Best 3d metal printer
Best metal 3D printers in 2022: comprehensive overview
What is the best metal 3D printer in 2022?
Over the past few years, there has been a surge in both supply and demand for metal 3D printers.
Manufacturers are launching metal additive manufacturing machines that are faster, easier to use, and more powerful with an increasing number of compatible metals.
Many businesses are adopting these 3D metal printing technologies to produce cost-effective metal parts and prototypes, benefiting as well from increased freedom of design linked to additive manufacturing. They are suitable for a variety of industries such as aerospace, automotive, health, engineering, and more.
Although metal 3D printer prices have been slowly and slightly decreasing, these machines are still relatively expensive acquisitions, mostly ranging from $80K to almost $1M.
With our metal 3D printer selection, we aim to provide a comprehensive overview of what’s available from well-established and distributed brands, at various price points, and with different metal 3D printing technologies.
The best metal 3D printers in 2022
Brand | Product | Build size | Country | Price Approximate starting prices based on supplier-provided information and public data. Prices may vary by region, over time and do not include additional products or services (taxes, shipping, accessories, training, installation, …). | |
---|---|---|---|---|---|
Markforged | Metal X (Gen 2) | 300 × 220 × 180 mm11.81 × 8.66 × 7.09 in | United States | $ 99,500125 000 €88,260 £14,831,072 ¥ | Quote |
Desktop Metal | Studio 2 | 300 × 200 × 200 mm11.81 × 7.87 × 7.87 in | – | $ 110,000110 000 €97,574 £16,396,160 ¥ | Quote |
Xact Metal | XM200C | 127 × 127 × 127 mm5 × 5 × 5 in | United States | $ 110,000100 000 €97,574 £16,396,160 ¥ | Quote |
Pollen AM | Pam Series MC | ⌀ 300 x 300 mm | – | $ 140,000135 000 €124,186 £20,867,840 ¥ | Quote |
TRUMPF | TruPrint 1000 | 100 × 100 × 100 mm3.![]() | – | $ 170,000170 000 €150,797 £25,339,520 ¥ | Quote |
3D Systems This brand is a certified partner from our network. | DMP Flex 100 | 100 × 100 × 80 mm3.94 × 3.94 × 3.15 in | – | $ 245,000245 000 €217,325 £36,518,720 ¥ | Quote |
EOS | EOS M 100 | 100 × 100 × 95 mm3.94 × 3.94 × 3.74 in | Germany | $ 350,000350 000 €310,464 £52,169,600 ¥ | Quote |
XJet | Carmel 700M | 501 × 140 × 200 mm19.72 × 5.51 × 7.87 in | – | $ 599,000599 000 €531,337 £89,284,544 ¥ | Quote |
Desktop Metal | Production System P-1 | 200 × 100 × 40 mm7.87 × 3.94 × 1.57 in | United States | upon request | Quote |
Digital Metal | DM P2500 | 203 × 180 × 69 mm7.99 × 7.09 × 2.72 in | – | upon request | Quote |
Formalloy | L-Series | 1000 × 1000 × 1000 mm39.![]() | United States | upon request | Quote |
GE Additive | Arcam EBM Spectra L | 350 × 350 × 430 mm13.78 × 13.78 × 16.93 in | United States | upon request | Quote |
GE Additive | M2 Series 5 | 250 × 250 × 350 mm9.84 × 9.84 × 13.78 in | – | upon request | Quote |
Renishaw | RenAM 500E | 245 × 245 × 335 mm9.65 × 9.65 × 13.19 in | – | upon request | Quote |
SLM Solutions | SLM 125 | 125 × 125 × 75 mm4.92 × 4.92 × 2.95 in | Germany | upon request | Quote |
SPEE3D | LIGHTSPEE3D | 300 × 300 × 300 mm11.81 × 11.81 × 11.81 in | – | upon request | Quote |
TRIDITIVE | AMCELL | ⌀ 300 x 350 mm | Spain | upon request | Quote |
Velo3D | Sapphire | ⌀ 315 x 1000 mm | – | upon request | Quote |
Expand to see more specs
Technology: The technologies listed above are main categories of metal 3D printing technologies. Most manufacturers have their own branded technologies, which fall into the main categories that are listed in the table.
The products in the table are ranked by price (low to high).
Brand | Product | Technology | Build size | Country | Price Approximate starting prices based on supplier-provided information and public data. Prices may vary by region, over time and do not include additional products or services (taxes, shipping, accessories, training, installation, …). | |
---|---|---|---|---|---|---|
Markforged | Metal X (Gen 2) | Extrusion | 300 × 220 × 180 mm11.81 × 8.66 × 7.09 in | United States | $ 99,500125 000 €88,260 £14,831,072 ¥ | Get a quote |
Desktop Metal | Studio 2 | Extrusion | 300 × 200 × 200 mm11.81 × 7.87 × 7.87 in | – | $ 110,000110 000 €97,574 £16,396,160 ¥ | Get a quote |
Xact Metal | XM200C | SLM/DMLS | 127 × 127 × 127 mm5 × 5 × 5 in | United States | $ 110,000100 000 €97,574 £16,396,160 ¥ | Get a quote |
Pollen AM | Pam Series MC | Extrusion | ⌀ 300 x 300 mm | – | $ 140,000135 000 €124,186 £20,867,840 ¥ | Get a quote |
TRUMPF | TruPrint 1000 | SLM/DMLS | 100 × 100 × 100 mm3.![]() | – | $ 170,000170 000 €150,797 £25,339,520 ¥ | Get a quote |
3D Systems This brand is a certified partner from our network. | DMP Flex 100 | SLM/DMLS | 100 × 100 × 80 mm3.94 × 3.94 × 3.15 in | – | $ 245,000245 000 €217,325 £36,518,720 ¥ | Get a quote |
EOS | EOS M 100 | SLM/DMLS | 100 × 100 × 95 mm3.94 × 3.94 × 3.74 in | Germany | $ 350,000350 000 €310,464 £52,169,600 ¥ | Get a quote |
XJet | Carmel 700M | Material Jetting | 501 × 140 × 200 mm19.72 × 5.51 × 7.87 in | – | $ 599,000599 000 €531,337 £89,284,544 ¥ | Get a quote |
Desktop Metal | Production System P-1 | Binder Jetting | 200 × 100 × 40 mm7.87 × 3.94 × 1.57 in | United States | upon request | Get a quote |
Digital Metal | DM P2500 | Material Jetting | 203 × 180 × 69 mm7.![]() | – | upon request | Get a quote |
Formalloy | L-Series | Directed Energy Deposition | 1000 × 1000 × 1000 mm39.37 × 39.37 × 39.37 in | United States | upon request | Get a quote |
GE Additive | Arcam EBM Spectra L | EBM | 350 × 350 × 430 mm13.78 × 13.78 × 16.93 in | United States | upon request | Get a quote |
GE Additive | M2 Series 5 | SLM/DMLS | 250 × 250 × 350 mm9.84 × 9.84 × 13.78 in | – | upon request | Get a quote |
Renishaw | RenAM 500E | SLM/DMLS | 245 × 245 × 335 mm9.65 × 9.65 × 13.19 in | – | upon request | Get a quote |
SLM Solutions | SLM 125 | SLM/DMLS | 125 × 125 × 75 mm4.92 × 4.92 × 2.95 in | Germany | upon request | Get a quote |
SPEE3D | LIGHTSPEE3D | Material Jetting | 300 × 300 × 300 mm11.![]() | – | upon request | Get a quote |
TRIDITIVE | AMCELL | Extrusion | ⌀ 300 x 350 mm | Spain | upon request | Get a quote |
Velo3D | Sapphire | SLM/DMLS | ⌀ 315 x 1000 mm | – | upon request | Get a quote |
Main types of metal 3D printing technologies
The four main types of 3D metal printing technologies are:
- Metal Powder Bed Fusion 3D printing (SLS, SLM, DMP)
- Directed Energy Deposition (DED)
- Metal filament extrusion (FFF, FDM)
- Material Jetting and Binder Jetting
There are also some resin-based metal 3D printers, and metal sheet lamination 3D printers, but they are harder to come by.
It is not uncommon to see different acronyms and names for similar technologies. Each brand markets their own, proprietary methods. Some metal 3D printer companies even use a mix of different technologies.
Here we provide a deeper look into each 3D metal printer from our list. They are grouped together according to their main 3D printing technology type (powder bed fusion, material/binder jetting, extrusion, and DED).
Extrusion-based metal 3D printer selection (FFF, FDM)
Extrusion consists of heating the material (filament) and pushing it through a nozzle. In the metal 3D printing case, the filament is generally made up of metal particles mixed into a binding agent.
After the part is 3D printed, the result is a raw object or part; it must go through several post-processing steps– such as debinding and sintering– to attain its final form.
Most extrusion-based metal 3D printing processes include these steps. The above illustration is sourced from Desktop Metal (Bound Metal Deposition™ process).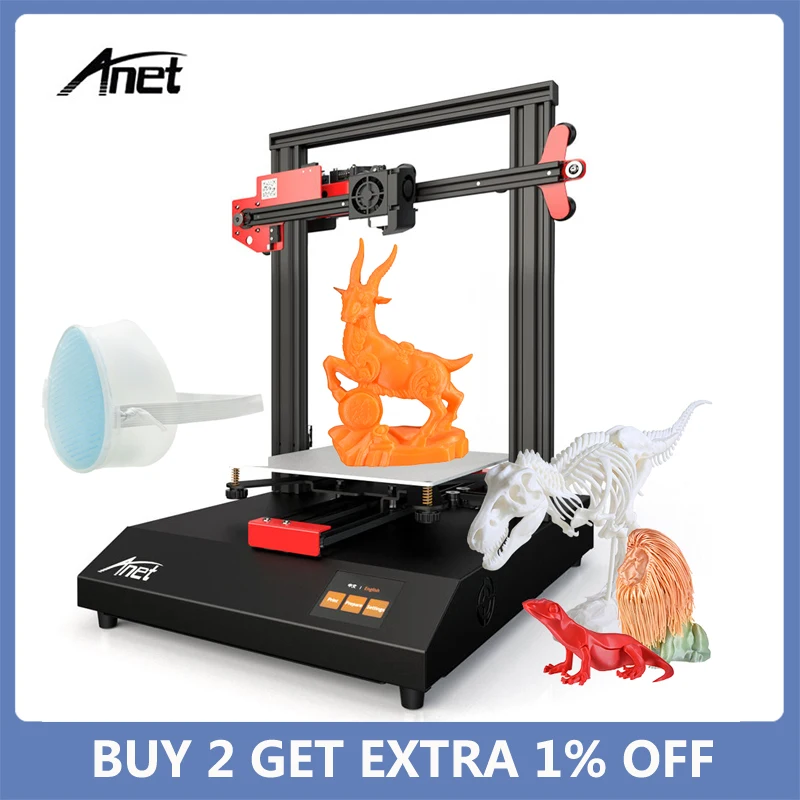
Desktop Metal’s Studio is an office-friendly, end-to-end metal 3D printing system. Aside from the printer, the Studio line also includes a debinding machine and a furnace for sintering. Indeed, parts 3D printed with this Desktop Metal 3D printer are “green”.
