3D printed house equipment
First 3D printed house in Borneo
- In the Press&
- Press Release
- 3D printed houses have sprung up all over the world, and has now reached even places like Borneo
- Precasting specialist SCIB, located in the Malaysian part of Borneo, revealed their first 3D printed house built using a BOD2 3D construction printer from Danish COBOD International
- The house is a 1000 square foot 3D printed house completed in only 46 hours
In the Northern coastal part of Borneo, which is more urbanized than the rainforest covered center, the large concrete pre-casting company Sarawak Consolidated Industries Berhad (SCIB) recently revealed their first 3D printed demo house in Sarawak.
The house consists of a built area of 1000 sq ft (90 m2), had a total printing time of 46 hours and was 3D printed using the BOD2 3D construction printer from Danish based COBOD International. The total length of the print was over 9 km that were extruded layer by layer on top of each other in a total of 145 layers each of 2 cm height. The SCIB team chose to plaster the outside walls of the house, which is normal practice in the region due to high humidity weather conditions. Also, plastering makes it easy to wash and clean when green algae grow on the walls which occurs due to the climate conditions.
The 3D construction printer SCIB used was supplied by market leader COBOD International, who’s printers have proven their worth around the globe from India, over Middle East, Africa and Europe, to North America, where COBOD 3D printers recently were used in two story buildings in Texas and Ontario.
Simon Klint Bergh, Head of Asia-Pacific for COBOD and located at COBOD’s regional office in Kuala Lumpur said: “When we created COBOD, we never envisaged, that we would have a market in a place like Borneo. The fact that our technology is now applied there shows, that the market for our technology is endless. When we can sell our printers in Borneo, we can sell them anywhere”.
The new 3D printed house in Borneo is located on the premises of the Malaysian Construction Industry Development Board (CIDB), which is the permitting body in Malaysia, at their training arm premises Malaysian Construction Academy (ABM) in Kuching, Sarawak (Malaysia) and was built in collaboration with the agency.
Group Managing Director and Chief Executive Officer of SCIB, Rosland Othman, said: “The use of technology such as 3D printing comes at a time when businesses are being scrutinized for the impact of their operations on the environment and society. Businesses have an important role in society and an important part is to operate responsibly. We believe 3D construction printing can be part of this and therefore we are also involved in a program with our university partner to develop and improve the skills and knowledge of the construction industry.”
Simon Klint Bergh concluded “At COBOD International we are proud to have SCIB as our customer and to see them execute a first building. SCIB is a very innovative company and with our technology, we are excited to see SCIB enable faster execution of construction projects, as well as more efficient construction at a lower cost. This will be the first of many 3D printed houses to come in Asia- Pacific”.
Image caption: The house was printed with a BOD2 3D construction printer from COBOD International 3D Construction Printer in Sarawek, Malaysia.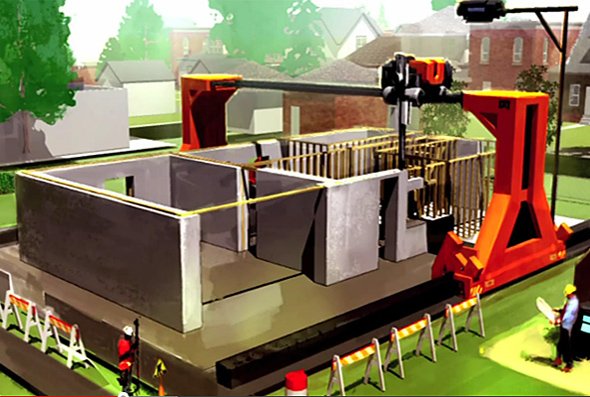
Largest 3D printed building in Africa
- Power2Build finished their second and largest 3D printed building yet in Angola with the BOD2 construction printer.
- 140 m2 house printed 4,5 times faster than the first 3D printed building Power2Build made.
- D.fab concrete solution from COBOD International and CEMEX enabling cost-saving up to 90% – first shown in Angola, now spread all over the world.
- COBOD completely dominates the 3D construction printing market in Africa with the six 3D printed buildings, all done with COBOD technology.
Power2build have recently finished their largest 3D printed building with a COBOD BOD2 construction printer in Angola. The company has set out to transform the housing market and are pioneers aiming to solve affordable housing in Angola with 3D printed buildings.
