3D printed bicycle frame
Canyon unveils sustainable concept 3D printed mountain bike prototype
0Shares
Bicycle manufacturer Canyon has debuted a concept 3D printed mountain bike prototype which aims to demonstrate a more sustainable method of bicycle production.
Working with software and 3D printing service provider Materialise, Canyon 3D printed the bike’s frame and fork as part of Bike Magazine Germany’s ‘Ride Green’ campaign. The finished bike was showcased at the recent Cycle Show in London.
The Ride Green bike
The aim of the Ride Green project was to design a bike that is as sustainable as possible, with all its components being fully recyclable. The materials used also needed to be reusable without compromising the quality of the parts produced, while reducing waste was another key goal of the project.
Canyon was tasked with building the bike’s cradle-to-cradle frame and fork, and settled on 3D printing as the most suitable, and sustainable, method of production. The firm enlisted Materialise’s selective laser melting (SLM) 3D printing technology to fabricate the components in order to achieve the frame’s desired unique shape.
Materialise is no stranger to the bicycle sector, having deployed its technology to print 2,000 parts for fellow bicycle manufacturer Pinarello’s Dogma F racing bike last year. In addition to achieving substantial weight reductions for a crucial seat clamp component for the bike, the company also created a full-service, customized production workflow for the project.
Canyon’s 3D printed bike frame. Photo via Bike Magazine.In order to meet the sustainability requirements of the project, the frame and fork were 3D printed from recycled aluminum powder. Canyon also wished to reduce the overall amount of raw material used in the fabrication of the frame, not only to improve the bike’s environmental impact but also to lower the frame weight and provide performance benefits.
The frame is comprised of a skeleton that forms its structure, which is enclosed within an outer shell to provide additional protection and more desirable surface properties.
The frame was 3D printed in three pieces, each taking around six hours to produce. Once printed, the frame and fork weighed just 2 kilograms. While Canyon says there are currently no plans for the bike to enter production, the project could potentially influence how the company’s future models are designed and manufactured.
The bicycle frame was 3D printed in three parts and glued together. Photo via Bike Magazine.Boosting cycling performance with AM
Given 3D printing’s ability to consolidate multiple parts into single lightweight components and produce components with previously unachievable geometries, the technology’s benefits have been increasingly realized by bicycle manufacturers in recent years.
For instance, custom bicycle producer Sturdy Cycles has switched the production of its titanium bicycle parts to Headmade Materials’ Cold Metal Fusion (CMF) technology, and has previously worked with RAM3D to print parts for its road bikes. British Cycling even enlisted Renishaw’s help to 3D print aluminum and titanium parts for its new track bike on show at the Tokyo 2022 Olympic Games.
Meanwhile, some 3D printing firms have taken to kickstarter to launch their 3D printed bicycle components, such as Headmade Materials and Element22 who launched their jointly-developed novel Titanum 3D printed bike pedal design on the platform last year.
Elsewhere, the likes of Fizik and Specialized have used Carbon’s DLS 3D printing technology to improve the weight and comfort of their saddles, while Stratasys’ h450 machine has been used by DQBD to produce fully personalized 3D printed saddles that offer increased performance efficiency.
The Argo Adaptive short-nosed saddle’s 3D printed lattice.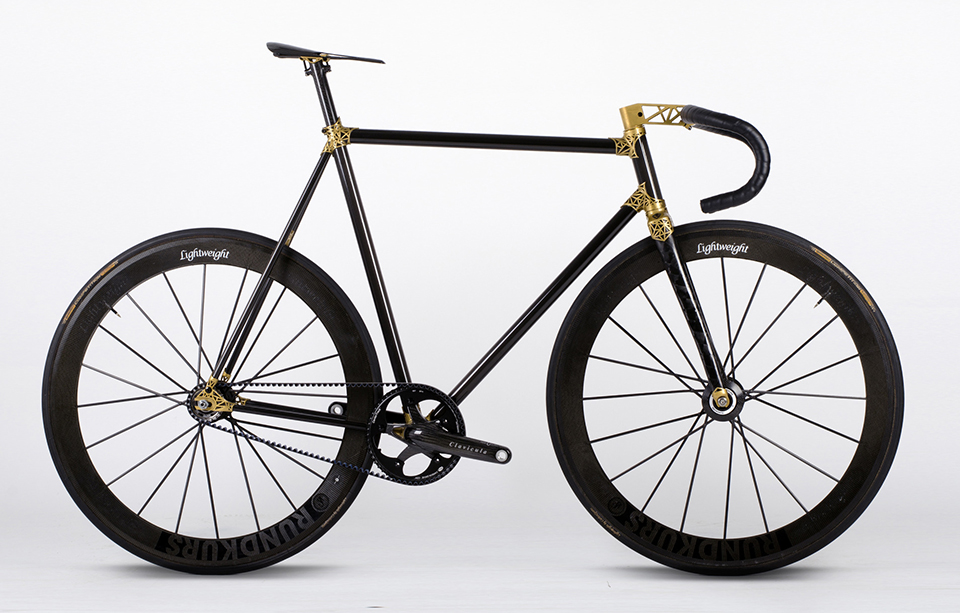
Subscribe to the 3D Printing Industry newsletter for the latest news in additive manufacturing. You can also stay connected by following us on Twitter and liking us on Facebook.
