3D printer electronic
3D printing electronics: Transforming the electronic industry
3D Learning Hub
See all categories
Contents:
- Introduction
- What are the advantages of 3D printing for electronics?
- 3D printing with electrostatic discharging properties
- Conductive 3D printing offering new opportunities
- 3D printed electronics: What is possible?
- What about the future of 3D printing in the electronics industry?
Introduction
What are the advantages of 3D printing for electronics?
3D print the perfect prototype
3D printing helps you get from the idea to the product in a matter of days.Launch your first series
Moreover, the electronics industry can truly benefit from additive manufacturing. No stock, no minimum number of units and short turnaround are the key upsides of using Sculpteo’s 3D printing service for your electronic devices, regardless of where they are in product life cycle management. Electronic production is made easy thanks to our 3D printing technology and will improve and simplify your whole supply chain management! 3D printing and electronics are strongly linked. Online 3D printing allows you to create a new kind of relationship with your clients.
Design freedom
Electronic components production can now be thought in terms of 3D design and not only 2D, with new ways of stacking the circuits. It opens new possibilities to design for electronics, that are new to explore! Customization is becoming a big asset while using additive manufacturing for the creation of your products: you can create parts perfectly adapted to a circuit board or any electronic device. 3D printing can be used to create personalized electronic enclosures, USB stick cases, and keyboards, for example. Using additive manufacturing also offers you flexibility in the creation of your design. More than a perfectly adapted device, you can also elaborate complex geometries impossible to make with other traditional manufacturing techniques.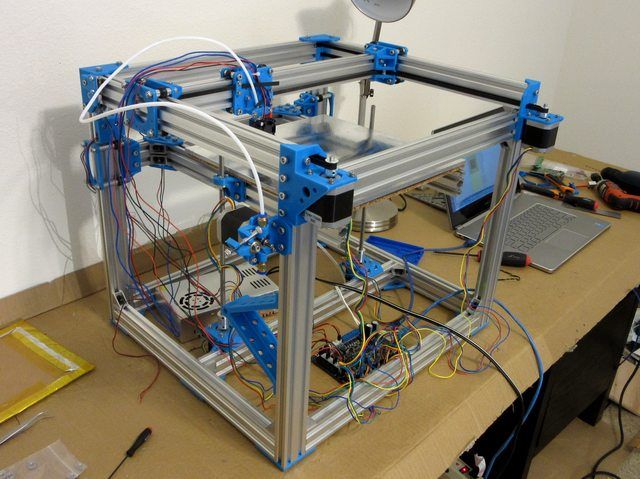
3D printing with electrostatic discharging properties
What is an electrostatic discharge?
What is called “electrostatic discharge” (ESD) is the flow of electricity between two electrically charged parts causes by contact. Static electricity often causes ESD through a process known as tribocharging. This static electricity can arise when surfaces rub together and this results in an excess of electrons on one surface and a deficiency on the other. The ESD occurs when differently-charged objects are brought close together or when the dielectric between them breaks down, often creating a visible spark. Electrostatic Discharges are a real problem and can damage sensitive electronic components. It can also lead to the alteration of magnetic media and set off fires, explosions in flammable environments! ESD is a big concern for the electronic industry, and being able to manufacture ESD-safe part is a real advantage to avoid any problem.
Focus on: Ultrasint PA 11 ESD
At Sculpteo, we are now offering you the possibility to manufacture your ESD-safe parts. If you are prototyping or producing a project where electrostatic discharging safety is critical, our Ultrasint® PA11 ESD material will be a perfect choice. Ultrasint® PA11 ESD is a bio-derived material, appearing to be a perfect choicel for increased process safety in advanced applications. With its interesting mechanical properties, this material offers new possibilities for a wide range of new applications, especially for the electronics sector. Indeed, with its low resistivity, Ultrasint® PA11 ESD is reducing the risk of electrostatically induced damage or failures, the material does not accumulate static electricity and can come in contact with electronic components without running any risk. The surface resistivity of Ultrasint® PA11 ESD is lower than traditional electrostatic dissipating materials. You can now make the most of the advantages of both additive manufacturing and electrostatic discharge properties. For electronic housing, electronic jigs and fixtures, this material is perfectly adapted. PA 11 ESD also as other advantages and interesting mechanical properties such as high tensile strength and elasticity, which could help you create efficient tools. What are you waiting for? With this material, you can create parts combining superior mechanical and thermal characteristics with outstanding electrostatic discharging properties. Get your parts 3D printed with Ultrasint® PA11 ESD by uploading your 3D file on our 3D printing service right now. It will only take a few clicks and you will get an instant quote.
