3D printer types pros and cons
3D Printing Materials: The Pros and Cons of Each Type
When you purchase through links on our site, we may earn an affiliate commission. Here’s how it works.
When you buy a 3D printer, it comes with a sample roll of filament to use. But what do you use when this runs out? Find out in our guide to the different types of 3D printer filament available now for fused deposition modelling (FDM) 3D printers. We'll look at the pros and cons of each material as well as which types will work with your 3D printer.
Swipe to scroll horizontally
Type | Pros | Cons | Cost per kg |
ABS | Tough; Common; Non-toxic | High melting point; Unpleasant fumes | $20 to $50 |
PLA | Easy to print with; Biodegradable | Prints degrade over time; Rough texture | $20 to $50 |
PVA | Water soluble; Fairly easy to print | Expensive; Risk of toxic fumes | >$100 |
Nylon | Tough; Inexpensive | High temperature requirement | $18 |
HDPE | Easy to dissolve; Lightweight | High temperature requirement | $30 |
T-Glase/PETT | Food-safe; Glass-like look | Slow to print; Heated printing bed needed | $30 |
Wood Filament | Attractive wood-like look | Finicky to use; Requires sanding | $60 to $100 |
Metal Filament | Attractive metal-like finish | Finicky to use; Expensive | $75 to $120 |
Carbon Fiber Mix | Mimics carbon fiber's lightweight strength | Tough on extruders; Expensive | $50 to $120 |
Flexible Filament | Produces flexible prints | Requires tinkering with the printer | $50 to $120 |
Conductive Filament | Conducts electricity; Similar to PLA | Expensive; Still experimental | $70 (for a 100g reel) |
ABS
A print made with ABS filament by the M3D Micro printerWhat it is: Acrylonitrile butadiene styrene (ABS) is the same plastic used in Legos. It’s tough, nontoxic and retains color well. It's also easy to shape, but tough to break, as it melts and becomes pliable at about 220 degrees C (about 430 degrees Fahrenheit).
These properties make ABS very suitable for 3D printing. You do need a large heater to reach that 220 degrees C melting point, but ABS becomes soft and pliable when heated and then sets quickly. A printer with a heated print bed is also usually needed as ABS will stick to a hot print bed.
As anyone who has stepped on a Lego will tell you, ABS is tough. It’s also water- and chemical-resistant. ABS does produce a slightly unpleasant smell when heated, and the vapor can contain some nasty chemicals, so you'll need good ventilation. Because ABS is broken down by UV radiation, it isn't suitable for long-term outdoor use, as it loses its color and becomes brittle.
Pros: Tough, impact-resistant material; Nontoxic and water resistant
Cons: High melting point; Unpleasant fumes; Not suitable for outdoor use
Good for: Gears and moving or interlocking parts
Cost: $20 to $50 per kilogram
Compatible with: Printers with extruders that heat to 220 degrees C, such as the Ultimaker 3 and TAZ Mini
PLA
A print made in the tough PLA offered by MakerbotWhat it is: Polylactic acid (PLA) is a polymer plastic, made from biological materials like cornstarch or sugarcane. It is similar to the material used in biodegradable plastic packaging and melts at between 180 and 200 degrees C, depending on other materials that are added for color and texture. PLA is a tough, resilient material with a matte, opaque quality, but it is not as tolerant of heat as ABS is. PLA begins to deform at temperatures above 60 degrees C, and it is not water or chemical resistant. There is a slight smell when it is heated, rather like microwave popcorn, but no toxic odors or vapor.
PLA is generally the preferred option for low-cost 3D printers, because it is easier to print with than ABS, as it is stickier. It will stick well to aprint base covered in white glue or blue painter's tape, which means that a heated print bed is not needed. The material is also biodegradable; like other corn- or sugar-based materials, it is slowly consumed by many common bacteria. It will last a long time in normal conditions, though. It's only when buried that it breaks down. That said, PLA is not food safe and somewhat brittle, making prints prone to shattering under stress. However, chemicals can be added that make it less brittle and more heat-tolerant, creating what some manufacturers call tough PLA.