The Studio printer, with its proprietary Bound Metal Deposition technology, uses filament that is filled with small, metal rods. During debinding, the binding material (wax and polymer binders) is dissolved thanks to a proprietary liquid substance. The part is left porous, and must go in the furnace for its particles to fuse and densify the part.
Contact manufacturer Get a quote Add to comparison
MarkForged is specialized in continuous fiber 3D printing, but also offers metal 3D printing with their Metal X system, featuring Atomic Diffusion Additive Manufacturing (ADAM) technology.
This MarkForged 3D printer extrudes metal-filled plastic filament to form the part, which must then be washed with a special debinding fluid (Wash-1 Station) and then sintered in a furnace (Sinter-1 or Sinter-2 MarkForged machines).
Available metal 3D printer filament includes various Steels (h23, A2, D2 tool steels, 316L stainless steel) as well as Inconel, Copper, and Titanium.
Contact manufacturer Get a quote Add to comparison
Canada-based Rapidia offers an interesting and unique way to 3D print metal. They use a water-based metal paste, which eliminates the need for chemical debinding. The water evaporates during the 3D printing process, so the part only needs to go through the furnace in order to completely solidify and attain its final form.
Confirmed, available paste types include several Stainless Steels, Inconel, and a few ceramics. Copper, Tungsten Chrome Carbide, Titanium, and various other metals are in development.
The ExOne Metal Designlab, designed in collaboration with Rapidia, works on the same basis.
Contact manufacturer Get a quote Add to comparison
Pollen AM is a French manufacturer that has been producing pellet 3D printers since 2013. Their Pam Series MC is a delta-style 3D printer (cylindrical build volume) that can print metals, ceramics, and thermoplastics.
It extrudes injection-molding-grade pellets instead of metal 3D printer filament, driving material costs down significantly. Pollen AM names their technology “Pellet Additive Manufacturing”.
Contact manufacturer Get a quote Add to comparison
This machine was built with one goal: enable mass production 3D printing of metal parts 24/7. The AMCELL is fully automated, with auto feedstock control, environment control (temperatures, humidity, air filtering), and an ejection system fitted with a conveyor belt.
Rather than providing one, big build volume, the TRIDITIVE AMCELL boasts eight delta-style ø 220 x 330 mm build areas. Its eight “robots” deposit metal-infused filament to create 3D metal parts. TRIDITIVE states that resulting parts are similar to ones produced with traditional MIM (Metal Injection Molding) methods.
TRIDITIVE’s technology is called Automated Multimaterial Deposition®.
Contact manufacturer Get a quote Add to comparison
Metal powder bed fusion 3D printer selection (SLS, SLM, DMP, and more)
At the moment, the most commonly used metal additive manufacturing technology is powder bed fusion 3D printing. Simply put, the 3D printer creates objects out of a bed of powdered metal by using a powerful laser.
3D Systems, a historical actor on many 3D printing fronts, presents the DMP FLEX 100 as a fast, precise, and affordable metal 3D printer. It offers impressive part repeatability and surface finishes, of around 20 μm and 5 Ra μm respectively. DMP stands for Direct Metal Printing.
The printer comes with 3D Systems’ software 3DXpert All-in-One Software Solution for Metal Additive manufacturing. Their LaserForm metal 3D powders are certified.
Contact manufacturer Get a quote Add to comparison
This compact metal 3D printer is destined for the production of small parts in small quantities. Its material portfolio is especially interesting for medical use cases, namely dental crowns and bridges. EOS certified metal powders include Cobalt-Chrome, Stainless Steel, and Titanium.
The EOS M100’s laser spot is precise enough to provide a great level of detail, backed by 200 W of powder.
Contact manufacturer Get a quote Add to comparison
Originally a Swedish company, Arcam was acquired by GE Additive a few years ago. The Arcam EBM Spectra L is up to 20% faster than its predecessors and is able to reduce part costs by around 10%.
This metal 3D printer is dedicated to Titanium 3D printing, but Copper is in the pipeline as well. Its laser beam power is equal to 4.5 kW, partly explaining the printer’s high melting capacity and productivity. Common applications for this printer include orthopedic implants and parts for the aerospace industry.
Contact manufacturer Get a quote Add to comparison
Concept Laser is the company behind GE Additive’s M2 Series 5. It offers an easy, optimized workflow, with a separate processing chamber and handling area that is integrated into the system. This closed-loop material system ensures a safe environment that is free of powder for the operator.
The M2 metal additive manufacturing solution is compatible with a range of metals, from Stainless Steels to Aluminum, Nickel, Titanium, and Cobalt-Chrome.
Contact manufacturer Get a quote Add to comparison
The RenAM 500E is Renishaw’s entry-level metal additive manufacturing solution. It offers a relatively large build volume and powder can be handled via a dedicated glove box to avoid powder from getting free.
This system is also equipped with an oxygen sensor and a proprietary emission-filtering system branded SafeChange™.
Contact manufacturer Get a quote Add to comparison
Officially established in 2006, SLM Solutions has been a historical player in the powder bed fusion industry for many years. The SLM 125 boasts an open software architecture that allows users to tweak the system’s parameters according to specific use cases, materials, and general needs.
Options such as laser monitoring and melt pool monitoring are available for businesses that require full transparency and control over their production series.
Contact manufacturer Get a quote Add to comparison
The TruPrint 1000 is TRUMPF’s most compact metal 3D printing system, with a 100mm-tall cylindrical build volume. It is suitable for the production of small parts and prototypes, and even small production series when equipped with the multilaser option that increases the printer’s speed.
This metal 3D printer can be operated remotely via a tablet application, which also gives access to its onboard camera stream.
Contact manufacturer Get a quote Add to comparison
The Velo3D Sapphire is a high-volume metal 3D printer from the US designed for production series. This metal 3D printer features Velo3D’s Intelligent Fusion technology to allow for complex geometries and 0° overhangs.
The system is also equipped with a range of metrology sensors that measure each and every layer that is 3D printed.
Contact manufacturer Get a quote Add to comparison
The XM200C is Xact Metal’s entry-level metal 3D printing solution. It is suitable for both research purposes and small production series. The XM200C benefits from a proprietary Xact Core gantry system for precise movements with a fusing speed of up to 500 mm/s.
Xact Metal offers their own materials, branded Xact Powder, including various Stainless Steels, Super Alloys, Tooling Steels, Aluminum, Titanium, Bronze, and Copper. Advanced users are able to use their own metal powders if needed.
Contact manufacturer Get a quote Add to comparison
Metal material jetting and binder jetting 3D printers
Material jetting 3D printers are equipped with various inkjet printheads (somewhat similar to 2D printing) that jet material onto a surface. The material then hardens, and another layer of “metal ink” is jetted on top.
Binder jetting is a similar process, but it is a binding agent that is jetted atop a layer of powder.
The Production System by Desktop Metal was designed for mass production. It is advertised by Desktop Metal as being a fast, cost-effective metal additive manufacturing solution, with a cost per part up to 20 times lower than with other metal 3D printing systems.
This Desktop Metal 3D printer is equipped with over 16,000 nozzles that are mounted onto a “print bar” that recoats the build plate with powder at the same time, hence explaining the technology’s name: Single Pass Jetting™.
Contact manufacturer Get a quote Add to comparison
Digital Metal, a Höganäs Group company, creates incredibly detailed metal parts with their DM P2500 system. It is able to print 3D metal parts with an accuracy as high as 0.001mm (1µ), and with a medical-grade surface quality of around 0.006mm (6µ).
Another interesting feat to point out is that almost 100% of leftover powder can be recycled for future prints. This metal AM machine is able to churn out serial production series efficiently and reliably; one of the company’s first DM P2500 printers has been running 24/7 since 2013, according to Digital Metal.
The Digital Metal DM P2500 is a certified metal 3D printer (CE and UL) that is compatible with certified metal materials (ISO 22068).
Contact manufacturer Get a quote Add to comparison
Australian manufacturer SPEE3D has developed an impressively fast metal 3D printing technology called Supersonic Deposition. The technology is based on metal cold spray, using compressed air to “jet” metal powder through a nozzle at high speeds.
This enables the LightSPEE3D to 3D print at up to 100 grams per minute and with a range of metals including copper.
Contact manufacturer Get a quote Add to comparison
XJet developed an impressive, proprietary jetting technology they call NanoParticle Jetting™. This inkjet method disperses millions of tiny droplets that contain nanoparticles of solid metal. The liquid material comes in cartridges that are easy to insert into the printer.
After being printed, the metal parts must go through support removal and sintering processes to attain their final form.
Contact manufacturer Get a quote Add to comparison
DED: Directed Energy Deposition metal additive manufacturing systems
Directed Energy Deposition (DED) is comparable to filament extrusion. The metal material is pushed through a special nozzle, like with FFF/FDM, but a powerful laser beam solidifies the material at its deposition point.
Formalloy produces a range of metal DED 3D printers with up to 5 axes of motion. They can be used to produce metal parts but also to repair or clad existing parts.