The house is the second 3D printed residential building in Angola. It is a 140 m2 house that holds a suite, two bedrooms, three bathrooms, a dining room, and a living room. As the three bathrooms indicate, this is not a social housing project, but rather a house showcasing the design and architectural possibilities of 3D printed buildings.
Power2build is working with COBOD’s 3D printing technology to significantly reduce the housing shortage in Angola. The 3D printing technology is an innovative method that allows construction of affordable and high-quality housing in the region in a faster and more competitive way.
Power2Build printed Angola’s first 3D printed building – a 53 m2 house. This was an incredible milestone, marking the beginning of a revolution, as the house was the world’s first 3D printed house in real concrete (defined by particle size above 8 mm).
While the first house was printed in 48 hours, the second house with 140 m2 was printed in 30 hours. This equates to a 4,5 times improvement in productivity. In addition to this, the team was able to both do the printing, and the water and electrical installations at the same time.
Ricardo Almeida, CEO from Power2Build said: “We are very proud of our progress; people were questioning if we couldn’t print bigger. We have now printed a 2,6 times bigger house and in about 2/3 of the time compared to the first house. We improved the speed of execution remarkably, but still believe there is room for improvement. In the future we will only become better at mastering this technology. We are getting more efficient by the day and closer to achieving our vision to deliver better housing at affordable prices to Angolan families.”
Angola was the first country in the world that printed with the D.fab solution from COBOD International and CEMEX, making printing of real concrete possible.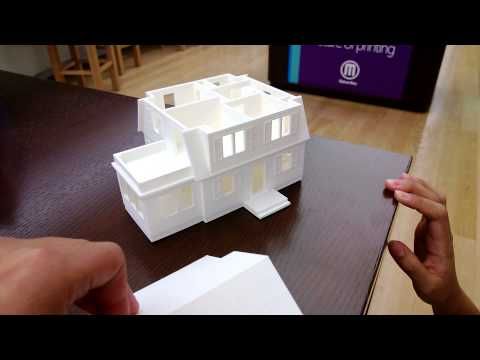
The 3D printed house was done with the D.fab material solution, a ground-breaking additive mix developed by COBOD and CEMEX, that enables printing with real concrete, leading to cost-savings of up to 90% compared to printing with mortars. D.fab enables the usage of 99% locally available materials and only 1% Magic Mix supplied by COBOD. 3D printing with real concrete is a genuine step change in the industry of 3D construction printing and serves as a prominent gateway to properly commercializing the technology.
Commenting on the successful build of the house, Henrik Lund-Nielsen, Founder & General Manager of COBOD International said: “We are proud to have made the technology for this project. Power2Build have increased their speed of execution tremendously compared to their first and now second project. This is a great example of how we and our customers are continuously improving the technology and can build faster, better, and cheaper as our customers and partners become experts at mastering the 3D printing technology. ”
COBOD International’s 3D construction printing technology is dominating the market in Africa, which so far has six 3D printed buildings all done with COBOD technology. The company was the first (and only) to print in Malawi, Madagascar, Kenya, and Angola, two of which are schools and four residentials. Later this year COBOD’s customer 14trees will begin printing a double-digit number of houses in Kilifi in Kenya.
In the front: the second and larger 3d printed building 3D printed 4,5 times faster compared to the yellow building in the background, which was Power2Build’s first 3D printed house. Image courtesy: Power2BuildWorld leader in 3D construction printing solutions with +50 printers sold world-wide.
COBOD’s mission is to build smarter through multifunctional construction robots based on 3D printing technology and COBOD’s vision is to automate minimum 50% of construction processes on building sites. All leading to better, faster, cheaper and more sustainable construction than conventional concrete. We constantly strive to reduce the co2 footprint of 3D printed concrete.
COBOD’s 3D printers made Europe’s first building in 2017. Subsequently our printers made the first 2- and 3-story buildings in Europe (Belgium & Germany), North America (US & Canada) and India. Also, the first 3D printed villa in Dubai and buildings in Africa have been done by COBOD 3D construction printers, just like the first wind turbine bases.
COBOD has an open-source material strategy, partnering with customers, academic institutions, and suppliers around the world.
