85
20False Book Commander or EDH Deckbox - Bookshelf Deck Box - Spellbook Cover
€3. -25% €2.84 79
01
King Cnidarian Fire Dispensers
Free
02Cnidarian Fire Dispensers
Free
03Condors of Conjuration
Free
04#3DBenchy - The jolly 3D printing torture-test
Free
05flexi turtle
Free
06PRINT-IN-PLACE SPRING LOADED BOX
Free
07Cute Mini Octopus
Free
08Corvidae Pattern Grav Bike
Free
🔁 Updated
Space Wolves Contemptor
€12. 50
SlingHAMMER - repeating Slingshot / Slingbow / Crossbow Pistol / Gun for 8mm Steel Balls
€12.50
APE NFT
Free
Second Generation Low-poly Pokemon Collection
€27.53
Full size Velociraptor skeleton Part05/05
Voidwalker Exosuits Truescale
SANTATLAS SNT-4 American Mecha Atlas Christmas Decoration (Santa Atlas)
Drum fed Autogun
Stumble guys ninja keychain
€0.56
Hellboy Hand
€3.99
black panther
€7
Gravity Falls - Mystery Shack
€15 -35% €9. 75
1pc Bubble Heart Bath Bomb Mold
€6
ORC BUST
€5.07
robot
€7
Controll Button for Climate device
Free
See all 3D models
Cults, the 3D printing platform
Welcome to Cults, the world’s leading independent website for 3D printer files. Discover and download the best 3D models for all your 3D printing & DIY projects.
Cults is a digital marketplace for 3D printing and design. Use our 3D model library to discover everything you can do with a 3D printer (FDM, SLA, DLP, SLS) event with CNC machining and laser cutting. You don’t know how to make a 3D file but you want to 3D print objects? Cults is for you! Browse our different categories and download the best 3D printer models for free, open-source or paid mode. The formats you can download are in STL, OBJ, 3MF, CAD, STEP, SCAD or DXF, DWG, SVG format, they are all 3D printable guaranteed or CNC compatible.
We are connecting 3D print files makers with people who want to use their 3D printer. Our 3D model repository acts as a real source of inspiration since the best designers share their best STL files daily to offer you their latest inventions!
On Cults you can also find a 3D printer nearby, get voucher codes to buy cheap 3D printers or filaments at best prices and also a whole series of 3D printing contests. Cults is a joyful community that brings together all 3D printing fans to dialogue and create together.
Commission system
You are a designer and you want to sell your 3D models optimized for 3D printing? Thanks to Cults you can earn money with your files STL, OBJ, CAD, 3MF, etc. ! For each download, you will receive 80% of the net selling price (excluding VAT) via PayPal. Cults keeps 20% of commission which is used to finance bank fees (about 5%) and then all the costs related to the technical maintenance of the platform: hosting, bandwidth, accounting, email communications, translations, etc. There is no subscription system or fixed fee to pay. You sell, you win!
If you are still hesitating to share your models on Cults, feel free to read this article Why publish my designs on Cults? List of advantages and benefits to get an idea.
- Designers 80%
- Cults 15%
- Banking fees 5%
Upload a 3D model
Various file formats for 3D printing・Cults
With the development of digital technology, 3D printing has become much more accessible today. Individuals and professionals can have their own equipment and make various print models. All that is required is a good understanding of the basic concepts, especially in relation to the respective file formats. Indeed, depending on the field and for historical or practical reasons, certain file formats are preferred for 3D printing. Here are the most common 3D printing formats and their main characteristics.
STL is short for "Stereolithography", one of the oldest file formats for 3D printing. Developed in the late 1980s, this type of format is still widely used today. It describes the surface geometry of a 3D object without displaying color, texture, or other attributes. The STL format has the ".STL" extension. These files are generated by computer-aided design (CAD) software. Programs such as FreeCAD, Blender, MeshLab, MeshMixer, SketchUp, SculptGL, and 3DSlash can be used to edit and repair STL files.
The STL file simplifies a 3D surface into a "tessellation", a series of small triangles that increase in number when it is necessary to represent and recreate curved surfaces as best as possible. When a large number of triangles need to be used, the size of the 3D model STL file increases rapidly.
The OBJ file format is also very popular in the 3D printing industry. Its extension is ".OBJ". It has the advantage that it also encodes color and texture information, which is stored in a separate file with a ".MTL" extension. OBJ files allow the use of non-triangular faces, with one face adjoining another. They can be opened with programs such as Autodesk Maya 2013, Blender and MeshLab .