Different laser wavelengths are available, as well as different build volumes: 200 x 200 x 200 mm, 500 x 500 x 500 mm, and 1000 x 1000 x 1000 mm. Metal 3D printers from Formalloy can be customized depending on company requirements.
Contact manufacturer Get a quote Add to comparison
Alternative metal 3D printers and special mentions
Hybrid metal manufacturing systems
Some manufacturers are specialized in hybrid metal manufacturing systems. They combine both subtractive and additive manufacturing methods, often with robotic arms that are able to move on more than three axes.
Some of the biggest actors on the hybrid metal AM system market are:
- Gefertec (Germany)
- DMG Mori (Germany)
- Matsuura (Japan)
- Sodick (United States)
XXL-sized metal 3D printers for industrial production
For those that require very large metal parts, there are several huge, industrial machines that offer gigantic build volumes for industrial production. To name a few:
- Sciaky EBAM 300
- Titomic TKF1000
- ADC Aeroswift
- ADIRA AddCreator
- Fabrisonic SonicLayer 4000
- ExOne X1 160PRO
- InssTek MX-600
- BeAM Modulo 400
- Optomec Lens CS 600
- Additive Industries MetalFAB1
Metal 3D printers from China
There has recently been a lot of growth in the metal 3D printer market in Asia, and more specifically in China. Some Chinese brands have been upping their game in that respect, providing industrial-grade metal 3D printing options:
- Farsoon
- ZRapid Tech
- Shining 3D
- Wiiboox
However, we feel that they are not yet playing in the same league as the 3D printers from our main selection, mostly due to a lack of distribution networks, after-sales service and training, and other factors which tend to matter when considering them together as a whole.
R&D metal 3D printers for labs
In certain cases, metal 3D printers are used for research purposes to develop and test new materials. There are a few machines that are specifically designed for this:
- Open Additive PANDA-6”
- Freemelt ONE
- Sharebot metalONE
Pros and cons of metal 3D additive manufacturing
Benefits of 3D printing metal parts
- On-demand production: Metal additive manufacturing offers more flexibility and control over the production line.
- Complex designs made possible: With 3D printing technology, it is possible to create highly detailed and intricate parts that would have to be broken down into several pieces with traditional methods.
- Waste reduction: Compared to CNC milling, for example, metal AM produces much less waste as it only consumes the material needed for a certain part. This is more true for extrusion-based methods than it is for powder-based methods, where it isn’t always possible to re-use 100% of unsintered or unbinded material.
- Lighter parts: Whereas metal parts are usually completely solid infill-wise with other methods, 3D printing allows parts to be more or less hollow without undermining their strength and resistance.
- Cost-effectiveness: All the above benefits of metal 3D printing can inherently reduce costs per part, although high metal 3D printer prices do represent a significant entry barrier. Reaching a positive return on investment can take a while depending on your throughput.
Limits of metal 3D printing
- Metal 3D printing prices: Metal AM systems are still quite expensive, as are metal powders and metal filaments. There are hidden costs, too (e.g. energy consumption, learning curve, etc.).
- Environmental constraints and safety precautions: Most metal 3D printers have a large footprint and require specific operating environments with controlled temperatures, hygrometry, and more.
- Post-processing: In many cases it is necessary for parts to be post-processed, whether it’s debinding and sintering or finishing touches for surface quality.
- Physical properties: It can be difficult to achieve the same physical properties that traditionally manufactured metal parts have. There are a number of factors (e.g. anisotropy) to take into account during the design process and file preparation before even trying to 3D print a certain part.
Metal 3D printing materials
Which metals can you 3D print?
A growing number of metals and metal alloys can be 3D printed. These are the main ones:
- Aluminum
- Titanium
- Nickel, Inconel
- Copper
- Bronze
- Cobalt, Cobalt-Chrome
- Steels (tooling, maraging, stainless)
- Precious metals (gold, silver, platinum)
Which metal 3D printing material formats are available?
Metal 3D printing material can be found in various formats, catering to different metal 3D printing methods. The most common are:
- Powder
- Wire
- Filament
It is also possible to find metal 3D printing resin as well as metal sheets for lamination-based 3D printers.
Metal 3D printer price: how much does a metal 3D printer cost?
Industrial metal 3D printer prices generally range from about $30,000 to over one million dollars for the most premium, industrial-grade metal additive manufacturing systems.
Additional costs to consider are the materials for metal 3D printing, which can cost a few hundred USD/kg, as well as costs linked to post-processing (tools, time, etc.).
Applications for metal AM systems
There are thousands of possibilities and use cases for metal 3D printing in a wide range of industries. A few industries have been incrementally using metal AM:
- Aerospace
- Automotive
- Medical
Whether it’s for tooling, replacement parts, or final products, many businesses can benefit from metal 3D printing.
However, metal additive manufacturing isn’t necessarily beneficial for every single metal part. Although some metal 3D printing systems have a relative capacity for serial production, it is generally cheaper to keep using traditional methods for simple parts.
For cases where complex geometries, rapid prototyping, and mass customization are required, metal AM is convenient and efficient.
Metal 3D printing services: order 3D metal parts online
For professionals with limited office space and human resources, low budgets, and/or few needs of custom parts and prototypes, metal 3D printing services can be an ideal solution.
These additive manufacturing service companies own a variety of high-quality 3D printers with different technologies, and their professionals are experts in 3D printing. It is possible to order metal 3D parts on-demand, without acquiring a 3D printer or having to buy a certain material for one-time use.
Here are some of the most trusted 3D printing service providers that offer metal printing services:
- Sculpteo
- Shapeways
- Hubs (ex 3D Hubs)
- Stratasys
- i.materialise
- Protolabs
Metal 3D printing technologies and acronyms
Many manufacturers develop proprietary variations of existing technologies and label them their own registered names:
- Powder Bed Fusion (PBF): DMLS (Direct Metal Laser Sintering), DMP (Direct Metal Printing), LaserCUSING, LBM (Laser Beam Melting), LMF (Laser Metal Fusion), SLS (Selective Laser Sintering), SLM (Selective Laser Melting)
- Directed Energy Deposition (DED): DMT (Direct Metal Tooling), EBAM (Electron Beam Additive Manufacturing), EBM (Electron Beam Melting), LENS (Laser Engineered Net Shaping), LMD (Laser Metal Deposition)
- Metal Material Jetting (MJ) or Binder Jetting (BJ): Magnet-o-Jet, Nanoparticle Jetting, SPJ (Single Pass Jetting), Metal Jet
- Metal filament extrusion/Fused Filament Fabrication (FFF): ADAM (Atomic Diffusion Additive Manufacturing), CEM (Composite Extrusion Modeling), FDM (Fused Deposition Modeling), FFD (Fused Feedstock Deposition), FMP (Filament Metal Printing), BMD (Bound Metal Deposition), MIM (Metal Injection Molding)
- Lamination: SL (Sheet Lamination), UAM (Ultrasonic Additive Manufacturing)
- Metal resin 3D printing: DLP (Digital Light Processing), FluidFM, SLA (Stereolithography)
Metal 3D printing FAQ
Is 3D printed metal strong?
Metal 3D printed parts can be as strong (or even stronger) as metal parts created with traditional manufacturing processes such as casting. The part’s strength will, however, depend on the metal AM method used and the conditions in which it is 3D printed.
When was 3D metal printing invented?
Metal 3D printing became possible in the 1990s with the development of Selective Laser Melting technology. However, 3D metal printing only started to gain traction and public interest from around 2010 onwards.
How does metal 3D printing work?
There are several ways to 3D print metal. Layers of metal filament can be deposited one after the other, producing a green part that must later go through debinding and sintering steps. It is also possible to fuse metal powder particles together with a laser, or with an inkjet printhead that deposits drops of binding material onto the powder.
10 Best Metal 3D Printers 2022 (Pros, Cons, FAQs & More)
Metal 3D printing has become a hot topic recently mostly due to the fact that the current 3D parts that are being printed are really good quality. So good in fact, some of it is actually better than what is made by normal methods.
Traditional methods tend to be wasteful when it comes to making metal and plastic parts. Often, when metal parts are made, almost 90 percent of the metal material is cut away creating a lot of waste and using a lot of energy. By using a 3D printer to create these same metal parts, manufacturers can use less energy and minimize waste.
Plus, the metal pieces that are printed can weigh up to 60 percent less than those pieces made with traditional manufacturing. Industries such as airlines can save a lot of money in fuel with this type of weight reduction. This has been an exciting new technology to keep an eye on as there can be so much development in a short period of time, things can progress almost within the blink of an eye.
Attempts to print with metal can actually be traced back to the 1880s by welders using carbon electrode arcs to fuse pieces of metal together. It really wasn’t until the development of the laser that 3D printing was brought to the general public and the eventual introduction by NASA of the technique called selective metal melting (SLM) Engineers at NASA has made it successful in producing parts with complex geometry and dimensional accuracy that is beyond what was thought possible with regular fabrication methods.
The fastest method of 3D printing has been discovered through depositing a powder metal matrix that has binders and, after each layer is deposited, the binder is melted and held together temporarily until a final baking in an oven. This process has been streamlined by Shapeways to give the public the fastest process possible from a variety of metal materials.
Industrial Metal 3D Printing
Buying a metal 3D printer for your business is a big and expensive step. It is probably not a wise business decision unless you plan on printing metal every day. The costs of just the printer can run between $100.000 and $500.000, plus you will need to add the additional cost of a salary for someone to not only run the printer, but who can also maintain it.
Instead of investing in your own 3D printer, you should probably look into hiring a 3D printing service that can take care of your needs, and companies like Sculpteo and iMaterialise will actually mail you your metal 3D printed parts right to your door. They currently offer 3D printing in the following metal materials:
• steel
• copper
• aluminum
• brass
• sterling silver
• bronze
• titanium
• gold
• platinum
Professional goldsmiths can also order the wax models that they need for casting custom orders. This has been a rapidly growing service all around the world with the 3D printing metal machines becoming more common at 3D printing services.Big companies have become fond of these services as they can easily create fully automated factories that are producing enhanced parts that allow you to evenly distribute the material in a part so it can be engineered to withstand more stress making it structurally sounder while still reducing its weight.