COBOD is privately owned by General Electric, CEMEX, Holcim and PERI as key shareholders, and our partners further include Dar Al Arkan (Saudi Arabia), L&T Construction (India), JGC (Japan), Siam Cement (Thailand) and Orascom (Egypt).
COBOD is headquartered in Denmark with regional offices and competence centers in Florida and Malaysia. Our team consists of +100 passionate pioneers from 25 nationalities and through our installed base of printers, we have a truly global presence in North- and Latin America, Europe, the Middle East, Africa, and Asia-Pacific.
Video of Power2Build house: https://youtu.be/zRKVQ6SNLlI
Examples of positive and negative applications of the 3D printer
Every year 3D printing becomes more and more popular. The 3D printer, as a tool for turning a digital model into a physical object, is gaining popularity, outperforming other production methods in many ways due to its affordability.
But do not forget that a 3D printer is just a tool. A lot depends on how this tool will be used.
Available 3D printing technologies
All 3D technologies can be conditionally divided into 4 types.
Layer by layer welding with molten material.
The principle of operation is similar to the familiar glue gun. The print media is melted to a semi-liquid state in the print head and applied with a nozzle to the print surface where it solidifies. This is how the finished 3D model “grows” layer by layer on the printing table. Not only thermoplastics can be used as consumables, but, for example, chocolate, icing, concrete, etc. nine0003
This is the most common type of printer. Inexpensive FDM printers are often used as home assistants. This is facilitated by an inexpensive price and a variety of consumables.
Selective curing of resin (photopolymer printers).
The material used is a photopolymer resin that hardens under the influence of UV radiation. As a source of UV radiation, a thin laser beam, a DLP projector or an LCD screen with a UV matrix, or any other design can be used. For example, some industrial 3D printers apply a photopolymer using thin nozzles and immediately illuminate it with a UV lamp. nine0003
Previously, these printers were quite expensive. Today, with advances in technology, photopolymer 3D printing has become affordable and photoresin printers have become popular as home hobby printers.
Selective bonding of powdered material.
On the print head of the printer there are several nozzles through which a binder is supplied, which is selectively applied to the powdered material. Various materials can be used as a material: for example, gypsum or metal powders. But gypsum is most often used. nine0003
Since dye can be added to the "glue" during printing, such printers are usually used for the production of color demonstration models or souvenirs.
Laser sintering of powdered materials.
The youngest technology, but with great potential for use in large-scale production. With the help of a laser or a heated print head, selective sintering of the metal powder occurs in an environment filled with an inert gas. nine0003
These are already serious industrial printers that are used for the production of functional metal assemblies and parts. Currently, such 3D printers are actively used in the aerospace industry.
Unethical use
3D piracy
Where there is duplication of objects, there are always disputes about copyright and piracy.
The production of any product is a long and painstaking work, and often more than one person. Before you get a finished decorative product, for example, a figurine, you need to think through everything to the smallest detail. Usually, before modeling, the artist draws a lot of sketches, the details of clothing and accessories are thought out. Only after that the 3D modeler gets to work and begins painstakingly recreating the 3D model. nine0003
Functional models are often redesigned by engineers after the prototype has been made. There can be a very long way between the initial idea and a stable working mechanism. And it’s very disappointing when such work is simply copied and posted in the public domain.
LEGO
It was one of the first mass manifestations of "3D piracy". At that time, 3D printing was only gaining popularity, and many users, having printed a dozen figurines, were looking for a useful application for a 3D printer. Given the low plastic consumption, the printed LEGO blocks were very inexpensive. nine0003
3D printed LEGO bricks
Despite the far from ideal surface, many were satisfied with such a copy. Some have argued that the accuracy of a home FDM printer is not enough for the bricks to fit well with the original LEGO, but for most users everything fit perfectly.