Conductive 3D printing offering new opportunities
3D printing complex electronic components could go even further with conductive 3D printing. The creation of electronic devices with conductive features using 3D printing can particularly be useful to develop IoT (Internet of Things) projects. This innovative technology could allow creating 3D printed devices like LED, or touch sensors. But this ability to 3D print conductive devices could be involved in bigger projects, in soft robotics, 3D electronics, and also for communication devices such as 3D printed Near Field Communication (NFC) antennas.
3D printed electronics: What is possible?
As you will see, this 3D technology can be used for various applications in the electronics industry. Get inspired by these innovative electronic devices made using additive manufacturing!
3D printed circuit board by Nano Dimension and Harris Corp: 3D Printed Circuit Boards
Nano Dimension is known to work actively on 3D printed electronic devices The Nano Dimension’s DragonFly™ system is used to 3D print functional electronics prototypes and complex multi-layer Printed Circuit Boards (PCBs). But that is not all.
Nano Dimension and Harris Corp partnered to develop 3D printed electronic devices to create a radio frequency (RF) amplifier. They now work to go further and create hardware for the International Space Station. Their goal is to optimize the 3D printing process for RF components for flight studies aboard the ISS. Using additive manufacturing is a solution for them to find new ways to create radio frequency and circuit boards to find new innovative techniques.
The Simusolar project
At Sculpteo, some of our customers are working on solar energy using 3D printing. On the blog, we already told you about Simusolar, a company created in 2014 and looking to bring solar energy to the rural population of Tanzania. They develop and implement small-scale sustainable solutions to help local people in their everyday life.
They decided to use 3D printing because they needed a lot of custom made parts, for a low price. Their clients are farmers, fishers, or rural residents looking for various equipment powered by solar energy.
Optomec developing the Aerosol Jet Technology
Optomec announced that their Aerosol Jet Technology will be printing embedded electronics at the micron scale. The innovative process relies on both local deposition and local curing. This way, electronics parts are more affordable and require less waste of materials, and all of this with a superior resolution.
Start 3D printing enclosures!
3D printing enclosures are one of the most common uses of 3D printing for the electronic industry. Solidity, quality, customization, and accuracy, this is what you will make the most of while 3D printing your electronics enclosures.
If you are interested in 3D printing your own enclosure, you can follow our 3D printed enclosure design guide!
What about the future of 3D printing in the electronics industry?
What if in a few years, we could be able to create fully-functional smartphones or multi-material products using additive manufacturing? If these ideas are still dreams today, the innovations related to conductive 3D printing and electronic devices are now showing new opportunities. It might be time to rethink the way we conceive enclosures, circuit boards, and electronic components. From your prototyping process to the production and the management of your supply-chain, additive manufacturing could help you go through new challenges.
As you can see additive manufacturing has a lot to offer for electronics. It could become quite common to 3D print electrical elements. If you have an electronic project, but you don’t know what software you could use to start it: here is our selection of the best CAD software for electronics. Then, don’t hesitate to try out our online 3D printing service. You will just have to upload your 3D file, we will take care of it and send you your 3D printed objects in a few days.
Related Topics
- Return to Top
Get the latest 3D printing news delivered right to your inbox
Subscribe to our weekly newsletter to hear about the latest 3D printing technologies, applications, materials, and software.
What are 3D Printed Electronics? Let us tell you.
