Stainless 3d printer
Desktop 3D Printers Designed for Professionals
Desktop 3D Printer Series
Professional desktop 3D printers built with the versatility to test design concepts and build strong end use parts. Our platform covers a wide range of applications - varying from flexible and elastic to strong and rigid.
Compare 3D Printers Talk to an Expert
Drive innovation. Right from your desktop.
Compare Our Desktop 3D Printer Models.
Onyx One™
Our core desktop printer for functional plastic parts with stunning surface finish.
Materials
Plastic
Onyx™
Specs
+320 x 132 x 154 mm build volume
+100 µm - 200 µm layer height
+Precision ground composite print bed
MSRP
$4,990
Talk to an Expert
Onyx Pro™
Our enhanced desktop printer for stunning prototypes, tools, and production parts.
Materials
Plastic
Onyx™
Precise PLA
Smooth TPU
Continuous Fiber
Fiberglass™
Specs
+320 x 132 x 154 mm build volume
+100 µm - 200 µm layer height
+Precision ground composite print bed
MSRP
$9,600
Talk to an Expert
Mark Two™
The best desktop printer for stunning prototypes, tools, high performance end-use parts, and replacement parts.
Materials
Plastic
Onyx™
Nylon White™
Precise PLA
Smooth TPU
Continuous Fiber
Continuous Carbon Fiber™
Aramid Fiber (Kevlar®)*
Fiberglass™
HSHT Fiberglass™
Specs
+320 x 132 x 154 mm build volume
+100 µm - 200 µm layer height
+Precision ground composite print bed
MSRP
$19,900
Talk to an Expert
Dupont™ and Kevlar® are trademarks and registered trademarks of E. I. du Pont de Nemours and Company
What can I build on a desktop 3D printer?
Micro carbon fiber filled nylon offers excellent heat resistance, surface finish, and chemical resistance
APPLICATIONS
- Functional Protos
- Production Covers
- Fit checks
- Job Aids
Learn more
Stiff, strong, and extremely light, carbon fiber reinforcement yields parts capable of replacing machined aluminum.
APPLICATIONS
- Custom production
- Bridge production
- High performance end-use parts
- High-strength tooling
Learn more
HSHT Fiberglass delivers the highest impact resistance and heat deflection temperature of our continuous fibers, and can be used for low-temp molds.
APPLICATIONS
- Welding fixtures
- Ruggedized enclosures
- Low-temp molds
- Forming tools
Learn more
Inexpensive and 11 times stiffer than ABS, this is the perfect entry level continuous fiber for 3D printing functional parts.
APPLICATIONS
- Workholding tools
- Functional Prototypes
- Moderate strength end-use parts
Learn more
Extremely durable and extremely resistant to catastrophic damage, Kevlar is an excellent choice for harsh environments.
APPLICATIONS
- Workholding tools
- Ruggedized enclosures
- Flexures
Learn more
Rubber-like material for high quality, flexible, impact-absorbent parts on demand.
APPLICATIONS
- Seals and gaskets
- Shock absorbers
- Wheels and treads
- Belts
Learn more
Colorful, cost-effective, and easy to print thermoplastic for design validation
APPLICATIONS
- Concept models
- Fit Checks
- Color-coded indicators
Learn more
Unmatched versatility
Our Desktop Series printers unlock production-grade performance and affordable prototypes, all on the same platform. Our most popular printing plastic, Onyx™, gives you a great start in material properties with excellent surface finish. Our selection of continuous fibers take our parts far beyond the mechanical and thermal properties of everyday FFF printing plastics, Smooth TPU 95A provides an efficient way to make high quality flexible parts in low-to-medium volumes, while Precise PLA delivers effective, reliable prototypes at an affordable price. No matter what properties you’re looking for, our desktop 3D printers have the right material for the job.
How does CFR 3D printing work?
Talk with a
Desktop expert
Let us put together an additive manufacturing solution to suit your needs.
Eiger 3D Printing Software | Markforged
Skip to navigation
Eiger™
A leading digital manufacturing software for driving business transformation.
Try It Yourself
Produce parts on-demand and at the point of need with the first connected, secure additive manufacturing platform.
Simulation takes the guesswork out of 3D printing
Try SimulationFrom design to part — easily and quickly
Eiger is an integrated, connected platform designed to take you from CAD to functional part quickly. The browser-based 3D printing software workflows are secure, fast, and intuitive.