Developed in the 1990s, 3DS is a file format that stores only the most basic information about geometry, appearance, scenes, and animation. It allows you to save properties such as color, material, texture, transmissivity, etc. With the ".3DS" extension, this 3D printing file format also has the advantage that it can be read by most programs on the market, such as 3dsMax, ABViewer, Blender, MeshLab, messiahStudio, Rain Swift 3D, SketchUp, TurboCAD etc.
An SLDPRT file or its .SLDPRT extension is a 3D printing image format used by the SolidWorks CAD software. It contains a 3D object or "part" that can be combined with other parts into a single ".SLDASM" assembly file. SLDPRT files are usually opened with the SolidWorks program. However, they can be viewed using SolidWorks eDrawings Viewer, Autodesk Fusion 360, Adobe Acrobat 3D, Acrobat Pro 9 or later .
The SCAD format (.SCAD extension) is generated by OpenSCAD, a freeware modeling program used for various 2D and 3D projects. The SCAD file can be used to design 3D objects, specifying the object's geometry and positioning information. It can only be opened with OpenSCAD .
The .BLEND format is an extension used for 3D animation and projects designed with Blender's 3D modeling tool. This file type can contain multiple scenes as well as all project elements such as objects, textures, 3D meshes and real-time interaction data, sounds, lighting data, animation keyframes, display layouts, and interface settings. Please note that only Blender can work with this 3D file format.
The 3MF file (.3MF extension) is used by various design programs to save 3D models for printing. This format includes model, material, and property data compressed using ZIP compression. 3MF files also store a print ticket, a thumbnail image, and one or more digital signatures. They can be opened with programs such as Microsoft 3D Builder, Microsoft Paint 3D, Dassault Systemes SolidWorks, Dassault Systemes CATIA, McNeel Rhino, PTC Creo and Ultimaker Cura .
The .GCODE file contains commands that define how the 3D printer should print. It stores instructions such as print speed, set temperature, and where to move print items. This 3D file format is created with cutting software such as Simplify3D and Slic3r. Reading can be done with Simplify3D, as well as Blaze3D, GCode Viewer and NC Viewer .
A .SKP file is a 3D model format created by SketchUp. This takes into account wireframes, textures, shadows, and edge effects. This file type is also used to store components that will be inserted into the document. Of course it can be opened with SketchUp, but also with programs like IMSI TurboCAD Pro or Deluxe, Okino Computer Graphics PolyTrans, ACCA Edificius and Trimble 3D Warehouse .
FBX is a 3D printing file format popular in the film and video game industry. Developed by Kaydara and acquired by AutoDesk, it supports geometry and appearance properties such as color and texture, as well as skeletal animation and morphs. AutoDesk will use the ".FBX" FBX file as an interchange format for its software portfolio such as AutoCAD, Fusion 360, Maya, 3DS Max, etc.
Other file types are not exclusive to 3D, but are regularly used in the field.
A .RAR file is an archive containing one or more compressed files. The compression ratio of this format is greater than that of the classic ZIP compression. It is used to compress files to reduce their size for easier transportation and storage. You can extract files from RAR archive using various unpacking programs such as RARLAB WinRAR, Corel WinZip or B1 Free Archiver .
.DWG files are databases of 2D or 3D models created in AutoCAD. They consist of information about the vector image and metadata that describes the contents of the file. There are many utilities available to open this file format, including: Autodesk Auto CAD, Autodesk Inventor, Autodesk Design, Autodesk DWG, AutoDWG DWGSee, CADSoftTools ABViewer, Canvas X, Adobe Illustrator, Bricsys Bricscad, etc.
Used in 3D editing programs such as Adobe Photoshop and Autodesk Maya, the .MTL format is used to store material settings. This file is stored along with another in .OBJ format and is used to describe how textures should be applied and the 3D coordinates they should be applied to.
This page has been translated using machine translation. Suggest the best translation
Previous
ShareNext
Similar publications
Since their invention, 3D printers have proven that printing many objects is much more efficient than conventional manufacturing techniques. However, calibration is required for optimal performance when printing 3D parts. Many 3D printer owners find this procedure tedious and time-consuming. However, it is much easier than it seems if you know the right tips on how to do it. Cults3D presents the various steps you need to follow in order to successfully calibrate your printer.