Pros: Easier to print with than ABS; Biodegradable
Cons: Prints degrade over time; Rougher texture than ABS
Good for: General printing, painted miniatures.
Cost: $20 to $50 per kg
Compatible with: All FDM 3D printers, including XYZ da Vinci Mini and LulzBot Mini.
PVA
A print made with ABS print material and PVA supports with the Ultimaker 3What is it: Polyvinyl alcohol (PVA) is one of a new class of 3D printing materials that are used to make supports that hold 3D prints in place. A synthetic polymer, PVA is water soluble. It melts at about 200 degrees C, and can release some nasty chemicals if heated to higher temperatures.
This is why PVA is used in 3D printing. It can be used in a standard 3D printer extruder to form parts that support other objects, and it sticks to a heated, glass print bed well. Once the printing is complete, you immerse it in water, and the PVA parts will dissolve, leaving the rest of the insoluble print behind. This makes it easier to print complex models that require supports, or even models that include moving parts. If you do use water to dissolve PVA, you'll need to properly dispose of it, as the sticky residue can clog drains. Check with your local water company for the recommended disposal method.
Pros: Water soluble; Good for supports; Fairly easy to print
Cons: Can release toxic vapors if overheated; Expensive; Requires appropriate disposal
Good for: printing complex models with PLA or ABS
Cost: More than $100 per kg
Compatible with: Standard FDM printers with multiple extruders, such as the Ultimaker 3
Nylon
Prints made with 680, a nylon printer filament from TaulmanWhat it is: The name nylon can be used for any one of a number of synthetic polymers originally created as replacements for silks. Nylon is a tough material that has a very high tensile strength, meaning that it can hold a lot of weight without breaking. It melts at about 250 degrees C and is nontoxic.
Nylon's use as relatively a 3D printing material is relatively new, but the material is becoming popular because the prints it produces are very tough and resistant to damage. It is cheap, because nylon is widely used in other industries, and it's not damaged by most common chemicals. However, nylon does require high temperatures to print: 250 degrees C is hotter than many extruders can manage. And it is harder to get it to stick to the print bed than with ABS or PLA. Generally, nylon requires both a heated print bed and white glue to stick while printing.
Pros: Tough; Inexpensive printing material
Cons: Requires high temperatures to print
Good for: Utensils that touch food, plant pots that fill with water
Cost: $18 per kg
Compatible with: FDM printers that can heat the extruder to 250 degrees C, such as the Ultimaker 3 or TAZ 6
HDPE
A print made in HDPE with the LulzBot TAZ 5What it is: High-density polyethylene (HDPE, though it's also known as high-impact polystyrene, or HIPS) is used in pipes and recyclable packaging such as plastic bottles and packages (ones with the recycling ID code 2). It is a light, flexible material that sticks to itself and other materials well. HDPE is also easy to dye and mold. It melts at about 230 degrees C, but releases unpleasant fumes if accidentally heated to higher temperatures.
In 3D printing, HDPE is often used instead of ABS, as comparable prints turn out lighter and stronger than ones with ABS. HDPE does require higher temperatures to print, though, and can release unpleasant fumes if the temperature is set too high. It is resistant to most chemicals, though you can dissolve HDPE with limonene, a solvent commonly used in industrial cleaners. HDPE does have a tendency to warp: as it cools, HDPE contracts slightly, which can lead to warped prints.
Solubility in limoleme means that HDPE can also be used for printing supports for 3D prints made with other materials. After the printing is complete, the supports can be dissolved by immersing the print in limonene, which won't affect materials such as ABS or PLA. HDPE does require an extruder that can reach 230 degrees C, though, and a heated print bed.
Pros: Easily dissolved in limonene, a common solvent; Lightweight
Cons: Requires high temperatures for printing
Good for: Lightweight prints, supports for ABS prints
Cost: $30 per kg
Compatible with: Any printer that can handle ABS
T-Glase/PETT
(Image credit: A print made in t-glase material (Credit: Thingverse.com))What it is: Polyethylene terephthalate (PETT) is the chemical name of a material sold as t-glase. It is similar to polyester, often used to make clothes. It melts at about 230 degrees C, but cools into a rigid solid that resembles glass. It can be dyed while still retaining its glass-like qualities, so it is available in multiple colors. T-glase is approved for food use by the FDA, so you can use it to make dishes, cups and the like.