Try It Yourself
Print with fibers, composites, and metals
Eiger, our 3D printing software, enables you to slice and print composite parts reinforced with continuous fibers and metals. You can prep parts for printing with a single click, or drill deeply into part settings to optimize your final product.
Interact seamlessly with printers
Eiger software fully integrates with all Markforged 3D printers, enabling you to create builds, print parts, and monitor prints in a seamless workflow.
Customize support placement
Eiger makes it easy to automatically generate supports that are optimized for most parts. Using Support Overrides, you can choose where to place supports to avoid internal channels, small overhangs, or threading or to provide extra support.
Try It Yourself
Validate part strength and optimize print parameters with Simulation
Incorporating 3D printing into tooling and end use applications requires total confidence in part strength. Traditionally, this required lengthy design-print-break testing cycles or costly analysis software. Simulation takes the guesswork out of 3D printing by integrating virtual testing and time/cost optimization into our familiar slice and print workflow.
Store and access parts effortlessly
A secure part library enables you to dynamically manage engineering projects of any size — complete with versioning. Eiger part files are securely stored and can be versioned, edited, and printed anywhere.
Try It Yourself
Manage projects with simple organizational features
Organize and bucket your parts in an intuitive, simple way with folders. Organize parts and projects alphabetically, by create date, or by edit date.
Find the right part every time
Easy-to-use filters sort parts by part name, material, or user — enabling you to quickly find the part you need when you need it.
Drive fleet wide success with real time monitoring
A single place to manage your printer fleet in real time, whether in one spot or worldwide. Benefit from automatic updates while getting analytics, usage data, and live telemetry in a single place.
Try It Yourself
Monitor devices in real time
Eiger empowers you to monitor any connected device in your organization from anywhere in the world. Get real time updates on critical project progress as it happens.
Customer success, built in
Eiger 3D printing software updates automatically push to your organization, unlocking new features and continuously improving printer performance. Support is fully integrated into the software experience and is directly accessible from both part and printer pages.
Eiger Core
Designed to take you and your teams from CAD to strong, functional parts quickly that can be shared and iterated.
Try Eiger
Eiger Fleet
Designed to scale your additive manufacturing operations through centralized control over printers, users, parts, and workflows.
Learn More
Offline Eiger
Designed to take you from CAD to strong, functional parts quickly when Internet access is intermittent or restricted.
Learn More
Learn about online and offline software operations in Eiger Deployment Options and Data Security
Learn the basics of 3D printing software in From Art to Part: A Step-by-Step Guide to 3D Printing
Blacksmith — Trust your parts off your print bed with in-process quality control
Markforged’s revolutionary software Blacksmith enhances part quality and provides both real time and documented part inspection, verifying that the part you printed is the right part for the job.
Learn More
Collaborative and Scalable
Share parts across teams. Kick-off and monitor prints from anywhere on a secure, connected infrastructure.
Day One Productivity
Turnkey for any skill level and feature-rich when you need it. It’s powerful — not complicated.
Constantly Improving
Automatic software updates continually make your hardware and parts better over time. We are always adding new features and enhancing existing ones.
Security built into your workflow
Our software’s security model, world-scale infrastructure, and unique capability to innovate will help keep your organization secure and compliant.
Already a Markforged Customer?
Talk to an expert Request a demo Try the softwareLet’s get started.
3D printing with stainless steel in the center of additive technologies St.
