3D printer cooling fan duct
Fan Duct best STL files for 3D printing・Cults
Bl-touch support for ADKS - ENDER 3 FAN DUCT V3
Free
BXN 3D Perf - Quiet Dual 5015 & 40x20 Without Direct-Drive
Free
double barrel duct
Free
CR-10 Circular Fan Duct for OEM fan
Free
Anet A6 circular fan duct
Free
Anycubic Mega Direct Extruder (TITAN)
Free
Adjustable fan duct
Free
E3D Style Bowden Super Cooling Adapter for 30mm to 50mm Fan!
Free
Ender 4 Magnetic 5015 Fan Duct
Free
Ender 4 Magnetic 40 mm Fan Duct
Free
mount & fan e3d V6 official or clone
Free
Rear Mount Bracket for Eyetecs Fan
Free
Titan extruder - dual fan ducts
Free
CTC - Lateral Fan Duct (for radial fan)
Free
Ender 3 Fan Cover (Hot Rod Edition) | now with power supply mount
Free
Ender 3 Easy Fans Optimizer
€0. 99
Duplicator D9 fan duct II
Free
Customizable ventilation grid
Free
Anycubic Chiron Extruder fan duct cooler
Free
Lightweight CR10 exruder fan holder
Free
Red Squirrel Compact Fan Housing - Ender 3 Pro - 5015 Rev1
Free
Hatchbox Alpha Blower Fan Mount
Free
Improved Anet A8 Center Nozzle Fan Duct
Free
Tronxy X5S Cooling Fan Duct for standard Printhead Carriage
Free
Wanhao Duplicator I3 Plus enclosure kit
Free
40/60mm fan duct/velocity stack (hero me compatible)
Free
Fan duct v1 for FPGE
Free
Prusa MK3s upgrade fan duct
Free
Cocoon Create Touch / Wanhao i3 plus reverse fan duct
Free
Dual fan duct for FlashForge Adventurer 3
Free
Prusa Mk3 fan duct (Includes double mount adaptor)
Free
Streamliner i3 Fan duct: Low profile, lightweight, effective cooling fan duct.
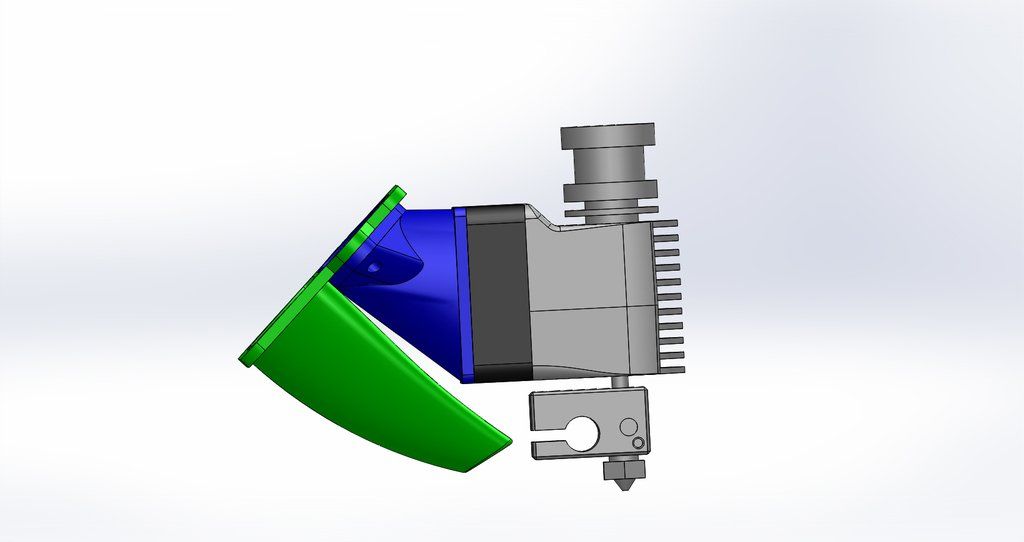
Free
Fluval Flex Aquarium Cooling Fan 40mm
Free
Semi-circular Fan Duct Anet A6
Free
Airodactylus -an Ender 3 fan duct
Free
Mecreator2 Fan duct - Bauteilkühler V4
Free
Tronxy X5S Cooling Fan Duct for standard Printhead Carriage
Free
tronxy x5sa fan duct
€0.50
Formbot Raptor V1 fan duct
Free
40 mm fan duct
Free
Arctic F12 fan funnel
Free
E3D V6 X Carriage Mount W/ 2XDuct Fans
Free
IKEA Lack Enclosure Anet A6 cooling duct assembly
Free
Creality hotend cooling and replaceable duct
Free
Quad fan ducted
Free
Mk2 to Mk3 Nozzle Fan Adapter
Free
Cobra Cooler Plus Rear mount remix for the Maker Select Plus
Free
Craftbot Fan adapter for Barts hotend upgrade
Free
A (nearly) comprehensive study of cooling fans and ducts : 3Dprinting
Motivation
I melted my DiiiCooler again. I was printing ABS, which most would say requires little to no cooling. My DiiiCooler was PETG, but after a few hours it started to sag and caught on the print. I should have taken it off or replaced it with something more resilient before I started, but such is life.
