3D metal printer mig welder
Researchers Develop a Low-Cost Metal 3D Printer Using MIG Welding - 3DPrint.com
Metal 3D printing, although it has gone down in cost, is still quite expensive. This limits access to the technology for small and medium-sized businesses, meaning that many applications go untried. In a paper entitled “Design and Development of a Low-Cost 3D Metal Printer,” a group of researchers discuss how they created a low-cost metal 3D printer that utilizes metal inert gas (MIG) welding and an open source microcontroller to fabricate parts.
The researchers took the design of their 3D printer from a Prusa i3 system and used several off-the-shelf components to build it.
“The components consist in developing 3D metal printer machine are; a pair of bearing holder and motor bracket, motor casing, shaft holder, ball screw, coupling, limit switch, linear bearing, stepper motor, polyurethane cylinder, polytetrafluorethylane (PTFE) plastic cylinder and various fastener,” they explain.
![]()
A MIG welding machine was used to supply the material and the energy to melt the material. The movement of the printer and the translation of command from the printer’s server to the host computer was controlled by firmware provided with an Arduino microcontroller. The cost of the entire system was about RM 3496, which translates to roughly $840, much more affordable than a typical metal 3D printer.
“In order to ensure the metal print is connected during operations, the MIG welding was set to switch on and off automatically,” the researchers continue. “The shielding gas was set to flow before the printing process starts. The welding torch was placed under the fixture design perpendicular to the bed to build the surface. The distance between the bed surface and nozzle was adjusted to about 6 mm by leveling the height of the welding torch.”
The MIG welding machine begins building a part layer by layer, from bottom to top. In order to test the system, the researchers performed two experiments in which a cylinder and a rectangle were 3D printed.
“The aim for the first experiment is to find the suitable voltage during 3D printing that produce relatively good bead geometry of 3D printed part,” the researchers state. “At first, the welding was deposited along the custom cylinder design. The parameter used for welding voltage varied from 18.5 V to 22.5 V. The first experiment was done with a constant speed of 50 mm/s and current of 100 A. The final dimensions were taken and compared with the actual CAD data. The second experiment was designed so that capability of the newly developed machine to 3D print a rectangular shape can be analyzed. The aim of the second experiment is to find the suitable value of speed in producing good structure.”
Five samples were 3D printed for the first experiment and their average values were recorded. They found that porosity occurred when voltage was either to high or too low, and that higher voltages reduce the size of the specimen due to the excessive flow of the molten metal. A voltage setting of 20.5V produced a good quality part, but it was not dimensionally accurate. In the second experiment, the researchers attempted to find the best printing speed. A too-slow speed resulted in a rough surface and poor fusion. They found that the speed should not be any higher than 20mm/s, however, so that the liquid had time to solidify. Post-processing was required in all cases to get better surface finish. As you can see the results are far from perfect but at this price point many would be able to try to improve such systems. Given more time and investment this could very well be a viable alternative to some metal parts.
Output of printing process (a) speed at 20 mm/s, (b) speed at 40 mm/s, (c) speed at 60 mm/s, and (d) speed at 80 mm/s
“Nevertheless, the study demonstrated that simple design specimens were successfully fabricated using the MIG welding and 3D printing process,” the researchers conclude. “The microstructure shows that the layer perfectly coincides with each printer layer and the top region of manufactured layer has the lowest hardness compared to the initial layer.
However, further research needs to be done in the future to improve the product’s quality and to study the mechanical behavior of the parts produced by this technique.”
Authors of the paper include N.A. Rosli, M.R. Alkahari, F.R. Ramli, S. Maidin, M.N. Sudin, S. Subramoniam and T. Furumoto.
Discuss this and other 3D printing topics at 3DPrintBoard.com or share your thoughts below.
Stay up-to-date on all the latest news from the 3D printing industry and receive information and offers from third party vendors.
Tagged with: low-cost 3d printers • metal 3d printer • mig welding • Prusa i3 • welding
Please enable JavaScript to view the comments powered by Disqus.