For 3D printing, t-glase can be printed onto a print bed heated to about 70 degrees C. It is mainly sold by Taulman, which introduced the material. While t-glase itself is strong and resilient, it has to be printed rather slowly to make sure that layers adhere properly. So printing with t-glase is typically much slower than with other materials.
Pros: Food-safe; Clear material with glass-like look
Cons: Requires heated print bed; Slow to print
Good for: Utensils, cups and others that touch food.
Cost: $30 per kg
Compatible with: FDM printers with high-temperature extruders and heated print beds, such as Ultimaker 3 and TAZ 6
Wood Filament
(Image credit: An iPhone case that was 3D printed in Woodfill filament (Credit: Thingverse.com))What it is: These filaments are not made out of wood, but instead contain very fine wood particles combined with PLA and a polymer that binds them together. When printed and polished, the finished material can look a lot like wood. Versions are available for many different types of wood, from bamboo to ebony and mahogany. Some of these filaments allow you to change the color of the printed material by varying the temperature; at higher temperatures, the wood particles take on a darker, burned look.
These materials are printed in the same way as PLA filaments, with similar extruder temperatures and the addition of white glue to help the print stick to the print bed. The addition of the wood particles does make the process more prone to problems, though, and each different filament will require a lot of experimentation for successful prints. The material also requires extra finishing, such as sanding or mild abrasive treatment, to bring out the wood look.
Pros: Attractive, wood-like finish
Cons: Finicky to print with; Often requires sanding or other treatments to get the final desired look
Good for: Sculptures or faux-wood carvings
Cost: $60 to $100 per kg
Compatible with: Any PLA printer, but experimentation with settings will be required
Metal Filament
(Image credit: A polished print made in Brassfill filament (Credit: MatterHackers.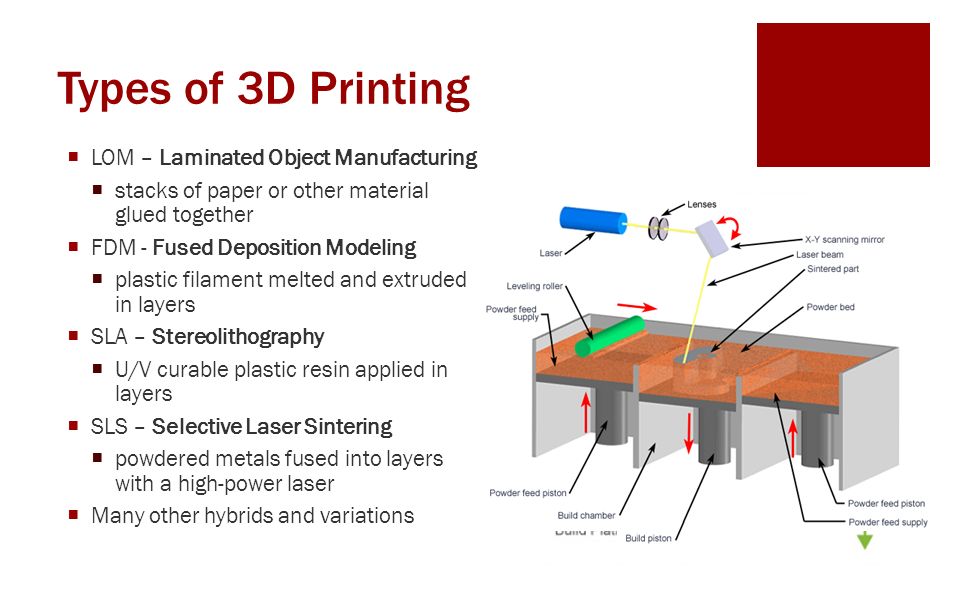
What it is: Metal filaments are made of very finely ground metals combined with PLA and a polymer glue. This means that they print like PLA, but have the look and feel of metals when you polish the final print. They work on any standard printer that supports PLA filament.