If you do intent to use one of these companies, they will require special software use like a special CAD Design or Shapeways has specific 3D printing metal guidelines.
Shapeways
Offering two types of services, Shapeways is one of the world’s most popular online 3D printing services allowing you to choose from a wide range of professionally designed items and then customizes them with your printed specifications. Shapeways is comparable to other 3D printing services giving designers the option of a storefront to print and sell their work. It can also provide rapid prototyping allowing customers to benefit from industrial grade printers like EOS and 3D Systems with dedicated technical support.
Shapeways uses the following 3D Printed Metals:
- Aluminum
- Brass
- Bronze
- Gold
- Platinum
- Precious plated metals
- Silver
- Steel
Shapeways can also make castable wax for jewelers.
Sculpteo
Similar to i.materialise and Shapeways, Sculpteo is an online 3D printing service that lets you upload a 3D model and they will then create it from a choice of materials. You can also open a storefront to sell your creations and it uses a lineup of 3D printers including high-end machines like EOS, 3D systems, ZCorp, and Stratasys. Using extensive technical documentation, Sculpteo helps you to find any design flaws and find just the right material you need to create your project.
Sculpteo uses the following 3D Printed Metals:
- Alumide (plastic added with aluminum particles)
- Brass
- Silver
i.materialise
Materialise works primarily with industrial clients to create 3D printed products and prototypes, but its online 3D printing company called i.materialise works with the individuals and the general public to allow them to upload their designs to print them out. After their products have been successfully reproduced, i.materialise allows them to sell it on their gallery or online store.
i.materialise uses the following 3D Printed Metals:
- Alumide (plastic with added aluminum powder)
- Brass
- Bronze
- Copper
- Gold
- Silver
- Steel
- Titanium
3D Hubs
You can also use 3D hubs to find individuals and businesses that provide 3D printing services in your area. You can connect with them directly and upload your STL file for an instant estimate. You can filter by distance, materials, and user rating. No matter what type of product you want printed, there is a good chance you will have someone in your area willing to do it, plus many of the materials can be printed in industrial quality which you can note with an »HD« in the search field.
3D Printed Metals Applications
You probably don’t even know it but 3D printing is being used more and more for average objects like dental and medical implants. Since they can be adapted to an individual’s needs, they are considered the best available option for patients.
Jewelry has also benefited from the improvement in 3D metal printing technology as it enables manufacturers to switch from lost wax casting and resin 3D printing to direct metal 3D printing. The aerospace industry has also seen an increase in use of 3D printing metal objects and the automotive sector is the next industry where the manufacturers are using 3D printing not just for prototypes, but to make actual car parts
3D printing is still overcoming some obstacles, mostly its high cost, as well as its low production speed which can cause problems for printing 3D metal objects. However, many of the issues that metal 3D printers contend with are similar to any 3D printer that consists of limitation with hardware and software, plus materials and material optimization. Most metal parts generated by a 3D printer are just as strong as components made with traditional methods if not above industry standards in some cases.
Metal 3D Printing At Home
For those interested in metal 3D printing at home, there are several obstacles to overcome including the need for very high temperatures to do the printing. This is not a technology that we will see for in home use probably within the next few years. But, as the technology evolves, there will be a lot of growth in these new applications.
It is possible to use added metal powders to a plastic filament that contain a high enough percentage of metal powders but also enough plastic that it can be printed at a low enough temperature that any 3D printer could do it. This combination will still have enough metal to have the feel and look of a metal object. The Dutch company Formfutura has a new metal 3D printing filament that they have increased their ratio up to 85 percent metal powder and 15 percent PLA for more of a metal feel.
If you do plan to try some of these metal 3D printing filaments, you may want to upgrade your 3D printer nozzle depending on your 3D printer’s quality. You may also want to invest in a durable printer hotends that is made of metal and can withstand high temperatures and can be mounted onto most 3D printers. Since metal 3D printing filament can be pretty abrasive, you will have to replace your 3D printer nozzle fairly often. And, don’t forget about investing in a proper finishing process like sand grinding, waxing, greasing, brushing, or coating so that your metal 3D print object can shine.
Available Metal 3D Printing Technology Types
Powder Bed FusionMost large companies are using powder bed fusion in their metal 3D printing process meaning that they use an energy source like a laser or another energy beam to fuse atomized, or perfectly round particles, powder to make the layers of the objects.
With eight major metal 3D printer producers in the world, this technology has already made its way into a number of machines and more and more are entering the market all the time. This technology is called DMLS (Direct Metal Laser Sintering) or SLM (Selective Laser Melting).
Binder JettingBinder jetting is another professional approach that uses a powder bed where the layers of metal particles are glued together and later sintered or melted together in a high-temperature kiln like with ceramics. Also similar to ceramics is the capability of mixing the metal powder into a metal paste and using a pneumatic extrusion 3D printer to create the 3D objects with the final step being sintered in a kiln. This approach is used by Mini Metal Maker 3D printer which is the only really affordable metal 3D printer on the market.
Metal DepositionThe final method for metal 3D printing is fused filament deposition which is not really possible for a desktop printer. This is a good option for very large industrial metal manufacturers who can deposit metal. The first option is called DED (Directed Energy Deposition) or Laser Cladding that uses a laser beam to fuse slowly released metal powder that is deposited as layers of an object with an industrial robotic arm in a closed chamber.
The second option is called EBAM (Electron Beam Additive Manufacturing) which is a type of soldering process that has a very powerful electron beam that is used to fuse molten metal and a 3 mm thick titanium wire and is shaped into very large metal structures. Only individuals that work for the United States Defense Department will need this type of technology.
Types of Metal Used
TitaniumOne of the most commonly used metals for 3D printing is pure titanium, either Ti64 or TiAl4V. Its versatility is an attractive quality as it can print out both light and strong. It is mainly used in the medical industry in creating personalized prosthetics and in the automotive/aerospace industries in making prototypes and parts.
Titanium is used in both binder-jetting and powder bed processes. It does have one catch, it tends to be highly reactive, so it can explode easily in powder form which is why when it is 3D printed, it uses a vacuum or in an argon gas atmosphere.
Stainless SteelWhen looking at affordability, stainless steel tends to be the most inexpensive as well as strong metal to 3D print. This is also a versatile metal that is used in many art and design projects as a well as a wide assortment of industrial applications. Because of this type steel alloy, you will find it almost exclusively used in industrial projects due the nickel and cobalt it contains making it have very high elastic properties while remaining hard to break.
InconelThe superalloy called Inconel is manufactured by Special Metals Corporation. Inconel is made of mostly chrome and nickel and retains a high-temperature resistance which is why it is mainly used for projects in the chemical, oil, and aerospace fields like black boxes on airplanes.
Aluminum is very light and versatile making it a popular metal to use with 3D printing projects. Primarily, it is used as different Aluminum based alloys.
Cobalt ChromeContaining a very high specific strength, this metal alloy is used mostly to make dental implants, turbines, and orthopedic implants. These are all applications where 3D printing has become a popular manufacturing method.
Copper and BronzeMostly used in wax casting processes, copper and bronze are usually not used a lot in powder bed fusion processes as they are not the perfect choice for industrial projects. They are more commonly used in arts and crafts.
IronIron is usually only used as an additive to PLA based filaments like ProtoPasta and TreeD.
Gold, Silver and Other Precious MetalsPrecious metals like silver, gold, and platinum are used mostly by powder bed fusion companies. This is a challenging process as the printer must manage the precious powders while maintaining the aesthetic properties of the materials. 3D printing of precious metals is used for medical, jewelry, and electronics applications.
Metal 3D Printer Reviews
1. Sciaky EBAM 300 – Metal Filament 3D PrintingFor those needing to print very large 3D metal structures, the Sciaky EBAM 300 has the capabilities of offering up the size you need and is mostly used by the United States defense and aerospace industries. The EBAM 300 is Sciaky’s largest regularly available system that features a build size envelope that measures 228” wide x 48” deep x 48” high.
Sciaky is one of the fastest growing industrial 3D printer commercial companies. The EBAM 300 can create a 10-foot long titanium aircraft structure at a rate of fifteen pounds of metal per hour completely the project in 48 hours. In comparison, it would take forgings between 6 and 12 months to build what this 3D printer can create in two days.
The unique technology that Sciaky’s uses can melt a 3 mm thick titanium filament with a high power electron beam gun providing standard deposition rates that range from 7 to 20 pounds per hour. The EBAM 300 has a maximum work envelope of 19′ x 4′ x 4′ x 8’ which is one of the biggest build platforms of any metal 3d printer that is commercially available.
The EBAM 300 is also the only 3D printer available that produces a metal structure over ten feet long, and it is created to additively manufacture prototypes from high-quality metals like niobium, titanium, Inconel, Tantalum, and other alloys. It also gives a very high level of control over the material composition and geometry of its patented IRISS Closed-Loop Control Technology. It also includes huge savings on raw materials like precious metals with the large reduction of waste.
The EBAM 300 is a full-scale method of production for institution and corporations that need more than just prototypes created. This system can be used to improve, repair, and create next-generation end-use technology in the defense and aerospace industry as well as the metals and energy industries.
The EBAM 300 is truly the largest 3D printing system in the world that is fit for actual use in the commercial and industrial world and not just a mega-scale 3D printer that cannot be used commercially or is only available to a small group of individuals that has few real-life applications. The Sciaky EBAM 300 can actually be used for practical purposes to create functional metal parts.
2. Fabrisonic UAM – Ultrasonic Metal 3D PrintingUsing Ultrasound Additive Manufacturing Technology, or UAM, Fabrisonic creates 3D print large metal parts with machines that use three-axis CNC mills with an additional welding head for additive manufacturing. With a build volume of 6” x 6” x 3”, metal layers are cut first cut and then welded together with an ultrasound.