I started researching alternatives and found this great study on the effectiveness of various fans and shrouds. (I will use 'shroud' and 'duct' interchangeably here, although I'm sure they have different meanings.) It looked like maybe the type of shroud didn't matter too much as long as you had a powerful fan. I was looking forward to using a shroud that would finally give me a clear view of the build plate.
I began experimenting and things snowballed. I ended up doing this "comprehensive" study on the most popular fans and ducts. The results were predictable (you jumped to the end already anyway, so you know), but there were some surprises. I'm not the first to do this type of experiment, but maybe I can add to the knowledge base.
Theory
[Feel free to skip this part. You probably already know why fans are important. I just go on and on about how cooling works.]
Filament is hot when extruded. That's sort of the whole idea. But, when you lay down a layer of extrudate (it's a word) you want it to be solid before you lay down another layer on top of it. If not, the layers start getting squished and you lose the integrity of your design. Not only that, but when you try to bridge or do an overhang, there's very little or even nothing under your current layer. The more quickly you can cool your filament below the glass transition temperature, the less your layer will sag. This is why we use fans.
I started thinking about how a fan cools a surface. There are a few important variables, but mainly there are two big aspects: air velocity and time. Air velocity contributes to the rate of cooling, while time is how long that moving air is in contact with the hot filament. Let's start with air velocity.
A cooling fan is capable of producing a certain pressure which, given a flow configuration, translates into an air velocity. Axial fans typically produce a lower pressure than a blower (also called a centrifugal fan). The type of duct also determines velocity due to the flow area and internal resistances. You can create a narrow duct opening and you'll get a higher velocity (but lower total air flow). Increase the size of the opening, and the velocity decreases but you get a larger amount of air. It is always a trade-off.
What about time? That one is more difficult. You only have so much time after you extrude to cool the filament before it starts to deform. You need to use that time as effectively as possible. Your fan is moving with your hot end, so you need to consider its zone of influence (ZOI), which is the characteristic length of the zone of high air velocity. For example, let's say you have a duct that points at your hot end from one direction and gives you a beam of cool air with a width of 20 mm. Your hot end is moving at, let's say, 50 mm/s. The hot filament will only be in the ZOI for 0.2 seconds. (The filament is extruded in the middle of the ZOI and 'moves' to the outer edge.) That's not a lot of time. So, naturally, you think it's time to get a wider duct and increase the width of your air beam. Well, you'll be lowering the air velocity in the process. Okay then, use a duct with a smaller nozzle to get a laser-focused beam of high-speed air. Well, you'll lower your total air flow and decrease the size of your ZOI (which, in turn, lowers the amount of time).
What does this all mean? I have no idea. Well, for one, I guess it means you should probably be using a blower if you care about cooling. But as far as choosing a duct... That's why you've got to do the tests.
Procedure
The plan was simple. Choose a selection of popular and different fan/duct combinations and print an overhang test. The overhang has angles of 30, 45, 60, 70, and 80 degree. I'd then compare the results and assign a purely arbitrary but relative score. The tests would use the same filament, the same gcode, and the same conditions. Only the fan and duct would change. 100% fan after the first layer.
Equipment
I've got a Monoprice Maker Select V2.1 with a Micro Swiss all-metal hot end, but the results should be applicable to most printers. I chose Hatchbox PLA as my filament. The axial fan is the stock 40mm fan. The blower is a 50mm 0.15A fan from amazon.
The Ducts/Shrouds Tested
No Fan At All
I don't expect this to work, but I needed a control. Who knows? Maybe this fan thing is a myth.
Stock Fan and Metal Duct
This comes with the printer, so you'd think it wouldn't be too bad. It has the advantage of being free and simple. I did the adjustment to get it pointed more squarely at the nozzle, but otherwise no changes.