Students Combine Prusa i3 Printer with a MIG Welder to Create an Affordable Metal 3D Printer - 3DPrint.com
The technology behind 3D printing is still at an early stage, but progressing rapidly. One area where researchers and engineers are focusing their attention now is affordable metal 3D printing. Currently if you wish to fabricate an object out of metal you need to have access to a machine costing close to, if not more than, $1 million. Just like with plastic 3D printing, however, such machines are certain to drop in price as their capabilities expand. There is more than just money keeping these printers out of people’s homes and garages, however. Safety is also a major concern, as high temperatures, powerful lasers, and potential fumes all present dangers to users and their environments.
With that said, a group of students at Delft University of Technology are in the process of creating what they hope to be an open source metal 3D printer, available to a wide audience, and capable of printing with decent resolutions. The printer — which basically takes an MIG (metal/inert-gas) welder and attaches it to a Prusa i3 — is already capable of printing decent sized test objects.
For those of you unfamiliar with welding, an MIG welder uses a continuous feed of wire which is melted as it acts as both a filler metal and an electrode. A shielding gas flows around the melted wire, protecting it from any sort of local contamination.
The project, which has been inspired by research and development conducted at Michigan Technological University, already seems to be off to quite a start. Basically the MIG welder is tethered to the machine where the extruder and hotend usually are located. Using the Prusa i3’s Cartesian method of printing, the welder slowly but surely melts the metal wire as it places the material down layer by layer. The wire is fed to the welder at a rate of 4 meters/minute. The travel rate of the torch according to the team’s initial settings was 300mm/minute. A typical thermoplastic-based FDM/FFF printer, in contrast, can print anywhere from 3,000 to 18,000 mm/minutes, so this is considerably slower.
A 3D printed test object
Using this method, the team has been able to 3D print a wall-like structure, which is surprisingly solid, as well as uniform, which you can see from the images and video they have provided. Other circular shapes were also made.
There is still a tremendous amount of work to be done on this project; however, this certainly could act as a springboard toward affordable metal 3D printing. Let’s hear your thoughts on this project in the MIG Welder/3D Printer forum thread on 3DPB.com. Check out the video of the machine in action below. For further details and to follow along as the team progresses further on this project, check out their blog.
Stay up-to-date on all the latest news from the 3D printing industry and receive information and offers from third party vendors.
Tagged with: 3d metal printer • cheap metal 3d printer • delft university • metal 3d print • michigan technological university • open source 3d printer • tu delft • welder printer
Please enable JavaScript to view the comments powered by Disqus.
With fire and wave: all about metal 3D printing
Everyone knows this: 3D printing today is one of the pillars of world technological progress. It's just a pity that news about revolutionary developments in this area rarely comes from Russia.
The more pleasing are the exceptions. Scientists from the Bryansk State Technical University (BSTU), with the support of the Advanced Research Foundation, have created an installation (the Taimen project), which has become a truly new word in metallurgy and metalworking. nine0003
Among the great variety of additive technologies that exist in the world, two are clearly in the lead - printing with molten plastic and laser sintering of metal powder. In the first case, a low-melting plastic thread is fed to the print head, the tip of the thread heats up and instantly turns into a drop of liquid melt, which is applied to the desired point of the formed product and soon solidifies. It would be nice to print with metal as well, but metal is not plastic or wax. How to create such a temperature in the print head that it instantly turns steel into a liquid? I had to first invent laser sintering for metal printing. nine0003
Welding prints
And then the answer was found. Within the walls of BSTU, for a couple of decades, the technology of 3D printing with metal using ... electric arc welding has been developed and improved. Here, almost everything is like in a plastic printer: instead of powder, there is a metal thread fed to the printing point, or simply wire (welders call it filler material). An electric arc discharge melts the filler material and places a drop of metal in a precisely defined place. “Arc welding is only the basis of our method,” says Andrey Kirichek, project manager, professor and vice-rector of BSTU. - In fact, we have to solve a very atypical task for welding work - to give a shape to a printed product, to build up walls. It is impossible to do it manually: we need automation and programmatic control of the process, which we did. On the other hand, there is an opportunity to use the experience gained in the field of welding. Devices and equipment for welding are mass-produced and inexpensive. ” nine0003
Impact on dendrites
3D metal printing technology using electric arc welding has serious prospects. Bryansk developers have competitors from Germany, the USA and Norway, and all these companies are experiencing rapid growth. Being at the forefront is already worth a lot, but Russia has managed to advance the farthest. The fact is that in addition to the additive module, which is actually engaged in growing the product, the domestic installation includes a hardening module. In the standard case, the part printed on the printer will have the crystalline structure of a conventional cast product. But if the build-up layers are periodically compacted with shock pulses, turning large dendrites into colonies of microstructures, then the strength of the part will seriously increase. In the case of austenitic steels, for example, the yield strength of the material increases by 2–2.5 times, and the tensile strength by 1.5 times. This makes it possible to use cheaper alloys. The hardening module is a generator of mechanical impulses, through which a deformation wave acts on the metal - this has a positive effect on the crystal structure, mechanical and operational properties of the hardened metal. nine0003
Work on the use of strain hardening in additive technologies at BSTU began about five years ago, and at the same time the FPI became interested in this problem, with the support of which a special laboratory was created at the university. Today, there is not a single company in the world that would produce equipment that combines the processes of growing a product by welding and wave strain hardening.
