3D printer automotive
9 Ways 3D Printing is Changing the Automotive Industry
Although you won’t be able to buy a 3D printed car at the dealership just yet, 3D printing has for many years been a vital part of the development process for automobiles. Recently, however, we’re starting to see 3D printing use cases gain a foothold throughout manufacturing.
3D printing can add enormous value to supply chains, unlocking a broad spectrum of production applications. The technology is growing more workable and affordable, with companies able to bring additive manufacturing in-house to support processes on the factory floor. New, resilient materials are opening opportunities for producing high precision, functional 3D prints that can stand in for final parts and offer (mass) customization opportunities and high performance, but that’s just the beginning.
Read on to find nine key ways 3D printing is powering innovation across the automotive industry, from design to manufacturing and beyond.
Prototyping has historically been the most common use case for 3D printing in the automotive industry. Thanks to the vastly increased speed at which prototyping can be carried out using 3D printing, rapid prototyping has become virtually synonymous with 3D printing, and the technology has revolutionized the product development process.
With 3D printing, automotive designers can quickly fabricate a prototype of a physical part or assembly, from a simple interior element to a dashboard or even a scale model of an entire car. Rapid prototyping enables companies to turn ideas into convincing proofs of concept. These concepts can then be advanced to high-fidelity prototypes that closely match the end result, and ultimately guide products through a series of validation stages toward mass production.
Prototyping used to be time-consuming and expensive as a product goes through many iterations. With 3D printing, highly convincing, representative, and functional prototypes can be created within a day, at a much lower cost than with traditional manufacturing methods. Desktop 3D printers allow engineering and design teams to bring the technology in-house in order to increase iteration cycles and shorten the distance between idea and final product, strengthening their overall product development workflows.
Ford designers used Formlabs 3D printers to prototype the lettering on the back of the Ford Puma in a matter of hours.
At Ford’s Rapid Technology Center in Merkenich, Germany, many 3D printing technologies are used to create prototypes with short turnaround times. Instead of sending out a job to a shop with a several-week lead time, engineers and designers are able to hold their designs in their hands in a matter of hours.
Designers are able to produce same-day prototypes in the Rapid Technology Center, iterating several designs in just a few hours. Physical prototypes can offer advantages over digital models, says Bruno Alves, additive manufacturing expert at Ford.
For instance, Formlabs 3D printers were used to prototype the lettering on the back of the Ford Puma, allowing designers to see how the lines and shadows would appear in different lighting conditions. “The printer is so fast, and so effective for this kind of lettering, that we could supply the designers the option to iterate,” says Alves. “It’s a thing that you can see it in CATIA or other software, you can simulate lighting, but it’s different to feel, to touch, and to see all the reflections when you put the lettering on the car.”
For more insight on how 3D printing is powering innovation at automotive giants, watch our webinar with Bruno Alves of Ford Motor Co. and Christian Kleylein of Brose.
WEBINAR
In this webinar, Christian Kleylein, Technologist at Brose, one of the largest family-owned Tier 1 automotive suppliers, and Bruno Alves, Additive Manufacturing Expert at Ford will share how 3D printing is powering innovation across the automotive industry, from design to manufacturing and beyond.
Watch the Webinar Now
IGESTEK is an automotive supplier in Spain specializing in the development of lightweight solutions using plastics and composite materials. Their team uses 3D printing throughout the product development process, from the conceptual design phase to verify geometries to the detailed design phase for the realization of functional prototypes. They also use 3D printing to manufacture rapid tooling, such as inserts for plastic injection molds or thermoforming tools for composites.
Topology optimization is a hot topic in lightweighting. IGESTEK uses Autodesk Fusion 360 to generate multiple solutions based on a list of parameters.
For one suspension mount, the team developed a multi-material architecture that combines metal 3D printing based on generative geometries and lighter composite materials to offer the best performance, in a 40% lighter package than current solutions on the market. These parts were prototyped on the Form 3L, which is large enough to prototype multiple designs simultaneously for even faster iteration and testing.
For more details on this application, plus two other ways IGESTEK lightweights automotive parts, read our story with IGESTEK.
Webinar
In this webinar, Formlabs Product Marketing Lead Jennifer Milne will provide a simple overview explaining what generative design is, framed in a way that is applicable to mechanical part design, including a step-by-step tutorial of Fusion 360 where she’ll produce a lightweight bracket.
Watch the Webinar Now
Vital Auto is an industrial design studio in the UK that works with major car brands, such as Volvo, Nissan, Lotus, McLaren, Geely, TATA, and more. When the original equipment manufacturers (OEMs) don't have time for experimentation themselves, they come to Vital to turn ideas, initial sketches, drawings, or technical specifications into a fully realized physical form.
“We've used 3D printing from day one. We wanted to introduce it to our manufacturing processes, not only to reduce costs, but to give the customer more diversity with their designs and their ideas,” said Anthony Barnicott, Design Engineer in charge of additive manufacturing.
Today, Barnicott runs a whole 3D printing department, including 14 large-format fused deposition modeling (FDM) printers, three Formlabs Form 3L large-format stereolithography (SLA) 3D printers, and five Fuse 1 selective laser sintering (SLS) 3D printers. “In terms of capacity, all those printers have run 100%, 24/7, pretty much since day one. We use these printers for all areas of our concepts and designs. Typically, we use the Fuse 1s for our production-based parts and we use our Form 3Ls for our concept-based parts,” said Barnicott.
3D printing not only helps the team create better products faster, but also attracts new business. They found that many of their customers turn to them because they want to have access to the latest technologies and they want to have their components made using the latest cutting-edge materials.
“The progression in technology and 3D printing over the last 10 years is phenomenal. When I first started, producing low volume, niche vehicles, some of the products that we produce today would simply have been inaccessible. And not only am I able to produce these parts today, but I’m also able to produce them very cost-effectively, very quickly,” said Barnicott.
For more insights on specific applications with 3D printed parts, check out our in-depth story with the Vital Auto team.
White Paper
In this guide, you’ll learn how rapid prototyping fits into the product development process, its applications, and what rapid prototyping tools are available to today’s product development teams.
Download the White Paper
Thanks to the rapid development of 3D printers and high-performance materials, additive manufacturing can now be used to produce parts that are up to the challenge of extreme environments.
3D printing can be leveraged in manufacturing to reduce overhead and increase efficiency with manufacturing aids like custom jigs and fixtures and produce low-volume rapid tooling for traditional manufacturing processes like injection molding or thermoforming.
3D printed end-use parts are also increasingly common in the automotive industry, especially for applications like aftermarket, custom, or replacement parts, where other means of production would be excessively costly and slow.
Makra Pro developed a novel technique for molding leather trim pieces using 3D printed dies.
Makra Pro is an additive manufacturing service provider that has developed a novel process for molding leather, a popular trim material in luxury cars that can be difficult to shape, using 3D printed dies. In partnership with some of their clients, including manufacturers of luxury cars, motorcycles, and motor homes, they have tested a method for shaping and embossing real leather.
Using molds printed on a Form 3, Makra Pro’s technique uses expanding foam to equally distribute pressure across a panel of stretched leather. As the foam hardens, the leather is pressed into the die and takes on its shape.
The finished leather parts can then be, for example, stretched over the door panel in a car or attached to the seat cover in a vehicle. One well-known tuning company of limited-edition luxury automobiles uses these molded leather parts for wall or ceiling panels in vehicle enhancements.
Read our in-depth story with Makra Pro or download our white paper for more rapid tooling applications, including injection molding, thermoforming, and more.
White Paper
In this white paper, learn how to combine rapid tooling with traditional manufacturing processes like injection molding, thermoforming, or casting.
Read the White Paper
Dorman Products produces go/no-go test jigs with Grey Resin that are accurate to +/- 0.05 mm.
Dorman Products designs and manages a database of more than 100,000 parts for hundreds of different vehicles. “Historically we’ve released between 4,000 and 5,000 new parts each year,” says Mechanical Design Team Manager Eric Tryson.