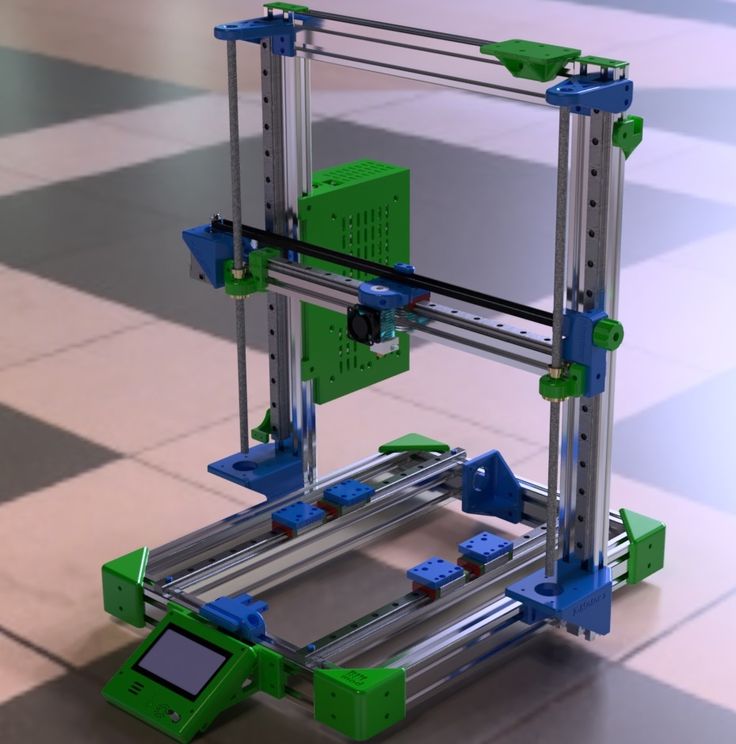
Stainless steel is one of the most used materials for metal 3D printing. Although stainless steel is notorious for being poorly processed by classical methods, it is one of the best materials for 3D printing.
Stainless steel does not oxidize and therefore does not suffer from humidity. Metal 3D printing uses very fine metal powders, which means that the surface area relative to the volume is very high. Which, in turn, indicates a high rate of reaction between the material and the atmosphere. And the slight amount of moisture in the air can rust normal steel powder, but not 3D printing stainless steel powders. nine0003
Other materials for 3D printing, such as aluminum or titanium, become combustible or even explosive in the form of micropowders. And stainless steel remains a relatively safe material for metal 3D printing.
Also, the surface quality of a part when 3D printed with stainless steel is usually better compared to other materials.
The choice of stainless steel powder for 3D printing should begin with the alloy composition requirements specified for a particular part. The second step is to find a manufacturer of powders from this alloy. There are many different stainless steel alloys in powders for 3D printing on the market, but only a few of them are in the warehouses of manufacturers, and in order to get the powder at an affordable price and in a reasonable time, it is better to choose an alloy from those that are widely used in metal 3D printing. nine0003
Metal powder for 3D printing is not just metal dust. In order to get good results in metal 3D printing, the powder must have a certain particle size distribution and have particles of a strictly spherical shape.
Why is particle shape so important in metal 3D printing? Spherical powders have the best fluidity, which in turn affects the uniformity of the layers. Given a typical layer thickness of 20-50 µm, the layer plane can be destroyed by any non-spherical or out-of-dimensional particle. nine0003
The second reason is that spherical powders have the highest bulk density. If we consider the density of stainless steel powder for 3D printing, then it will be 1. 5 times less than that of a solid part (~4.5g/cm³ for spherical powders and ~7.7g/cm³ for a solid steel part). This means that the powder is compressed to 60% of its original volume during the stainless steel 3D printing process. Thus, if you want to get dense parts devoid of porosity, you should only choose strictly spherical stainless steel powders for 3D printing. nine0003
Here you can see some of the 3D printed stainless steel samples that were produced in our Additive Technology Center (ATC) in St. Petersburg.
Usually when people talk about 3D metal printing, they only think about parts for the space or aviation industry. But 3D printing with stainless steel today can be found in completely different industries. Based on our own experience, we can highlight the following examples:
- nine0002 3D printed 316L stainless steel watch case
-
3D Printed 316L Stainless Steel Computer Port Shields
-
316L Stainless Steel and 15-5PH Printed Automotive Turbo Hose Plugs
-
3D printed stainless steel special adapter sleeves
-
3D printing stamps for stainless steel leather goods stamping
-
3D printed stainless steel housing for electronic components Ph2
-
Each of our 3D printers contains at least 10 stainless steel printed parts.
Even
-
316L stainless steel 3D printed decorative items
You can order stainless steel 3D printing in our Additive Technology Center (ATC).
3D Steel Printing - Quick Guide / Sudo Null IT News0001
Metal 3D printing using pure steel and alloys produces durable functional parts for mechanical and industrial products.
Any metal 3D printing technology can print with steel. This is the most popular material. But which steel grades and which technology is best for your application? Will printed steel parts really be as strong and durable as traditionally made parts?