At the moment, LEGO is actively removing models that copy the original sizes of the famous bricks and men from the network. On popular sites, only custom elements of LEGO-men and LECO are left that are not the original size. nine0059
Custom heads for LEGO men
Games Workshop
Games Workshop, which produce the most expensive table soldiers in the world, sued Thomas Valenti (USA) back in 2012. Thomas has modeled, printed and made publicly available several miniatures based on the Warhammer universe. The court sided with Games Workshop and the models had to be removed. nine0003
3D Printed Chaplain
Chaplain 3D model from Warhammer 40k
Games Workshop went one step further by banning fans from creating art and other work based on the original settings and characters. As a boycott, users of the Warhammer 40,000 section on Reddit are proposing to abandon the company's products as much as possible - print game figures on 3D printers, use paints from other companies, or switch to other universes. nine0003
Hollywood
The production of modern films is not a cheap pleasure, and film companies try to recoup their costs not only by showing them in cinemas, but, for example, by producing souvenirs.
DreamWorks has an entire consumer goods division that helps recoup the cost of a movie if it fails at the box office. Film companies recognize that fan-made productions often surpass the official "souvenir" in accuracy and detail. nine0003
DC Universe Batman fan model
Many film companies are closely following the development of 3D printed merchandise, but do not yet know how to respond. For example, Paramount Pictures, Marvel Studios and Warner Bros. They themselves began to upload models for 3D printing to the network, before the release of new films.
Weapon Seal
Seal of weapons
24-year-old law student Cody Wilson was the first to make a gun on a 3D printer. Cody designed and 3D printed a combat pistol on his own. After 8 years, the idea of making firearms using 3D printing has not only not died out, but flared up with a bright fire. nine0003
It started in Texas in 2012. It was there that the company Defense Distributed was registered, the ideology of which was the development of models of firearms that anyone could make on a home 3D printer.
Guns
Liberator
The first “swallow” was the Liberator - a compact plastic pistol printed on a 3D printer from ABS plastic. The only thing that could not be made on a 3D printer was the striker, which was successfully replaced by an ordinary nail. The first printed pistol was made on a Stratasys Dimension SST 3D printer. nine0003
Liberator - the name is borrowed from a cheap pistol that was developed in 1942 in the USA.
The Liberator fired a fairly weak .380 ACP round and could only last a dozen rounds at most.
Failed Liberator
Zig Zag
In the spring of 2014, a video appeared on the Internet with a man shooting from a plastic revolver with a huge drum. The video greatly stirred up all of Japan. nine0003
Zig Zag
Unknown was Yoshitomo Imura (Yoshitomo Imura) - 28-year-old employee of the Shonan Institute of Technology. Despite Imuru's claim that he fired blanks on the tape, he was arrested and sentenced to 2 years in prison.
The Zig Zag design was a reimagining of revolvers popular in the 19th century, which used a rotating .38 caliber barrel block mounted on a pistol grip. nine0003
Washbear
In 2015, mechanical engineering student James Patrick posted a video online showing a 3D printed PM522 Washbear in operation.
PM522 Washbear
The PM522 visually resembled a children's pistol from a science fiction movie, but at the same time the pistol had a strong and rigid frame. Washbear is also safer than its predecessors. At rest, the firing mechanism was not in line with the primer, so the PM522 was protected from accidental firing, for example, when dropped. The only metal part was the nail that replaced the striker. nine0003
Rifle
Grizzly
Canadian with the nickname CanadianGunNut, ThreeD Ukulele or simply Matthew, inspired by the Liberator project, designed and posted his project - Grizzly. Grizzly is an ABS+ plastic rifle. It took the Canadian 3 days to design the rifle and another 27 hours to manufacture it using a Stratasys Dimension 1200es industrial 3D printer.
Grizzly 9 Rifle0063
The first version of the Grizzly had a smooth and straight .22 barrel. But this turned out to be not a very good decision, and the barrel cracked after the first shot. Subsequently, Matthew replaced the barrel with a tapered barrel with rifling inside.
Plastic “cutting” could not affect the ballistics of the bullet in any way, but added strength to the barrel.
Shotgun
Liberator 12k
The Liberator 12k is a 12-round shotgun made by a well-known, in narrow circles, enthusiast in the world of 3D printing - Jeff Rodriguez. nine0003
Liberator 12k
Rodriguez managed to create a simple and at the same time reliable design, "mixing" a pistol and a pump-action shotgun in the design of the Liberator 12k. A huge plus for manufacturing and reliability was the absence of small parts in the shotgun mechanism.