In addition to the sheer logistical challenge of operating as an aftermarket supplier, Dorman’s product design and manufacturing teams need to be particularly agile, says Additive Manufacturing Lead Chris Allebach. “The OEMs have teams of people designing a single part, sometimes starting two years prior to a new car coming out. We need to find ways to ensure our replacements are reliable while also being fast to market.”
Before integrating 3D printers into their workflow, the lack of custom test fixturing was an obstacle to quick development. Machining was prohibitively expensive and time-consuming.
“Now, with the 3D printers, we develop the test fixtures and gauges along with prototyping the product, so when we decide on a final design, we can have the fixture to test it as well. We’re trying to be as proactive as possible,” says Allebach.
Since Dorman acquired their first 3D printer ten years ago, Allebach and Tryson have added more printers steadily, continually maxing out capacity on their existing units, and utilizing the full materials library on their Formlabs SLA printers, including a large-format Form 3L.
“[Our first 3D printer] paid for itself within two months. When we’re doing the cost justification or an ROI for any of the Formlabs printers, we can justify the payoff in months instead of a two-year time frame. That gives our leadership confidence that 3D printing is a worthwhile investment,” says Tryson.
Dorman Products is using 3D printing for several other applications. Read our article to explore them.
White Paper
For manufacturers, maximizing production speed while maintaining high part quality is critical for success. Jigs and fixtures are used to make manufacturing and assembly processes simpler, more reliable, and more efficient, reducing cycle times and at the same time improving worker safety.
Download the White Paper
BTI Gauges designs telemetry displays for high-performance cars.
Like many successful businesses, BTI Gauges started with a gap in the market. Brandon Talkmitt, founder and owner, was looking for a customizable approach to telemetry display for his high-performance car.
Talkmitt searched, unsuccessfully, for a gauge that contained multiple performance metrics, so his windshield wasn’t littered with multiple screens and distracting read-outs. He then began by prototyping the external casings of the gauges on a 3D printer and testing them out himself, subjecting the casings to high-heat environments inside cars and ovens, and modifying the design to complement multiple car models.
Right away, there was interest in his product from clientele driving 1990’s style Japanese race cars, Lamborghinis, Dodge Vipers, and other high-performance vehicles.
Talkmitt began evaluating other 3D printing options, including expensive plastic powder bed fusion 3D printers, resin 3D printers, and an inexpensive compact SLS option. But between the half a million dollar price tags on some, and the complex materials purchasing process from others, there just weren’t any options available. That is until he heard about the Fuse 1. “When I got the sample I thought, ‘Man, if my parts can look like this.’ So I ran some tests, and figured out what kind of heat it could tolerate. Did the finishing and painting process on it, and everything worked,” says Talkmitt.
During the supply chain issues of the last two years, BTI Gauges faced several shortages of the touchscreen displays, and other components needed for their nine product lines. By bringing 3D printing in-house with the Fuse 1, he was able to pivot immediately to a new design, without having to spend thousands of dollars on new tooling, or dealing with a backlog of now-obsolete products.
“I would have been stuck with all that plastic, but with the Fuse 1, I could make the change on the fly. It was a 30-minute thing for me to change the files. Without it, I would definitely be stuck right now,” says Talkmitt.
Find out more about producing end-use aftermarket parts in our in-depth story with BTI Gauges.
White Paper
In this white paper, we evaluate the value proposition of bringing SLS 3D printers in-house, in comparison with outsourcing SLS parts from a service bureau.
Download the White Paper
3D printing is a toolless fabrication process that is a great match for motorsports and a powerful tool to achieve low-volume production and custom manufacturing rapidly and cost-efficiently. By eliminating tooling time and costs, it provides the flexibility to revise products quickly and accelerate time to market. It increases design freedom and gives the ability to customize products, and build complex shapes such as lattices without any additional costs.
By using in house 3D printing, motorsport teams can develop faster, keep their IP secure, test more ideas, and ultimately beat their competition.
Forge Motorsport’s redesigned duct reduced intake air temperature by 6° C.
Forge Motorsport, which makes aftermarket parts for performance cars, uses 3D printing to prototype their parts. When the Toyota Yaris GR was released, the engineers at Forge noticed a few opportunities to improve the inlet duct design—moving the airbox opening, and increasing the overall size of the part—that would reduce fluctuations in intake air temperature (IAT), which make it hard to anticipate engine performance, while reducing the average temperature overall.
They reverse engineered the OEM part using 3D scanning and made the design changes virtually in SOLIDWORKS, where they were able to simulate airflow. Once they had a workable 3D model, they prototyped it in fast-printing Draft Resin, which they used to confirm that the new location for the airbox opening would work as intended and that the overall increased size of the part wouldn’t interfere with other components or cables. With basic fit confirmed, they reprinted the part in Tough 1500 Resin, a strong and impact-resistant material, painted it black to resemble the final part, and gave it to a customer to test.
The customer used the 3D printed part in his Yaris GR for five months, during which time he collected data on performance under different conditions, including on tracks and uphill climbs. The IAT on the stock part varied between 42-45 °C, with considerable variations observed during the course of a race; with the redesigned part, printed in Tough 1500 Resin, the customer measured IATs between 35-36 °C. As anticipated, the redesigned part had both lower overall IATs and reduced fluctuations. With this data in hand, confident that their part was an improvement over the OEM design, Forge moved forward into manufacturing the final production part with carbon fiber.
For more on the reverse engineering workflow using 3D scanning, watch our webinar with Forge Motorsport and Peel3D.
WEBINAR
In this webinar brought to you by Formlabs, Solid Print3D, and peel 3d, we talk to Forge Motorsport, who manufacture performance upgrades for the aftermarket automotive industry such as valves, intercoolers, and actuators.
Watch the Webinar Now
By 3D printing molds in-house, TU Berlin’s competition team could drastically cut their costs and lead time for this carbon fiber part.
The Formula Student is a yearly engineering design competition in which student teams from around the world build and race formula-style cars. The Formula Student Team TU Berlin (FaSTTUBe) is one of the largest groups; 80 to 90 students have been developing new racing cars every year since 2005. The team added a Form 3 SLA 3D printer to their toolset that they have used to save time, reduce costs, and create carbon fiber parts that would be prohibitively expensive any other way.
3D printing molds for composites allowed the team much greater flexibility, shorter lead times, and saved costs when designing key parts like the steering wheel chassis. Machining the mold for this part would have required sourcing expensive specialized tools, and outsourcing the molded part would have taken weeks and cost nearly €1000. Instead, 3D printing the mold in-house and laminating it by hand cost only €10 in materials and 1.5 hours of working time.
The team is also using 3D printing to prototype designs, lightweight parts, and even fabricate end-use parts. Read our story with them for more details on these applications.
3D printing has given the FaSTTUBe team new flexibility, design freedom, and cost savings. Additionally, students have gained experience fabricating prototypes, tooling, and even end-use parts for their project. These skills will stay with the students as they enter the workforce, bringing valuable experience to every discipline of engineering.
White Paper
Download this white paper for composite mold design guidelines and step-by-step guides to the prepreg and hand laminating methods to create carbon fiber parts.
Download the White Paper
The intake manifold, printed in Rigid 10K Resin, recorded a lower post-race temperature than the original aluminum part.
Andrea Pirazzini has been riding motorcycles since 2012. He wanted to challenge himself to design and fabricate a functional, safe 3D printed intake manifold for his own bike. In the past, he had tried using FDM printing technology, but the result was not what he hoped for, as the part was not airtight and compromised the engine’s function.
To develop the project, Pirazzini used 3D scanning and Autodesk Fusion 360 software to reverse engineer the design. The scan of the four-stroke engine (two-valve) engine with its frame and carburetor helped him to correctly size the manifold and then to position it optimally. With the use of CAD software, it was possible to align the diameter of the head inlet with the carburetor, avoiding steps and any pressure drop or turbulence.
The new manifold design was printed with the Form 3 using the Rigid 10K Resin at a 100 microns layer height, creating a smooth surface without visible layer lines. As for the finish, Pirazzini used classic water-based sandpaper to smooth the surface. Unlike an FDM manifold, which has to be treated externally and internally to be watertight, SLA printing creates solid and waterproof parts.