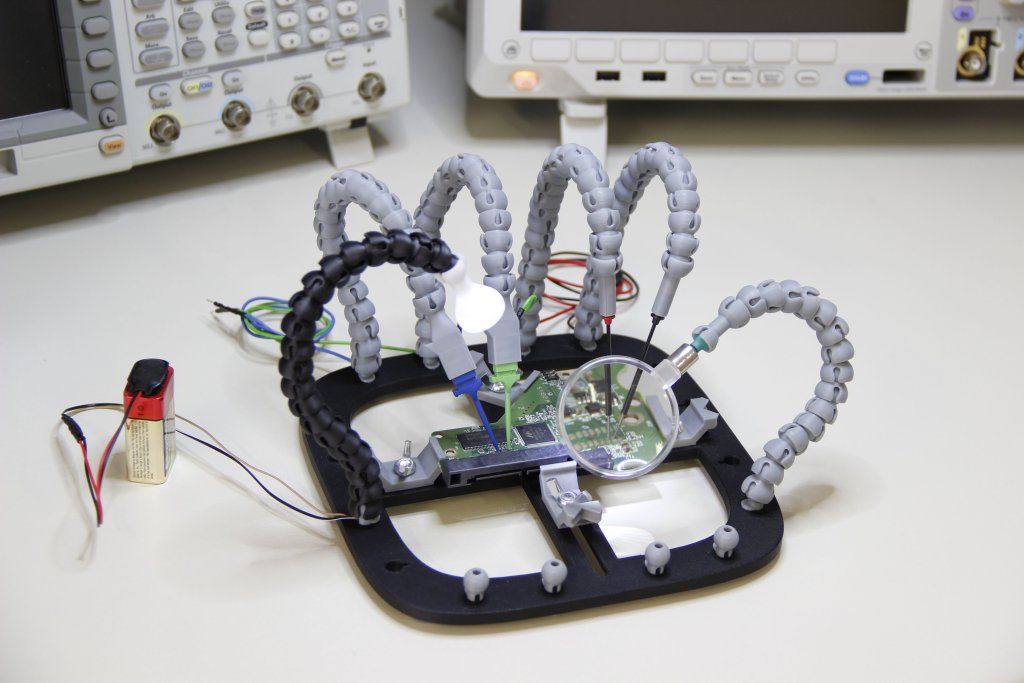
Design
The complexity of electronics combined with the capabilities of 3D printing. Heard of 3D printed electronics but want to know more?The ability to 3D print electronics is making waves in an industry plagued by long stints of R&D and a never ending cycle of prototypes and new releases.
But what exactly does this process entail? And how, as a designer, architect, or artist, can it help you? Is it sustainable? What are the dangers? And what should you know about it?
This guide is a useful starting point for you to find out…
With 3D printing electronics it is possible to make various types of boards that can be programmed and connected to prototypes – ©iakovenko123/Depositphotos.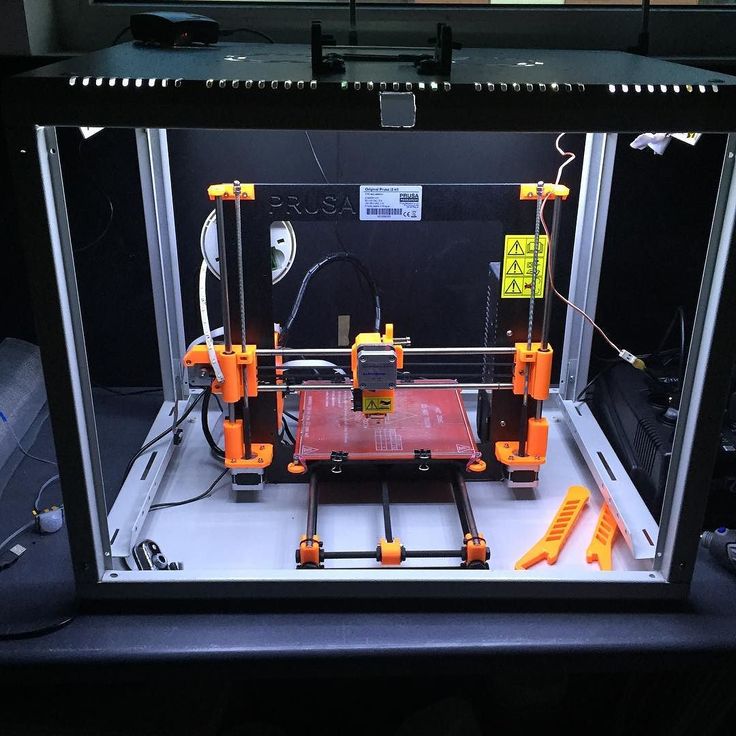
3D Printing objects with electronic functionality is a relatively new concept.