Looking for a career in additive manufacturing? Visit 3D Printing Jobs for a selection of roles in the industry.
Subscribe to our YouTube channel for the latest 3D printing video shorts, reviews, and webinar replays.
Featured image shows Canyon’s 3D printed bike frame. Photo via Bike Magazine.
Tags British Cycling Canyon Carbon Cycle show 2022 Element22 fizik Headmade Materials Materialise Pinarello RAM3D Renishaw Ride Green campaign Specialized Stratasys Sturdy Cycles
Hayley Everett
Hayley is a Technology Journalist for 3DPI and has a background in B2B publications spanning manufacturing, tools and cycling. Writing news and features, she holds a keen interest in emerging technologies which are impacting the world we live in.
Have 3D Printed Bicycle Frames Finally Become a Viable Reality?
Search
-
1031
Have we finally reached a tipping point where 3D frames will be both practical and commercially viable?In global engineering and manufacturing, 3D printing has been big news for quite a while. In the case of bicycle frames, this means rather than joining pre-made tubes together with some form of welding or gluing, the entire frame is built from scratch in one process, by adding many fine layers in quick succession of whatever the frame material might be, such as titanium or carbon fibre.
It would have to be a decade already since we first started seeing reports of 3D printed bicycle frames. There has even been a failed Australian attempt, through Melbourne based Titomic with input from frame building and design veteran Peter Teschner.
But despite huge promises of efficiencies that would allow commercially viable custom production of bicycles even in high wage countries like Australia, we’ve yet to see anything beyond predictions and prototypes.
One of the challenges has been that the equipment and software engineering required to 3D print something as large and complex as a bicycle frame is very expensive.
But with the bike industry booming and more venture capital than ever flooding in, that hurdle has been overcome, at least by Silicon Valley (USA) based Arevo.
In early September Arevo announced not only, ‘the completion of the world’s largest 3D printing facility for carbon fibre composite additive manufacturing’, but also the first shipment of bicycles and e-bikes with frames made by their 3D printer.
During Eurobike 2019, Arevo presented a prototype 3D-printed carbon fibre composite bicycle frame. Since August 2020, they’ve been offering on-demand production of customised frames.
Now with the introduction of the next generation high speed additive manufacturing system for large continuous carbon fibre composite structures, Aqua 2, the production process has become four times faster than its predecessor.
The Arevo Aqua 2 3D printer can make an entire carbon fibre bicycle frame from scratch. Is this how bicycle frame manufacture is going to look in future?Arevo is operating a full range of production systems – including 70 Aqua 2 3D printers. According to one source the Arevo Aqua 2 3D printers cost US $500,000 (A$685,000) each.
In true Silicon Valley style, Areva has raised US$85 million (A$116 million) in funding so far, from some of the biggest names in venture capital.
According to Arevo, additive processes such as 3D printing enables, ‘fast, on-demand and comparatively cost-effective production’ compared to conventional methods. As a result, the company is using these systems to print not only bicycle frames and other sports equipment, but much more, such as automotive parts, aerospace components and even complex architectural structures.
Arevo CEO Sonny Vu said, “After introducing the Aqua2 3D printing system last year, which is four times faster than the Aqua 1, we have now focused on the production and operation of these systems. Currently, a total of 76 systems are in live production worldwide. They are all connected to the cloud and in use at our various sites. This puts Arevo in an excellent position to serve the growing global demand for both our own consumer brands and the needs of our B2B customers.”
Arevo’s own brands include Superstrata, a bicycle and e-bike brand, and Scotsman, an e-scooter brand. Coinciding with the completion of the new facility, Arevo has also shipped the first Superstrata bicycles and e-bikes with carbon fibre composite frames out of the 3D printer. In addition, the developers are just completing engineering for the Scotsman e-scooter.
Join the Conversation:
What do you think about the prospects of 3D printing for the bicycle industry?