The manifold that Pirazzini printed with the Form 3 has withstood high and low temperatures perfectly and is still mounted on his pit bike. Thanks to the use of a thermal imaging camera, Pirazzini discovered that Rigid 10K Resin also offered a significantly better thermal performance: The 3D printed manifold with cooling fins recorded a 40-50 degrees Celsius lower temperature compared to a classic aluminum manifold. Moreover, after a race of about 20-25 minutes at an outside temperature of about 33 degrees Celsius, it was possible to touch the manifold without getting burned.
The project not only succeeded, but it even improved the function of the engine. Based on some improvements Pirazzini made to the original design, the engine had more horsepower (about one HP, almost 10% increase) available compared to the standard machined manifold, while remaining within the limits imposed by the rules of the championship.
Find out more about how Pirazzini developed the project in our detailed case study.
White Paper
3D scanning and 3D printing workflows can be applied to replication and restoration, reverse engineering, metrology, and more. Download our white paper to explore these applications and learn how to get started.
Download the White Paper
Amid the 3D printing hype of the early 2010s, excitement grew in popular media around 3D printing large-scale, complex assemblies, including entire 3D printed cars. However, even the biggest proponents of “fully” 3D printed cars shifted focus to printing structural and trim components like the chassis, body, and seats, not the engine or other electromechanical assemblies.
Some companies, including Local Motors and EDAG, created full concept cars where the chassis and body were 3D printed, exhibiting them to the public at trade events like SEMA in the mid-2010s. However, none of these projects reached serial production.
Besides weather resistance, the cover on EDAG’s Light Cocoon provides absolute freedom when it comes to design and individualization. (source: EDAG)
Currently, the projects and companies closest to serial production seem to be Divergent 3D and XEV.
Divergent 3D combines generative design and 3D printing to create custom-tailored components for auto parts manufacturers. Once a component is designed, it’s constructed using the company’s metal 3D printers. Their first public project is the Czinger 21C hypercar, while they’re also a supplier of major OEMs, including Aston Martin.
On the other end of the spectrum, the YoYo, developed by the Italian company XEV, might be the first “mass market” 3D printed electric car that is now shipping to customers. Apart from the chassis, the seats, and the windshield, all the visible parts of the YoYo are also 3D printed. Thanks to the extensive use of 3D printing, the company has managed to reduce the number of components from 2,000 to only 57, resulting in a light design that weighs only 450 kilos.
The YoYo is the first “mass market” 3D printed electric car that is now shipping to customers.
As we have seen through all these examples, 3D printing has already been proven repeatedly to offer significant advantages to the supplier, the OEM, and the consumer when it’s leveraged creatively to reduce time to market and improve vehicle performance. In some cases, 3D printing technology is pushing boundaries and helping achieve entirely new possibilities in design and production. In others, the technology is lowering production costs and saving time.
As the understanding of the value and realities of 3D printing continues to spread through the industry, and as the technology and available material base grow ever more versatile, additive technology will continue to reshape the way we design, build, and maintain vehicles around the world.
Learn About 3D Printing for Automotive & Transportation
3D Printing for Automotive | 3D Systems
Applications of Additive Manufacturing in the Automotive Industry
-
Optimize your cabin’s physical, functional, and visual experience.
Without requiring expensive tooling, our additive manufacturing solutions allow you to create better concept car prototypes. You can make these with realistic texture and surface finishes that can be printed, plated, painted, and wrapped directly. Additionally, you can create innovations such as fastening systems and integrated latching to provide new design methods for manufacturing and service.
Collaborating with You to Enhance Automotive Design and Development
Watch One of Our Automotive Webinars
Talk to an Expert
You must have JavaScript enabled to use this form.
First Name
Last Name
Business Email
Company
Country -- Select Country --AfghanistanAlbaniaAlgeriaAmerican SamoaAndorraAngolaAnguillaAntarcticaAntigua & BarbudaArgentinaArmeniaArubaAscension IslandAustraliaAustriaAzerbaijanBahamasBahrainBangladeshBarbadosBelarusBelgiumBelizeBeninBermudaBhutanBoliviaBosnia & HerzegovinaBotswanaBouvet IslandBrazilBritish Indian Ocean TerritoryBritish Virgin IslandsBruneiBulgariaBurkina FasoBurundiCambodiaCameroonCanadaCanary IslandsCape VerdeCaribbean NetherlandsCayman IslandsCentral African RepublicCeuta & MelillaChadChileChinaChristmas IslandClipperton IslandCocos (Keeling) IslandsColombiaComorosCongo - BrazzavilleCongo - KinshasaCook IslandsCosta RicaCroatiaCuraçaoCyprusCzechiaCôte d’IvoireDenmarkDiego GarciaDjiboutiDominicaDominican RepublicEcuadorEgyptEl SalvadorEquatorial GuineaEritreaEstoniaEswatiniEthiopiaFalkland IslandsFaroe IslandsFijiFinlandFranceFrench GuianaFrench PolynesiaFrench Southern TerritoriesGabonGambiaGeorgiaGermanyGhanaGibraltarGreeceGreenlandGrenadaGuadeloupeGuamGuatemalaGuernseyGuineaGuinea-BissauGuyanaHaitiHeard & McDonald IslandsHondurasHong Kong SAR ChinaHungaryIcelandIndiaIndonesiaIraqIrelandIsle of ManIsraelItalyJamaicaJapanJerseyJordanKazakhstanKenyaKiribatiKosovoKuwaitKyrgyzstanLaosLatviaLebanonLesothoLiberiaLibyaLiechtensteinLithuaniaLuxembourgMacao SAR ChinaMadagascarMalawiMalaysiaMaldivesMaliMaltaMarshall IslandsMartiniqueMauritaniaMauritiusMayotteMexicoMicronesiaMoldovaMonacoMongoliaMontenegroMontserratMoroccoMozambiqueMyanmar (Burma)NamibiaNauruNepalNetherlandsNetherlands AntillesNew CaledoniaNew ZealandNicaraguaNigerNigeriaNiueNorfolk IslandNorthern Mariana IslandsNorth MacedoniaNorwayOmanOutlying OceaniaPakistanPalauPalestinian TerritoriesPanamaPapua New GuineaParaguayPeruPhilippinesPitcairn IslandsPolandPortugalPuerto RicoQatarRomaniaRussiaRwandaRéunionSamoaSan MarinoSaudi ArabiaSenegalSerbiaSeychellesSierra LeoneSingaporeSint MaartenSlovakiaSloveniaSolomon IslandsSomaliaSouth AfricaSouth Georgia & South Sandwich IslandsSouth KoreaSouth SudanSpainSri LankaRepublic of Sudan (North Sudan)St. BarthélemySt. HelenaSt. Kitts & NevisSt. LuciaSt. MartinSt. Pierre & MiquelonSt. Vincent & GrenadinesSurinameSvalbard & Jan MayenSwedenSwitzerlandSão Tomé & PríncipeTaiwanTajikistanTanzaniaThailandTimor-LesteTogoTokelauTongaTrinidad & TobagoTristan da CunhaTunisiaTurkeyTurkmenistanTurks & Caicos IslandsTuvaluU.S. Outlying IslandsU.S. Virgin IslandsUgandaUkraineUnited Arab EmiratesUnited KingdomUnited StatesUruguayUzbekistanVanuatuVatican CityVenezuelaVietnamWallis & FutunaWestern SaharaYemenZambiaZimbabweÅland Islands