The third module of the installation in question is the milling module, which provides, if necessary, machining of the part. “It must be admitted that, compared to laser sintering, our product formation technology is somewhat rougher,” Andrey Kirichek explains, “but even the most advanced “powder” printers give an error of at least 0.1 mm, and for precision mechanics (for example, in gas turbine) is too much. Therefore, machining, which ensures high accuracy of forms, is still indispensable. The advantage of our installation is the ability to alternate the operation of the modules as required. For example, to grow only a part of the product in order to process its internal surfaces that are hard to reach in the final form. nine0003
And cheaper, and our
Due to the greater accuracy, laser sintering technology is better suited for medium-sized complex-shaped parts with internal cavities, thin ribs, etc. But there are many large-sized products that also need to be grown. In this case, considerations of economy or scalability come to the fore. And here the new technology has a lot of advantages. Laser sintering is a very expensive technology, and the powder itself is especially expensive. Companies that produce sintering equipment configure it exclusively for powders of their own production. The range of powders even from well-known companies is small. In Russia, they are not produced on an industrial scale, and this greatly limits the capabilities of the technology. Plus, the welding method has a productivity about 6 times higher. And most importantly, it is not economically feasible to produce any large part by sintering, but it is quite possible and profitable to create an installation for printing and hardening metal beams of complex shape. nine0003
Like a hammer, only better
It is interesting to compare the technology of wave work hardening with traditional forging, because the goals and methods of these processes are generally similar. “Indeed, deformation and hardening occur here and there,” says Andrey Kirichek, “but in our case, energy enters the deformation zone in the form of a wave. A wave is a stream of impulses that have duration, amplitude, and shape. When forging, the pulses are short and rare; many processes that can change the structure of the metal simply do not have time to go through. We work with prolonged (10 times longer) pulses with a frequency of 8 to 40 Hz, the impact on the material is long-term, the efficiency of the impact energy on the elastic-plastic deformation of the hardened material is 5-10 times higher compared to a conventional impact and reaches 65% . With a simple impact, this figure is only 5-12%. nine0003
The part is created using three modules - additive, hardening and milling. The peculiarity of the process is that the work of the modules alternates depending on the need. For example, machining of a surface can be done even before the complete growth of the part.
The wave passes through all sections of the metal, is repeatedly reflected from areas with different acoustic hardness and from the surface on which the part lies. Due to this, wave states are actually formed in the product. At the intersection nodes of direct and reflected waves, more intense hardening occurs, and at intervals, less intense. This distribution has a good effect on operational properties. In fact, the technology makes it possible to provide a greater depth of hardening, to strengthen all layers at the same time. Perhaps today this is the only way that allows you to achieve such a result. nine0003
Prospects
The range of application of new technologies is potentially huge - from the manufacture of parts for rocket and space and aviation equipment to the automotive industry and the production of special equipment. In June 2019, US-based additive synthesis firm Relativity Space signed an agreement with NASA to convert its Mississippi factory into the world's first automated Relativity Space Terran 1 rocket factory. The factory plans to use a new version of the Stargate printer, which is smaller than the original can be placed on a moving platform to print building-high rocket parts. nine0003
In Russia, experiments have already been carried out on the use of wave hardening to impart armor properties to initially non-armor materials, which cost 5-10 times cheaper. It was also possible to increase the bullet resistance of conventional armor by 15-30%.