Read more The plate is one of the most important parts of a 3D printer. For optimal printer performance, it must be properly cleaned after each print session. Traces of the thread are deposited on it over time. While cleaning a 3D printer plate is not a difficult task, it can quickly become one if you don't have an effective method or the right cleaner. How to clean this important part of the 3D printer? We invite you to identify the most effective methods.
quick tips for moving from a CAD model to a printed object / Sudo Null IT News
was withdrawn from publication due to a technical error. Please be understanding. Thank you!
Whether it's just a hobby or a source of income, 3D printing is always based on product design. Those accustomed to traditional technologies will have to rethink the entire approach to product design and manufacture.
When the project is ready, a number of additional operations are performed: setting the orientation of the model and other parameters that ensure the proper printing process. In addition, it is necessary to take into account the fact that most 3D printers allow you to choose the degree of filling the model with cellular structures. The correct choice of this parameter provides protection of the object from deformation and destruction during the printing process, as well as significant savings in material and reduction in production time.
Finally, the last factor influencing the success or failure of the 3D printing process is the strength of the connection between the model and the table. If the workpiece is separated from the table during printing, then all the work will go down the drain.
Here, we'll walk you through the 3D printing process and give you a few simple tips for using the power of additive manufacturing in the design phase. In addition, we will dwell on the methods of preparing a finished project for printing, and also consider ways to securely fasten the workpiece to the table.
These guidelines apply primarily to Fused Deposition Printers (FDM) printers, but may apply to other types of printers as well. The process of obtaining a finished part by 3D printing is basically the same regardless of the method used.
Designing an object
Any 3D printing starts with construction. If you are developing a product yourself, then you need to build a 3D model of it in a computer-aided design (CAD) system to turn the designer's idea into reality. In this case, the object can be both very simple and very complex. However, too thin and too small models should be avoided.
3D-CAD from Siemens from this article for 49900r (90% discount), the promotion is valid until March 20, 2020. Read more>>
Saving the file in a special format for printing
To print an object, its model must be saved in a special file format - for example, STL, which has become the de facto standard in the world of 3D printing. In this format, model surfaces are represented as a grid of triangles. Simple surfaces are broken down into a small number of triangles. The more complex the surface, the more triangles you will need. Today, other formats are used in 3D printing, in particular, the 3MF format developed by Microsoft. But the most common is still STL.
CAD-systems make it very easy to save the model in the desired format: just click the Save As command. To improve print quality, it is desirable to set a number of settings for saving to the STL format - for example, the tolerance during transformation and the angle of the plane. The lower the conversion factor and the better the angle, the smoother the printed part will be.
Opening the file in the slicer program
Most, if not all, 3D printers come with their own slicer software. The slicer loads the STL file created in the CAD system and cuts it into layers, and then creates a control program for the printer.
Place the model correctly in the print space
After entering the print settings, the model (or several models) needs to be placed on the printer table. You can print many objects on one table at once. At the same time, compared to printing a single object, the time slightly increases, but in general it still turns out to be less. Here are some tips for choosing the right model orientation.
Set parameters
In the slicer program, the user sets parameters such as print speed, material consumption, nozzle and desktop temperatures. Most slicers have simple settings for beginners. In this case, most often there are also advanced settings so that experienced professionals can achieve optimal results. Advanced settings include percentage infill, amount of backing material, and type of backing or raft (this is a small, thin base that keeps the printed part stable. The backing is removed when it's finished). The number of options is truly endless. Specific settings vary depending on the brand of printer. It's easy enough to set them up.
Sending the control program to the printer
After setting the print settings, the placement of future objects on the table, their orientation and quality, it's time to finally start the printer. It is enough to press the Print button and find something to do while the production is in progress. Depending on the complexity of the design, the process takes from several minutes to several hours.
Finishing
Finishing includes removing the printed part from the table, as well as removing the support material by melting, mechanical separation or dissolution (depending on the design of the printer). The part may require some light sanding or polishing, but overall a properly printed object looks good from the start. Other types of finishing are placing plastic parts in a container with acetone to smooth out surface roughness, gluing (if the dimensions of the structure exceed the dimensions of the 3D printer or individual elements of the object must have different orientations), drilling holes and painting.
3D printing process
3D printer design considerations
Eliminate sharp corners
If the direction of the surfaces changes abruptly (for example, a vertical wall intersects with a horizontal overlap), then such a model is difficult to print. The printer will build excessive inner surfaces, wasting too much material. There are two easy ways to prevent this: add chamfers to smooth out where the surfaces meet, or round the corners so the printer gradually builds a vertical surface. In addition, rounding will increase strength, since destruction most often occurs at sharp corners.