Let's see how a 3D printed steel part revolutionizes manufacturing and opens the door to new applications in aerospace, medical equipment, automotive, tool making, heavy industry, architecture and more. In addition, more affordable desktop printers are expanding the scope and scope of real steel 3D printed parts. nine0003
Strength of steel printed parts.
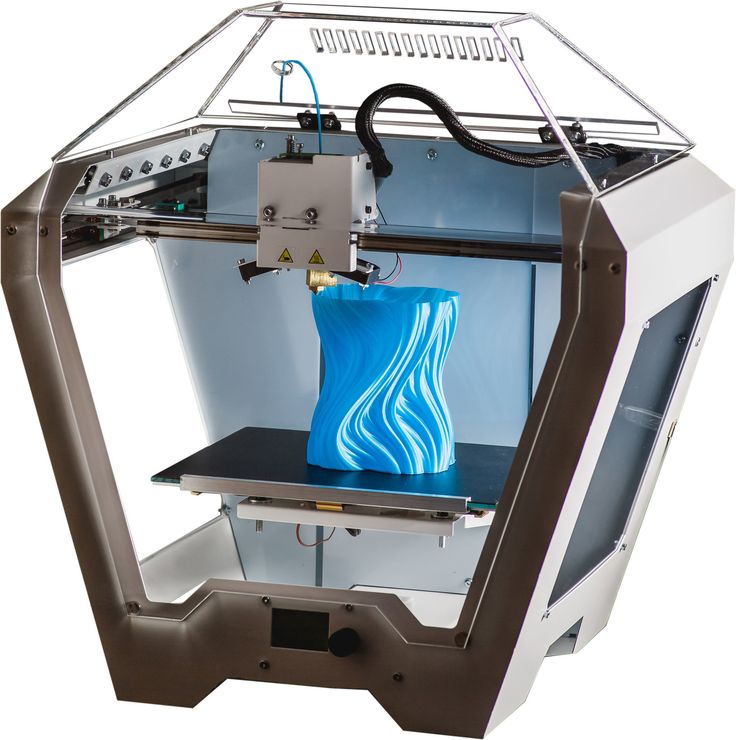
The most common question when it comes to a 3D printed metal model is "Will it be as strong as a forged or cast part?" ?". The short answer is yes... and no.
3D printed steel parts can be just as strong, and sometimes even stronger, than those made in the traditional way. It depends on many factors such as: end use, type of steel, choice of 3D printing method, post-processing and shape of the part. Also, the comparison depends on which of the strength characteristics you focus on: tensile strength, static load strength, fatigue strength, etc. nine0003
Parts printed from steel are used in the aerospace industry, for the military, and also, for example, for the manufacture of a footbridge, shown below. Therefore, the strength of printed products is beyond doubt, but let's take a closer look.
Queen Maxima of the Netherlands officially opens a 3D printed metal bridge.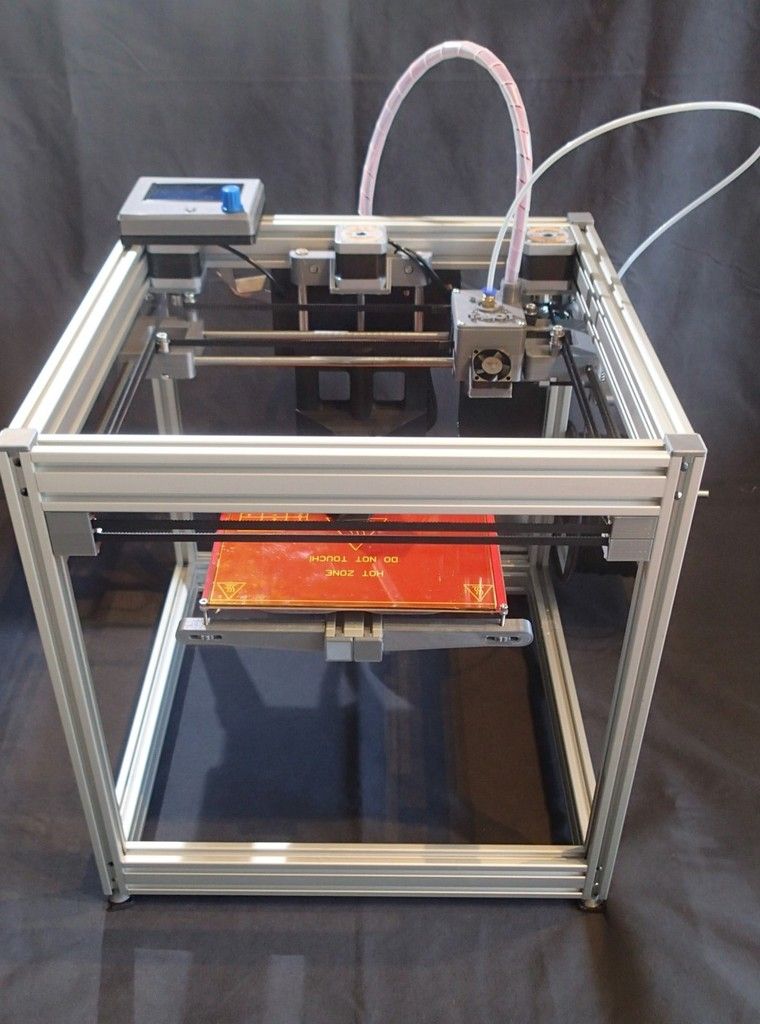
A 3D printed or laser powder sintered (LPBF) steel part has a finer grain structure than cast metal products. This provides better tensile strength characteristics, but in other respects the cast parts are currently still stronger. Most often, LPBF 3D printing is used to replace cast components, but in some cases, 3D printed components can replace forged parts. nine0003
One study showed that, under certain conditions, stainless steel parts made using LPBF 3D printers were three times stronger than parts made from the same steel using the traditional method.
In experiments comparing 3D printed steel parts to traditionally made steel parts, researchers create identical parts using two methods and compare their performance. However, head-to-head comparison of details is only part of the big picture. nine0003
The main advantage of printing with steel is not only its strength, but also the unique ability to create internal channels and lattice fillings in parts, which is impossible using traditional manufacturing methods. Metal 3D printing makes it possible to produce parts faster than traditional production, since this method does not require the use of special equipment and tools, it allows you to create assemblies as a whole, eliminating the need for subsequent assembly and welding. Designing a printed part usually means that less metal is needed to make it, and therefore less weight, for the same strength. nine0003 MX3D Wire Arc Additive Manufacturing (WAAM) printed steel architectural support (Source: MX3D)