Stock Metal Duct, but with a blower (via adapter made by me)
If the stock fan is okay, then this should be even better, right? It involves removing the stock axial fan and replacing it with the fan adapter and blower. It sticks out a bit, but blasts plenty of air. It's advantage is that it's an easy mod and the duct won't melt.
DiiiCooler by Pawpawpaw85 with blower
This is the de-facto standard that everyone says is the duct to use. I've had good luck with it, but I had to see how it compared. The advantage is omni-directional cooling. The disadvantage is that it can be a pain to print and can be a headache attaching and removing (which is why they keep melting). Also, it blocks your view so you can't see that sweet, sweet hot-end-on-build-plate action.
DiiiCooler with axial fan (via 40mm fan adapter)
The DiiiCooler is great, but is it the fan or the duct (or both)? This test changes the blower for a 40mm axial fan using the adapter that the designer provides. It's definitely less air flow, but maybe that doesn't matter. (Spoiler: it matters.)
Simple 50mm part cooling fan for wanhao i3/ alike by DevilZMods
If I were a betting man, I would have said this design would win the day. After reading the fan/shroud study, I thought the best plan would be to point your blower at the nozzle and pat yourself on the back for being so clever. The advantage of this design is the high air flow, since there is very little between the fan and nozzle to slow it down. The only disadvantage is that this particular design wants you to glue a little nozzle on the fan. I taped mine and it stayed on fine for one print.
WANHAO i3 Fan duct by Thorped
This is another very popular fan duct that blasts air from three sides. So, it should be 75% as good as the DiiiCooler? That math checks out, but I've got to run the test anyway. It has the advantage of giving you a nearly unobstructed view of the hot end. The big disadvantage is the method of mounting, which is on the back of the extruder carriage and, depending on your printer model, might require tapping a mount hole. Also, it isn't designed for my printer, so I had to use an adapter.
CiiiCooler for Wanhao Duplicator i3 / Maker Select also by Pawpawpaw85
Added by popular demand and because it just makes sense. From the same designer of the DiiiCooler, this model gives a clear view of the hot end, but is supposed to also provide great cooling. Should be an interesting comparison. Like Thorped's design, it attaches to the back of the extruder carriage, so I had to use the provided adapter on my Monoprice Maker Select V2.1. Indecently, the adapter, like the duct itself, is really elegantly designed. Somehow, this duct was even more challenging to print than the DiiiCooler, but that may have been just me.
Results
Check my photos for a visual guide to the notes and scores below. Score is from 0 to 10; 0 being a total disaster and 10 being the perfect print.
Fan/Duct Type | Notes | Score |
---|---|---|
None (control) | Not so great.![]() | 2 |
Stock Fan and Metal Duct | Better than nothing, but honestly not that much. The 60 degree angle fared much better, but otherwise only a very moderate improvement. | 3 |
Blower w/ Stock Duct | This was a huge surprise. 30 and 45 degree overhangs are excellent. 60 and 70 are both pretty good. In fact, 80 isn't even that bad. | 8 |
DiiiCooler w/ Blower | Time to shine. This should be the best - and it is... but not by that much. It is only very slightly better than the stock duct with a blower. Everything up to and including 60 degrees is about perfect. There's a little stutter at 70 and 80 is about as good as you can hope for. | 9 |
DiiiCooler w/ Axial Fan | This was a little shocking also. No better than stock. Also, it's an abomination.![]() | 3 |
DevilZMods simple 50mm | I had such high hopes, but alas... It was about in the middle of the pack. 30 is great, 45 had a little issue, really started to flop on 60 and up. Bummer. | 6.5 |
Thorped's Wanhao i3 Fan duct | Again, I really wanted this one to work out. It's okay and scored in the top half of the group (such as it is). Nearly the same results as DevilZMods simple 50mm. Hiccup on 45, 60 and 70 are okay, 80 is not that terrible. | 7 |
CiiiCooler | This late addition turned out to be right about where you'd expect it. Not quite as good as DiiiCooler, this design still did very well. I have to call this better than Thorped's duct or DevilZMods', just due to the performance on the 45 degree slope, which was about flawless. Up from there, 60 was decent, between 70 and 80 was a problem, but otherwise pretty clean. | 7.5 |
Summary of all results
Conclusion
First, throw out your axial fan and get a blower if you haven't already.
Second, the opinion of the masses seems to be true here. The DiiiCooler is the reigning champion, and for good reason.