The UAM process uses ultrasonic welding to build up solid metal objects into a three-dimensional shape with a series of metal tapes. The process includes periodic machining operations that create a shape detail of the object. A transducer produces vibrations that are transferred to the disk-shaped welding horn that makes an ultrasonic solid-state weld between a base plate and the thin metal tape.
With a continual roll of the horn, the entire tape is welded to the plate with a series of layers welded together onto to create the height of the object. This repeated process occurs until the finished component is created with a final CNC contour milling used to is then used to accomplish the necessary surface finish and tolerances.
Ultrasonic welding gives Fabrisonic its solid-state bond that has been around since the 1960s. The welding process uses ultrasonic vibrations to generate motion similar to friction between two surfaces that are being held together with pressure which can cause plastic deformation and shearing that can cause contaminants and surface oxides to disperse. As the sharpness disappears, the contact between metal and metal is increased and forms a solid bond between the parts because of the heat and pressure.
Fabrisonic has been working on parts for defense contractors, aerospace companies, and a few other high-tech manufacturing companies. They are also anticipating growth and looking to expand in the future.
3. Concept Laser XLine 1000 – Powder Metal 3D PrintingWith a build volume of 630 x 400 x 500 mm, the Concept Laser XLine 1000 is the biggest powder metal 3D printer currently on the market. Similar in size to a single story house, the XLine 1000 is able to build parts that weigh up to 1000 kg and uses a 1,000-watt laser at the core of its system. This build envelope is able to build a standard V6 engine with additive manufacturing and can significantly increase productivity in comparison to other commercially available laser melting systems.
Not only can the X line 1000R increase construction rates, but it also can improve surface quality, system reliability, and higher reproducibility due to its process monitoring and its qualification for using a variety of projects with a wide range of powder materials. It works with a wide variety of metals like nickel-base alloy, stainless steel, cobalt-chromium alloy, hot work tool steels and precious metals like silver and gold alloys and reactive powder materials like aluminum and titanium alloys. The versatility of the XLine 1000 makes it a good choice for many industries like automotive, aeronautics and space, jewelry, and medical and dental.
Of the above industries, the automotive and aerospace industries will benefit the most from the use of lightweight aluminum alloys that replace expensive tool and die casting processes to build a highly ridged structure with weight-optimized geometries into lightweight structures.
As the capabilities of 3D printing hardware rapidly evolve, printers can now build huge components with great precision and fine resolution at faster speeds. As the technology improves, machines like the XLine 1000 can transform industries in new ways that can move the competition advantage to high volumes of low cost production.
Now, for those of you looking for a metal 3D printer that can sit on your desk, the Desktop Metal Studio isn’t quite small enough, but it is as close as you will get, plus it is a great addition to your workplace. This printer actually comes with a furnace and can print parts that can be ready in just one hub using a process called Microwave Enhanced Sintering. This is actually a pretty inexpensive printer when you consider its many capabilities and features that it offers, plus it can 3D print as fast as 16 cm3/hr.
The Desktop Studio is one of the most inexpensive and fastest metal 3D printing technologies that you can find on the market and is actually around ten times cheaper than its competitors. Instead of selectively using melt metal powder, the Studio 3D printer uses metal rod extruders in a way that is comparable to how a plastic FDM printer works. By eliminating the safety requirements that are normally used with metal 3D printing when you are opening alloys and using new features like closed-cell infill to create lightweight strength.
The Studio System is comparable to Metal Injection Molding (MIM) by using bulk sintering to accomplish densities that are higher than 98% and parts that are created that perform similarly to wrought alloys. The Desktop Metal Studio features a software controlled workflow that has every stage of the process managed and automated by software, plus a proprietary separable supports technology that makes it possible to take out parts by hand.
As the technology grows closer to allowing a metal 3D printer into our homes, the Desktop Studio will be one of the printers that helped us get there. It is only one step removed from at home capabilities and it shouldn’t be surprising if they have an at home model available in the next few years.
Revolutionizing 3D technology, Markforged has created Metal X for their metal printing field that can manufacture parts with incredible speed. It has incredible geometrical accuracy when it prints, and the parts it creates uses metals that can be used in the automobile, aerospace, and weapons industries.
The Metal X actually creates real metal parts with its full metal 3D printer out of powdered metal that hardens with massive heat and creates durable and lightweight materials. It has an extruder that creates the initial shape on a build plate that the material is bonded to in small furnace reduce the size of the object but it also has the ability to evaluate any shrinkage and automatically adjust the design as it works.
Using new technology called Atomic Diffusion Additive Manufacturing or ADAM., the Metal X gives you unique design features that include the capability to add honeycomb internal structures that lower the weight of the components. With a build volume of 200 mm x 200 mm x 250 mm and a 50-micron layer height, you can hardly tell the difference between the parts that are printed and those that are cast.
Metal X can print the following metals:
- Stainless Steel 17-4 and 303
- Aluminum (Beta) 6061 and 7075
- Tool Steel (Beta) A-2 and D-2
- IN Alloy (Inconel) 625 (Beta)
- Titanium Ti-6Al-4V (Beta)
Even though the price of this machine is incredibly high, it is one of those machines that is awesome to know is out there and helping to raise the bar for metal 3D printing.
On the smaller metal printer side is Shining 3D’s EP-M100T that is perfect for jewelry, dental applications, and education. It uses a 100 to 200 Watt laser that can process a very wide range of powders into a metal object. It uses the selective laser melting 3D printing technology (SLM) that selectively melts metal powder layers.
The Shining 3D EP-M100T has a practical and compact design and has the following features:
- A build chamber that is compact and perfect for printing small parts that can be used in the medical, dental, and jewelry industries.
- A laser with 100W/200W power
- Monitoring through remote control and smartphone
- Eplus 3D printing software
The Shining 3D EP-M100T 3D printer can use the following metals:
- Titanium alloy
- Aluminum alloy
- High strength steel
- Tungsten alloy
- Copper alloy
- Stainless steel
Using Selective Laser Melting technology, the Shining 3D EP-M100T selectively melts fine layers of metal powder directly from a 3D file. With its smaller build chamber, the EP-M100T is great for a lab environment where you need less power and less accessory equipment. And with its open system, the EP-M100T gives you limitless possibility for lab experiments.
With a practical and compact design, the EP-M100T gives you a touch screen with user-friendly controls and a remote control and diagnosis through a phone. There is also a multiple precaution system protecting both people and machine, plus an integrated design that makes maintenance and operation convenient.
The EP-M100T also features high property and high precision printing quality that uses an intelligent powder coating method, plus a quick scanning speed that guarantees a more efficient printing process. It also has a lean design that helps to guarantee a low-cost operation with a compact chamber design and tightness that reduces powder consumption.
The EP-M250 can be used an in a wide variety of applications including education, dental, and jewelry. It also uses a diverse amount of printing materials making it very useful for the workplace.
Notable for using a Kickstarter campaign to start its production, Aurora Labs S-Titanium Pro uses a wide variety of metallic powders. It uses a hybridization of different metal printing technologies including SLM, SLS, and DED making it very versatile so that you can apply its products to various industries.
After an intellectual property dispute, the initial Aurora Labs Kickstarter project fell through and they began development of a 3D printer that would be even faster. They also offer an affordable product for their class with the S-Titanium that features a 300W laser and allows you to print more metal materials than its competitors including:
- Stainless Steel 316
- Stainless Steel 420
- Inconel 625
- Inconel 718
- Hastelloy C276
- Stellite 1
- Stellite 6
- Stellite 21
- NiBSi + WC60%
Eventually, it has plans to include materials like:
- Titanium Grade 1
- Titanium Grade 2
- Titanium Grade 4
- Titanium Grade 6
- Titanium Grade 12
- Bronze, Brass
- Gold
- Silver
- Aluminium AlSi7Mg
- Aluminium AlSi10Mg
It is also compatible with some third-party metal powders as long as they follow their specific purity and size requirements. Each machine is basically three printers in one that can print in one of three modes:
- Selective laser sintering (SLS)
- Selective laser melting (SLM)
- Directed energy deposition (DED)
You can also do on the fly alloying in DED mode, as well as pseudo-alloying due to three independently controllable powder hoppers.
Aurora Labs has received a lot of interest and is in full production to keep producing their machines. With their incredible versatility and use of multiple metals, Aurora Labs S-Titanium Pros is a less expensive and popular model that is helping to take metal 3D printing to the next affordable level.
8. Xact Metal XM200In contrast to the other 3D metal printers, the Xact Metal XM200 uses a chamber that is flooded with Argon gas plus high power laser beams and powders on a conveyer belt to create objects. It has a little smaller build volume, but it is still an affordable metal 3D printer by a US-based manufacturer. The XM200’s beam has is consistently orthogonal across the entire surface of powder that helps it to consistently produce the right fusing properties throughout the entire build area.
Xact Metal XM200 features:
- Uses a 250 W fiber laser that builds layers that are as thin as 20-100 microns with a spot size greater than 10 microns that allow a high level of precision.
- Utilizes cloud connectivity for one or more 3D printers that provide remote monitoring of the entire 3D printing process.
- Easy access to the build area that allows for convenient cleaning and quick set up.
The Xact Metal is compatible with several metals including:
- Xact proprietary powder 316L
- Stainless Steel and the proprietary powders
- Inconel 718 Superalloy
- Titanium 6Al 4V
- Aluminum Si10Mg
- Maraging Steel
The Xact Metal utilizes a traditional and laser powder bed system that allows you to create elaborate metal prints. By using a laser, the printer can fire right onto the material while it is on the platform and it can then use a high-speed scanner while the powder shapes leading to a consistent power level across all the different areas.
The unique build chamber system is a little on the small side, but it is needed because of the controlled gas system that lets out all of the oxygen to fill up with argon instead. Depending on the type of company you work for, it may not fit with your model due to its small build volume, plus it requires a special power system that you may have to invest in.
9. M400 by EOSDesigned by German manufacturer EOS, the EOS M 400 is an industrial 3D printer that is based on the DMLS (Direct Metal Laser Sintering) 3D printing technology that was developed by EOS. This printing technique utilizes fiber lasers to melt and fuse fine metal powder creating a series of layers as the object is built. With this method, you can create 3D printed products using complex geometry elements like deep slots, freeform surfaces, and/or coolant ducts.