State -- Select State --Buenos AiresCatamarcaChacoChubutCiudad Autónoma de Buenos AiresCórdobaCorrientesEntre RíosFormosaJujuyLa PampaLa RiojaMendozaMisionesNeuquénRío NegroSaltaSan JuanSan LuisSanta CruzSanta FeSantiago del EsteroTierra del FuegoTucumánAustralian Capital TerritoryNew South WalesNorthern TerritoryQueenslandSouth AustraliaTasmaniaVictoriaWestern AustraliaBurgenlandKärntenNiederösterreichOberösterreichSalzburgSteiermarkTirolVorarlbergWienAcreAlagoasAmapáAmazonasBahiaCearáDistrito FederalEspírito SantoGoiásMaranhãoMato GrossoMato Grosso do SulMinas GeraisParáParaíbaParanáPernambucoPiauíRio de JaneiroRio Grande do NorteRio Grande do SulRondôniaRoraimaSanta CatarinaSão PauloSergipeTocantinsAlbertaBritish ColumbiaManitobaNew BrunswickNewfoundland and LabradorNorthwest TerritoriesNova ScotiaNunavutOntarioPrince Edward IslandQuebecSaskatchewanYukon TerritoriesAisén del General Carlos Ibañez del CampoAntofagastaAraucaníaArica y ParinacotaAtacamaBío-BíoCoquimboLibertador General Bernardo O'HigginsLos LagosLos RíosMagallanesMauleRegión Metropolitana de SantiagoTarapacáValparaísoAnhuiBeijingChinese TaipeiChongqingFujianGansuGuangdongGuangxiGuizhouHainanHebeiHeilongjiangHenanHong KongHubeiHunanJiangsuJiangxiJilinLiaoningMacaoNei MongolNingxiaQinghaiShaanxiShandongShanghaiShanxiSichuanTianjinXinjiangXizangYunnanZhejiangÎle-de-FranceOccitanieAuvergne-Rhône-AlpesBourgogne-Franche-ComtéBretagneCentre-Val de LoireCorseGrand EstHauts-de-FranceJuraNormandieNouvelle-AquitainePays de la LoireProvence-Alpes-Côte d'AzurBaden-WürttembergBayernBerlinBrandenburgBremenHamburgHessenMecklenburg-VorpommernNiedersachsenNordrhein-WestfalenRheinland-PfalzSaarlandSachsenSachsen-AnhaltSchleswig-HolsteinThüringenAndaman and Nicobar IslandsAndhra PradeshArunachal PradeshAssamBiharChandigarhChhattisgarhDadra and Nagar HaveliDaman and DiuDelhiGoaGujaratHaryanaHimachal PradeshJammu and KashmirJharkhandKarnatakaKeralaLakshadweepMadhya PradeshMaharashtraManipurMeghalayaMizoramNagalandOdishaPuducherryPunjabRajasthanSikkimTamil NaduTripuraUttar PradeshUttarakhandWest BengalCarlowCavanClareCorkDonegalDublinGalwayKerryKildareKilkennyLaoisLeitrimLimerickLongfordLouthMayoMeathMonaghanOffalyRoscommonSligoTipperaryWaterfordWestmeathWexfordWicklowAgrigentoAlessandriaAnconaAostaArezzoAscoli PicenoAstiAvellinoBariBarletta-Andria-TraniBellunoBeneventoBergamoBiellaBolognaBolzanoBresciaBrindisiCagliariCaltanissettaCampobassoCarbonia-IglesiasCasertaCataniaCatanzaroChietiComoCosenzaCremonaCrotoneCuneoEnnaFermoFerraraFirenzeFoggiaForlì-CesenaFrosinoneGenovaGoriziaGrossetoImperiaIserniaLa SpeziaL'AquilaLatinaLecceLeccoLivornoLodiLuccaMacerataMantovaMassa - CarraraMateraMedio CampidanoMessinaMilanoModenaMonza e BrianzaNapoliNovaraNuoroOgliastraOlbia-TempioOristanoPadovaPalermoParmaPaviaPerugiaPesaro e UrbinoPescaraPiacenzaPisaPistoiaPordenonePotenzaPratoRagusaRavennaReggio CalabriaReggio EmiliaRietiRiminiRomaRovigoSalernoSassariSavonaSienaSondrioSiracusaTarantoTeramoTerniTrapaniTrentoTrevisoTriesteTorinoUdineVareseVeneziaVerbano-Cusio-OssolaVercelliVeronaVibo ValentiaVicenzaViterboAichiAkitaAomoriChibaEhimeFukuiFukuokaFukushimaGifuGunmaHiroshimaHokkaidoHyogoIbarakiIshikawaIwateKagawaKagoshimaKanagawaKochiKumamotoKyotoMieMiyagiMiyazakiNaganoNagasakiNaraNiigataOitaOkayamaOkinawaOsakaSagaSaitamaShigaShimaneShizuokaTochigiTokushimaTokyoTottoriToyamaWakayamaYamagataYamaguchiYamanashiBusanDaeguDaejeonGangwonGwangjuGyeonggiIncheonJejuNorth ChungcheongNorth GyeongsangNorth JeollaSeoulSouth ChungcheongSouth GyeongsangSouth JeollaUlsanJohorKedahKelantanMelakaNegeri SembilanPahangPerakPerlisPulau PinangSabahSarawakSelangorTerengganuWilayah Persekutuan Kuala LumpurWilayah Persekutuan LabuanWilayah Persekutuan PutrajayaAguascalientesBaja CaliforniaBaja California SurCampecheChiapasChihuahuaCoahuilaColimaDurangoFederal DistrictGuanajuatoGuerreroHidalgoJaliscoMexico StateMichoacánMorelosNayaritNuevo LeónOaxacaPueblaQuerétaroQuintana RooSan Luis PotosíSinaloaSonoraTabascoTamaulipasTlaxcalaVeracruzYucatánZacatecasŚląskieŁódzkieŚwiętokrzyskieDolnośląskieKujawsko-pomorskieLubelskieLubuskieMałopolskieMazowieckieOpolskiePodkarpackiePodlaskiePomorskieWarmińsko-mazurskieWielkopolskieZachodniopomorskieAdygeya, RespublikaAltay, RespublikaAltayskiy krayAmurskaya oblast'Arkhangel'skaya oblast'Astrakhanskaya oblast'Bashkortostan, RespublikaBelgorodskaya oblast'Bryanskaya oblast'Buryatiya, RespublikaChechenskaya RespublikaChelyabinskaya oblast'Chukotskiy avtonomnyy okrugChuvashskaya RespublikaDagestan, RespublikaIngushetiya, RespublikaIrkutskaya oblast'Ivanovskaya oblast'Kabardino-Balkarskaya RespublikaKaliningradskaya oblast'Kalmykiya, RespublikaKaluzhskaya oblast'Kamchatskiy krayKarachayevo-Cherkesskaya RespublikaKareliya, RespublikaKemerovskaya oblast'Khabarovskiy krayKhakasiya, RespublikaKhanty-Mansiyskiy avtonomnyy okrug-YugraKirovskaya oblast'Komi, RespublikaKostromskaya oblast'Krasnodarskiy krayKrasnoyarskiy krayKurganskaya oblast'Kurskaya oblast'Leningradskaya oblast'Lipetskaya oblast'Magadanskaya oblast'Mariy El, RespublikaMordoviya, RespublikaMoskovskaya oblast'MoskvaMurmanskaya oblast'Nenetskiy avtonomnyy okrugNizhegorodskaya oblast'Novgorodskaya oblast'Novosibirskaya oblast'Omskaya oblast'Orenburgskaya oblast'Orlovskaya oblast'Penzenskaya oblast'Permskiy krayPrimorskiy krayPskovskaya oblast'Rostovskaya oblast'Ryazanskaya oblast'Sakha, RespublikaSakhalinskaya oblast'Samarskaya oblast'Sankt-PeterburgSaratovskaya oblast'Severnaya Osetiya-Alaniya, RespublikaSmolenskaya oblast'Stavropol'skiy kraySverdlovskaya oblast'Tambovskaya oblast'Tatarstan, RespublikaTomskaya oblast'Tul'skaya oblast'Tverskaya oblast'Tyumenskaya oblast'Tyva, RespublikaUdmurtskaya RespublikaUl'yanovskaya oblast'Vladimirskaya oblast'Volgogradskaya oblast'Vologodskaya oblast'Voronezhskaya oblast'Yamalo-Nenetskiy avtonomnyy okrugYaroslavskaya oblast'Yevreyskaya avtonomnaya oblast'Zabaykal'skiy krayCentral SingaporeNorth