But, there were some surprises. The runner-up was the stock duct with a blower jammed onto it. And it was really close! Why is this? Maybe, since there is so little flow resistance in the stock duct, the air flow is high and spread over a larger zone of influence. Maybe you don't need omni-directional cooling after all.
Between the DiiiCooler and CiiiCooler, the results are pretty clear. DiiiCooler just kills it, while the CiiiCooler is very strong, but just not on that level. It's easy to guess that the difference is due to the gap in the shroud, but I'm not willing to make that leap just yet.
Also, why didn't DevilZMods simple 50mm or Thorped's Wanhao i3 fan duct perform better? I really wanted one of these to come out on top, since they provide an unobstructed view of the hot end. Maybe, in the case of DevilZMods design, the air is too laser-focused and has too small of a zone of influence. Maybe Thorped's design has too much flow resistance, since the air has to flow around a corner. Both designs seem to direct flow down toward the build plate, rather than in toward the hot end. I just don't know.
Anyway, my plan from now on will be to use the DiiiCooler for PLA and swap in the stock duct with a blower for materials that don't need much fan (e.g. ABS and PETG). That way, there's nothing to melt.
This was a tough test. You probably shouldn't be printing overhangs this extreme without supports anyway. I mean, I was printing a 0.4mm width and 0.2mm thickness, so any overhang greater than about 63 degrees means there is NO support from the previous layer. Even 60 degrees is basically trying to print without any support. The fact that some of these ducts worked so well for 70 and 80 degrees is nothing short of amazing.
And one final thought. As I went through this process, I came to realize that these designs are more than clever technical components - they are also functional pieces of art. An incredible amount of work went into their creation, so take a moment to thank the designer of your favorite duct (or any other model). Show your appreciation by tipping them on Thingiverse or leaving an encouraging comment.
What Next?
I'm done for now. You do what you want. But, there are plenty of unanswered questions.
"What about MY favorite duct/fan/mod?!" You test it. (Although I kinda want to try the Cobra).
What about bridging?
How does the cooling rate affect inter-layer adhesion and strength?
What about other filament materials?
What about different orientations, print directions, speed, repeatability, etc?
Don't like my results? Cool, cool. I've got no dog in this fight. Use what works for you.
UPDATE: /u/cyborgcanuck did a study on the effect of orientation on the blower performance. The results may surprise you.
model of the best circular airflow of the nozzle
How to upgrade the blower unit of a 3D printer and maximize print quality?
One of the parameters of the 3D printer that affects the quality of the model is the cooling of the filament. Airflow is responsible for lowering the temperature of the plastic. It is proposed to increase the capabilities of the cooling unit by installing powerful fans and upgrading the air duct.
Why do I need airflow for a 3D printer?
The principle of FDM printing is to heat the plastic to a softening temperature and extrude it through a nozzle onto the worktable. Further, the polymer solidifies, the layers at the same time are connected, forming a homogeneous three-dimensional object. But the heated plastic has fluidity, and if the previous layer does not have time to cool down to the curing temperature, the model begins to lose its desired shape. The heat of the heated nozzle also has its effect: the already cooled layer softens again when the extruder moves directly above it. nine0003
Temperature deformation is especially noticeable on miniature and thin-walled objects. This is due to the following points:
- small parts are constantly exposed to heat coming from the nozzle;
- thin model elements heat up faster.
To prevent the temperature rise of already finished layers and to cool the last of the printed ones faster, 3D printers are equipped with airflow.
What is a cooling unit? nine0023
The blower unit consists of the following components:
- fan;
- air duct.
Fan speed and start times are set in the slicer. The duct creates a directional flow, providing cooling to the desired area.
Important! Slicer airflow settings are set by default. But for each type of plastic and the shape of the 3D part, it is recommended to set special parameters, which makes it possible to maximize the quality of the model. nine0003
There are no universal values, each user of a printing device selects them empirically.
How can I improve print quality with airflow?
To set the cooling of the model as correctly as possible, consider the following:
- Type of plastic.
ABS and PETG have a high melting point and require less airflow. Large objects sometimes print with the fan turned off. Parts made of PLA, especially small ones, may require 100% airflow; when printing several figures at the same time, the fan speed can be reduced to 60-70%. nine0016
- Model value. When printing large-sized objects, the plastic has time to cool down so much that when the next portion of plastic comes from the extruder, the previous layer does not heat up to the critical fluidity temperature. Accordingly, the formation of a part with a small surface area should occur with blowing, the intensity of which will be the higher, the smaller the size of the print area.