Available versions include steel, brass, bronze and copper particles to create the look and feel of those respective metals. The addition of the metal does change how they print, though, so experimentation is required to find the right settings on your 3D printer. These filaments also require sanding or polishing to create the metallic look. Right off the printer, they generally look like ceramics, but brushing with steel wool ora metal polish will expose the metal particles to create the metal look.
Metal filaments are not as heavy as solid metal, so a print of a statue with a bronze filament will not weigh as much as a cast bronze version. Also, since the particles of metal are bound by the PLA and glue, these filaments won't conduct electricity.
Pros: Attractive metal finish.
Cons: Requires experimentation to find correct print settings; Expensive
Good for: Metal sculptures, figurines
Cost: $75 to $120 per kg
Compatible with: Any PLA printer, but experimentation with settings will be required
Carbon Fiber Mix
(Image credit: An RC car whose nonelectronic parts were printed with carbon fiber filament (Credit: ColorFabb.com))What it is: Carbon fiber filaments — like this one from MatterHackers that uses nylon, or this one from Proto-pasta that uses PLA— combine carbon fiber and the filament material to give you some of the advantages of this new material: rigidity, strength and very low weight. However, this should be used with caution. Carbon fiber is a very abrasive material that can wear away the hot end of the extruder very quickly, so you'll need to get a reinforced extruder or replace it after a few prints.
There is one company that is making true carbon fiber 3D printers: MarkForged. Its Mark Two, Onyx and Mark X printers can print using the company's own pure carbon fiber filament. But those printers aren't cheap; the Mark Two will cost you a cool $13,499, while the carbon fiber filament it uses costs $149 a reel.
Pros: Has some of the lightweight strength of carbon fiber
Cons: Can damage some extruders; Expensive
Good for: Structural prints that need to be strong and lightweight.
Cost: $50 to $120 per kg
Compatible with: Any FDM printer with a replaceable extruder
Flexible Filament
(Image credit: A 3D printed watch strap that uses flexible material (Credit: YouImagine.com))What it is: Most 3D printing materials strive for rigidity, creating prints that are strong. That's not always what you need, though, and flexible filaments like NinjaFlex, PolyFlex or TrueFlex produce rubber-like prints that can be used to make things like phone covers, flexible joints and wearable prints.
However, this flexibility also poses a problem. FDM 3D printers work by pushing the filament into the heated extruder, where it melts. You can't do that as easily if the material is flexible: it would just block up the print head. So most printers will require modification to use these flexible filaments. 3D printer maker LulzBot, for instance, offers a replacement print head, called the Flexystruder, that's designed to handle flexible filaments
Other manufacturers offer what they call semiflexible filaments, like MakerBots Flexible Filament or the new TPU95 A from Ultimaker. These aren't as rubber-like as the ones above, but they still provide some flexibility; for instance, the MakerBot filament becomes flexible when you put it in hot water, allowing you to reshape or squish a print into a tight-fitting spot before the material cools and becomes rigid again.
Pros: Produces squishy, flexible prints
Cons: Requires modification of the printer or extruder
Good for: Wearable prints, phone covers, toys
Cost: $50 to $120 per kg, plus the cost of a modified extruder
Compatible with: Any FDM printer with a replaceable extruder
Conductive Filament
(Image credit: A print using conductive filament. (Credit: Thingiverse))What it is: New on the market are conductive filaments from companies like Proto Pasta or BlackMagic 3D that combine PLA with graphene, a form of carbon that conducts electricity. This means that you can print electric circuits directly without needing to add wires. This can be great for things like touch buttons, wearable electronics or styluses that conduct electricity.
These materials do require care when printing, as the layers of the print don’t stick to each other as well as normal PLA. The prints also tend to be brittle, and bending them can break the conductive graphene part so that they no longer conduct electricity. They are best used alongside normal PLA filament. Generally, you would print a PLA case around the parts that conduct electricity to protect it and give it more strength.