It involves the use of material jetting technology, which is used to jet conductive and insulating inks onto the printing surface.
These inks are applied in lines as thin as a few microns before UV light is used to solidify the inks.
The use of material jetting facilitates multi-material 3D printing, which is particularly useful for the electronics industry.
This means that the different elements necessary in electronics, such as functional circuitry and enclosures, can be manufactured in a single print run.
3D printing electronics involves the use of material jetting technology, which is used to jet conductive and insulating inks onto the printing surface – ©IgorVetushko/Depositphotos.comWhat materials are used when 3D printing electronics?Where systems could typically use just one material in the 3D printing process, recent advancements have enabled the involvement of multiple materials.
This allows manufacturers to merge conductive materials with non-conductive materials.
The thermoplastics used in the 3D printing process are often made with copper, carbon and graphene.
Meanwhile, proprietary conductive and dielectric inks are used simultaneously to build functional circuits and antennas. This expands the range of functions in 3D printed electronics.
Because the process combines multiple materials into the same 3D object it also requires a solvent to ensure their compatibility. The particular solvent used is known as an orthogonal solvent, which is specifically designed not to cause damage to the different components.
The thermoplastics used in the 3D printing process are often made with copper, carbon and graphene – © Julian Pagliaccio, via Wikimedia CommonsWhat can 3D printing electronics produce?With 3D printing electronics, it is possible to make various types of boards that can be programmed and connected to prototypes.
A very wide range of inks can be utilized enabling a full range of printed electronics functionality: conductors, semiconductors, dielectrics, resistors and more.
The process can be used to manufacture electronic components such as resistors, capacitors, antennas, sensors, and thin film transistors.
Using the 3D printing process, it is also possible to rapidly 3D print fully functional electronic circuits that contain electrically-conductive metallic inks and insulating polymeric inks, which could be useful for medical devices, radio frequency shielding surfaces and novel structures for harvesting solar energy.
Today, however, it’s main applications include printing electronics for use in prototypes for upcoming products, prosthetics and more complexly shaped electronic products.
Give me a step-by-stepWhile several methods exist for 3D printing electronic components, they typically mirror the various steps utilised in regular 3D printing. The main difference is the use of a dual-material fused filament process with conductive thermoplastic filaments.
As with all 3D printing, a digital CAD model of the desired part is designed, which serves as the printer’s instruction model.
When the printing process begins, a trace or “fingerprint” is created, and then the requisite materials needed for that specific part are added in layers.
The process flow of the 3D systemWhat machinery is used when 3D printing electronics?Specialised machinery is required which integrates a precise inkjet deposition printer with dedicated nano-inks and software capable of printing electronic circuits such as printed circuit boards (PCBs), antennas, capacitors and sensors.
Can I do it at home?Due to the complexity of the process, it is not possible to replicate it at home unless you have the capability of manufacturing your own 3D printer.
With the relevant machinery, it is possible to 3D print electronics at home.
Find out more about manufacturing processes, don’t miss What is Explosive Forming? Let us tell you…
The benefits of 3D printing electronics range from faster time-to-market, greater freedom of design and customizationWhat are the pros & cons of 3D printed electronics?At the core of every electronic device is a Printed Circuit Board (PCB) which is difficult to produce. Luckily, with the advent of 3D printing, manufacturing these circuit boards is less challenging.
The benefits of 3D printing electronics range from faster time-to-market, greater freedom of design and customisation.
This is because with the advent of 3D printing electronics manufacturers can create prototypes of circuits and circuit birds in-house, reducing procurement expenses and eliminating concerns about IP infringement.
3D printing also opens up opportunities to design complex shapes and components. For example, multilayer circuits can now be 3D printed on non-flat, flexible surfaces, which would not be possible with traditional manufacturing techniques.
Components can also be printed onto 3D surfaces eliminating the need for a separate substrate and reducing the size, thickness and weight of the end product.
However, there are several limitations when it comes to 3D printing electronics, not only because it is limited in the types of parts it can produce.