The EOS line of industrial metal 3D printers uses the following metals:
- Titanium
- Cobalt chrome alloys
- Aluminum
- High-grade steel
- Nickel
- Maraging steel
The EOS M 400 includes additive manufacturing system produces of high-quality large metal parts with a building volume of 400 x 400 x 400 mm. The EOS M 400 allows for the production of an industrial scale of large metal parts without any need for tools directly from CAD data. It includes the following features:
- High productivity with proven quality
- Due to 1kWlaser, it has increased productivity
- Reduces non-productive time by recoating both sides
- Reduces filter costs with a new recirculating filter system that has an automatic cleaning function
With a modular platform, the EOS M 400 contains a setup station and a process station, plus for future innovation, it facilitates easy integration. It also includes an extensive monitoring feature that takes quality management to the next level and sophisticated software that separates job preparation and calculation from the actual building process.
Improved usability makes the EOS M 400 very user-friendly as it supports the production of complex metal parts with its fast and easy touch screen operation with a broad material portfolio. EOS also offers a large number of metal materials to meet your individual requirements.
10. ALUNAR Metal 3D Printer Fully Assembled High Precision Auto-Leveling FDM Desktop 3D Printing MachineThe Alunar 3D printer allows you to discover a new hobby or take one you already have to the next level. With 3D printing, you are opening yourself up to tons of new possibilities, basically, if you can dream it, you can make it. With the Alunar 3D printer, you can customize and personalize items creating endless products for your business.
The Alunar 3D printer also allows you to foster new learning experiences through experimentation, and through problem solving and critical thinking, you can turn your dreams into actual sellable objects. With 3D printing you can print individual objects, parts for a larger project, or complex objects that move. You can even expand your creation by using other tools along with the Alunar 3D Printer to create multi-material projects.
The Alunar 3D Printer R200 is a small to medium sized high-performance printer that is affordable and accurate, plus it is easy to setup and use. Featuring a flexible and user friendly software system, the Alunar 3D printer is quick and convenient to install, plus you can get simple-combined and colorful printing by just changing out the filament while the printer is working. You can also outfit it with a small 0.4mm extruder to guarantee its accuracy and quality.
The Alunar 3D printer also features all metal frames that are easy to put together, plus it is not necessary to set up heating beds as the print is started right on the On Patent Print Plate with strong filament bonding. The Color Touch Screen Control makes it easy to control and operate while printing, plus it makes it expandable with more functions.
Other features include a support 1.75mm ABS/PLA filament, an Auto Install and Uninstall filament function, and a memory function allowing you to print from a stop point. This also means it is possible to print several colors since you can stop printing to replace the filament. Of all the metal 3D printers on this list, the Alunar 3D printer has the most possibilities for the average person and is worth checking out.
Metal Filament Reviews
1. 3D Solutech Silver Metal 1.75mm 3D Printer PLA Filament
Professional grade 3D printer filament by 3D Solutech can provide printed objects in various materials and colors. Each spool is hand checked and vacuumed seal to ensure high-quality levels, and the 3D Solutech PLA filament is consistent in its printing experience and in maintaining a smooth product.
You will find that 3D Solutech 3D Printer filament is always round and you won’t find any bubbles, residue, breaks, or kinks. Using their ultra-smooth technology, Solutech filaments are able to product smoothly and beautifully to create delicate objects. These filaments are also tested on various models of 3D printer to make sure consistent quality throughout the market.
Pros:
- Consistent and spooled well
- Good quality, prints smoothly
- Has a bit of shine to it
Cons:
- Has a tendency to jam
For a different look, Gizmo Dorks metal copper fill filament lets you make unique products with a metallic finish and look. With a unique mix of real copper powder with PLA filament, you will get prints that are similar to regular PLA, and it can be printed on build plates that are either heated or non-heated.
When using metal copper fill, make sure to consider heat migration as heat will move faster through filament than normal. Metal copper filled prints can also be post-processed by using coarse steel wool to polish your surface.
Pros:
- Good quality, great adhesion
- Great color, easy to print
- A lot brighter than other coppers
Cons:
- Not easy to polish
3. SainSmart Copper Metal 1.75mm Filament
If you are looking for vibrant color, the SainSmart 3D Printer Filament provides quality filament that will allow you to bring your ideas to life. This professional grade filament is good quality filament that is always round with no air bubbles, breaks, kinks, or oil residue.
SainSmart Copper Metal is used throughout eduction, building, electronics, health care, toys, automobile, and anime fields. It also works common 3D printers like FlashForge, MakerGear, Reprap, MakerBot, and Solidoodle.
Pros:
- Prints well, very consistent
- Good strength and rigidity
- Prints really well, good adhesion
Cons:
- Pretty brittle right off the spool
4. MeltInk3d Silver 1.75mm PLA 3D Printer Filament
Made with 100% raw materials. MeltInk3D is made with high-quality standards and all of their filaments are guaranteed to be 1.75mm in diameter. All filaments are vacuum packed to guarantee all of your printing projects will be of the highest quality.
Pros:
- Great color quality, metallic look
- Easy to print, high-quality results
- Nice flow and adhesion
Cons:
- Color is too dark for some people
A dense material that prints easily, the Proto-pasta SSP11701 makes heavy cast metal looking prints that can be sanded, brushed, or polished making it perfect for costumes, jewelry, props, and figurines. Proto-pasta does not require a heated bed, and it uses a direct-drive system with 0.4mm nozzles although a larger, wear resistant nozzle is suggested for more service intervals.
Pros:
- Nice heavy material
- Easy to print
- Sands down smooth with very little effort
Cons:
- Extruder doesn’t keep up very well
Final Thoughts
The last few years has seen amazing progress in the metal 3D printing industry. Each material has a unique set of properties that can suit a wide range of products including jewelry, medical and dental products, and prototypes. As the technology has developed, it has shown to be in some cases better than what is manufactured by traditional methods and keep in mind it is just getting started.
[mc4wp_form]
How metal 3D printers work. Overview of SLM and DMLS technologies. additive manufacturing. 3D metal printing.
Metal 3D printing. Additive technologies.
SLM or DMLS: what's the difference?
Hello everyone, Friends! 3DTool is with you!
BLT metal 3D printer catalog
Selective laser melting ( SLM ) and direct metal laser sintering ( DMLS ) are two additive manufacturing processes that belong to the family of 3D printing using the powder layer method. The two technologies have much in common: they both use a laser to selectively melt (or melt) metal powder particles, bonding them together and creating a pattern layer by layer. In addition, the materials used in both processes are metals in granular form.
The differences between SLM and DMLS come down to the basics of the particle bonding process: SLM uses metal powders with a single melting point and completely melts the particles, while in DMLS the powder consists of materials with variable melting points.
Specifically:
SLM produces single metal parts while DMLS produces metal alloy parts.
Both SLM and DMLS technologies are used in industry to create final engineering products. In this article, we will use the term "metal 3D printing" to summarize the 2 technologies. We will also describe the main mechanisms of the manufacturing process that are necessary for engineers to understand the advantages and disadvantages of these technologies.
There are other manufacturing processes for producing dense metal parts, such as electron beam melting (EBM) and ultrasonic additive manufacturing (UAM). Their availability and distribution is rather limited, so they will not be presented in this article.
How 3D printing with SLM or DMLS metal works.
How does metal 3D printing work? The basic manufacturing process for SLM and DMLS is very similar.
1. The printing chamber is first filled with an inert gas (such as argon) to minimize the oxidation of the metal powder. It then heats up to the optimum operating temperature.
2. A layer of powder is spread over the platform, a powerful laser makes passes along a predetermined path in the program, fusing the metal particles together and creating the next layer.
3. When the sintering process is completed, the platform moves down 1 layer. Next, another thin layer of metal powder is applied. The process is repeated until the entire model is printed.
When the printing process is completed, the metal powder already has strong bonds in the structure. Unlike the SLS process, parts are attached to the platform via support structures. The support in metal 3D printing is created from the same material as the base part. This condition is necessary to reduce deformations that may occur due to high processing temperatures.
When the 3D printer's chamber cools down to room temperature, excess powder is removed manually, such as with a brush. The parts are then typically heat treated while they are still attached to the platform. This is done to relieve any residual stresses. They can then be further processed. The removal of the part from the platform occurs by means of sawing.
Scheme of operation of a 3D printer for metal.
In SLM and DMLS, almost all process parameters are set by the manufacturer. The layer height used in metal 3D printing varies from 20 to 50 microns and depends on the properties of the metal powder (fluidity, particle size distribution, shape, etc.).
The basic size of the print area on metal 3D printers is 200 x 150 x 150 mm, but there are also larger sizes of the working area. Printing accuracy is from 50 - 100 microns. As of 2020, metal 3D printers start at $150,000. For example, our company offers 3D metal printers from BLT.
metal 3D printers can be used for small batch production, but the 3D printing capabilities of such systems are more like those of mass production on FDM or SLA machines.
The metal powder in SLM and DMLS is recyclable: typically less than 5% is consumed. After each impression, the unused powder is collected and sieved, and then topped up with fresh material to the level required for the next production.
Waste in metal printing, are supports (support structures, without which it will not be possible to achieve a successful result). With too much support on the manufactured parts, the cost of the entire production will increase accordingly.
Adhesion between coats.
3D metal printing on BLT 3D printers
SLM and DMLS metal parts have almost isotropic mechanical and thermal properties. They are hard and have very little internal porosity (less than 0.2% in 3D printed condition and virtually non-existent after processing).
Metal printed parts have higher strength and hardness and are often more flexible than traditionally made parts. However, such metal becomes “tired” faster.
3D model support structure and part orientation on the work platform.
Support structures are always required when printing with metal, due to the very high processing temperatures. They are usually built using a lattice pattern.
Supports in metal 3D printing perform 3 functions:
• They form the basis for creating the first layer of the part.
• They secure the part to the platform and prevent it from deforming.
• They act as a heat sink, removing heat from the model.