Steel 3D printing is also more stable and cost effective as it reduces waste. When using subtractive manufacturing methods, such as CNC machining, you make a part by cutting it out of a large one, with a lot of waste. With additive manufacturing, you only use the material you need to make the finished product. nine0003
Steel 3D printing is not intended to replace traditional methods in all areas, but it may be a better choice for a wide range of applications. Particularly when the required parts are unique and designed for specific applications, such as rocket engines, racing cars or the oil and gas industry. 3D printing is the fastest and most flexible technology for mass production and prototype production. For military and industrial applications, steel 3D printing is a faster and more efficient way to create individual parts for vehicles and machines. Stainless steel 3D printing is rapidly finding applications in medicine to create unique surgical instruments and implants. nine0003
If you know what characteristics your final product should have (tensile strength, compressive strength, hardness, density, etc.), then all these parameters can be incorporated into the product at the production stage.
Kinds of steel for 3D printing
Metal powder is the most used metal material for 3D printing (Source: GKN Additive) There are thousands of kinds of different steel grades and alloys with different mechanical properties, used in traditional manufacturing but in 3D printing there are only a few dozen of them, and some of them are unique, created specifically for this technology. Among the steel options, the following can be distinguished:
-
Stainless steel (316L, 304L , 17-4PH, 15-5PH, 420, 254, Ph2, GP1, 630, 410).
-
Tool steel (D2, M2, h23, h21, MS1, 1.2709).
-
Low alloy steel (4140).
-
Structural alloyed (20MnCr5).
Recently, unique alloys have been developed specifically for 3D printing, designed to solve the problems that occur with classical production methods. nine0003
For example, 3D printer manufacturer Desktop Metal released a patented stainless steel in 2022 that the company says combines the tensile strength, ductility, and corrosion resistance of 13-8 PH stainless steel, combined with the hardness low alloy steel like 4140. The company says customers can go to market with this material and skip the galvanizing step to protect products from corrosion.
ExOne offers two special blends of steel and bronze that the company says allows 3D printed steel parts to achieve increased corrosion resistance while being easy to machine and polish. nine0003
While most of the metal powders used in 3D printing are similar to those used for other manufacturing methods, their numbers are on the rise as more companies adopt the technology. Some metal powder manufacturers, such as GKN, also make custom powders for specific 3D printing applications.