Since the plastic was not strong enough, Rodriguez reinforced the design of the Liberator 12k with metal pins and added metal tubes inside the barrel and drum. The metal parts were purchased from a regular hardware store, so anyone could easily make a Liberator 12k with their home 3D printer. nine0003
Semi-automatic weapons
Shuty-MP1
The first sign was the Shuty-MP1, a semi-automatic pistol made by an amateur gunsmith with the nickname Derwood, in April 2017.
Shuty-MP1
Shuty AP-9
The Shuty AP-9 still uses a pistol barrel, but the trigger and return spring are taken from the civilian version of the M16. This improved the reliability of the rifle. nine0003
Ethical use
Despite the negative examples of application, 3D printing is actively used in many areas, helping to save time and create products that cannot be produced by other methods.
Medicine
Implants
Metal-printing 3D printers are actively used in medicine for the manufacture of titanium implants. For example, a patient needs to have a hip joint implant made. According to the results of CT, the necessary area of bone tissue replacement is agreed with the doctors and a prosthesis model is created that is ideal for this patient. After all approvals, the finished model is sent for printing. nine0003
3D model of implant
The main areas of 3D printing of implants in medicine are maxillofacial surgery, traumatology, orthopedics, oncology and veterinary medicine. A big advantage over classical methods of manufacturing implants is the ability to create a cellular or porous structure. This allows for better integration of the prosthesis into the bone tissue.
nine0062 Samples of printed implants and pins
Dentures
The manufacture of even a relatively simple traction prosthesis is a rather laborious and lengthy process. 3D printing has reduced costs and accelerated the production of prostheses. In addition, it became possible to customize the prosthesis.
Customized child prostheses
Some enthusiasts are modeling and posting models and detailed instructions for assembling traction prosthetic hands and fingers in the public domain so that any user can print and make a prosthesis at home. nine0003
Simple Traction Hand Model
Production
Building custom drones
Aerialtronics is a small Dutch company that specializes in building unique, customized drones. Aerialtronics manufactures and develops unique drones, the characteristics of which can vary depending on the needs of the customer. nine0003
Initially, a basic concept model was designed, which consists of a platform and a set of elements that can be changed at the request of the customer. Changes can affect almost any part of the drone. The customer can choose the number of motors and their power, payload, flight time, supported software and much more.
Aerialtronics base model
But any, even minor changes in the characteristics and design of the drone required the manufacture of new elements and design changes. Classical manufacturing methods turned out to be quite laborious and long. To save time and money, a Stratasys uPrint SE Plus 3D printer was purchased. nine0003
Drone Assembly
Thanks to 3D printing, it was possible not only to speed up production, but also to devote more time to improving individual components, because the finished model is ready the next morning. Rapid manufacturing allows you to print a part, test it, make the necessary changes to the 3D model and make a new sample. Aerialtronics engineers manage to manufacture and test 8-10 variants of a part in a few days in order to achieve maximum quality. nine0003
Prototyping
Gas turbine prototyping.
Prototyping by traditional methods is often time consuming and expensive. Because of this, the price of an error in calculations and 3D modeling can be very expensive.
For example, the production of turbine engine parts is usually based on careful preparatory calculations, but even this does not always prevent errors in the production of a test prototype. After all, even the most modern software methods cannot replace physical tests. But due to the high cost (over $20,000), it becomes impossible to produce multiple prototypes for testing. nine0003
Turbine Technologies (Wisconsin, USA) and its subsidiary Kutrieb Research have found a way out - 3D printing. Thanks to the 3D Systems ProJet 3D printer, it was possible to reduce the cost of prototyping by about 10 times to $2,000.
3D model and printed part of turbine
A turbine model is printed on a wax 3D printer, tested and then cast from metal. In addition to the cost, it was possible to significantly speed up production. After all, the production of traditional stencils with filling in molds took up to 5 weeks, and the 3D printed model is ready by the morning. nine0003
Totals
Despite the unethical side of 3D printing, there are still more positive use cases. 3D printers have become indispensable assistants in various industries - from home hobbies to serious industries. With the help of 3D printers, unique products are made that could not be obtained using other machines.
Popularization of 3D printers is a matter of time. But do not forget that 3D printing is just a tool, just like a drill or a hammer. It depends only on the user how it will be used. nine0003
Raise3D: using 3D printing to create furniture and interior items
With the advent of 3D printers, many advanced designers tried to use 3D technologies to create furniture and interior elements, but the first attempts were more experimental.
