3D printer casting resin
%100 Ash-Free Casting 3D Printer Resins for Jewelry & Dental – powerresins
Best Direct Casting Quality
Our castable resins do not require any post-curing or special treatment for casting.
DISCOVER CASTABLE RESIN
Enjoy Enhanced Casting Quality with PowerResins Opaque
DISCOVER OPAQUE RESINSharp and High details with PowerResins Dark
No need to do extra polishing! Reach high details and smooth surfaces without visible layers.
DISCOVER DARK RESIN
Excellent Metal Production with PowerResins Burn
Easily produce high quality crowns, bridges, custom bars, hybrid abutment crowns and partial frameworks
DISCOVER BURN RESIN
Get Smooth Surface and Easily Set Stones with PowerResins Wax
DISCOVER WAX RESINSpecial Ceramic Based 3d Printer Resin for Dental Model Printing
DISCOVER MODEL RESINBest Direct Casting Quality
Our castable resins do not require any post-curing or special treatment for casting.
DISCOVER CASTABLE RESIN
Enjoy Enhanced Casting Quality with PowerResins Opaque
DISCOVER OPAQUE RESIN
Sharp and High Details with PowerResins Dark
DISCOVER DARK RESIN
Excellent Metal Production with PowerResins Burn
Easily produce high quality crowns, bridges, custom bars, hybrid abutment crowns and partial frameworks
DISCOVER BURN RESIN
Get Smooth Surface and Easily Set Stones with PowerResins Wax
DISCOVER WAX RESIN
Special Ceramic Based 3d Printer Resin for Dental Model Printing
DISCOVER MODEL RESIN
Best Castable Resins for Jewelry Production!
Best Dental Resins for Digital Dentistry!
Jewelry and Dental Customer Gallery
Discover Compatible DLP, LCD and SLA 3D Printers
COMPATIBLE PRINTERS AND SETTINGSTestimonials
Adam Berry
Co-Founder of PageFly
Lorem ipsum dolor sit amet, consectetur adipisicing elit. Error reprehenderit repellendus iure, dolor, tenetur suscipit laboriosam at quisquam explicabo natus! Minus placeat, deleniti ipsum.
Adam Berry
Co-Founder of PageFly
Lorem ipsum dolor sit amet, consectetur adipisicing elit. Error reprehenderit repellendus iure, dolor, tenetur suscipit laboriosam at quisquam explicabo natus! Minus placeat, deleniti ipsum.
Adam Berry
Co-Founder of PageFly
Lorem ipsum dolor sit amet, consectetur adipisicing elit. Error reprehenderit repellendus iure, dolor, tenetur suscipit laboriosam at quisquam explicabo natus! Minus placeat, deleniti ipsum.
Use PowerResins Castable resins with all 3D Printers
AnyCubic 3D Printers
DISCOVER
Asiga 3D Printers
DISCOVER
Phrozen 3D Printers
DISCOVER
Elegoo 3D Printers
DISCOVER
Solus 3D Printers
DISCOVER
B9 3D Printers
DISCOVER
Novafab 3D Printers
DISCOVER
Dentafab 3D Printers
DISCOVER
Do you have a Sticking Problem on your Build platform?
Solution :
Primer Resin Strong Adhesion
PowerResins Primer, is a resin that has very strong adhesion properties and designed to use for any LCD, DLP and SLA technology printers who has adhesion issues with.
Learn More
Casting Webinar
Customer Experiences
PowerDent Temp profile settings for Anycubic Photon 3D Printer
We will provide some profiles for PowerDent Temp DLP resin, however you can adjust ...
CONTINUE READING
Elegoo Mars 3D Printer Settings
You can use PowerCast Burn DLP resin with Elegoo Mars 3D Printers. You simply need to adjust the printing profiles ...
CONTINUE READING
PowerCast Burn Resin with RapidShape 3D Printers
The DLP PowerResins such as PowerCast Burn or PowerCast Wax have been formulated . ..
CONTINUE READING
Solus Printing Settings
We provide here printing profile settings used by some of our customers for PowerCast Solus resin, however you can adjust these parameters according ...
CONTINUE READING
Who we are?
We are a team of 3D printer material experts developing and manufacturing 3d printer resins for jewelry manufacturers and dental laboratories.
MORE ABOUT US
Castable resin for 3D printers
Sort byRelevanceBestsellersCustomer ReviewsPrice, Low to HighPrice, High to LowNew arrivalsHighest Discount
-
000 g
- High precision
- Wax-based
- Clean and ash-free burnout
-
- For dental, jewellery and industrial applications
- Ashless burnout
- Low shrinkage factor
-
- No post-curing necessary
- No ash residue
- Simple post-processing
-
- Smooth surfaces
- No ash residue
- Low shrinkage
-
- Castable resin
- Hardly any ash residue
- Reworkable by hand
-
000 g
- Real wax content of over 30%
- Exact details and structures
- Burning out without residue
-
- Castable synthetic resin
- Very little shrinkage
- High precision
All prices incl. VAT.