- The shape of the feature. Here, the wall thickness, the presence of supports and the density of filling are taken into account. Models with small, thin, openwork elements are printed, be sure to turn on the fan. The same requirement applies to parts with less than 30% infill. The higher the percentage of filling, the less airflow is allowed.
nine0016
Important! When setting the fan operation mode in the slicer, all the above conditions are taken into account. Experienced users recommend keeping statistics on settings and print results. So by trial and error, over time, the maximum quality of the final result is achieved.
It is not always possible to achieve the desired result by changing the software settings of standard equipment. The maximum effect is achieved by installing high-power fans and other designs and replacing air ducts. nine0003
The best models of blowing nozzle for 3D printer
To modify the plastic cooling system, three blowing options are most often used:
- Direct (one-way) with an improved air duct and a more powerful fan.
- Double-sided.
- Circular.
Any of these is suitable for improving the print quality of a 3D model.
Straight
The simplest option is to replace the stock fan with a "snail" or the same, but more powerful, and leave the standard air duct. But another solution is also proposed: the installation of an improved duct. It has a reshaped spout, which allows for a more directed air flow, and a seat for a fan. nine0003
By redirecting the air jet, more precise cooling of the target area is achieved with minimal impact on nozzle temperature. And due to the installation of a productive fan, a wide adjustment of the blowing speed is provided.
Double ended
Dual outlet ducting is another way to improve your airflow system. But separating the air stream into two significantly reduces the power of each. This means that a stronger air blower is needed (the standard one will definitely not cope). Most often, seats for two fans are formed in the duct box - one for each outlet. Double-sided blowing does not have a noticeable disadvantage of one-sided blowing, when, depending on the direction of movement of the extruder, there is a different cooling intensity of the plastic. nine0003
Circular
Circular, or annular, cooling is a uniform blowing of the zone from all sides. The air flow is directed in such a way that it does not affect the nozzle. The standard fan also needs to be replaced here. Instead, they put one or two more powerful ones, for the installation of which a seat is provided on a modified duct box.
Users of 3D printers who have applied this solution note the following drawback: the circular air duct strongly blocks the view, making it difficult to control the quality of the print. nine0003
Important! Any increase in fan power results in increased noise during fan operation. The same can be said about installing two coolers at once. Experienced users recommend paying attention to expensive models of well-known brands, whose developers have made every effort to reduce the noise of their devices.
***
Changing the airflow settings has a significant effect on the quality of 3D printing. When software settings are not enough, you should pay attention to the modernization of the cooling unit. Users offer different solutions, tested on their own experience. It remains to choose the appropriate one for the tasks assigned to the printer. nine0003
- May 17, 2021
- 7017
Get expert advice
Free 3D file Rigidbot 2 cooling fan duct parts Rev2・3D printing template to download・Cults
Shattered Pirate Sword - Bicolor
Free
Low detail high poly head
Free
Death Star Laser Turret - Simple
Free
Circle Center Finder
Free
Christmas Tree Topper - Angel Moroni
Free
Death Star Laser Turret - Homing Cannons
Free
Double Head Calibration Plate - Control Board
Free
Quilt Rule Holder
Free
The best files for 3D printers in the Tools category
zipper
Free
nine0022 Tool box for 3D printer4,70 €
Tile crossbar 4mm
Free
MODULO 8 - modular desk organizer
7,55 €
2020 Nozzle Rack 6
Free
Test Models
Free
nine0022 Watchmen NeoPixel GogglesFree
Protective visor Covid 19
Free
Bestsellers in the Tools category
INDICATOR FOR BETTER BED LEVELING FOR ENDER 3 V2
2. 81 €
Bit holder Spartan 4 mm Hex
1,80 €
nine0022 ENDER 3 S1, S1 PRO, SPRITE, V3 AIR DUCT FAN 5015, ACCELEROMETER, LED strip €2.68 -twenty% 2.14 €
Shrek Pooping Toothpaste Topper
2.82 €
Fire hydrant storage container
1.88 €
nine0022 Phone holder2.43 €
PET-Machine, make your own plastic bottle filament at home!
15 €
3D printed wave transmission (harmonic drive)
4.99 €
Cooling system Minimus Hotend
€2. -10% 2.10€ 33
Display holder FLSUN v400
€9.99 -fifty% 4.99 €
Armadillo - flexible wire conduit
€1.67 -10% 1.50 €
2,81 €
Business card embossing system
3 €
ENDER 3 S1, S1 PRO, SPRITE, HOT END DUCT 4020 OR 5015 FAN, PROBE NO Y OFFSET
€2.28 -twenty% 1.