EastNorth WestSouth EastSouth WestA CoruñaÁlava / ArabaAlbaceteAlicante / AlacantAlmeríaAsturiasÁvilaBadajozBalearsBarcelonaBurgosCáceresCádizCantabriaCastellón / CastellóCiudad RealCórdobaCuencaGironaGranadaGuadalajaraGuipúzcoa / GipuzkoaHuelvaHuescaJaénLa RiojaLas PalmasLeónLleidaLugoMadridMálagaMurciaNavarra / NafarroaOurensePalenciaPontevedraSalamancaSanta Cruz de TenerifeSegoviaSevillaSoriaTarragonaTeruelToledoValencia / ValènciaValladolidVizcaya / BizkaiaZamoraZaragozaAargauAppenzell AusserrhodenAppenzell InnerrhodenBasel-LandschaftBasel-StadtBernFribourgGenèveGlarusGraubündenJuraLuzernNeuchâtelNidwaldenObwaldenSankt GallenSchaffhausenSchwyzSolothurnThurgauTicinoUriValaisVaudZugZürichChanghua CountyChiayi CityChiayi CountyHsinchu CityHsinchu CountyHualien CountyKaohsiung CityKaohsiung CountyKeelung CityMiaoli CountyNantou CountyPenghu CountyPingtung CountyTaichung CityTaichung CountyTainan CityTainan CountyTaipei CityTaipei CountyTaitung CountyTaoyuan CountyYilan CountyYunlin CountyŞırnakŞanlıurfaİstanbulİzmirAğrıAd?yamanAdanaAfyonkarahisarAksarayAmasyaAnkaraAntalyaArdahanArtvinAydınBalıkesirBartınBatmanBayburtBilecikBingölBitlisBoluBurdurBursaÇanakkaleÇankırıÇorumDenizliDiyarbakırDüzceEdirneElazığErzincanErzurumEskişehirGaziantepGiresunGümüşhaneHakkâriHatayIğdırIspartaKırşehirKırıkkaleKırklareliKahramanmaraşKarabükKaramanKarsKastamonuKayseriKilisKocaeliKonyaKütahyaMalatyaManisaMardinMersinMuşMuğlaNevşehirNiğdeOrduOsmaniyeRizeSakaryaSamsunSiirtSinopSivasTekirdağTokatTrabzonTunceliUşakVanYalovaYozgatZonguldakCrimeaCherkasyChernihivChernivtsiDnipropetrovskDonetskIvano-FrankivskKharkivKhersonKhmelnytskyiKirovohradKyivLuhanskLvivMykolaivOdesaPoltavaRivneSumyTernopilVinnytsiaVolynZakarpattiaZaporzhzhiaZhytomyrAberdeen CityAberdeenshireAngusAntrimArgyll and ButeArmaghAvonBanffshireBedfordshireBerkshireBlaenau GwentBordersBridgendBristolBuckinghamshireCaerphillyCambridgeshireCardiffCarmarthenshireCeredigionChannel IslandsCheshireClackmannanshireClevelandConwyCornwallCumbriaDenbighshireDerbyshireDevonDorsetDownDumfries and GallowayDurhamEast AyrshireEast DunbartonshireEast LothianEast RenfrewshireEast Riding of YorkshireEast SussexEdinburghEssexFalkirkFermanaghFifeFlintshireGlasgowGloucestershireGreater ManchesterGwyneddHampshireHerefordshireHertfordshireHighlandHumbersideInverclydeIsle of AngleseyIsle of ManIsle of WightIsles of ScillyKentLancashireLeicestershireLincolnshireLondonLondonderryMerseysideMerthyr TydfilMiddlesexMidlothianMonmouthshireMorayNeath Port TalbotNewportNorfolkNorth AyrshireNorth East LincolnshireNorth LanarkshireNorth YorkshireNorthamptonshireNorthumberlandNottinghamshireOrkneyOuter HebridesOxfordshirePembrokeshirePerthshire and KinrossPowysRenfrewshireRhondda, Cynon, TaffRoxburghshireRutlandShetlandShropshireSomersetSouth AyrshireSouth LanarkshireSouth YorkshireStaffordshireStirlingSuffolkSurreySwanseaTorfaenTyne and WearTyroneVale of GlamorganWarwickshireWest DunbartonshireWest LothianWest MidlandsWest SussexWest YorkshireWiltshireWorcestershireWrexhamAlabamaAlaskaAmerican SamoaArizonaArkansasCaliforniaColoradoConnecticutDelawareDistrict of ColumbiaFederated MicronesiaFloridaGeorgiaGuamHawaiiIdahoIllinoisIndianaIowaKansasKentuckyLouisianaMaineMarshall IslandsMarylandMassachusettsMichiganMinnesotaMississippiMissouriMontanaNebraskaNevadaNew HampshireNew JerseyNew MexicoNew YorkNorth CarolinaNorth DakotaNorthern Mariana IslandsOhioOklahomaOregonPalauPennsylvaniaPuerto RicoRhode IslandSouth CarolinaSouth DakotaTennesseeTexasUnited States Minor Outlying IslandsUS Virgin IslandsUtahVermontVirginiaWashingtonWest VirginiaWisconsinWyoming
Industry - None -Academic & ResearchAerospace & DefenseDentalHealthcareManufacturing & PrototypingTransportation & Motorsports
Sub-Industry - Select -Medical Device ManufacturersMedical Contract ManufacturersHospital or Medical ClinicMedical SchoolsOther HealthcareDental ClinicsDental Equipment ManufacturersDental LabsDental SchoolsOther DentalMilitary AviationCommercial AviationDefenseSpace & UAVOther Aerospace & DefenseAutomotiveTruck, Bus & RailMotorsportsAftermarket & ServiceRecreation & MarineOther Transportation3D Printing Service BureausFoundriesElectronics & ConnectorsSemiconductorTurbomachineryJewelryConsumer & Durable GoodsOther Manufacturing
Address
Postal Code
Job Level -- Select Job Level --C-LevelPresident or VPDirectorManagerProfessional StaffConsultant or ContractorIntern or StudentHobbyist
Job Function -- Select Job Function --Engineering - SoftwareEngineering - HardwareManufacturingFinanceITLegalMarketingPurchasingSalesService Technician - HardwareService Technician - SoftwareOther
Level of Interest -- Select Your Level of Interest --Beginning ResearchEvaluating Solutions and CompetitorsInterested in Buying in 1-3 MonthsInterested in Buying in 3-6 MonthsInterested in Buying in 6-12 MonthsI would like to speak with a Solutions SpecialistI have a Support Issue or Question
Area of Interest - Select -Printers• Professional Printer (ColorJet, MultiJet)• Production Printer (SLA, SLS, Metal/DMP)• Figure 4• Titan Additive• OtherSoftwareHaptics• HapticsHealthcare• Virtual Surgical Planning• Anatomical Modeling• Kumovis Additive
3D Printer - Select -MJP• ProJet 2500• ProJet 2500 Plus• ProJet 2500W• ProJet 2500 IC• ProJet 3600• ProJet 5600CJP• ProJet 260 Plus• Projet 360• ProJet 460 Plus• ProJet 660Pro• ProJet 860ProDMP• DMP Flex 100• ProX 200• DMP Flex 200• DMP Flex 350• DMP Factory 350• DMP Factory 500• ProX 100• ProX 300SLS• SLS 6100• SLS 380• sPro 140• sPro 230SLA• SLA 750• ProJet 6000• ProJet 7000• ProX 800• ProX 950Figure 4• Figure 4 Standalone• Figure 4 Modular• Figure 4 Production• Figure 4 JewelryNextDent• NextDent 5100Kumovis• Kumovis R1Atlas• Atlas H• Atlas HSMaterialsBioprinter
Software product - Select -3D Connect Manage3D Connect Service3D Modeling Services3D Sprint3D Sprint Pro for SLA3DXpertGeomagic Control XGeomagic Design XGeomagic for SOLIDWORKSGeomagic FreeformGeomagic SculptGeomagic TouchGeomagic Touch XGeomagic WrapOpenHapticsPhantom Premium
Area of Interest - Select -Medical Device Design and ManufacturingMedical SimulatorsAnatomical ModelsD2P SoftwareDental Manufacturing and Design Services
I consent to receive 3D Systems CommunicationsWould you like to receive special offers, product updates, and event news from 3D Systems? By clicking "Yes", you agree to receive follow-up communications from 3D Systems or our partners. You can also choose to opt out of communications at any time. Please click here to view our Privacy Policy or click here to manage your Preferences.