Conductive filaments are also not cheap. You’ll typically pay about $70 for a small 100g reel of this experimental new filament.
Pros: Conducts electricity; Prints like PLA
Cons: Expensive; Still very experimental
Good for: 3D printing electrical devices
Cost: $70 for a small 100g reel
Compatible with: Most printers that support PLA
- Best 3D Printers
- 3D Printing Gets More Colorful with Da Vinci Color
- Best All-in-One Printers
Get instant access to breaking news, the hottest reviews, great deals and helpful tips.
Richard Baguley has been working as a technology writer and journalist since 1993. As well as contributing to Tom's Guide, he writes for Cnet, T3, Wired and many other publications.
Topics
Gadgets
What are the types of 3D printing and which is right for me? — RDM Innovation
Have you ever considered creating a prototype with a 3D printer? You may want to consider the different types of 3D printers that are out there! Knowing which printer to use requires knowledge on the proper material to 3D print with. In product design, deciding if the parts need to be stiff or durable, flexible or rigid, or even production quantity and part cost all have a factor in deciding how to 3D print a product design. We’ve grown from the traditional DIY Makerbots to SLA printers and SLS printers. We see so many applications of parts and product designs with clients that need prototypes, ranging from medical instrumentation to consumer applications, so we have a wide range of experience. This article will hopefully help you decide on the method of 3D printing you decide to choose. To make it easy, here’s RDM’s list of the Pros and Cons of the three main types:
a. FDM Pros: Fast, low cost, wide range of materials
b. FDM Cons: Low resolution, prone to breaking, requires support and wasted material
c. FDM Best Use: economical proof-of-concept models and large parts (by volume)
A popular choice for Proof-of-Concept prototypes, FDM printing yields lightweight and durable parts. While, limited to select materials like ABS, which is not as accurate as its SLS and SLA counterparts, FDM is a perfect match for those seeking a fast and economical solution.
a. SLA Pros: High accuracy, high resolution, durable parts
b. SLA Cons: More expensive, limited materials, requires support
c. SLA Best Use: functional prototypes, molding**
If your components require high accuracy and excellent surface finish, SLA is a great solution. With a wide range of engineering-grade materials, the design remains unconstrained. These 3d printers and parts from SLA machines are perfect for proof-of-concept prototypes and pitch presentations/investor meetingsThe superior quality of the SLA parts comes at a higher price and typically cost more than the other 3D printing styles. Additionally, SLA 3d print times are long which will limit throughput at scale.
**molding — some engineering resins are made with inhibiting agents to plastics that are often desirable molding materials (platinum cure silicone, RTV/RTX Silicone, polyurethane, etc). Please be sure to research and perform testing before moving molds into production that were made on a SLA 3D printer.
a. SLS Pros: High accuracy, medium surface finish, no supports required, high through-put
b. SLS Cons: Not possible for smooth surface finish without post processing, limited materials
c. SLS Best Use: functional prototypes, production manufacturing
SLS is best suited for printing strong, functional models, which have a sandy surface finish and do not have a smooth surface like injection molded parts. This method is limited to engineering thermoplastics, specifically Nylon, and requires post-processing to achieve the desired surface finish. This post-processing is typically a combination of clearing unfused material from the build platform as well as a final bake in an oven if the model of SLS 3D printer that you are using requires it. If you are looking for high-strength, industrial-grade models, SLS is the recommended 3D printing method.
By leveraging advanced 3D printing technologies, RDM offers fast parts and prototyping with a wide selection of materials and dimensional accuracy to accommodate your needs. We use 3D models provided by you or created by us, we create built and finished parts with rapid turn-around time. In-house finishing processes seal and texture production-ready prototypes. 3D printing is an area of expertise that RDM has a great deal of experience in. If you’re looking to 3D print a prototype of your own, feel free to reach out to RDM on our “Contact Us” page to see how we can help you make your idea come to life!