How to print with steel
The strength, properties, and applications of 3D printed steel products largely depend on which 3D printing technology you use. Some methods produce stronger parts, other methods provide better hardness or abrasion resistance, and some technologies are simply very fast. nine0003
Below are the main metal 3D printing methods, their properties and some of the most common application examples.
Fused Deposition Printing (FDM)
BCN3D's Epsilon printer extrudes metal filament from stainless steel (Source: BCN3D) as more printer manufacturers certify metallic filaments for use on their printers, such as Ultimaker, BCN3D, Makerbot, Raise3D.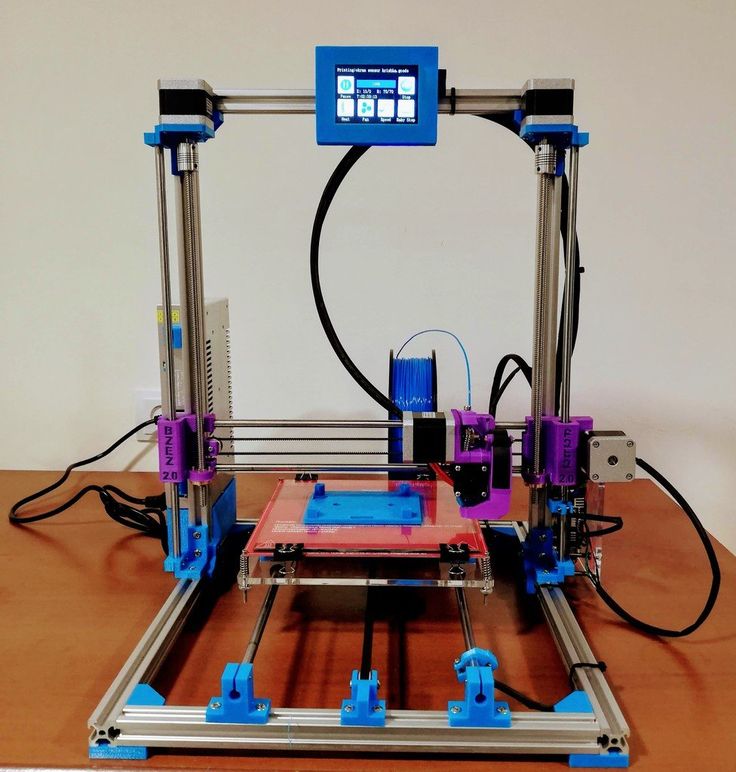
FDM media was once limited to thermoplastics. Companies like BASF Forward AM and The Virtual Foundry now offer metal filaments that can be used on almost any FDM printer as long as it has a hardened steel nozzle for abrasive media.
These materials are approximately 80% metal and 20% plastic. After printing, the post-processing process removes the plastic, resulting in 100% metal parts. nine0003
Due to the removal of the bonding plastic, FDM metal parts shrink during post-processing. The amount of shrinkage is constant and can be taken into account in CAD systems, which allows to obtain relatively accurate finished parts.
Forward AM's 316L Stainless Steel Ultrafuse filament produces finished parts with material properties that the company claims are comparable to injection molded metal parts. nine0003 (Source: BCN3D)
While 3D printing with metallic materials may not be suitable for demanding applications such as aerospace, the economics of producing simple metal components without critical loads on an affordable FDM printer can outweigh the impossibility of applying them in some areas.
Metal prototype parts and finished parts that will not be subjected to extreme stress are ideal uses for this technology. nine0003
Bound Metal Deposition (BMD)
Desktop Metal's Studio System 3D printer used bonded metal bars that were extruded layer by layer to form a metal part (Source: Desktop Metal) Similar to FDM, Metal mesh deposition method (BMD) or bonded powder extrusion (BPE) is a 3D printing process based on extrusion. This method uses bonded metal rods or bonded powdered metal filaments, which consist of a much higher percentage of metal powder than the filaments used in FDM. As with FDM, post-treatment to remove the binder and heat treatment in a final sintering oven are required. nine0003
There are only a few 3D printers using this method such as Desktop Metal, Markforged and more recently 3DGence, but more companies are entering this market, so stay tuned. These printers are valued as a convenient solution for office 3D metal printing, they are more expensive than most FDM printers, but cheaper than the powder-based metal 3D printing technologies described below.