Area of Interest - None -Appearance ModelsCast UrethaneCJPCNCCNC MetalCNC PlasticDie CastingDigitalization/ScanningDMPEngineering ProjectsFDMInjection MoldingInjection ToolingInvestment CastingInvestment Casting PatternJigs and FixturesMetal CastingMJPMJP-ElastomersQuick Cast PatternsRIMSheet MetalSLASLSToolingVacuum castingVacuum forming
Custom Area of Interest
PPP
PST
Software
Healthcare
ODM
Area of interest Required
This site is protected by reCAPTCHA. The Google Privacy Policy and Terms of Service apply.
Industrial 3D printer CreatBot D600 for large parts. FDM 3D printing of car parts. Business Ideas 2020
Contents:
- 1. The choice of material and characteristics of the stand.
- 2. Selecting a 3D model for printing and setting up a slicer.
- 3. Filling the plastic and preparing the printer.
- 4. Calculation and sending for 3D printing of a BMW rim.
- 5. Printing process.
- 6. Part removal and post-processing.
- 7. Total.
Hello everyone, Friends! 3DTool is with you!
Quite often we are asked the question, is it possible to print a bumper for a car on a 3D printer? And this is not a common meme among 3D printers, or some kind of boring joke, for example, representatives of a tuning studio really ask such questions first of all when they are interested in additive technologies. Well, we decided to print something really impressive in one run and evaluate how suitable FDM 3D printers are for such tasks? 9 was chosen as a stand for the experiment.0023 3D printer Creatbot D600 PRO is one of the most powerful and generally affordable printers. Let's see step by step what's what.
1. Selection of material and characteristics of the stand.
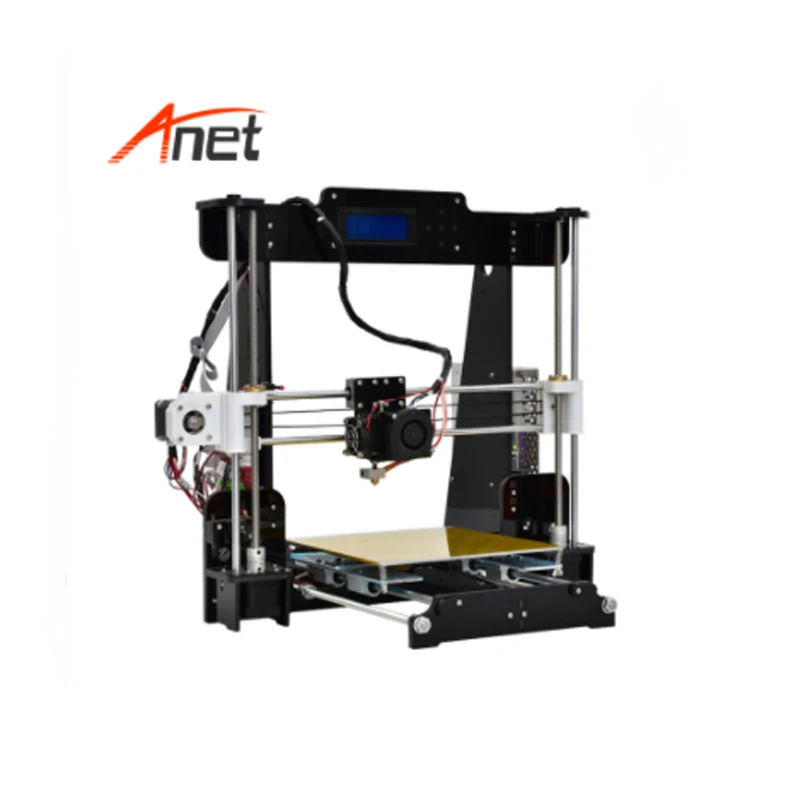
Let's pick the material first. It is not difficult to guess that this stage is characterized by the capabilities of the existing device. As a rule, large products are always printed from polymers with low shrinkage and not subject to delamination, such materials as PLA and its derivatives. However, this approach is only a tribute to the limitations of the first kinds of available models FDM 3D printers, for the most part, did not have closed chambers and even heated tables.
When it comes to professional devices, or even industrial ones, which is our bench Creatbot D600 PRO , such questions fade into the background.
A little about the printer.
You can find a detailed review of Creatbot D600 PRO on our website in the articles section on THIS link. We will confine ourselves to quoting its characteristics.
As you can see, Creatbot supports almost all materials available on the market, with the exception of very rare ones. So in the material we are not limited, but what if something goes wrong? It is better to choose the most affordable filament so that the cost of a mistake is not so painful. This means that we reject various composites and engineering thermoplastics.
Since the print is really voluminous, it is quite possible that we will need post-processing as well. So, based on the foregoing, our requirements are best suited to the beloved by domestic printers ABS .
Although this material is quite difficult for beginners, thanks to the chamber heating system, a powerful heating table and a productive all-metal extruder, printing this material on the CreatBot D600 PRO 3D printer should not cause any difficulties. In addition, we will use the well-proven adhesive from the company Picaso3D -
However, you can use the option that suits you best. For example, bundled with device PVA glue stick.
Well, we figured out the material, chose the adhesive, we have at our disposal 0. 2 cubic meters of working chamber volume, two extruders and a choice of different nozzle diameters. What to print?
2. Selecting a 3D model for printing and setting up a slicer.
Let's start with the subject itself. Best of all, the dimensions of the print and clarity will be demonstrated by an ordinary rim of a car. And although it will be an impossible task to install it on the car due to the chosen material, it will be much easier to compare the dimensions with a real object.
Open Thingiverse and select a disk, for example from BMW.
Before us is a complete copy of the object with realistic proportions and thicknesses. Now it's time to load the program and scale the model according to the real prototype.
We will work in the slicer Ultimaker Cura 4.4 . Initially, CreatBot 3D printers are designed to work in their native software CreatWare , but we are often asked to show the configuration of alternative slicers for working with such devices and we decided to demonstrate it.
First, let's open the bundled CreatWare .
In the menu Machine -> Add New Machine select the source printer.
Now let's open its settings and fix them in memory, or write them in a notepad.
After that, open Cura 4.4
Initially, our device is not in this program and first we need to add it. We go at Settings -> add printer -> add a non net-worked printer
And in the drop-down menu, select the scroll Custom .
In order not to get confused, enter the real name of the device in the field Printer Name and click add .
After that, a new device will be added and we can proceed to its configuration.
By pressing Machine Settings we will open the printer settings menu and now it's up to the small. Transfer settings step by step from the parameters we saved to Create Ware , as well as enter a suitable starting G-code . In CreatWare, you can find it in the star/End-Gcode tab. It is fully syntactically compatible with Cura, since in fact both programs use a common engine.
After copying all the settings, you should get the following result:
Note that we have already set the diameter of the second nozzle to 0.6 mm because We are planning volume printing and productivity is critical for us.
The next step is to check whether we have configured everything correctly, and whether our printer is also calibrated.
We will not dwell on the settings of Cura 4.4 in detail, because this is a topic for a separate large article, just select advanced settings and specify the required minimum parameters for our printing.
Because we set the nozzle to 0.6 mm , layer thickness will be 0.3 mm , thread width 0.7 mm , infill approx. 20% and Overlap infill approx.
Cura 4.4 uses a profile system for the material, which means we will need to create a new profile for our plastic.
To do this, open Settings -> Extruder ½ -> Material -> Manage Materials
Select the base material and click Duplicate .
In the dubbed material, remember to change the name Display Name and temperature settings Print Settings
Now we can assign this material to our extruder.
Let's check whether everything turned out right and send a test file for printing.
Open the model and press Slice , we selected the print settings in advance. It is important to say that we will be testing printing with two extruders, but in the future we will need only one.
The resulting G-Code is saved to a USB flash drive and inserted into the printer.