Elimination of thin walls and small geometries
Layer by layer fusing technology consists in supplying hot plastic through a nozzle with the formation of a printed object layer by layer. The thickness of the extruded plastic layer cannot be made smaller than a certain limit, depending on the diameter of the nozzle and the speed of the print head. Excessively thin-walled details are difficult to print - often the result is a chaotic weave of fibers. If the part can be printed, it is very fragile and breaks easily.
Too thick walls - also bad
On the other hand, if the walls are too thick, they become brittle and crack easily. This is especially important when printing from materials other than resins, as excess thickness during the manufacturing process leads to internal stresses in the part. Even when printing from plastics, material is wasted on walls that are too thick and time is wasted.
Removing large overhangs
3D printers allow you to create amazing shapes and surfaces, but they are not capable of printing directly in the air. If there is a void in the part with material above it, additional support material must be used. Most slicers add material automatically, but require you to specify the orientation and volume of the support structure. Printers with a single nozzle create an array of thin columns, which then have to be broken off. The result is an uneven surface. Therefore, it is recommended to avoid large overhanging elements whenever possible in order to reduce the need for support material.
If such an element is unavoidable, you can try to flip the object. Most printers are capable of printing overhanging elements with an angle of about 45 degrees. At a certain height, the edge of such an element may sag somewhat. The actual capabilities of a particular printer are determined by trial and error.
Holes shrink
Remember that the part is made of heated plastic. As it cools, it inevitably shrinks. Therefore, holes and other critical structural elements have to be made larger so that after shrinkage their size is as close as possible to the required one.
However, if a tight tolerance hole needs to be made, it is better to print it in a smaller diameter and then ream it with a suitable tool. This is especially true for holes whose axis is parallel to the printer table.
Increasing the footprint
If the area of contact between the object and the base is small, the part may separate from the table during printing. To prevent this from happening, wide bases are added to the model legs, which are installed on the printer table. In general, the closer to the table, the more material must be added to the support. There are other ways to securely fasten the part to the table, which we will discuss a little later.
Special moves
The right approach to design makes printing easier. In addition, there are special post-processing techniques that are important to be aware of.
Arrange round surfaces vertically
The model should be oriented so that the minimum amount of support material is used. Ideally, it should rest on the table with a large flat edge. In addition, circular geometry must be placed so that the circular faces are vertical. If we look at the printer table from above, we should see a round silhouette of the object. In this case, the part comes out as symmetrical as possible with the formation of a solid round structure.
Place voids and holes vertically
If there are voids in the model (for example, it is a rectangular pipe), it is desirable to place such voids vertically in order to reduce the volume of the support material. If you print the pipe in a horizontal position, you will have to provide support for the entire interior. If you put the pipe on the end, then no support is required at all.
The same is true for holes: to get a hole with a straight axis, it is best to print it vertically - in the form of a stack of rings, which avoids warping or deforming a round hole into an oval one.
Set print quality settings
Proper selection of print parameters, such as STL conversion tolerance and slicer software settings, allows parts to be produced with a surface quality that matches that of cutting. However, this entails an increase in print time. When choosing quality parameters, one should proceed from the purpose of the object: is it a finished product or a prototype? Will the part be visible or hidden?
The quality parameters also affect the shape of the holes in the part. In CAD files, holes are represented as a set of straight lines at an angle to each other. The higher the quality of the model in the saved STL file, the less the circle looks like a polygon.
Reducing the layer thickness
To obtain the best quality, especially when using layer-by-layer deposition technology, it is necessary to reduce the thickness of the layers. It does increase the print time, but the end result is worth it!
Optimizing the filling with honeycomb structures
In terms of strength, objects do not have to be solid. Similar to a honeycomb, printers can create a honeycomb infill that balances strength and saves expensive polymer material. However, if the printed part serves as a prototype for strength testing, and the serial product will be manufactured by traditional methods, and also if the part is subjected to certain types of mechanical stresses and pressures, a solid design will be preferable.
Choosing material
The success of printing largely depends on the correct choice of material. Materials have different properties. For example, the melting point of thermoplastic polyurethane (TPU) and polylactic acid (PLA) is lower than that of acrylonitrile butadiene styrene (ABS). In addition, the material is taken into account when choosing the type of support structures. For an object made of polylactic acid, supporting elements can be made from the same polylactic acid, since it will be quite easy to separate them from the finished part. If the part is printed from ABS plastic, then the support elements must be made from a different material, and it is better not to use such elements at all in thermoplastic polyurethane parts.