3D printers advantages and disadvantages
If you ask any owner of a 3D printer what the main advantage of his device is, he will begin to talk about the high quality of printing and the ability to make any prototypes. When asked about the shortcomings, the answer is usually about some shortcomings in the design of the printer: someone is not satisfied with an insufficiently rigid frame, some complain about too slow printing rates. In the article, we understand what advantages most 3D printers have and find out what disadvantages their owners have to face. nine0003
Despite a relatively slow start, additive technologies are finally gaining momentum. Now 3D printers have gained well-deserved popularity both in the user environment and in the field of production. We have already appreciated the many benefits of 3D printing, including the ability to print complex models, but the peak of popularity and functionality of 3D technologies is yet to come. We talk about the main advantages and disadvantages of 3D printers.
Benefits of 3D printers
Let's start with the benefits: 3D printing allows you to quickly and relatively inexpensively produce the desired prototypes with high accuracy, independently adjusting the printer settings and choosing the optimal parameters. Let's dwell on each plus of 3D printers in more detail.
The advantage is the speed of production
3D printers can significantly reduce the time spent on each project. Unlike traditional manufacturing methods, when using additive technologies, the entire printing process will take from several weeks or days, and the bulk of the models can be printed in a matter of hours. Some manufacturers have decided to optimize their inventory by starting to make parts to order. This approach allows you to take mass production to a new level: now you do not need to store a lot of parts in stock, because you can simply print them as needed, immediately sending them to sale. nine0003
Advantage - cost of production
Large-scale projects with a large number of 3D printed parts are not cheap, but additive manufacturing still remains more profitable than traditional technologies. Many manufacturers use 3D printing for short runs or prototyping. For example, it is much more profitable for jewelers to print wax prototypes of jewelry than to cast them from metal. The plastic used in 3D printing is relatively inexpensive, and even the simplest printer can help save money. nine0003
Product quality
Modern 3D printers demonstrate high product quality. In our opinion, the quality depends on the following characteristics of the device:
- Photopolymer printing. This technology allows you to get the highest possible quality of the finished product.
- FDM technology. Despite the fact that FDM printers are in demand, they simply cannot create detail above 100 microns.
- Metal housing. When choosing FDM printers, you should give preference to models whose body is made of metal. Such printers demonstrate the best quality of products at high print speeds. nine0032
- Regardless of which printer model is chosen, the finished product printed at low speed and quality materials is almost the same as that produced on high speed equipment.
Thus, it is possible to achieve decent print quality on inexpensive printers using high-quality filament at low speeds.
Copy Accuracy
3D Printing Accuracy is the minimum layer height allowed. Modern devices can produce high quality down to 20 microns, but in order to actually obtain prototypes of such accuracy, the user will need to meet certain conditions. nine0003
First of all, the accuracy of the finished copies depends on the 3D printer itself - on its technical characteristics, layout, etc. You should not rely only on the layer height value that is indicated in the device description.
The accuracy of prototypes depends on many factors. For example, printers made in a closed case are able to produce much better model accuracy than their counterparts in an open case, due to the uniform temperature regime inside the printer. nine0003
In addition, it is required to correctly set all print settings, monitor the calibration of the table, the operating conditions of the device, and the temperature regime. High-quality plastic plays an important role in the accuracy of the copies made.
Production flexibility
The introduction of 3D printing in various areas of production is due to the fact that the technology makes it possible to create geometric shapes of almost any size and unlimited complexity.
Printers print with a wide variety of materials, making the production process as flexible as possible. For example, on the same device, you can create both waxes for jewelers and dentures for dentists. Such versatility cannot be achieved using standard production equipment. 3D printers open up new horizons and prospects for the development of their own business and additive technologies for engineers, designers and device owners.
Availability
The availability of 3D printing makes it possible to experiment using printers both at home and at work. Even the most inexpensive 3D printer can be used in architecture, construction, small-scale production, medicine, education, jewelry, printing, souvenirs, and advertising. A standard spool of filament will last for a long time, and almost everyone can afford to buy a 3D printer. One of the most budget models costs about $100. nine0003
Any technique has its downsides, and 3D printers are no exception. Therefore, today additive technology has a certain number of significant drawbacks.