Casting on burnt master models on the example of SLA 3D printers from Kings 3D
News
precision casting of metals, where photopolymer resins or filaments are used as a material for 3D printing. In this article, we will briefly review the technology using examples of products obtained using Kings 3D laser stereolithographic 3D printers.

Casting from 3D printed master models allows you to obtain castings without cores, slopes, bays and seams, with tighter dimensional tolerances and with reduced machining allowances compared to casting from foam and wax blanks.
This technology is already used in some Russian enterprises in the aerospace, automotive, jewelry and other industries, although its implementation in Russia, for a number of reasons, is much slower than its counterparts in the US, EU, China and other industrialized countries.
In the Chinese city of Xi'an, one of Kings 3D's clients has several dozen SLA 3D printers installed, including three Kings 600Pro with a working volume of 600x600x400 mm, which print master models around the clock with burn-out photopolymer resin.
The use of burn-out 3D-printed photopolymer master models in foundries allows to optimize production processes and reduce costs, including by reducing the time to receive castings and produce finished products. The advantages of laser stereolithography include the ability to produce complex geometries with very high precision and the increased strength of master models compared to similar parts made from wax and Styrofoam.
3D Lost Wax Casting is a more precise process than wax and foam master casting, making it well suited for aerospace, engineering, jewelry, dentistry and other industries with high dimensional accuracy requirements.
When preparing digital models for 3D printing, software defines a cellular internal structure that allows:
The main advantages of casting on 3D-printed burnt-out master models:
- no deformation during heat treatment, obtaining a mold;
- high casting accuracy with significant reduction in post-processing costs;
- possibility of single and small-scale production.
The main stages of the technological process of casting on 3D-burned models:
- 3D printed master model.
- Sprue holder.
- Forming the flask.
- Burn-in of photopolymer.
- Pouring metal into a finished mold.
- Product finishing.
Manufacture of Sanctioned Parts by Reverse Engineering and Casting from 3D Printed Master Models
Today, due to sanctions, there are certain difficulties with the import of a number of spare parts for equipment from the EU countries, Japan, and the USA. However, having an original part in hand, it can be reproduced by casting using burnt master models.
First you need to get a digital model using reverse engineering, then print a master model on a 3D printer, then make a mold and make a casting. The technology makes it possible to manufacture complex parts such as track shoes, impellers, housings, gears and much more.
Some examples of such products:
Prepared by Z-Axis, the exclusive distributor of additive equipment from Shenzhen Kings 3D Printing Technology Co. on the territory of Russia and the countries of the customs union. Detailed information about Kings 3D 3D printers and consultations on the topic of casting on burnt master models are available through the official website.
Do you have interesting news? Share your developments with us, and we will tell the whole world about them! We are waiting for your ideas at [email protected]
More interesting articles
5
Follow the author
Follow
Don't want
Compared to traditional casting, 3D printed sand casting has several advantages...
Read more
5
Subscribe to the author
Subscribe
Don't want
Anodizing is a process aimed at creating protective oxide layers on the surfaces of products. ..
Read more
84
Subscribe to the author
Subscribe
Don't want
Collaboration 3D
We are pleased to present you our joint development with Speci...
Read more
Wax Castable Jewelry 3D Printing Resin
Liqcreate Wax Castable is a blue wax based photopolymer with reliable processability and printing accuracy on LCD/MSLA, DLP and laser 3D printers. Parts 3D printed from this material capture intricate details and show sharp details. This wax based material offers smooth surfaces with clean burnout for a reliable casting process. Create custom elegant organic geometry with positive and negative engraving to match your preference. Liqcreate Wax Castable creates ideal casting patterns for jewelry, dental and industrial parts.
Key benefits
- - High precision
- - wax based
- - Clean and Ashless Burnout
- - Excellent casting engravings
3D printer compatible
- – Phrozen Sonic Mini 4K
- – Anycubic Photon
- – Elegoo Mars
- - And more 385-405 nm DLP, LCD and SLA 3D printers
Wax-based Clean and ash-free burning High accuracy
Ash-free, clean burn-in wax castable resin ideal for jewelry engraving
One of the key benefits of using Liqcreate Wax Castable resin is accurate and flawless engraving on rings, as shown on the rings below.
Processing Wax Castable resin
Due to the high amount of wax, Liqcreate Wax Castable hardens at 17-18˚C. It is not recommended to use this product at an ambient temperature below 18˚C. storage or transport of Liqcreate Wax Castable below 18˚C. Before processing, it is necessary to heat the product to the liquid phase. This can be done by leaving the product for 5 hours at room temperature or by placing the package in a warm room (without direct light, in the original package) up to 50°C for 20 minutes.
3D Printing with Liqcreate Wax Castable Resin
It is important that the parts printed on the 3D printer are flawless in order to get the best casting results. A layer thickness of less than 0.05mm is highly recommended along with a well calibrated 3D printer. Find out your printer settings here, or send an email to [email protected] for more information on printer settings and compatible 3D printers.
Investment material for Wax Castable resin
During the development of Wax Castable, all casting tests were carried out using Prestige Unicast investment material. Other materials may also work with Liqcreate. Wax Castable. It is important to follow the instructions of the investment material in order to get the best results.