These printers use their own proprietary filament. Desktop Metal and Markforged offer four types of steel. nine0003
Ideal niches for this technology are metal prototype parts, where it is necessary to test the functionality of a part before mass production using traditional methods. Popular applications are molds, punching dies, nozzles, impellers, fasteners and heat exchangers.
For example, Shukla Medical uses Markforged's Metal X printer to print steel prototypes of its orthopedic implant removal instruments. nine0003
Laser powder sintering.
Laser powder sintering technology uses one or more lasers to melt powdered metal layer by layer into a desired shape.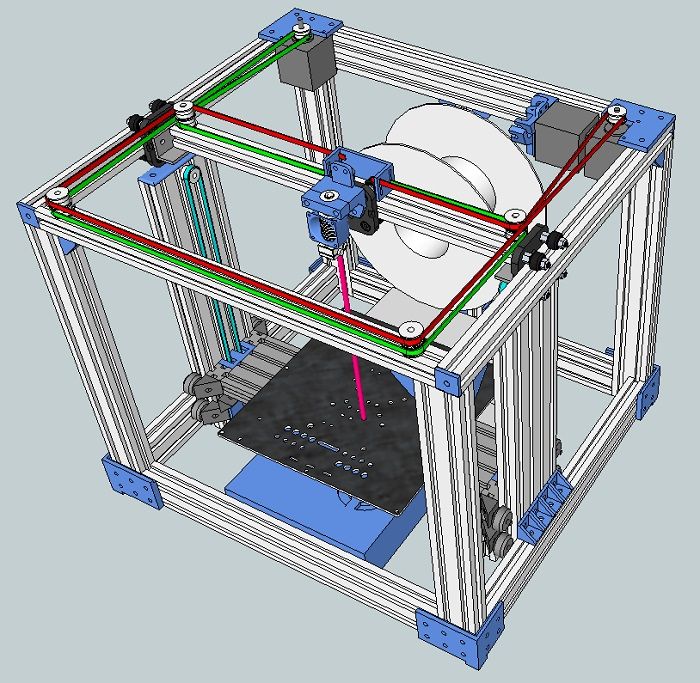
This method uses powerful lasers to selectively sinter metal powder layer by layer. nine0003
LPBF 3D printers are available in a wide range of sizes, prices and laser powers. These and other characteristics affect the properties of the finished part, print speed and other parameters of the finished products.
Steel and steel alloys are the most popular material for LPBF equipment and, unlike FDM and BMD, metal powders are commercially available as they are most commonly used in traditional production methods.
LPBF is a technology that maximizes the quality of a 3D printed part. Applications include aerospace components such as monolithic thrust chambers, rocket engine components and heat exchangers, molds, tools and other applications, as well as high wear parts and surgical instruments. nine0003
Binder Jetting
Binder 3D printing technology uses powdered metal and a binder to form metal parts (Sorrce: ExOne) binder, and not with a laser.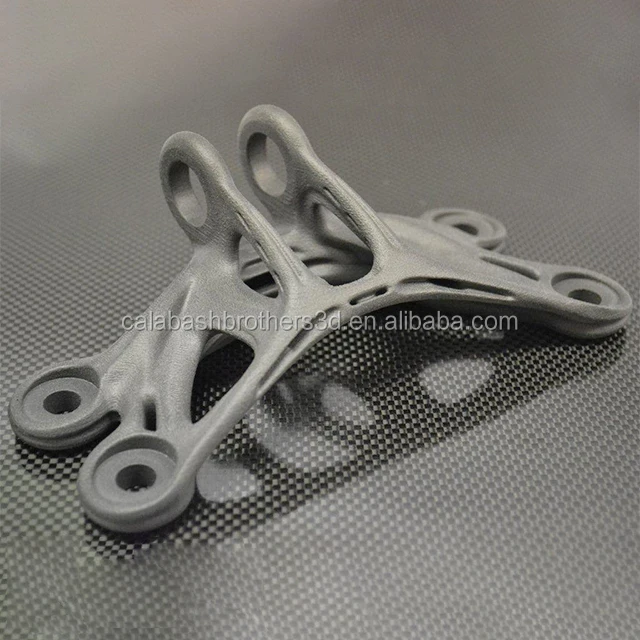
Binder application stands out for its high printing speed compared to other 3D printing methods or traditional manufacturing, and metal parts made with this technology have material properties equivalent to those made by metal injection molding. nine0003
The number of manufacturers producing metal-bonded inkjet 3D printers is much smaller than that of LPBF machines. Leading manufacturers include ExOne, Desktop Metal, Digital Metal, GE Additive and HP.