Minus - the small size of the camera
Perhaps the most significant drawback of printers are the small size of the print area. Look at any 3D printer, evaluate its dimensions - that's it, everything is limited to them. The device can only print the model that will fit on its platform. If you need to create a larger prototype, you will have to resort to various tricks: for example, you can print the model in parts, and then assemble them in some way. Despite the fact that there is already a prototype of a 3D printer with an unlimited size of the working platform, it is not yet possible to talk about the mass introduction of such a technology. nine0003
Minus - inaccuracies of the part
It is impossible to completely get rid of thermal contraction or shrinkage of the finished model. This is a physical process - you can only compensate for it. The layers floated, the vertical is not observed, the layers do not lie exactly on top of each other. The protrusions on the top layer of the part can be either open or closed. Essentially, this is due to the sagging of the plastic, which does not have time to cool when printed in the air without supports. nine0003
Disadvantage - post-processing
Most finished products printed on a 3D printer require post-processing and cleaning. The process helps to achieve the best look and smoothness of the model. Finished models are processed in various ways. Users grind parts, chemically process them, cut supports, dry products. The need for post-treatment depends on many factors. For example, the scope of work varies depending on the size of the model, the material, the type of technology chosen in the manufacture of the prototype. Thus, given that 3D printing allows fast production of parts, the speed of production can be reduced through subsequent post-processing. nine0003
Strength properties of models
As a rule, the production of a three-dimensional model using additive technologies occurs by layer-by-layer application of a filament. Despite the fact that the layers are well glued together, this is not a guarantee of the perfect solidity of the finished product, and it can delaminate under certain loads. This problem is especially common when using FDM printers. Experienced users advise using injection molding to improve the strength properties of parts. Using this method, the structure of the finished part is more uniform and less brittle. nine0003
3D printers are not user-friendly
Manufacturers claim that 3D printers are easy to use. Some companies produce devices specifically for beginners. However, even for the initial assembly and preparation of the printer for operation, the user will need certain skills. Calibrating the desktop on your own, setting up the slicer program, and setting the desired print settings is not as easy as the manufacturers assure. Some models are delivered already assembled - we advise you to choose them as your first printer. nine0003
Harmful emissions
The size of the device and the amount of thermoplastic produced by the printer greatly affect the amount of harmful aerosol emissions into the atmosphere. The chemicals settle in our lungs and also contribute to the increase in the size of the ozone hole. A team of researchers led by Professor Brent Stevens conducted their own experiment, which tested five models of 3D printers. As a result, scientists were able to calculate the concentration of nanometer particles that are formed during the 3D printing process. nine0003
The results of the experiment did not please either printer manufacturers or device owners and users. The fact is that 3D printers using polylactic acid (PLA) in printing have demonstrated extremely high levels of ultrafine particles - from 20 billion per minute. Acrylonitrile butadiene styrene (ABS)-powered gadgets emit up to 200 billion particles per minute into the atmosphere.
Scientists have stated that harmful emissions in such quantities are similar to emissions into the atmosphere from burning tobacco or scented candles, burning natural gas. In addition, when using a laser printer using powder as a printing material, no less harmful emissions are produced. nine0003
Slow
3D printers are actually very slow. Some manufacturers claim high print speeds, but this figure is relative. Especially when it comes to making a lot of prototypes. Many users who own budget printers leave them running all night to have a small finished model by morning. Depending on the dimensions and quality of the printed product, the process may be delayed. On average, the process of creating a model can take from several hours to several days. The duration is directly proportional to the size of the object: the larger the future prototype, the more time it will take to print. nine0003
Environmental pollution
Waste plastic by-products of additive printing have long been of interest to conservationists. Production waste ends up in landfills, creating a negative additional burden on the environment. Scientists believe that the ABS plastic used in most 3D printers is quite toxic. This type of filament has a long period of decomposition in the soil. However, ABS is the most common type of material used in additive printing. PLA is a greener alternative to ABS. This material is more biodegradable and less toxic. The problem of environmental pollution can be solved with the spread of household plastic convertors into 3D printing filament. nine0003
Three-dimensional printers open up a wide range of possibilities for their owners. The list of advantages of such devices is endless, but we have chosen only the main ones. In our opinion, one of the main advantages of 3D printers is their affordability. Finished models are of sufficient quality even on budget models. The main thing is that the user sets the correct settings and fills the printer with good material.