3. Filling the plastic and preparing the printer.
Time to fill the plastic and calibrate the 3D printer .
First, install the plastic spool ABS from ESUN . The compartment for plastic in the CreatBot D600 PRO printer is located at the back in a special niche, for each coil separately.
We stretch the thread along the guides and catch it at the output of the printing unit. It is problematic to do this operation alone, so we will resort to the help of colleagues. So, the thread is in place.
We thread it into the hole of the broaching mechanism and select the menu Load Material 9 on the display0116 .
Don't forget to change the plastic temperature in menu Status as The default temperature may not be sufficient.
Excellent! We got through almost everything.
Let's calibrate the table and start printing.
Creatbot D600 PRO is equipped with a special sensor that allows you to adjust the level of the desktop in auto mode - BL Touch .
So our task is greatly simplified. Simply run Auto Leveling from the display menu and verify that the calibration is correct.
To do this, we print our test task and check the result.
Everything seems to work out, let's move on to the final part of the story.
4. Calculation and sending for 3D printing of the BMW rim.
We are almost ready to start our grand seal. It remains to do a couple of last steps.
First, let's determine the size of our disk. Let its diameter be 17 inches.
By simple calculations, we get the result:
Which is equal to ~ 431 millimeters. Let's scale our model in the program.
As you can see, the model fits perfectly in the workspace, but let's still compress it in height to get a more or less sane print time, because. we are limited in terms of the execution time of the experiment. Seems like 120 mm will be enough with prosperity.
We leave the print settings that we set at the beginning, however, we additionally include support:
We decided not to use the second support material, because the result was unpredictable and I did not want to spend the rather expensive Hips . In addition, it is a pleasure to remove support from a product of this size and we use only 1 extruder.
Press Slice we get a pretty good result:
After checking on Preview whether everything was cut as it should, we will send G-code to the printer.
5. Printing process.
So, after the printer has warmed up, it will automatically check the level of the table again and start printing. The most important thing now is to check the correctness and evenness of the printing of the first layer and periodically monitor the process in the future.
Never leave long-duration devices completely unattended. Though D600 PRO and has the necessary assistance and control systems, such as shutdown protection with the ability to start from the same place when printing was interrupted, you cannot leave the printer completely alone.
It is best to check the process every 5 - 10 hours , or install a webcam.
So. Let's follow our progress.
A little more and the disc will be ready ..
6. Part removal and post-processing.
After our part is ready, we remove it from the platform.
A fairly large layer of 300 microns is not very good quality, so we will use the acetone surface smoothing technique. To do this, we need a spatula and wire cutters to remove the supports, a brush and a bottle of acetone.
Pour acetone into a convenient container, dip the brush and gently smear the surface of the disc. The process should look something like this:
Also, you can combine this technique with sanding and further painting to achieve the perfect result.
You can read more about post-processing in THIS article of ours.
Well, as a result of our efforts, we got such a natural rim.
And here it is, but in comparison with the real one.
Let's summarize the process of our experiment.
7. Total.
For ourselves, we wanted to answer the main question - is it possible to print large objects made of complex plastics 3 D in almost the entire print area of the FDM 3 D printer?
Experience has shown that it is possible.
Is it possible to print bumper on 3 D printer?
- It is possible, but it will have to be done in parts, albeit large ones, and in any case, post-processing will be required. And also the material will have to be additionally reinforced, because. At this scale, ABS is still quite fragile.
Is 3 D printer Creatbot D600 PRO suitable for auto-tuning or printing parts?
- This is highly dependent on the specific task, however, everything indicates that the capabilities of this device are enough to solve many problems associated with 3D printing with refractory plastics in large sizes.
Well, personally, the result seems successful to us. What do you think?
Write your opinions below in the comments.
And that's all we have! See you soon!
You can purchase the Creatbot D600 PRO 3D printer from our company. We are the official distributor of the manufacturer's plant for the sale and service of CreatBot3D equipment in the Russian Federation.
Our contacts:
• By email: [email protected]
• By phone: 8(800)775-86-69
• Or on our website: http://3dtool.ru
Also, don't forget to subscribe to our YouTube channel:
Subscribe to our groups in social networks:
In contact with
5 Ways 3D Printing Is Changing the Automotive Industry / Sudo Null IT News
You can't buy a fully 3D printed car in a car dealership yet, but additive technologies have been used in car design for many years. Every year, especially in recent years, 3D printing is taking an increasingly important place at all stages of production. This is evidenced by the rapid growth of 3D printing market share in automotive manufacturing, which is projected to reach $2.5 billion by 2023.
For example, luxury car companies including Bentley, Porsche, BMW and Ferrari are using 3D printing to create custom car interior parts. GM, Volvo, Ford are using 3D printing to produce tooling to save money, improve designs and reduce delivery times.
Source 3dprinting.com
3D printing is constantly emerging with new opportunities, it is becoming more accessible. If the first 3D printers cost about $20,000, now you can find 3D equipment for $100. Now companies can, with the help of additive technologies, produce the necessary components directly at their own enterprises and not depend on suppliers.
With new materials, 3D printers can print highly precise, functional end pieces. Additive technologies facilitate the production of custom products and increase productivity.
But this is only the beginning of the journey. Here are five key ways 3D printing is driving innovation in the automotive industry, from car design to production. Plus one bonus.
1. Changing the prototyping process
It was with the manufacture of prototypes that the use of 3D printers in the automotive industry began. 3D printed prototypes took much less time than traditional methods required.
Using Raise3D 3D printers and ideaMaker software, Crazy Grandpa Garage was able to automate the process of creating custom car parts. Production costs have been reduced by 50%, design reliability has improved significantly, and lead time has been reduced by 83%. The parts now come out very well fitted to the car.
Source: facebook.com
Using 3D printing, car designers can quickly prototype individual parts or assemblies, from interior detail to dashboard, or even full-size car models. Thanks to 3D prototyping, the initial idea quickly turns into a physical embodiment of the concept - a conceptual model. The concept can then be developed into full-featured, high-fidelity prototypes, and after several validation steps, mass production begins. For the automotive industry, getting through these steps quickly is vital, and the entire downtime of an automobile production line in just an hour is very costly for the company.
For example, the assembly plant of the American car manufacturer General Motors claims that the purchase of a 3D printer in 2016 saved more than $300,000.
Ringbrothers designers and engineers are not dependent on third parties to implement laser stereolithography (SLA) in their facility. The cost is reduced, the development time is reduced. Source: formlabs.com
Hose for Eventuri BMW M4, Source: ultimaker.com
Traditional prototyping was time-consuming and costly, in part because the product went through more iterations. With 3D printing, you can create high-quality prototypes in one day and at a much lower cost. More examples.
The Ford Fiesta ST with 3D printed parts, ext. SEMA 2016, ultimaker.com
For example, General Motors has partnered with Autodesk to produce low cost, lightweight automotive parts using 3D printers. Tools, fixtures and fittings can now be produced at a fraction of the cost, according to Autodesk. For example, a 3D printed tool used to align engine and transmission ID numbers costs less than $3 at General Motors. A traditionally produced instrument will cost $3,000. In addition, downtime due to faulty tools can be significantly reduced as new tools are produced in-house.
2. Creating custom and complex parts
Daihatsu, Japan's oldest car manufacturer, launched a project in 2016 to customize its Copen model.
Source: 3dprint.com
In partnership with Stratasys, Daihatsu customers can design and order custom 3D printed panels for their front and rear bumpers with a choice of over 15 basic patterns in 10 different colors.
Source: 3dprint.com
In Europe, the BMW MINI brand also uses 3D printing to create personalized car parts. Since the beginning of 2018, MINI customers have been able to personalize various trim elements such as the instrument panel, LED treadplates and illuminated bumpers, as well as choose from different colors and textures. These parts are then 3D printed using a range of technologies from DLS Carbon to SLS.
Source: formlabs.com
Volkswagen Motorsport's I.D. R Pikes Peak is designed with over 2000 3D printed test parts.
Source amfg.ai
The use of 3D printers makes it possible to experiment in the development of non-standard designs, reduces the cost of their production. Long production processes for custom-made products are becoming much shorter.