Whilst the recyclability of 3D printed electronics is an area being explored by various researchers, it remains a con due to what is currently possible.
Another downside to 3D printed electronics, and in fact, all 3D printed products is their structural integrity.
Whilst printed layers adhere together in some cases, and under certain stresses or conditions, they can delaminate.
Another major downside to 3D printing as a whole is its increasing popularity and accessibility. On one hand, it democratises the manufacturing processes but it also makes it easier to fake and counterfeit products.
I want to know if it’s sustainable…Whilst 3D printing electronics can minimise the manufacturing footprint by localising production, the difficulty in recycling the various components means it can’t be considered a sustainable process.
There are several resources that are useful when it comes to building your knowledge around 3D printed electronics.
If you want to learn more check these out:
- A visual demonstration of the 3D printing process used to manufacture electronics.
- An explanation of the various capabilities of 3D printing electronics.
- A paper detailing the evolution of 3D printing electronics.
- A breakdown of the various benefits and current systems employed when 3D printing electronics
- A detailed research into the future of 3D printing electronics and its benefits when used for prototyping.
Fascinated by 3d printing? Don’t miss 3D printing ceramics: Interview with Hilda Nilsson.
Techno Print 3D Company
This is our first review of the most popular and inexpensive 3D printers for 2020. The list will include the best-selling devices in two price ranges (up to 30 tr and up to 60 tr). Printers working with both plastic filament (FDM) and photopolymers (LCD/DLP) will be presented. This list will always be up to date, as it is periodically updated and supplemented. Read more→
The Chinese company Dazz3D announces the launch of the project on KickStarter and accepts pre-orders for Dazz3D Basic and Dazz3D Pro 3D printers. These revolutionary new devices are aimed at both the professional and amateur markets. Read more→
We all know that precise calibration of the 3D printer desktop is the foundation and the key to successful printing on any FDM printer. In this article we will talk about the main and most popular ways to level the "bed". So, as mentioned above, 3D printing without desktop calibration is impossible. We face this process Read more→
It's hard to go through a day today without hearing about 3D printing technology, which is bursting into our lives at an incredible speed. More and more people around the world are becoming addicted to 3D printing technology as it becomes more accessible and cheaper every day. Now almost anyone can afford to buy a 3D printer, and with the help of Read more→
The FormLabs Form 2 and Ultimaker 3 are perhaps the most popular 3D printers today, capable of high quality printing with incredible surface detail. Moreover, these two devices use completely different technologies, and therefore, there are a lot of differences between them. Many will say that it is wrong to compare them or Read more→
XYZprinting, best known for its daVinci line of desktop 3D printers, is bringing five new devices to the professional and industrial environment. One will use laser sintering technology, the second full color inkjet printing and three DLP machines. First of all, the novelties will be of interest to dentists and jewelers. Read more→
Cleaning the nozzle of a 3D printer is a fairly common process that any user of such a device has to deal with. This is not at all a complicated procedure that anyone can handle. You can complete this task in 15 minutes, using only handy tools and accessories. Read more→
Acetone steam polishing of ABS plastic is a process for smoothing the surface of 3D printed models. The result of this treatment makes your printed products look as if they were made by a professional mold casting method. If you want to understand how this is done correctly, then read this article. Aceto Read more→
EBM Industrial Metal 3D Printers
Electron Beam Melting (EBM) Additive Metal Powder 3D Printing Technology
Industrial 3D printers for printing metals using electron beam melting (sintering) are designed for the production of ready-to-use metal products (parts). At the same time, the printed parts can have an arbitrary shape, internal cavities, various filling factors (porosity), arched design, parts in parts made in a bionic design to reduce weight and increase the strength of products.
In world practice, industrial EBM 3D printers are often used for the production of osteoimplants (artificial bone implants) according to the individual dimensions and geometry of the patient's bones, taken using computed tomography. And there are a number of good reasons for this. Titanium and stainless steel alloys are used to construct osteoimplants. Unlike SLM 3D printers, where the sintering energy is generated using a laser, electron beam printers can use metal powders of a coarser (larger) fraction, for example, 75-120 microns.