Binder blasting is ideal for medium to high volume production of metal tools and spare parts.
In fact, HP claims that its Metal Jet 3D printer was designed specifically for mass production of 316L stainless steel products. HP has partnered with Parmatech to produce metal parts for the medical industry. Pennsylvania-based ExOne uses this technology to manufacture hard metal cutting tools and tool steels. nine0003
Electron Beam Melting (EBM)
(Source: GE Additive) Electron Beam Melting (EBM) is another powder cladding technology. It works in a similar way to selective laser melting (SLM), but instead of using a laser as the energy source, it uses a much more powerful beam of charged particles.
The recoater moves the powder onto the printing plate and an electron beam selectively melts each layer of powder. After each layer is printed, the plate is lowered and another one is applied on top of the previous layer. nine0003
EBM can be much faster than SLM, but SLM produces smoother and more accurate pieces. The electron beam is wider than the laser beam, so EBM cannot produce the same precise parts as SLM. Another difference is that the manufacturing process takes place in a vacuum chamber, which reduces the amount of impurities in the material that can lead to defects. That is why EBM is often chosen for printing components for the aerospace, automotive, defense, petrochemical and medical implant industries. nine0003
Titanium is the most popular metal for most EBM applications, however steel can be used.
Cold Spray
(Source: Impact Innovations)Cold spray 3D printing is done by injecting metal powders through a jet nozzle into a supersonic stream of pressurized gases such as air, nitrogen or helium. The process is called "cold" because the metal particles do not melt, but hit the metal substrate and adhere to its surface during the so-called plastic deformation. nine0003
Cold spray printed products are not prone to porosity, thermal cracking and other defects associated with melt-based technologies. This method has several advantages over other production methods. The technology is used in the military and aerospace industries around the world. For example, the US Army uses cold spray to repair the mounts of a worn Bradley 25mm steel turret gun.
In the automotive industry, cold spray steel is used for crash repairs because the high strength steel substrates in cars can be susceptible to thermal repair methods such as welding. nine0003
Direct Energy Deposition (DED) and Wire Arc Additive Manufacturing (WAAM)
WAAM Steel Parts from MX3D (Source: MX3D) Direct Energy Deposition (DED) uses welding powder or wire that enters through a nozzle and is fed into the power source to melt the metal. A melt region is created and applied to the substrate. DED is a new process, reminiscent of an old building technology known as "cladding", in which a coating is applied to a substrate, often for thermal insulation or weather resistance. DED is useful for fabricating large objects as a whole, as well as complex geometries that require extensive machining. DED can get such parts much closer to finished than traditional CNC machining. nine0003
Because DED uses a coating process, it can be used to add complex geometries to existing steel parts, thus combining complexity with cost reduction. For example, the French company AddUp advertises a rocket nozzle that uses a preformed large 304 stainless steel hopper cone printed with an isogrid structure, usually made from a larger piece by traditional methods.
A technology related to DED is wire-arc additive manufacturing (WAAM). Instead of powder, WAAM uses a metal wire that is melted by an electric arc. The process is controlled by robotic arms. WAAM is also capable of producing large-sized metal parts, as demonstrated by the Dutch company MX3D and its nine thousand-pound 41-foot stainless steel bridge in Amsterdam, as well as an oil and gas equipment repair part, proving that parts can be made in the field. nine0003
Micro 3D printing
Micro parts printed from steel (Source: 3D MicroPrint)Micro scale additive manufacturing, or micro 3D printing, can produce products with a resolution of a few microns (or less). There are three micro 3D printing methods to produce metal parts.
LMM (lithography-based metal fabrication) is a light-based technology that creates tiny parts from raw materials, including stainless steel, for applications such as surgical instruments and micro-mechanical parts. nine0003
Electrochemical deposition is the latest micrometal 3D printing process developed by the Swiss company Exaddon. In this process, the printing nozzle applies liquid with metal ions, creating details at the atomic level.