Ringbrothers uses 3D printing to create customized end pieces, such as ventilation grilles. Source: formlabs.com
Large companies are merging 3D printing technologies with traditional manufacturing methods. Volkswagen has recreated its iconic 1962 Microbus by replacing the petrol engine with a 120 hp electric one. The Type 20 concept electric minivan has received many improvements using 3D printed parts. These improvements include cast aluminum wheels. Even the wheel hubcaps, while looking like stamped steel, are actually printed on a Formlabs SLA 3D printer, then electroplated and polished. 9another example Bentley has used cutting-edge metal 3D printer technology to produce a grille, side vents, door handles and exhaust pipes much more complex than those used on current production models.
Bentley used metal 3D printing to create intricate micron precision parts. Source: formlabs.com
Source: youtube.com
3D printing has also made it possible to create parts that could not be made in any other way.
Bugatti's monobloc brake caliper is a prime example. For some components, Bugatti would have preferred titanium due to its high performance, but processing this metal with traditional methods is expensive and difficult. 3D printing has allowed Bugatti to produce a titanium alloy brake caliper. Due to the thin walls, the caliper turned out to be very light - almost two times lighter than forged aluminum. At the same time, the strength of the 3D-printed monoblock is superior to that of aluminum. The 3D printed titanium monoblock has a tensile strength of 1250 N/mm2. This means that a force of just over 125 kg will be applied per square millimeter of this titanium alloy without tearing the material. The new titanium caliper is 41 cm long, 21 cm wide and 13.6 cm high and weighs only 2.9kg compared to currently used aluminum, which weighs 4.9 kg.
Source: youtube.com
The Bugatti brake monobloc is the industry's largest functional 3D printed titanium component for a car. Source: formlabs.com
3. Tool making
Various devices help to facilitate and speed up the production and assembly processes, improve the safety of workers. Automotive factories and component suppliers use a large number of non-standard tooling that is specifically designed and optimized for end use. As a result, a lot of non-standard equipment and tools are made, which increases production costs.
This 3D protective wheel disc was purchased for 800 euros but can now be printed for just 21 euros. Tool development time has been reduced from 56 to 10 days.
Source: ultimaker.com
Delegating custom tooling and fixtures to service providers who machine parts from solid metal or plastic stock can delay production by weeks.
For example, a commutator motor can take up to four months to develop and prototype using conventional manufacturing techniques and cost about half a million dollars. Thanks to 3D printing, Ford was able to develop several variants in just 4 days and 99.4% cheaper - only $3,000.
Source: youtube.com
Additive technologies allow you to complete the task in a few hours and significantly reduce costs compared to ordering from a third-party enterprise. Since increasing the complexity of a 3D printed model does not incur additional costs, products can be better optimized for their application. New elastic materials for 3D printing in many cases allow you to print plastic parts instead of metal or create prototypes on a 3D printer to test the tool before using it in production
Gradually, the production of 3D printed accessories and tools is becoming one of the largest applications of additive technologies.
Pankl Racing Systems uses 3D printed fixtures to fasten workpieces to a conveyor belt. Source: formlabs.com
For example, Pankl Racing Systems uses multiple Formlabs SLA 3D printers to make critical manufacturing tools. The multi-stage production of parts for transmissions on automatic lathes requires a series of fixtures and tools designed for each specific part.
With the help of 3D printing, Pankl's engineers have reduced the production time for the aids by 90%, from 2-3 weeks to around 20 hours. Costs were also reduced by 80-90%, saving $150,000.
The shift to 3D printing has helped Volkswagen Autoeuropa cut tooling development costs by 91% and tooling times by 95%.
4. Troubleshooting Parts
Spare parts have always been a problem for the automotive industry. The demand for them is either there or not, so the production of spare parts is not economically viable, and the storage of pre-fabricated replacement components is also costly. But if there are no repair parts available, difficulties arise and the main product becomes less valuable.
3D printing could solve the problem of parts in the automotive industry in many ways. The main factors are printed materials, which can match the characteristics of traditional materials used in parts and be cost-effective. There are prerequisites for this.
Using computer-aided design, drawings of all parts can be stored digitally, so there is no need to store the parts themselves. The parts needed by the client can be printed on a 3D printer right in the workshop.
Even obsolete parts whose drawings have not been preserved can in principle be recreated by making a 3D scan of existing parts of this type and applying reverse engineering (reverse engineering). You can read more about this on our blog. Old projects can take on new life. There are many lovers of vintage cars, with the help of 3D printing it would be possible to create parts for them.
Ringbrother 3D printed the Cadillac emblem for a custom built old car. Source: formlabs.com
5. Production of standard parts
As 3D printers and materials for 3D printing become more affordable, a gradual transition to the production of mass-produced automotive parts using additive technologies is possible.
3D printing makes it possible to combine components into a single whole. Let's say there is a mechanism assembled from six or seven car parts that can be combined into one printed part. It will save time and assembly costs. With 3D printing, it is also possible to reduce the weight of the combined assembly, as a result, the car will use fuel more efficiently.
3D Systems has developed an advanced exhaust pipe for a sport bike. In the image below, you will see 20 sheet metal and hydroformed parts needed to assemble the original exhaust pipe. On the right is a monolithic exhaust pipe that does not require assembly, made using metal 3D printing.
Source designnews.com
The 3D printed tube was produced using Grade23 titanium in just 23 hours, compared to three weeks for traditional production. Design development time reduced from 6 weeks to 6 days. Additive manufacturing also eliminates the need for tooling, fixtures, multiple welding and multiple inspections.
Geometry optimization has reduced the amount of material required for maximum productivity. All elements of the original exhaust pipe are incorporated into the new design and, when printed with a typical wall thickness of 0. 5mm, the 3D printed exhaust pipe is about 25% lighter than the original one.
A wide range of 3D printing materials is beginning to meet the requirements of various vehicle components. Since additive methods reduce costs compared to traditional methods (such as molding and injection molding), it makes a lot of sense from a production and financial point of view to further introduce 3D printing into the production of basic parts.
Volkswagen, one of the world's largest and most innovative car manufacturers, is using an HP Metal Jet 3D printer to produce high-performance functional parts with special design requirements, such as shift knobs and mirror mounts. Volkswagen's long-term plans to work with HP include accelerating the production of mass-customized parts such as key rings and exterior nameplates.
Source: youtube.com
+1. 3D printed cars
While 3D-printed cars have yet to hit the market, there are some interesting designs and concepts that can suggest a possible direction for the automotive industry.
Light Cocoon . German engineering firm EDAG was clearly inspired by nature to create the 3D printed supporting structure of the Light Cocoon concept car. The frame resembles the veins of a tree leaf or its branch. Despite the fact that the design of the EDAG took less material than a conventional frame, all the strength requirements for structurally significant components are met. Outside, the case is covered with a lightweight and durable waterproof fabric.
The cover protects EDAG Light Cocoon from bad weather and gives the car a unique personality. Source: formlabs.com
Blade . Blade ("Blade") announced as "the world's first 3D-printed supercar." It meets supercar standards but is made from inexpensive materials: carbon fiber tubes and aluminum rods, combined with 3D printed metal parts. Blade turned out to be very light and does not take long to assemble.
The world's first 3D printed Blade supercar. Source: formlabs.com
Strati . The American company Local Motors 3D printed and assembled the Strati electric car right at the exhibition stand, in just 44 hours. Most of the components were printed - the body, seats, interior parts. A car is made up of less than 50 assemblies, far fewer than the thousands of parts that go into a traditional car. The company intends to reduce the print time to 10 hours.
The Strati from Local Motors consists of less than 50 individual parts*. Source: formlabs.com
LSEV. Developed by the Italian company XEV, the LSEV could be the first in the 3D printed electric vehicle market when it goes on sale. The 3D printed chassis, seats, windshield and all visible parts of the LSEV. Thanks to the active use of 3D printing, the number of components was reduced from 2000 to just 57, resulting in a very lightweight design. The electric car weighs only 450 kg.
The LSEV is the first 3D printed electric vehicle to hit the market in 2020.
Learn more