For use inside the human body, the surface roughness of the osteoimplant is not critical and can even provide better fusion with the rest of the body tissues and germination with mesh and arch structures of artificial bones. Larger fractions of metal powders have a lower cost, which reduces the cost of the production process.
Also, 3D printers that print metals using electron beam melting have a higher speed of building a product. The printing itself takes place at a high temperature in the chamber, including metal powder. This makes it possible to obtain finished products with a high degree of sintering (fusion) without the need for additional heat treatment in vacuum furnaces, as in printing using SLM technology.
In the products themselves, there are no residual thermal stresses that contribute to the formation of cracks and subsequent destruction during the loaded operation of the products.
What is the additive 3D technology of electron beam melting EBM?
A removable build platform is firmly attached to the piston of the elevator system of the 3D printer. A vacuum is created in the sealed chamber of the 3D printer, which is necessary for the free movement of electrons. By the way, the principle of operation of a cathode-beam printer strongly resembles the operation of the kinescopes of the first televisions.
The scattered electron beam heats up the removable platform and chamber. The moving carriage applies and levels the first layer of metal powder onto the platform. The scattered beam of electrons, if necessary, produces additional heating of the powder layer. Then the beam is focused to a point and at a high scanning speed, in accordance with the program, begins to fuse the metal powder. Electrons are emitted by a tungsten cathode heated to the glow temperature. They are accelerated by a high voltage of 60 kV applied to the anode, which is the build platform and the powder chamber.
The primary anode serves to improve the focusing of the electron beam. The focusing coil compresses the beam, while the scanning coil deviates it along the X and Y axes. Focused to a point with a diameter of 0.2 mm, an electron beam with a power of up to 3 kW easily fuses even an increased layer of metal powder. Scanning by a magnetic field of a beam of electrons flying at the speed of light is absolutely inertialess, in contrast to a scanning system with mirrors and lasers. It allows you to move the electron beam at a tremendous speed up to 10 km / s and fuse metal powder in a multi-beam way at 100 points simultaneously!
Which accordingly affects the increase in printer productivity, which is at least two to four times higher than the productivity of similar metal laser printers. It should be understood that the energy saturation of electron beam 3D printers of EBM technology is many times higher than the energy of existing models of laser 3D printers using SLM technology. Although inferior to them in the accuracy of the additive construction of products.
After the first layer of metal powder has been melted, the piston moves down by a construction step (about 0.2 mm), the carriage applies and levels the next layer of powder, and the next cycle of zone electron beam melting takes place.
To level the inaccuracy of the platform on which the product is printed, and to level the horizontal surface, at the beginning of the additive printing process, legs - stands are printed. The requirements for their strength and quality are low, so they are printed with a low degree of volume filling. It should be noted that when printing, a large amount of heat is released in the product, so heating with a scanning beam is done only when necessary. In general, the preheating temperature of the powder surface can vary in the range of 500 - 1000°C depending on the material of the powder.
At the end of the production of the finished product, the piston moves up, with the help of a special industrial vacuum cleaner and brush, unused metal powder is collected.
Attention! It is possible to open the vacuum chamber and let oxygenated air into it only after the chamber has cooled down. Metal powders are extremely flammable and ignite instantly in air, especially when heated to high temperatures.
Attention! Work on cleaning unused powder is carried out in a respirator to prevent damage to the respiratory organs by fine metal powder.
After the chamber has cooled down and the unused powder is completely removed, the build platform with the finished product welded to it is unscrewed from the piston. Then, using a tungsten string on an electroerosive machine, the part is cut off from the platform. It is further machined to remove the remnants of the legs. If necessary, sandblasting is performed to reduce the surface roughness of the product.
Additional heat treatment of parts in most cases is not required. The product is ready for use immediately after printing. And this also affects the cost reduction of additive metal printing on electron beam 3D printers. It should be noted that in the cost of additive 3D printing with metal powder using SLM laser technology, the depreciation of a 3D printer is up to 70% of the cost of the finished product. And the contribution to the cost of a rather expensive, at first glance, metal powder is in second or third place.
Electron beam 3D printers, having higher productivity, make a much smaller contribution from printer depreciation to the cost of the finished product and, accordingly, reduce its cost.