It has only recently become a real business idea with the advent of affordable professional printers that designers and small businesses can afford.
Janne Kitanen, a digital sculptor, has pioneered the use of 3D hardware for design creation, creating complex geometric objects with incredible designs, from exclusive platform shoes to chairs and even ping-pong tables. Despite the space cost (by the standards of a simple layman), Janne's products are sold out like hot cakes. nine0003
The cost of this sofa is $100,000
The main advantages of using 3D printing in this area are:
- new opportunities in design solutions;
- implementation of complex exclusive projects;
- cost is lower compared to traditional production methods.
Let's tell you about 3 designers who use Raise3D 3D printers to create interior and furniture items.
Wanhao Chai - designer and owner of Yujia Metal Science
Yujia Metal Science creates exclusive metal furniture, and Raise3D N2 is used to streamline manufacturing processes. Wanhao Chai says, “The 3D printer can improve efficiency and save labor costs. Products become clear visually already at the prototyping stage, you can see all the details and quickly make adjustments.»
Sofa printed on Raise3D N2
Yujia Metal Science creates metal household items: partitions, doors, windows, furniture, wine cabinets, metal decorations and other interior elements. Positioning itself as a designer furniture boutique and exclusive manufacturing, Yujia operates in a narrowly segmented direction - the manufacture of furniture and interior items according to individual order.
Yujia Metal Science turned to 3D printing to solve the main problem - to increase speed of production and frequency of new products./p> nine0003
Prior to using Yujia 3D printers, very expensive wooden prototypes were ordered to validate and validate models. This process was repeated before the steel version was made. repeatedly. Many factories do not welcome this format of cooperation with small-scale production, considering it not rational to spend time on the production of single prototypes. Therefore, Yujia often found themselves in a difficult situation and were rejected by companies due to small volumes of orders. nine0003
Using Raise3D 3D printers, the company has been able to:
- Reduce production time by using 3D printers, and by sharing prototype printing across multiple printers.
- Reduce costs by reducing labor required and using cheaper materials for prototypes.
- Move the production of prototypes and products entirely to your own production. Thanks to this, they got rid of the extra costs and uncertainty that were inevitable when working with outsourcing companies. nine0386
- Create the largest and most complex versions of your designs with the large printable area and high precision of Raise3D.
Production process:
Prototyping requires only product drawings, a slicer, printing plastic and Raise3D N2 printers. At the beginning, the required file is converted to STL, then the print preview is used to minimize the number of supports and optimize all layers, layout of elements, and the appearance of the model. nine0003
The purpose of printing the first model is to see the appearance of the structure. Using the printed prototype, the designer can physically interact with it, see all the nuances and shortcomings, decide on changes and quickly correct the model.
Metal parts and legs will be used in the final design of the chair
As a result of using 3D printers we have achieved:
- 91.67% reduction in total production time
- 75% reduction in working hours
- 99.17% reduction in prototype costs
Marco Rubini, Italian architect and designer
Prints furniture prototypes on the Raise3D N2 Dual Plus.
Marco founded his own design studio in 1992. His main areas of activity are design development and consulting in the field of architecture. It has always been important for Marco to offer his customers customized solutions, which N2 Plus is currently helping him with. nine0003
He uses Raise3D to print prototypes and original pieces of furniture in 1:1 scale.
What Marco values most about the 3D printer is its endurance and durability, seeing Raise3D as a workhorse.
Hanger 100% printed on Raise3D
Corey Zwerlin (Still Alive Lights LLC) - 3D printed lighting fixtures
Corey designs designer lampshades (including solar-powered lamps and LED lights). nine0003
On the Raise3D N2 Plus, he prints shades in the shape of animals, flowers and more. To achieve maximum transparency and the best light transmission, Corey adjusts the print settings to the smallest thickness of the model. For his creations, he uses ordinary PLA plastic.
Currently, 3D printing allows you to create complex objects of unusual shape, the production of which by other methods is the most expensive and difficult to implement. Additive technologies increase productivity and reduce material and labor costs, which is why many companies are already using 3D printing and 3D scanning to produce furniture and interior items.