Parts are often oriented at an angle. However, this will increase the amount of support required, the printing time, and ultimately the overall cost.
Deformation can also be minimized with laser sintering templates. This strategy prevents the accumulation of residual stresses in any particular direction and adds a characteristic surface texture to the part.
Since the cost of metal printing is very high, software simulations are often used to predict how a part will behave during processing. These topology optimization algorithms are otherwise used not only to increase mechanical performance and create lightweight parts, but also to minimize the need for supports and the likelihood of part distortion.
Hollow sections and lightweight structures.
An example of printing on a BLT 3D printer
Unlike polymer powder melt processes such as SLS, large hollow sections are not typically used in metal printing as the support would be very difficult to remove, if at all possible.
For internal channels larger than Ø 8 mm, it is recommended to use diamond or teardrop cross-sections instead of round ones, as they do not require support. More detailed recommendations on the design of SLM and DMLS can be found in other articles on this topic.
As an alternative to hollow sections, parts can be made with sheath and cores, which in turn are machined using different laser power and pass speeds, resulting in different material properties. The use of sheath and cores is very useful when making parts with a large solid section, as it greatly reduces printing time and reduces the chance of warping.
The use of a lattice structure is a common strategy in metal 3D printing to reduce part weight. Topology optimization algorithms can also help design organic lightweight shapes.
Consumables for 3D metal printing.
SLM and DMLS technologies can produce parts from a wide range of metals and metal alloys, including aluminum, stainless steel, titanium, cobalt, chromium and inconel. These materials meet the needs of most industrial applications, from aerospace to medical applications. Precious metals such as gold, platinum, palladium and silver can also be processed, but their use is of a minor nature and is mainly limited to jewelry making.
The cost of metal powder is very high. For example, a kilogram of 316 stainless steel powder costs approximately $350-$450. For this reason, minimizing part volume and the need for supports is key to maintaining optimal manufacturing cost.
The main advantage of metal 3D printing is its compatibility with high-strength materials such as nickel or cobalt-chromium superalloys, which are very difficult to machine with traditional methods. Significant cost and time savings can be achieved by using metal 3D printing to create a near-clean shape part. Subsequently, such a part can be processed to a very high surface quality.
Metal post-processing.
Various post methods. treatments are used to improve the mechanical properties, accuracy and appearance of metal printed products.
Mandatory post-processing steps include the removal of loose powder and support structures, while heat treatment (heat annealing) is typically used to relieve residual stresses and improve the mechanical properties of the part.
CNC machining can be used for critical features (such as holes or threads). Sandblasting, plating, polishing, and micro-machining can improve the surface quality and fatigue strength of a metal printed part.
Advantages and disadvantages of metal 3D printing.
Pros:
1. Metal 3D printing can be used to make complex custom parts, with geometries that traditional manufacturing methods cannot provide.
2. Metal 3D printed parts can be optimized to increase their performance with minimal weight.
3. Metal 3D printed parts have excellent physical properties, metal 3D printers can print a wide range of metals and alloys. Includes difficult-to-machine materials and metal superalloys.
Cons:
1. Manufacturing costs associated with metal 3D printing are high. The cost of consumables is from $ 500 per 1 kg.
2. The size of the working area in metal 3D printers is limited.
Conclusions.
• Metal 3D printing is most suitable for complex, one-piece parts that are difficult or very expensive to manufacture using traditional methods, such as CNC.
• Reducing the need for building supports, will significantly reduce the cost of printing with metal.
• 3D printed metal parts have excellent mechanical properties and can be made from a wide range of engineering materials, including superalloys.
And that's all we have! We hope the article was useful to you.
Catalog of 3D printers for metal BLT
You can purchase metal 3d printers, as well as any other 3d printers and CNC machines, by contacting us:
• By email: [email protected]
• By phone: 8(800)775-86-69
• Or on our website: http://3dtool.ru
Also, don't forget to subscribe to our YouTube channel:
Subscribe to our groups in social networks:
In contact with
Metal 3D Printing - The Essential Guide
There is no hotter trend in 3D printing today than metal. We will talk about metal printing at home, how it is done on an industrial scale, about technologies, applications, printers, processes, prices and materials.
Metal 3D printing has grown in popularity over the past few years. And this is quite natural: each material offers a unique combination of practical and aesthetic qualities, can be suitable for a wide range of products, prototypes, miniatures, decorations, functional details and even kitchen utensils.
The reason metal 3D printing has become so popular is because the printed objects can be mass-produced. In fact, some of the printed parts are just as good (if not better) than those made with traditional methods.
In traditional production, working with plastic and metal can be quite wasteful - there is a lot of waste, a lot of excess material is used. When an aircraft manufacturer makes metal parts, up to 90% of the material is simply cut off. 3D printed metal parts require less energy and waste is reduced to a minimum. It is also important that the final 3D printed product is up to 60% lighter than a traditional part. Billions of dollars could be saved in the aviation industry alone—mainly through weight savings and fuel savings.
So, what do we need to know about metal 3D printing?
3D metal printing at home
If you want to make objects at home that will look like metal, it is best to pay attention to metalized PLA filaments (Photo: colorFabb)
where to start if you want to print metal objects at home? Given the extreme heat required for true metal 3D printing, a conventional FDM 3D printer will not be able to do this.It is unlikely that in this decade it will be possible to print with liquid metal at home. Until 2020, you probably will not have a printer specialized for this purpose at home. But in a few years, as nanotechnology advances, we may see significant developments in new applications. This can be 3D printed with conductive silver, which will emit in much the same way as it does in 2D home printers. It will even be possible to mix different materials like plastic and metal in one object.
Materials for metal 3D printing at home
Even though you can't print actual metal objects at home, you can turn to plastic filament that has metal powders added to it. ColorFabb, ProtoPasta and TreeD Filaments all offer interesting metal-PLA composite filaments. These filaments, containing a significant percentage of metal powders, remain pliable enough to be printed at low temperatures (200 to 300 Celsius) on virtually any 3D printer. At the same time, they contain enough metal to make the final object look, feel, and even weigh like metal. Iron-based filaments even rust under certain conditions.
But you can go further. Typically, up to 50 percent metal powder is added to 3D printing filament. Dutch company Formfutura says they have achieved 85 percent metal powder with 15 percent PLA. These filaments are called MetalFil Ancient Bronze and Metalfil Classic Copper. They can be printed even at "moderate" temperatures from 190 to 200 degrees Celsius.
Metallic 3D Printing Filament Spools, in this case from SteelFill and CopperFill colorFabb (Steel and Bronze), Ancient Bronze (Ancient Bronze) from Formfutura
Here are the key points about metal printing at home
- Gets a unique metal surface and look
- Ideal for jewelry, figurines, housewares, replicas
- Durability
- Objects are not flexible (structure dependent)
- Objects do not dissolve
- Not considered food safe
- Typical print temperature: 195 - 220°C
- Extremely low shrinkage on cooling
- No table heating required
- Printing complexity is high, requires fine tuning of nozzle temperature, feed rate, post-processing
Preparing your home printer for metal 3D printing
Since getting metal 3D prints is more difficult than usual, you may need to upgrade your 3D printer nozzle, especially if you are an entry-level printer. The metal filament wears it out quickly. There are hard-wearing hot-ends (like the E3D V6) that are themselves made of metal. They can withstand high temperatures and fit most printers. Be prepared for the fact that the nozzles will have to be changed frequently, because the metal filament is very abrasive.
You will also need to take care of the final finishing of the surface (cleaning, sanding, oiling, waxing or priming) so that the printed metal object shines as it should.
How much does metal filament for 3D printing cost?
And what about metal filament for 3D printing? - you ask. Here are a few examples:
- ColorFabb's 750 gram Bronzefill spool is $56.36
- ColorFabb 750g Copperfill Coil $56.36
- Protopasta's Polishable Stainless Steel PLA Composite is $56 for 56 grams of
- Protopasta's Rustable Magnetic Iron PLA Composite is $34.99 for 500 grams of
Industrial metal 3D printing
But what if you want a better result or even full metal 3D printing? Should a real "metal" 3D printer be purchased for business needs? We wouldn't recommend it - unless you're going to be doing it every day. A professional metal 3D printer is expensive: EOS or Stratasys devices will cost you 100-500 thousand dollars. In addition, the costs will be even greater, since you will have to hire an operator, a worker to maintain the machine, as well as to finalize the printouts (polishing, for example). Just a note: In 2016, an affordable metal 3D printer didn't exist.
Lowering Metal 3D Printing Costs
If you are not going to open a metal 3D printing business, but still need a professionally 3D printed metal part, it is better to contact the appropriate company that provides such services. 3D printing services like Shapeways, Sculpteo and iMaterialise offer direct metal printing.
They currently work with the following metal materials in 3D printing:
- aluminum
- steel
- brass
- copper
- bronze
- sterling silver
- gold
- platinum
- titanium
If you are a jeweler, you can also order wax models for casting in precious metals.
If we talk about wax models, then in most cases they (with subsequent melting) are used when printing with metals (including gold and silver). Not all orders are carried out directly by these firms. They usually turn to other metal 3D printing companies to complete the order. However, the number of such services around the world is growing rapidly. In addition, metal 3D printing techniques are becoming more and more common in companies that offer such services.
The reason 3D printing is so popular with large companies is that it can be used to build fully automated lines that produce "topologically optimized" parts. This means that it is possible to fine-tune the raw materials and make the components thicker only if they must withstand heavy loads. In general, the mass of parts is significantly reduced, while their structural integrity is preserved. And this is not the only advantage of this technology. In some cases, the product turns out to be significantly cheaper and affordable for almost everyone.
Please note that metal 3D printing requires special CAD software for modeling. It is worth paying attention to the recommendations of Shapeways - 3D printing metal guidelines. To delve further into the topic, check out Statasys’ information on related 3D printers and the nuances of metal 3D printing.
Here are some examples of Benchy test model prices for metal 3D printing:
- Metal plastic: $22.44 (former alumide, PLA with aluminium)
- Stainless steel: $83.75 (plated, polished)
- Bronze: $299.91 (solid, polished)
- Silver: $713.47 (solid, mirror polished)
- Gold: $87.75 (gold plated, polished)
- Gold: $12,540 (solid, 18K gold)
- Platinum: $27,314 (solid, polished)
As you might expect, solid metal 3D printing prices are quite high.