A lot of power metal parts that are part of machines and structures in a complex stress state could be produced using welded 3D printing with subsequent sealing. “The prospects are huge,” Andrey Kirichek explains, “but there are also many obstacles to the spread of technology. I remember the history of laser cutting systems. When they first appeared, enterprises reacted to the new technology with caution, even with skepticism. The equipment is expensive, there are no trained personnel, the amount of work, the production of which would pay off the complex, is not guaranteed. At first, it was necessary to create regional laser centers where companies placed single orders. 10 years have passed, and manufacturers have realized the advantage of technology, a market has formed; now almost every enterprise has one or more machines for laser cutting and metal cutting. Apparently, we will have to follow a similar path. In addition, the manufacture of critical parts, for example, for aviation, the defense complex, requires certification, and this process is costly and slow. But there are no other options." nine0003
Source
Tags:
Bryansk State Technical University (BSTU), 3D metal printing, 3D metal printing technology using ... arc welding, laser sintering
Attention!
We accept news, articles or press releases
with links and images. [email protected]
what is it, how to cook with argon
Argon welding allows you to accurately weld different metals, creating strong and beautiful seams at the same time. This is a progressive type of welding used in the chemical and food industries, mechanical engineering. Such welding will not hurt in the garage, a private workshop. Consider what is needed for argon welding, how it is carried out, which metals are welded in what modes.
In this article:
- What is argon welding nine0089 Classification of argon welding by type
- What you need for Argon welding
- Argon equipment
- How to cook with argon
- What metals are boiled with argon
- Advantages and disadvantages of argon welding
What is argon welding
Argon welding is a kind of electric arc welding, only with a non-consumable electrode and a different principle for protecting the weld pool. The arc is ignited between the workpiece to which the mass is attached and the tungsten electrode. It does not melt, but the temperature of the arc is sufficient to melt the edges of the metal. Electrode vibrations can be controlled by the weld pool by adjusting the welding speed, seam width, penetration depth. nine0003
A filler wire is used to fill gaps or build up a high bead. It is chosen with the same composition as the metal being welded. The welder feeds the wire with his free hand.
Argon shielding gas is supplied through the burner nozzle into the welding zone. It blows out the atmosphere around the electrode, isolating the molten metal from the outside. Without argon, carbon is strongly released, the weld pool boils, and the seams are porous.
The welding inverter acts as a power source. It is designated TIG and this is different from MMA equipment. It has special connectors for a burner, an additional gas supply channel, and a different form of control.
Classification of argon welding by type
In production, there are three types of argon welding, which are classified into the following categories:
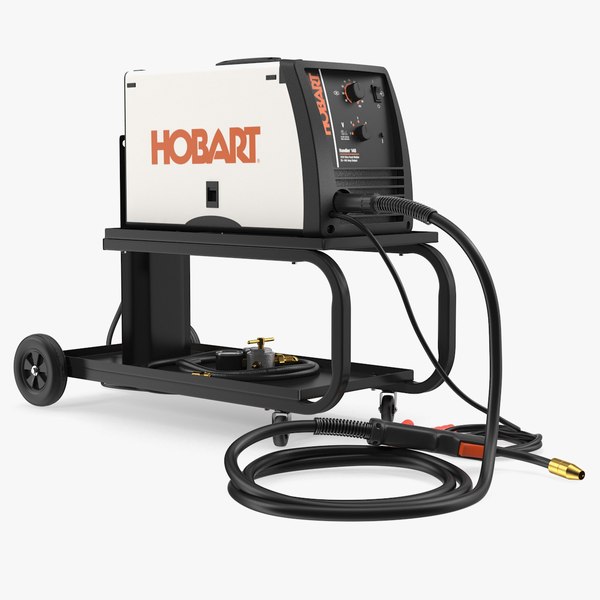
In addition, argon welding is divided according to the method of execution with or without filler wire. You can do without an additive in the case of welding thin steels with a cross section of up to 2 mm. The sides should not have gaps - a tight clamp is important. Then the tungsten electrode melts the edges, and this metal is enough to connect the sides. The seams are thin, smooth (practically without scales, like a mirror), airtight. But when broken, they are easily damaged.
With an additive, cook longer, the seams are scaly (the number of layers of scales depends on the frequency of feeding the filler wire into the weld pool), but you can fill in gaps 3-5 mm wide, create tubercles for the groove. The method with an additive is used for welding thick metals with a cross section of 3 mm or more nine0003
Direct welding
corner welding
T-welding
What you need for welding with argon
To weld with argon arc welding, it is necessary to assemble a set of equipment and accessories, as well as consumables and PPE.