JOIN THE CONVERSATION:
3DNews Technologies and IT market. News cars, motorcycles, vehicles... American startup Avero will print... The most interesting in the reviews 07/14/2020 [14:16], Vladimir Fetisov Silicon Valley-based startup Avero is not known in the cycling world. However, that hasn't stopped him from using his expertise in 3D printing and composite materials to create the "world's first" unibody electric bike. nine0007 3D printed bikes will be sold under the Avero Superstrata brand. Potential buyers will be able to choose between the Superstrata Terra, which is a lightweight analogue of a conventional bike for different riding styles, and the Superstrata Ion, an electric bike with a 250W motor, a 252Wh battery and a range of about 100 km. The frame of the new bikes is made from a single piece of thermoplastic carbon fiber. This means that it is a one-piece piece, rather than a welded construction, as is the case with many standard bicycle frames. 3D printing can be costly and time consuming, but Superstrata CEO Sonny Vu says it results in a bike frame that is strong and durable, as well as a more custom design. It takes about 10 hours to produce one bicycle frame using this method. The manufacturer claims that it can create up to 250,000 unique design combinations. The developers have not yet managed to form all the supply chains of the components necessary for the production of bicycles on a 3D printer. It is expected that Superstrata bikes will soon appear on the Indiegogo crowdfunding platform, where anyone can place a pre-order for the purchase of any model. nine0007 The Terra will reportedly cost $2,799 when it goes into series production, while the electric Ion will cost $3,999. Source: If you notice an error, select it with the mouse and press CTRL+ENTER. nine0007 Related materials Permanent URL: https://3dnews.ru/1015663 Headings: News Hardware, cars, motorcycles, vehicles, Tags: superstrata, avero, electric bike ← B past To the future → |
Santa Cruz Bicycles
Custom creation
For Santa Cruz Bicycles (hereinafter referred to as Santa Cruz), a bicycle is much more than just a way to get from one place to another. Santa Cruz bikes are the epitome of the company's ultimate goal: to create the world's most reliable, top-performing, high-performing mountain bikes that can propel their owners over rough terrain (and into new vistas). What makes this concept real? Nothing but the spirit of innovation that dominates the company. nine0007
A good illustration of this is the case of Danny MacAskill. Danny, an avid mountain biker and professional bike tester, asked Santa Cruz to build a custom bike for him. Danny chose this company because of their reputation: many Santa Cruz bikes are based on a carbon fiber frame, which makes them both strong and light. Such rigid frames and other components (no less strong) allow cyclists to conquer landscapes that were traditionally considered passable only for mountain goats. Many professional bikers and enthusiasts love Santa Cruz bikes for their quality and reputation. nine0007
The dilemma for the company in the case of a custom order was that this time it needed a "one-off", unique design, created specifically for Danny's requests. Usually Santa Cruz bikes are mass-produced in Asia, but now it was necessary to develop and produce a new carbon fiber frame "at home", in-house, and on a tight schedule.
“Designing the bike for Danny was really terra incognita for us,” says Geoff Casey, design director of the company. And development manager, Nic McCrae, adds: "What we've been trying to achieve is something that meets all of Danny's specifications exactly, is as solid as possible, and also provides us with a good base for future development and experimentation with various techniques and manufacturing techniques."
3D printing helped develop and flesh out design concepts. Printed frames gave designers the ability to visualize and refine various structural design ideas much faster. nine0072 “Being able to have a real, non-abstract 3D printed frame helps us a lot, because that way we can see what we need to change without having to make special carbon tools and finalize the frame, which of course requires a huge amount of money. and time ,” says Jack Russel, senior industrial designer. - It's so cool to feel this frame with your hands and see the proportions of the tubes live. You never get that feeling from a model on screen." nine0073
However, even when the design was finally approved, there was still the problem of making the bike itself using carbon fiber. And for the production of a new model of a bicycle, a completely new set of molds and tools was required. Once again, McCray and his team solved this problem with the help of 3D printing technologies. Using ULTEM™ 1010 material, the team created cores that formed the basis of mold tooling that could then be used to make a carbon fiber frame. nine0007
According to McCray, ULTEM 1010 opened the door to shapes that would be extremely difficult to produce with traditional methods, or that would require endless setup on a five-axis CNC machine, which would waste time and money. The use of 3D printing not only allowed Santa Cruz to cut costs, but also meet deadlines. With the new tools, design development has become just a matter of hours, and the whole journey from a CAD drawing to a ready-to-use prototype is a matter of weeks. nine0007
Wide application
Santa Cruz collaborated with Stratasys to develop the first tools to build Danny's bike, but they soon bought their own Fortus 450mc™ 3D printer. According to McCray, it was the success with Danny's custom bike project that prompted the company to buy its own Fortus system, with the ability to use both high-impact Nylon12 and ULTEM 1010 material. Currently, 3D printing in Santa Cruz covers a huge range of tasks - from the modeling of concepts and ideas to the production of composite tooling and tools. nine0007
“We actually use the printer every day. It is needed not only by the development and design department, but also by the testing laboratory. Carbon fiber is being used extensively to test parts for impact and wear resistance, says McCray. – I have a feeling that now we can finally use the sheer amount of technology that Stratasys has to offer, and in the end we can develop better bikes faster in a more efficient way. And deliver great products to the market for people to enjoy.