EBM200 industrial cathode beam 3D metal printer technical parameters
3D printer settings | Meaning |
Maximum build size | 200x200x240 mm |
Product construction accuracy | (Standard - Ti6Al4V) ± 0. |
Maximum electron beam power | 3 kW |
Accelerating anode voltage (on powder) | 60 kV |
Accelerating anode current | 0-50mA |
Hot cathode type | Tungsten filament |
Minimum Beam Spot Diameter | 0.2mm |
Maximum Beam Scanning Speed | > 10 km/s |
Multipath melting | Up to 100 points |
Ultimate vacuum | <10 -2 Pa |
Helium partial pressure | 0. |
Powder heating | Scattered Beam Scanning |
Powder surface temperature | 500-1000℃ |
3D printer cooling system | Chiller using distilled water |
Monitoring the build process | Through the glass of the vacuum chamber |
CAD Interface | STL file format |
Software | Meta Build v1.2, for PC |
Printer size | 2100x1000x2300 mm |
Printer weight | 2000 kg |
Source of power | 3 phase, 380 V, 36 A, 8 kW |
Catalog
Download >>> View >>>
3D printer kit
- Industrial 3D printer of EBM technology.
- Chiller, for the 3D printer cooling system with distilled water.
- Vacuum drying chamber for metal powder.
- Industrial vacuum cleaner.
Optional:
- Pneumohydraulic machine (sandblaster).
- Machine for electroerosive cutting.
- Air conditioner and dehumidifier.
Room requirements for metal additive 3D printing by electron beam method:
- 9029one Maintaining a stable temperature and humidity regime.
- Maintaining a stable temperature and humidity regime.
- Temperature 20-26 degrees.
- Humidity less than 40% non-condensing.
- To do this, the room for 3D metal printing should be equipped with an air conditioner and a dehumidifier.
Types of metal powders for additive 3D printing by electron beam method
- Titanium and titanium alloys.
- Aluminum alloys.
- Heat resistant steel alloys.
- Cobalt and chromium alloys.
- Stainless steel 316L.
- Copper alloys and many others.
Applications for 3D cathode beam metal printers:
- aerospace,
- medical,
- military,
- industrial area.
Benefits of Electron Beam Additive 3D Printing (EBM):
- High performance EBM 3D printers compared to SLM technology.
- Low cost of products.
- Uses less expensive coarser grade metal powder.
- Possibility of recycling of metal powder after its screening and vacuum drying.
- The electron beam is controlled by magnetic fields.
- Expensive optical mirrors and germanium or diamond lenses are missing.
- Inertialess electron beam control gives the highest scanning speed.
- Beam scattering allows heating metal powder without the use of additional heaters and obtaining a high density of products.
- It is successfully used for the production of orthopedic bone implants (osteoimplants) made of titanium, made porous and arched, promoting osseointegration - fusion of bone tissues with an implant (implant).
- Allows you to print products from two different materials with a gradual gradient of composition change along the Z axis.
- Allows you to create heat-resistant nozzles and blades for gas turbines, including jet engines. In addition, it is used to create load-bearing titanium elements of an aircraft wing.
- Used to create elements of rocket engines: combustion chambers and nozzles with resistance to temperatures above 3000°C. Where high pressure and temperature require the use of refractory and durable materials such as titanium.
- Unlimited by the geometric complexity of the manufactured parts without the need for subsequent assembly or welding.
- Ability to print internal cavities and details in parts.
Disadvantages of electron beam additive 3D technology (EBM):
- Relatively small size of the build chamber.
- Increased roughness, printed products.
- During the operation of a 3D printer, X-ray bremsstrahlung occurs, from which it is necessary to protect both equipment and maintenance personnel.
- Respiratory protection of service personnel from fine metal powder is required.
- Tendency to ignite metal powders of titanium and steel.
China is the world's first economy and the world's largest manufacturer of 3D printers.
The quality of Chinese 3D printers often exceeds American and German counterparts due to mass production and application. At the request of the customer, American lasers and German scanners, Japanese servomotors, and Taiwanese controllers are used in 3D printers. Industrial 3D printers and software are updated and improved every 2 weeks. Hundreds of prototyping centers operate throughout China to provide quality prototypes and finished products to China's most powerful industry in the world.
Video