Metal 3D printing. Applications
GE LEAP aircraft engine parts 3D printed at Avio Aero (Photo: GE)
There are several industries already using 3D printers to make everyday objects - you may not even know that these objects are printed.
- The most common case is surgical and dental implants, which in this design are now considered the best option for patients. Reason: they can be tailored to individual needs.
- Another industry is jewelry. Here, most manufacturers have abandoned resin 3D printing and wax casting, switching directly to metal 3D printing.
- In addition, the aerospace industry is becoming more and more dependent on 3D printed metal objects. The Italian company Ge-AvioAero was the first to do all-metal 3D printing. It manufactures components for LEAP aircraft engines.
- Another industry targeting metal 3D printing is the automotive industry. BMW, Audi, FCA are seriously considering this technology, not only for prototyping (3D printing has been used for this for quite some time), but also for making real parts.
Before metal 3D printing really takes off, however, there are some hurdles to overcome. And first of all, this is a high price, which cannot be made lower than during molding. Another problem is the low production speed.
Metal 3D printing.
Technologies
Most metal 3D printing processes start with an “atomized” powder
You can talk a lot about “metal” 3D printers, but their main problems remain the same as any other 3D – printers: software and hardware limitations, material optimization and multimateriality. We won't talk too much about the software, we'll just say that most of the major specialized software companies, such as Autodesk, SolidWorks and solidThinking, try to emphasize as much as possible the fact that as a result of the 3D metal printing process, you can get any shape you want.
In general, printed metal parts can be as strong as parts made by traditional processes. Parts made using DMLS technology have mechanical properties equivalent to casting. In addition, the porosity of objects made on a good "metal" 3D printer can reach 99.5%. In fact, manufacturer Stratasys claims that 3D printed metal parts perform above industry standards when tested for density.
3D printed metal can have different resolutions. At the highest resolution, layer thickness is 0.0008 - 0.0012" and X/Y resolution is 0.012 - 0.016". The minimum hole diameter is 0.035 - 0.045". formed layer)
The metal 3D printing process used by most relevant large companies today is called Powder Bed Fusion. This name indicates that some source of energy (a laser or other energy beam) melts an "atomized" powder (i.e., a metal powder that is carefully ground into spherical particles), resulting in layers of a printed object.
There are eight major manufacturers of metal 3D printers in the world that already use this technology; while we are talking here, there are more and more such companies. Most of them are in Germany. Their technologies are called SLM (Selective Laser Melting - selective laser fusion) or DMLS (Direct Metal Laser Sintering - direct metal laser sintering).
Metal 3D printing No. 2:
binder Jetting (spraying the binder)
under 3DP-technology EXONE Metal objects are printed by binding the powder in the mountain : ExOne)
Another professional approach that also uses a powder base is called Binder Jetting. In this case, the layers are formed by gluing metal particles together and then sintering (or fusing) them in a high-temperature furnace, just like it is done with ceramics.
Another option, which is similar to working with ceramics, is mixing metal powder into metal paste. A pneumatically extruded 3D printer (similar to a syringe bioprinter or an inexpensive food printer) forms 3D objects. When the required shape is reached, the object is sent to the furnace, i. e. in the mountains
This approach is used in the Mini Metal Maker, apparently the only inexpensive "metal" 3D printer.
Metal 3D printing process #3: 9Metal Deposition This is not entirely true. Of course, on some desktop device, simply fusing metal threads onto the base will not work. However, very large steel companies can do it. And they do. There are two options for working with "metal surfacing".
One is called DED (Directed Energy Deposition) or Laser Cladding. Here, a laser beam is used to melt the metal powder, which is slowly released and solidifies as a layer, and the powder is fed using a robotic arm.
Normally the whole process takes place in a closed chamber, but the MX3D project used conventional 3D printing techniques to build a full-size bridge. Another option for metal fusion is called EBAM (Electron Beam Additive Manufacturing - additive electron beam technology), which is essentially soldering, in which a very powerful electron beam is used to melt 3 mm titanium wire, and the molten metal forms very large finished structures. As for this technology, its details are known so far only to the military.
Metal 3D printing. Metals
3D Printing Metal #1: Titanium
Pure titanium (Ti64 or TiAl4V) is one of the most commonly used metals for 3D printing and is definitely one of the most versatile, strong and lightweight. Titanium is used both in the melting process in a preformed layer and in the process of spraying a binder and is used mainly in the medical industry (for the manufacture of personal prostheses), as well as in the aerospace industry, automotive and machine tools (for the manufacture of parts and prototypes). But there is one problem. Titanium is very reactive and explodes easily in powder form. Therefore, it is necessary that titanium 3D printing takes place in a vacuum or in an argon environment.
3D printing metal #2: Stainless steel
Stainless steel is one of the cheapest 3D printing metals. At the same time, it is very durable and can be used in a wide range of manufacturing and even artistic and design applications. The type of steel alloy used also contains cobalt and nickel, is very difficult to break, and has a very high elasticity. Stainless steel is used almost exclusively in industry.
3D Printing Metal #3: Inconel
Inconel is a superalloy manufactured by Special Metals Corporation, its registered trademark. The alloy consists mainly of nickel and chromium and is very heat resistant. Therefore, it is used in the oil, chemical and aerospace (for black boxes) industries.
3D Printing Metal #4: Aluminum
Due to its lightness and versatility, aluminum is very popular in 3D printing. Aluminum alloys are commonly used.
3D Printing Metal #5: Cobalt Chrome
gap). It is most commonly used in the manufacture of turbines, dental and orthopedic implants, where 3D printing has become the dominant technology.
3D printing metal #5. Copper and bronze
With some exceptions, copper and bronze are used in wax melting processes, rarely in layer melting. The fact is that these metals are not very suitable for industry, they are more often used in the manufacture of works of art and crafts. ColorFabb offers both metals as the basis for a special metal filament.
3D printing metal #6. Iron
Iron, incl. magnetic, also mainly used as an additive to PLA-based filaments, which are produced, for example, by ProtoPasta and TreeD.
3D printing metal #7. Gold, Silver, and Other Precious Metals
Most preformed layer companies can 3D print precious metals such as gold, silver, and platinum. Here, along with the preservation of the aesthetic properties of materials, it is important to achieve optimization of work with expensive starting powder. Precious metal 3D printing is required for jewelry, medical applications and electronics.
Metal 3D printing. Printers
Do not even hesitate - the purchase of a metal 3D printer will not pass without a trace on your budget. It will cost at least 100-250 thousand dollars. Here is a list of a variety of "metal" printers, some of which can be found in firms providing 3D printing services.
Metal 3D Printer #1:
Sciaky EBAM 300 - metal filament printing
If you need to print really large metal structures, Sciaky's EBAM technology is your best bet. By order, the device can be built in almost any size. This technique is used mainly in the aerospace industry and the military.
Sciaky's largest production printer is the EBAM 300. It prints objects in a volume of 5791 x 1219 x 1219 mm.
The company claims the EBAM 300 is also one of the fastest industrial 3D printers on the market. A three-meter-sized titanium part for an aircraft is printed on it in 48 hours, while the material consumption is about 7 kg per hour. In general, forged parts that usually take 6-12 months to complete can be made in 2 days with this 3D printer.
The metal layers are first cut and then ultrasonically welded. The largest Fabrisonic 7200 printer operates in a volume of 2 x 2 x 1.5 m. The metal powder 3D printer is the Concept Laser XLine 1000. It has a modeling volume of 630 x 400 x 500 mm and is the size of a house.
Its German company, one of the main suppliers of 3D printers for aerospace giants like Airbus, recently introduced a new machine, the Xline 2000.
This machine uses two lasers and has a working volume of 800 x 400 x 500 mm. Uses LaserCUSING laser technology (a variant of selective laser fusion) from Concept Laser, which allows you to print alloys of steel, aluminum, nickel, titanium, precious metals and even some pure substances (titanium and stainless steel).
Metallic 3D printing. Services
There are more than 100 companies worldwide offering metal 3D printing services. We list the most popular services for consumer needs.
#1 Metal 3D Printing Service: Shapeways
The world's most popular 3D printing service, Shapeways offers two types of services. As a consumer, you can choose from a wide range of professionally designed objects, customize them, and then have them printed to your specifications. Like other 3D printing services, Shapeways offers a platform for designers to sell and print their work. Shapeways is also a good place for rapid prototyping: customers benefit from industrial-grade printers (EOS, 3D Systems) and personal technical support.
3D printing metals: aluminium, brass, bronze, gold, platinum, precious metal plating, silver, steel. There are also wax molds for jewelry purposes.
Metal 3D Printing Service #2: Sculpteo
Like Shapeways and i.materialise, Sculpteo is an online 3D printing service that allows anyone to upload 3D models and send them to fabrication in a wide range of materials . Like its competitors, Sculpteo provides a platform for hobbyists and professionals to showcase and sell their designs. The stable of Sculpteo printers includes highly professional machines from 3D Systems, EOS, Stratasys and ZCorp. Extensive technical documentation will help identify design flaws and select the right material for the project.
Metals for 3D printing: alumide (plastic with aluminum particles), brass, silver.
Metal 3D Printing Service #3: iMaterialise
Materialise is a company that works with industrial customers to prototyping 3D printed products. For casual users and designers, Materialize offers an online 3D printing service called i.materialise. As with Shapeways, this service allows anyone to upload their 3D designs and print them out. Once an object has been uploaded and successfully printed, a designer can list it for sale either in the gallery of the i.materalise online store or by embedding some code into their site.
3D printing metals: alumide (plastic with aluminum powder), brass, bronze, copper, gold, silver, steel, titanium.
Metal 3D Printing Service #4: 3D Hubs
Through 3D Hubs, you can search for individuals and companies that offer 3D printing services in your area, upload STL files (which are immediately evaluated for defects ) and contact service providers directly to get the job done.