But 3D printers also have their drawbacks. In addition to the fact that they are not very easy to calibrate and prepare for work, they produce harmful emissions into the atmosphere, and production waste in the form of plastic practically does not decompose, polluting the environment. Another disadvantage of the devices is the low print speed. However, 3D printing is too useful to pass up. In our opinion, printers are being improved every year, and very soon their shortcomings will be minimized. nine0003
- May 18, 2020
- 17526
Get expert advice
Advantages and disadvantages of 3D printers — GeograFishka.ru
3D printing, also known as additive manufacturing, is becoming more and more popular among manufacturers. Demand for it is growing due to some of the revolutionary benefits it has to offer. However, like almost any technology, it also has disadvantages that need to be considered. nine0003
This article is designed to help you make the right choice. We will look at all the advantages and disadvantages of 3D printers.
Do not know where to buy Russian-made 3D printers? On the site https://magnum3d.ru you can not only place an order for the purchase of Magnum 3D printers, but also buy spare parts and accessories.
What are the benefits of 3D printing?
This manufacturing process has several advantages over traditional manufacturing methods.
1. Flexible design capability
3D printers can be used to design and print more complex designs than traditional manufacturing methods. More traditional methods have design limitations that do not apply to 3D printing.
2. Rapid Prototyping
3D printers can produce parts in hours, which speeds up the prototyping process. As a result, each step can be completed faster. Compared to machine prototyping, 3D printing is cheaper and faster to produce parts because a part can be made in a matter of hours. nine0003
3. Print-on-demand
Print-on-demand is another advantage because, unlike traditional production methods, it does not require a large storage space. This saves space and money as there is no need to print large runs when they are not needed.
All 3D design files are stored in the virtual library as they are printed along with the 3D model as CAD or STL files, which means they can be found and printed if needed. Design changes can be made very economically by editing individual files. nine0003
4. Strong and lightweight parts
The main material used for 3D printing is plastic, although some metals can also be used. However, plastics have advantages because they are lighter than their metal counterparts. This is especially important in industries such as automotive and aerospace, where light weight is important and can lead to better fuel efficiency.
In addition, parts can be made from special materials to achieve certain properties such as heat resistance, increased strength or water repellency. nine0003
5. Rapid design and production
Depending on the design and complexity of the part, an item can be 3D printed in a few hours, which is much faster than cast or machined parts. 3D printing not only saves time in the manufacture of individual elements, but also speeds up the design process by creating STL or CAD files, which can then be printed.
6. Waste minimization
Only the materials needed to make the model itself are required to produce a part. Compared to alternative methods for cutting large parts from non-recyclable materials, there is virtually no waste. This process not only saves resources, but also reduces the cost of the materials used.
What are the disadvantages of 3D printing?
Like almost any other process, 3D printer technology has disadvantages that must be considered.
1. Limited materials
Although 3D printing can be used to create products from a variety of plastics and metals, the range of raw materials available is not comprehensive. This is because not all metals and plastics can be thermally affected in 3D printing. In addition, many of these printed materials are not recyclable and some are not food safe.
2. Limited size
3D printers currently have small print chambers that limit the size of parts. Anything larger must be printed in separate parts and assembled after production. This can increase the cost and time required to produce large parts because the printer has to print more parts before they can be assembled by hand.
3. Post Processing
Most 3D printed parts require some form of cleaning to remove the backing and smooth the surface to achieve the desired finish. Finishing methods include waterjet, sanding, chemical soaking and washing, air or heat drying, assembly, and others. The amount of post-processing required depends on factors such as the size of the part being manufactured, the intended use, and the type of 3D printing technology used for manufacturing.