Burn-in Chart for Liqcreate Wax Castable Resin
We followed the instructions of the investment compound (Prestige Unicast). The following burn-in is used graph:
Parts have a matt finish when cast and polishing is necessary to achieve a glossy metal. As a reference, we have shared an image below of the printed part, the freshly cast part, and on the right side of the (partially) polished part.
Frequently Asked Questions
In this section, we will review the most frequently asked questions. Most post-cast defects can be attributed to the printed part, post-processing, or type of investment.
Printing with Liqcreate Wax Castable resin.
The investment material will take over every detail of the printed part. This means that the quality of the 3D printed wax model must be as perfect as possible. Printing with Wax Castable resin can be more difficult compared to other resins due to the significant amount of paraffin present in the resin. At temperatures below 18 degrees Celsius, the resin hardens. It is important that the resin is completely liquid during printing. Also the room temperature in which you used Wax Castable resin temperature should be at least 20°C. The resin does not normally harden during printing, however, when printing in a cold room, droplets left on the platform may harden. This will complicate the washing process. It is important that the wash solvents also have a temperature of at least 20°C to prevent solidification during the wash.
Many 3D printers are already optimized with Liqcreate. Wax Castable resin. Find out if your printer is listed here. Send an email to [email protected] if your printer is not listed. Most settings have been optimized for filigree designs, these are subtle designs that often require longer exposure times. If you have larger designs, the exposure time for your details may be shorter.
We have noticed that the wax inside the resin gives poor adhesion to anodized aluminum oxide platforms such as the Elegoo Mars series. In order for the parts to fit better on the platform, it is recommended to make some changes to the support. The raft of supports has a large area and often pulls the part off the platform. To change the raft settings, printing will be much easier. Changing the height and thickness of the raft by 0.1 mm will solve most of these problems.
The orientation of your parts.
Part orientation is especially important for engraved rings. For engraved rings, it is recommended to place the rings at a 20 degree angle rather than vertically. The reason is that the chance of overhealing your engravings in this position is much lower. See image below for better orientation. If you still have questions, if your orientation or settings are good, feel free to contact us at [email protected]
Post-processing Wax Castable resin.
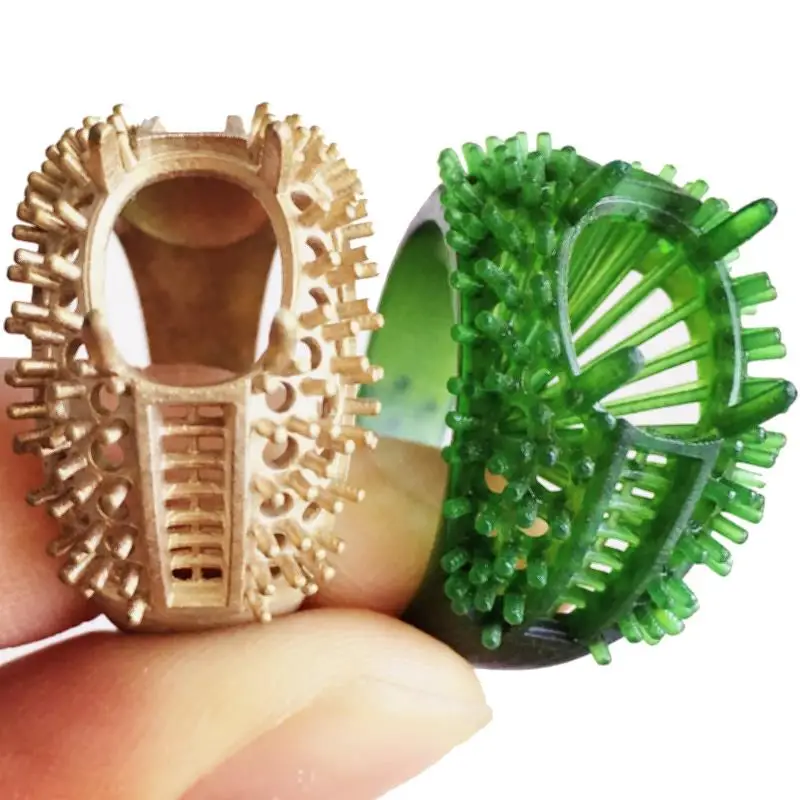
In addition to adhesion, it is important that all layers of parts are fully visible. Parts should be non-tacky and have a matte finish after washing and drying. Excess resin or sticky surfaces can react with the investment and create pores in castings.
If no anti-aliasing or blur settings are used, layers should be clearly visible in perfectly printed and blurred parts. An example of a part printed and washed correctly can be found in the image below. It should be noted that the investment material and therefore the cast metal parts will also have these visible features. If this is undesirable, sanding before casting or using smooth or blur settings can help reduce the effect of the layer.
Investment material for Liqcreate Wax Castable resin.
Choosing the right investment material when using 3D printed wax models is very important. Resins, as well as wax-based resins, have a higher thermal expansion compared to regular wax. The investment material must be strong enough to withstand this expansion without cracking.