Cellular filling
A solid body is not always the best choice for 3D printing. Printing solid parts has its advantages, but the internal honeycomb structure saves both expensive material and time.
Creating objects with a specified degree of filling with honeycomb structures is a unique opportunity for 3D printing. Moreover, it is not required to design such a structure: this is done by the slicer program. As a rule, it is enough to set only the percentage of filling (the closer it is to 100, the more solid the object will turn out) and select the type of cells, if the printer has such an opportunity.
In addition to saving time and material, the internal honeycomb structure has many other advantages.
Cellular filling prevents warping
Printing large objects as a single piece introduces a danger of warpage. By reducing the infill percentage, the air during printing passes through the part, providing more uniform cooling and eliminating warpage.
Cellular filling does not lead to loss of strength
Printing cells instead of solid material does not reduce the strength of the part. In many cases, a honeycomb part is strong enough for the chosen application, but lighter and less material intensive.
The function determines the choice of cell geometry
Most slicers support a wide variety of cell geometries. The optimal option is determined by the functional purpose of the object. Standard box padding simplifies printing, while hexagonal and triangular boxes add strength. Wave fill allows the object to bend or twist.
How do I choose the right filling percentage?
In general, the strength of an object increases as the percentage of infill increases. Most printers have a default infill percentage of 20, which is optimal in some cases but too high or too low in others. Consider mechanical stresses in the printed object and increase the percentage of infill in areas where greater strength is required. If high strength is not required, choose the lowest possible filling. This saves material and speeds up printing. Most often, the selection of the optimal percentage of filling is done by trial and error.
Ways of fastening the workpiece to the table
“Rafts”, “brims”, “skirts” – these terms sound funny, but they just refer to the three main ways of attaching a 3D printed part to a printer table. Let's take a look at each of these methods and their areas of application.
Skirt
The skirt involves creating a few rings around the object at the beginning of the print to make sure the plastic is extruded normally. The skirt is not in contact with the object at all. It surrounds the printable area and helps start the fusing process. When creating a skirt, a large volume of hot thermoplastic polymer passes through the nozzle. This prepares the printer for printing the part itself. This guarantees good adhesion to the table and obtaining smooth surfaces of the object.
Brim
The brim is a wide, flat area connected to the main object as a support base (think of a brim of a hat). It is very similar to a skirt, but connected to the model. In addition to all the advantages of a skirt, the brim keeps the edges of the object being made on the table.
When printing, the outside of an object often cools faster than the middle, causing the edges to curl. Brim prevents this phenomenon by holding the edges.
Raft
A raft is a detachable base, made in the form of a thin mesh platform, located under the entire object (which lies on the raft). To create a raft, the printer first prints a flat plate in two or three layers, and then begins to manufacture the object.
The rafts provide excellent adhesion to the table surface and also provide a strong print base. This is especially useful when making small and oddly shaped parts that do not fit well on the table, as well as thin-walled objects.
After printing is completed, in most cases the raft will separate easily from the part.
If the printer does not have a heated desktop function
Rafts are used if the printer does not have desktop heating. In this case, excessive adhesion becomes a problem.
An alternative method is to apply adhesive paper tape to the printer platform, with the edges down if possible (this protects the platform itself). You can also use packing tape, but it is usually more expensive.
If buckling does occur or the object separates from the table, apply a dissolvable glue stick to the adhesive tape. This will enhance adhesion.
Find out the features of a specific 3D printer and take them into account when preparing your model
3D printing is not only a science, but also an art. Effective design for subsequent 3D printing requires an understanding of the technological process, taking into account its features and the purpose of the future object. This will greatly improve print performance.
Using Solid Edge in 3D printing
Not all CAD systems are suitable for 3D printing
The capabilities of the applied system should not limit the designers. Our Solid Edge system is designed with the latest 3D printing technologies in mind. Various 3D printers and 3D printing services are supported.
Take it to the next level with specific techniques for designing 3D printed parts
Generative modeling in Solid Edge opens up new possibilities: the designer selects a specific material, sets the design space, allowable loads, restrictions and target mass of the part, and the system automatically calculates the desired geometry. As a result, 3D printing methods can produce the most complex shapes.
In addition, when building models, the use of the results of three-dimensional scanning is provided. Solid Edge successfully combines the traditional boundary representation of solid models (B-Rep) and the representation of surfaces in the form of a grid of triangles, which avoids time-consuming transformations that are fraught with errors.
If you've already downloaded an STL file for printing, our unique synchronous technology allows you to quickly and easily edit your imported models in Solid Edge in preparation for the process.