Correct burner.
To work, you need an argon burner. The burner is distinguished by a connection connector containing gas supply channels, a power cable, a chip for powering control buttons. nine0003
When choosing a burner, pay attention to the location of the button. It can be both below and above. Affects ease of use. The length of the loop determines the welder's maneuverability zone. For desktop work, 3 m is enough. For welding large containers, choose a hose package of 5-8 m. If you plan to cook at currents of 250-400 A regularly, look for a water-cooled model.
A non-consumable tungsten electrode is inserted into the burner. Consumables differ in tip color for different types of metals. If you are a beginner, buy an electrode with a blue tip. It is more versatile and suitable for any task. nine0003
The second cable, necessary for closing the electrical circuit, is the mass. It is fixed to the product with the help of a "crocodile". The better the contact, the more stable the arc.
Connect shielding gas
To supply argon to the welding zone, you will need a gray argon cylinder. Capacity is from 10 to 80 liters. For field work, it is practical to have a small cylinder. The tank is connected through a reducer. Gas is supplied to the apparatus through a special welding hose. It must be black. If you choose a length of 10 m, you will be able to move around the workshop with the device without dragging the cylinder along with you. nine0003
Personal protective equipment for a welder
Argon welding is no less dangerous than RDS, so personal protective equipment is needed. In order not to burn yourself on hot objects, use leggings and a protective apron. The welding process is controlled through a mask. It is more convenient to work in a chameleon mask than in a shield with permanent blackout. You can always choose a comfortable welding helmet at an affordable price.
Equipment for working with argon nine0003
One of the most important for argon welding is the TIG inverter machine. The possibilities of penetration and joining of various metals depend on its characteristics and functionality. Choosing the right machine for argon arc welding is the key to success.
In production, there are three types of argon welding, which are classified into the following categories:
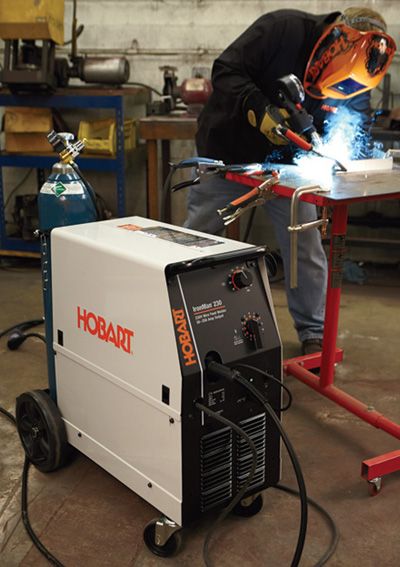
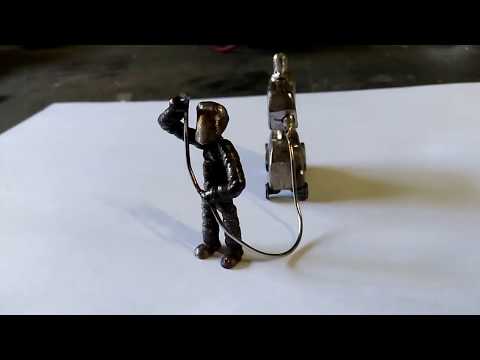
How to cook with argon
Set up the machine first. On the simplest models, set the current and gas flow. The modes depend on the thickness of the metal. nine0003
Metal thickness, mm | Current strength, A | Gas consumption, l/min |
---|---|---|
one | 30-40 | 6 |
1.5-2 | 45-70 | 7 |
3 | 75-90 | eight |
In more advanced versions, set the following settings (for example, we will select the parameters for welding steel with a thickness of 1.5 mm):
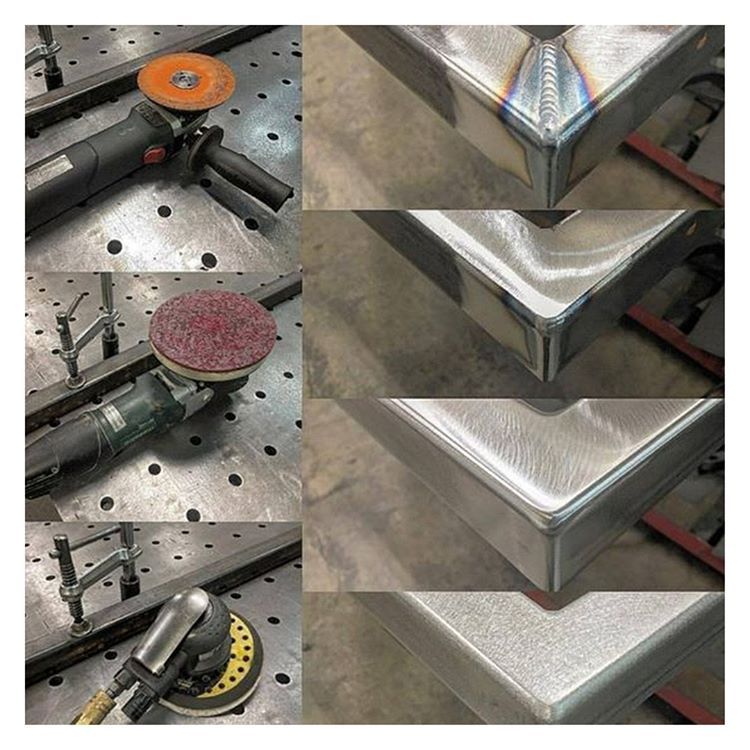
There are two ways to ignite the arc, depending on the capabilities of the device. The contact method requires touching the tip of the electrode on the product. Sometimes the tungsten needle sticks, because of which it dulls faster, you have to spend time re-sharpening. Non-contact ignition works with a high-frequency pulse (built-in oscillator), initiating an electric arc without touching. It is more convenient, the needle is less blunt.
Argon welding is carried out in the following sequence:
- Switch on the inverter TIG.
- Attach ground to product.
- Insert a sharpened tungsten electrode into the torch.
- Open the gas bottle.
- Bring the torch to the product at a distance of 3-5 mm from the surface to the tip of the needle.
- Put on the mask, press the power button. It is most convenient to cook with the 4T mode. Then it is not necessary to keep the power button pressed all the time.
- When the electric arc starts, hold it on the joint to form a puddle of metal. Circular movements of the electrode achieve fusion of the sides. Hold the burner at an angle of 45 degrees relative to the surface.
- Slowly feed the needle from right to left, carefully feeding the filler wire with the other hand. The additive is fed in front of the electrode.
- When the seam is finished, press the button but do not release it. The welding current will be reduced to close the crater, avoiding a fistula at the end. nine0090
What metals are boiled with argon
Using argon arc welding, they connect:
Video Source: Aurora Online Channel
Advantages and disadvantages of argon welding
Using argon welding, you can join aluminum, copper, titanium - metals that are difficult to weld in other ways. Another advantage is neat seams, increased tightness. On stainless steel, they are almost mirror-like and do not require machining. The convenience of welding lies in the absence of slag, since an inert gas is responsible for protecting the weld pool. nine0003
The main disadvantage of argon welding is the low speed of the process when performed manually. Consumables for welding (tungsten electrodes, filling cylinders with argon) are not cheap. The TIG welding method is suitable for the manufacture of stainless steel structures, welding of cracks in the cylinder block, repair of light alloy wheels.
Answers to the questions: what is argon arc welding and how to cook with argon?
How to weld vertical seams with argon? nine0003
HideMore
Welding is carried out according to the same principles as in the lower position. The main thing is to lead the seam from top to bottom. Reduce the current strength by 10-20% compared to the same joint in the lower position so that the metal does not flow down.
How to sharpen a tungsten electrode?
HideMore
Sharpen the rod on a rotating diamond wheel. It will last longer than a regular grinder. Place the electrode with the tip away from you on the end of the rotating circle. Achieve a sharpening angle of 20-30 degrees. For welding at currents of 200-300 A, sharpening of 60 degrees is needed. Thin metal 1-1.5 mm is more convenient to weld with a tip, like a needle - the sharpening angle is about 10 degrees. nine0003
What should I do if the weld pool is bubbling a lot?
HideMore
Adjust the argon supply on the reducer. There is either too little gas (carbon escapes out of the metal) or too much.
How to cook with argon welding outdoors in windy weather?
HideMore
Cooking like in a workshop will not work - the wind blows off the protective gas and leaves the weld pool open to external influences.